How PCB Baking Works
The PCB baking process typically involves the following steps:
-
Solder Paste Application: Solder paste, a mixture of powdered solder and flux, is applied to the copper pads on the PCB where components will be placed. This is often done using a stencil or solder paste dispensing machine.
-
Component Placement: The components are then placed onto the PCB, with their leads/pins aligned with the solder paste-covered pads. Surface mount components are placed using pick-and-place machines while through-hole components are inserted manually or with machines.
-
Reflow Soldering: The populated PCB is then sent through a reflow oven which heats it to specific temperatures following a reflow profile. The typical reflow profile consists of four stages:
Stage Temperature Range Time Preheat 90-150°C 30-90 sec Soak 150-200°C 60-120 sec Reflow 215-250°C 30-90 sec Cooling Gradual cooling to room temp 30-90 sec During the reflow stage, the solder paste melts and forms solder joints between component leads and PCB pads as it cools.
-
Inspection: After baking, the PCBs are inspected, often using automated optical inspection (AOI) systems, to check for any soldering defects like bridges, tombstones, insufficient solder, etc. Any problems are corrected, if needed, through a second reflow cycle or manual rework.
Reflow Oven Types
There are two main types of reflow ovens used for PCB baking:
-
Convection Ovens: These use hot air circulation to heat PCBs. The heat transfer is gradual and uniform. Convection ovens are the most common type for PCB baking.
-
Infrared (IR) Ovens: These use infrared lamps or ceramic heaters to heat PCBs. The heat transfer is faster but less uniform compared to convection. IR is often used for rework or selective soldering.
Some ovens use a combination of convection and IR heating for optimum results.
Benefits of PCB Baking
PCB baking offers several benefits in electronics manufacturing:
-
Reliable Solder Joints: Reflow soldering results in consistent, reliable solder joints compared to manual soldering. The controlled heating and cooling ensures proper wetting and avoids defects.
-
High Throughput: Reflow ovens enable mass soldering of hundreds of joints simultaneously, significantly increasing production speed and throughput compared to manual methods.
-
Automation: PCB baking is a highly automated process, reducing labor costs and human errors. Paste dispensing, pick-and-place, and inspection can all be automated.
-
Compatibility with SMT: Surface mount technology (SMT) components, which are smaller and more densely packed than through-hole, require reflow soldering. PCB baking makes assembling SMT-based designs feasible.
-
Reworkability: Defective boards can be sent through the reflow process again to remove and replace faulty components, enabling rework and reducing scrap.
Challenges in PCB Baking
While advantageous, PCB baking does pose some challenges:
-
Thermal Damage: Excessive or prolonged heating can damage sensitive components on the PCB. Following the correct reflow profile is critical.
-
Warping: PCBs can warp or twist during baking due to uneven heating or improper support. This can cause component misalignment and stress.
-
Moisture Control: Moisture absorbed by PCBs or components can vaporize and cause defects during reflow. Proper storage and baking before reflow is necessary.
-
Flux Residue: Some flux in solder paste can leave corrosive or insulative residues after reflow which may require cleaning.
-
Complex Profiles: Boards with a mix of different component sizes or thermal requirements may need complex, customized reflow profiles to avoid damage. Creating and validating profiles takes time and expertise.
Despite the challenges, PCB baking remains the standard method for mass PCB Assembly in the electronics industry.
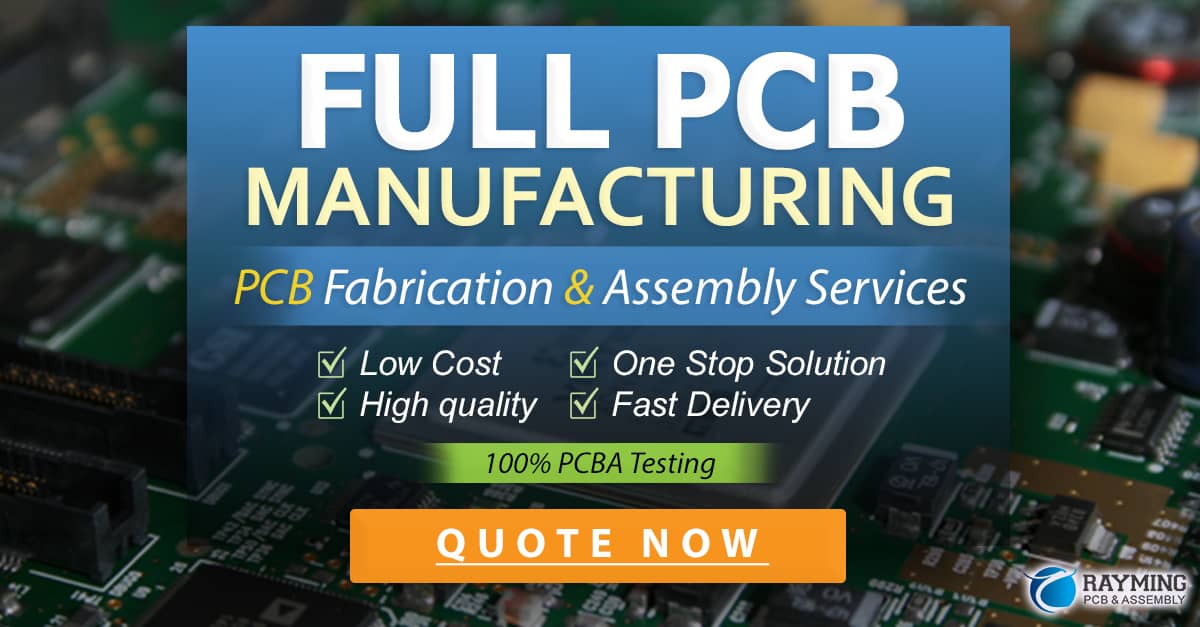
Equipment for PCB Baking
Setting up a PCB baking process requires several key pieces of equipment:
-
Reflow Oven: A convection or IR reflow oven capable of following the necessary temperature profiles. Ovens range from small benchtop models for prototyping to large inline systems for high volume production.
-
Solder Paste Printer: Used to apply solder paste to PCB pads. The most common type is a stencil printer which uses a laser-cut stencil to deposit paste. Automated dispensing systems are also used.
-
Pick-and-Place Machine: Robotic systems that pick up and place SMT components onto the solder paste with high speed and precision. They use vacuum nozzles and vision systems to handle a range of component sizes.
-
Inspection Systems: Automated optical inspection (AOI) systems scan boards after reflow to check for soldering defects. They use cameras and image processing to spot problems like bridges, tombstones, insufficient solder, etc. Manual visual inspection with microscopes is also used.
-
Rework Stations: Used to manually repair or rework PCBs after reflow. They include hotair pencils, soldering irons, tweezers, and microscopes for removing and replacing individual components.
-
Fume Extraction: Reflow soldering generates fumes from flux and solder which should be vented away using fume extraction equipment for operator safety and environmental reasons.
The exact equipment needs depend on the production volume, PCB complexity, component types, and quality requirements.
PCB Baking Process Optimization
Achieving high quality and yield in PCB baking requires careful optimization of the process parameters, especially the reflow profile. Some key considerations include:
-
Reflow Profile Customization: The reflow profile should be tailored to the specific PCB design, considering factors like component thermal limits, PCB thickness, solder paste type, etc. Profiles are often developed through trial and error and validated with thermal profiling systems.
-
Oven Temperature Uniformity: The PCBs should be heated uniformly across the oven to avoid hot or cold spots that can cause defects. Oven temperature uniformity should be regularly checked and calibrated.
-
Conveyor Speed: The speed at which PCBs move through the oven affects heating time. It should be optimized based on the reflow profile and oven length.
-
Nitrogen Atmosphere: Some reflow ovens use nitrogen gas instead of air to reduce oxidation of the solder joints. This can improve joint quality but adds cost and complexity.
-
Paste and Component Placement Accuracy: The accuracy of solder paste printing and component placement directly impacts soldering quality. Regular maintenance and calibration of the printer and pick-and-place machines is important.
-
Moisture Control: PCBs and components should be baked before reflow to remove absorbed moisture which can cause defects. Humidity-controlled storage and handling are also important.
Continuous monitoring, data collection, and analysis of the process parameters and resulting defect rates is key to optimizing the PCB baking process over time.
Frequently Asked Questions
- Q: What is the difference between reflow soldering and wave soldering?
A: Reflow soldering is used for surface mount components and involves melting solder paste in an oven. Wave soldering is used for through-hole components and involves passing the PCB over a molten solder wave. Reflow allows for smaller, denser assemblies compared to wave.
- Q: Can I bake PCBs in a regular kitchen oven?
A: No, kitchen ovens are not suitable for PCB baking. They lack the precise temperature control, uniformity, and cooling needed for proper reflow soldering. Using a kitchen oven can result in damaged components, poor solder joints, and even fire hazards.
- Q: What is the typical temperature range for PCB baking?
A: The peak temperature in a reflow profile is typically between 215-250°C, depending on the solder paste type. The entire process from preheat to cool down spans a wider range from room temperature up to the peak.
- Q: How long does the PCB baking process take?
A: The total time for a single PCB to go through the reflow oven is usually 3-8 minutes, depending on the specific profile and oven. However, inline ovens can process thousands of PCBs per hour.
- Q: What are some common defects in PCB baking?
A: Some common reflow soldering defects include:
– Bridging: Solder connecting adjacent pins/pads, causing shorts
– Tombstoning: Components lifting up on one end due to uneven heating or pad sizes
– Insufficient solder: Weak or missing solder joints due to too little paste
– Blow holes: Small holes in the solder joint due to moisture or contamination
– Solder balls: Small spheres of solder that can cause shorts
Proper process control and inspection help minimize these defects.
In conclusion, PCB baking is a critical process in electronics manufacturing that enables reliable, high-volume assembly of surface mount PCBs. By carefully controlling the reflow profile and other process parameters, a wide range of electronic products can be produced with high quality and consistency. As electronics continue to advance in complexity and miniaturization, effective PCB baking will remain an essential capability for the industry.
0 Comments