Why Use a PCB assembly Service?
There are several reasons why electronics companies use PCB assembly services rather than building circuit boards in-house:
- Access to advanced equipment and skilled technicians
- Cost savings compared to investing in in-house PCB assembly
- Faster turnaround times and higher volumes
- Ensured quality control and reliability testing
- Flexibility to assemble prototype and production quantities
By outsourcing PCB assembly, businesses can focus on core competencies like PCB design and product development while leveraging the expertise and capabilities of the assembly provider.
The PCB Assembly Process
The process of assembling a printed circuit board typically involves the following steps:
-
Design review: The assembler reviews the customer’s PCB design files, bill of materials (BOM), and other documentation to ensure everything is complete and the design is manufacturable. Any issues are resolved with the customer before proceeding.
-
PCB fabrication: The bare printed circuit boards are either supplied by the customer or fabricated by the assembler based on the PCB design files. This involves applying copper traces, solder mask, silkscreen, and drill holes on the board substrate.
-
Solder paste application: Solder paste, a mixture of tiny solder spheres and flux, is applied to the PCB pads where components will be placed. This is typically done using a solder paste stencil and automated paste dispensers.
-
Component placement: The electronic components are placed on the PCB in their designated locations. For surface mount assembly, an automated pick-and-place machine rapidly places components. Through-hole components are inserted manually or by machines.
-
Soldering: The PCB with placed components goes through a reflow oven which melts the solder paste, permanently attaching the components to the board. Wave soldering is used for through-hole components on the bottom side of the board.
-
Inspection and testing: The assembled PCBs are visually inspected and electrically tested to identify any defects or malfunctioning boards. Automated optical inspection (AOI) and X-ray inspection may be used. Faulty boards are reworked or scrapped.
-
Final assembly: Additional items like wire harnesses, casings, or heat sinks may be added. Conformal coating is applied if required. The PCBs receive a final visual inspection before being packaged for shipment.
The exact PCB assembly process can vary depending on the assembler’s capabilities, equipment, and the complexity and requirements of the particular PCB being built. Factors like PCB size, layer count, component types (SMD, BGA, through-hole), and special requirements influence the process flow.
Choosing a PCB Assembly Service
With numerous PCB assembly providers available, it’s important to select one that aligns with your needs. Key factors to consider include:
Technical Capabilities
Ensure the provider has experience building the types of PCBs you need in terms of complexity, size, component types, etc. Ask about their equipment and the manufacturing standards and certifications they comply with (e.g. IPC class 2 or 3).
Quality and Testing
Inquire about the assembler’s quality control processes, inspection and testing capabilities, and typical defect rates. Ensure they can meet your reliability and quality expectations.
Delivery Lead Times
For time-critical projects, select a provider that can meet your delivery deadlines. Many offer expedited services for a higher cost. Understand their typical lead times for your type of PCB assembly.
Manufacturing Location
The provider’s geographic location impacts lead times and shipping costs. Offshore assemblers (e.g. in China) often have lower prices but longer lead times compared to domestic assemblers.
Minimum Order Quantities
Depending on the volumes you need, ensure the assembler can handle your batch sizes. Some specialize in high-volume production runs while others cater to smaller quantities or prototypes.
Design Support
Some assemblers offer PCB design assistance and can help optimize your design for manufacturability and assembly. This is valuable if you have limited PCB design experience in-house.
Cost
Get quotes from multiple providers to compare pricing. However, avoid making a decision on cost alone, as the cheapest option may have lower quality or reliability. Look for the best value in terms of capabilities, quality, and price.
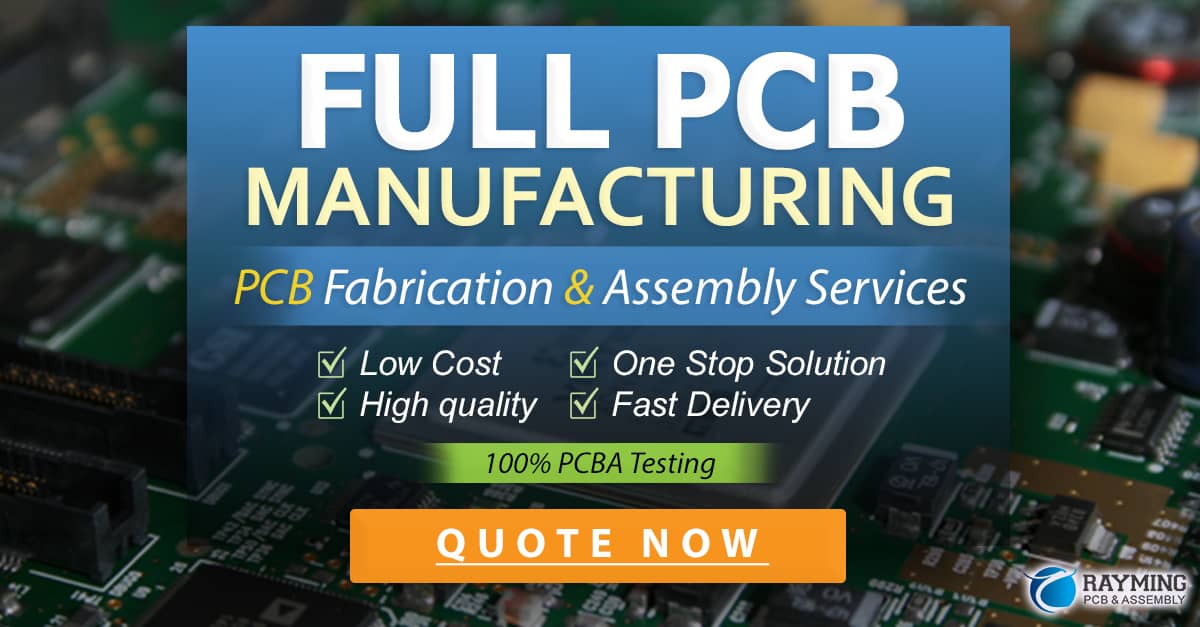
PCB Assembly Technologies
PCB assembly services utilize various technologies depending on the types of circuit boards and components being assembled. The two main categories are surface mount technology (SMT) and through-hole technology (THT).
Surface Mount Technology (SMT)
SMT is the most common PCB assembly method today. Surface mount devices (SMDs) have small metal leads or pads that are soldered directly onto the surface of the PCB. SMT allows for smaller components and higher component density compared to through-hole mounting.
The SMT assembly process typically involves:
- Solder paste application onto the PCB pads via a stencil
- Placing surface mount components onto the solder paste using a pick-and-place machine
- Sending the PCB through a reflow oven to melt the solder and permanently attach the components
Advantages of SMT include:
- Smaller PCB sizes and higher component density
- Faster and more automated assembly
- Lower costs for high-volume production
- Better mechanical performance and shock resistance
Through-Hole Technology (THT)
In THT assembly, the components have long metal leads that are inserted into holes drilled in the PCB. The leads are then soldered to pads on the opposite side of the board. Through-hole components are typically larger than SMDs.
THT assembly involves:
- Inserting the component leads into the PCB holes manually or with machines
- Soldering the leads to the pads, usually via wave soldering
- Trimming the excess leads on the solder side of the board
Advantages of THT include:
- Stronger mechanical bonds between components and the PCB
- Easier to assemble by hand for prototypes or small batches
- Some components are only available in through-hole packages
- Well-suited for high-power and high-voltage applications
Many PCB designs use a combination of SMT and THT components. The PCB assembly process is adjusted to incorporate both methods as needed.
PCB Assembly Challenges and Considerations
PCB assemblers face various challenges when building circuit boards, particularly for complex designs. Some key considerations include:
Miniaturization
As electronic devices get smaller, PCBs need to pack more functionality into less space. This means using smaller components, finer pitch leads, and denser layouts. Assembling such PCBs requires precise equipment and skilled operators to place and solder the tiny components accurately.
High-Density Interconnect (HDI) PCBs
HDI PCBs have a higher wiring density than traditional PCBs, enabling smaller boards and finer circuit features. They often incorporate micro vias, blind and buried vias, and multiple laminated layers. Assembling HDI PCBs requires specialized equipment and processes to achieve the necessary precision and reliability.
Ball Grid Arrays (BGAs)
BGAs are surface mount ICs that have an array of solder balls underneath the package instead of leads. They enable a high number of interconnects in a small space. However, the solder joints are not visible underneath the BGA, making defects harder to detect. X-ray inspection is often used for quality control.
Harsh Environments
Some applications like automotive, aerospace, and industrial controls require PCBs to operate reliably in harsh conditions such as extreme temperatures, vibration, and moisture. The PCB assembly process needs to account for these factors, using appropriate components, solder alloys, and conformal coatings.
Electrostatic Discharge (ESD) Protection
Many electronic components, particularly semiconductors, are sensitive to damage from ESD. PCB assembly facilities need proper ESD controls like grounded workstations, ESD-safe packaging, and personnel grounding to prevent device failures.
Rework and Repair
Despite careful process controls, some assembled PCBs may have defects that require rework or repair. This involves removing and replacing faulty components using specialized tools and techniques to avoid damaging the board. Skilled technicians are essential for rework and repair.
Prototype vs Production PCB Assembly
PCB assembly services cater to both prototype and production quantities, but there are some differences in the approach and processes used.
Prototype PCB Assembly
Prototyping involves building a small number of boards (often just a few) to test and validate a new design before committing to full-scale production. Key aspects of prototype PCB assembly include:
- Quick-turn services to get boards assembled in days instead of weeks
- Ability to handle frequent design changes and iterations
- More manual processes since automation is not cost-effective for small quantities
- Focus on functionality and debugging rather than cosmetic perfection
- Often used for proof-of-concept, testing, and certification
Production PCB Assembly
Production PCB assembly involves building larger quantities of boards on an ongoing basis. Key aspects include:
- Focus on efficiency, consistency, and cost reduction
- Highly automated processes using advanced equipment like pick-and-place machines and reflow ovens
- Rigorous quality control and testing procedures to minimize defects
- Emphasis on process optimization and lean manufacturing principles
- Strict adherence to the approved design and BOM to ensure repeatability
The transition from prototype to production is a critical step. The assembler will review the design and suggest changes to optimize it for manufacturability, reliability, and cost-effectiveness in production quantities.
PCB Assembly Quality Standards
To ensure consistent quality and reliability, PCB assemblers adhere to various industry standards and certifications. Key standards include:
IPC Standards
The Association Connecting Electronics Industries (IPC) publishes the most widely used standards for PCB design, fabrication, and assembly. Key standards include:
- IPC-A-610: Acceptability of Electronic Assemblies
- IPC J-STD-001: Requirements for Soldered Electrical and Electronic Assemblies
- IPC-A-600: Acceptability of Printed Circuit Boards
These standards define the criteria for workmanship, defects, and acceptable quality levels for different classes of products.
ISO Standards
The International Organization for Standardization (ISO) publishes quality management standards that many PCB assemblers comply with:
- ISO 9001: Quality Management Systems Requirements
- ISO 14001: Environmental Management Systems
These certifications demonstrate a commitment to quality, continuous improvement, and environmental responsibility.
RoHS Compliance
The Restriction of Hazardous Substances (RoHS) directive restricts the use of certain hazardous substances in electronic products. PCB assemblers need to use RoHS-compliant components and processes for products sold in regions that mandate RoHS compliance.
Choosing a PCB assembler that adheres to relevant quality standards ensures that your boards will meet the necessary reliability and performance requirements.
FAQ
What is the typical turnaround time for PCB assembly?
Turnaround times vary depending on the complexity of the PCB, the quantity ordered, and the assembler’s capacity. Prototype quantities can often be assembled in 1-2 weeks, while production lead times are typically 3-6 weeks. Many assemblers offer expedited services for a higher cost.
What files are needed to get a PCB assembled?
The key files needed are:
- Gerber files: The PCB design files that define the copper layers, solder mask, silkscreen, and drill holes
- Bill of Materials (BOM): A list of all components used on the PCB, including quantities, reference designators, and manufacturer part numbers
- Pick-and-place file: A file that specifies the location and orientation of each component on the PCB
- Assembly drawings: Drawings that provide additional instructions or specifications for the assembly process
What is the minimum quantity most PCB assemblers will build?
This varies depending on the assembler. Some specialize in low-volume prototype runs and will assemble as few as one or two boards. Others focus on higher-volume production and may have minimum order quantities of 100 or more. It’s best to discuss your quantity needs with potential assemblers to find the best fit.
Can I supply my own components for assembly?
Yes, most PCB assemblers will allow you to supply your own components, often called consigned parts. This is common for hard-to-find, custom, or sensitive components. The assembler will typically require the parts to be properly packaged and labeled, and may charge a handling fee.
How much does PCB assembly cost?
PCB assembly costs depend on several factors, including the PCB size and complexity, number of components, component types (SMD vs through-hole), quantities ordered, and any special requirements. Setup fees, component costs, and testing requirements also impact the total cost. It’s best to get detailed quotes from multiple assemblers based on your specific PCB design and requirements.
0 Comments