Key Components of Electromechanical Assembly
Electromechanical assembly typically involves the following key components:
- Printed Circuit Boards (PCBs)
- Electrical components (resistors, capacitors, inductors, etc.)
- Mechanical components (housings, brackets, fasteners, etc.)
- Connectors and wiring harnesses
- Sensors and actuators
- Power supplies and batteries
- Displays and user interfaces
Each of these components plays a critical role in the overall functionality and performance of the electromechanical system.
Factors to Consider for Electromechanical assembly design
When designing an electromechanical assembly, several factors must be considered to ensure the final product meets the desired requirements. These factors include:
1. Functionality and Performance
The primary consideration in electromechanical assembly design is the intended functionality and performance of the final product. This includes:
- Defining the system’s purpose and desired outputs
- Identifying the required sensors, actuators, and control systems
- Determining the necessary power requirements and power management strategies
- Establishing performance metrics, such as speed, accuracy, and efficiency
2. Reliability and Durability
Electromechanical assemblies must be designed to withstand the environmental conditions and stresses they will encounter during operation. Factors to consider include:
- Temperature and humidity ranges
- Vibration and shock resistance
- Electromagnetic interference (EMI) and electrostatic discharge (ESD) protection
- Corrosion and wear resistance
- Fatigue life and cyclic loading
Designing for reliability and durability helps to minimize downtime, maintenance costs, and premature failure of the system.
3. Size and Weight Constraints
The size and weight of an electromechanical assembly can significantly impact its application and performance. Designers must consider:
- Space limitations for the assembly and its components
- Weight restrictions, especially for portable or mobile applications
- Cooling and ventilation requirements
- Ergonomics and user interaction
Minimizing size and weight often requires careful component selection, efficient packaging, and innovative design solutions.
4. Manufacturing and Assembly Processes
The design of an electromechanical assembly must take into account the manufacturing and assembly processes that will be used to produce the final product. This includes:
- Material selection and compatibility
- Tolerances and fits for mating parts
- Fastening and joining methods (screws, adhesives, welding, etc.)
- Automation and manual assembly considerations
- Testing and quality control procedures
Designing for manufacturability and assembly helps to reduce production costs, improve yields, and ensure consistent quality.
5. Cost and Time-to-Market
Electromechanical assembly design must balance performance and reliability with cost and time-to-market constraints. Factors to consider include:
- Component and material costs
- Tooling and equipment investments
- Labor and overhead expenses
- Design and development timelines
- Regulatory and certification requirements
Effective cost management and project planning are essential for delivering a competitive product within the desired budget and schedule.
6. Scalability and Flexibility
Electromechanical assemblies should be designed with scalability and flexibility in mind to accommodate future changes and improvements. This involves:
- Modular design approaches
- Standardized interfaces and connections
- Upgradeable firmware and software
- Adaptability to different applications or configurations
Designing for scalability and flexibility allows for easier product updates, customization, and adaptation to evolving market needs.
7. Environmental and Regulatory Compliance
Electromechanical assemblies must comply with various environmental and regulatory standards, depending on their application and target market. Considerations include:
- RoHS (Restriction of Hazardous Substances) and REACH (Registration, Evaluation, Authorization, and Restriction of Chemicals) compliance
- EMC (Electromagnetic Compatibility) and EMI (Electromagnetic Interference) regulations
- Safety standards, such as UL, CE, and CSA
- Environmental regulations, such as WEEE (Waste Electrical and Electronic Equipment) and Battery Directives
- Industry-specific standards, such as automotive, aerospace, or medical
Designing for compliance helps to ensure that the product can be legally sold and operated in the intended markets.
Electromechanical Assembly Design Process
The electromechanical assembly design process typically involves the following steps:
- Concept development and feasibility analysis
- System-level design and architecture definition
- Detailed component selection and design
- Mechanical and electrical integration
- Prototyping and testing
- Design refinement and optimization
- Manufacturing and assembly planning
- Verification and validation
- Production and quality control
Each step in the process requires close collaboration between mechanical, electrical, and manufacturing engineers to ensure that the final product meets the desired requirements.
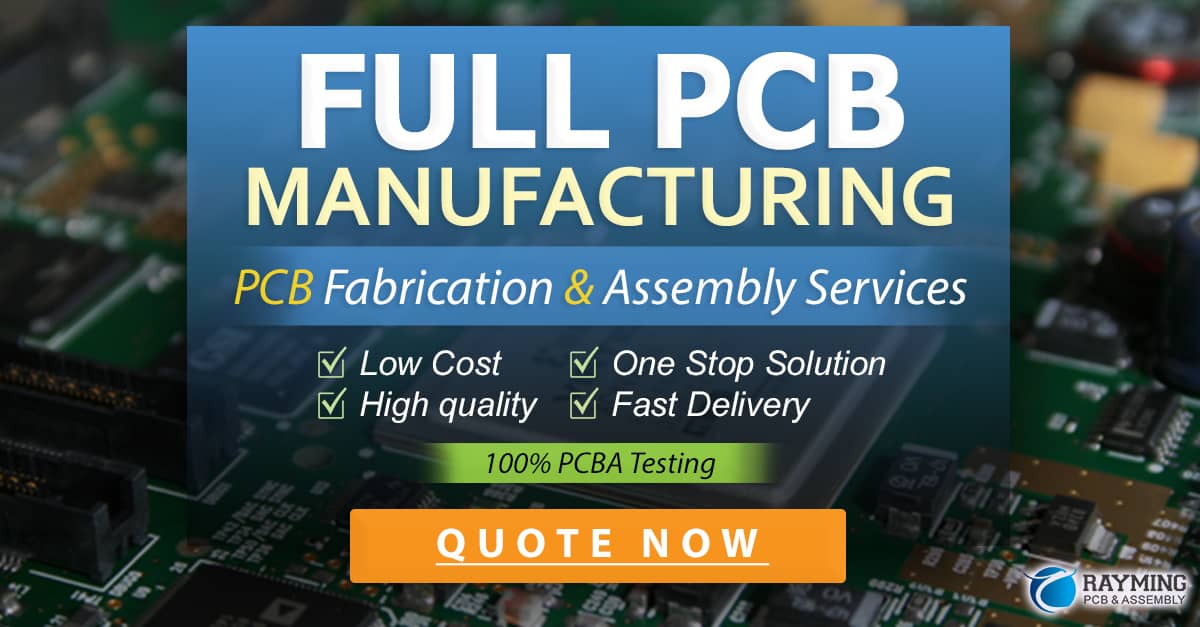
Best Practices for Electromechanical Assembly Design
To optimize the performance, reliability, and cost-effectiveness of electromechanical assemblies, designers should follow these best practices:
- Use modular and standardized designs whenever possible
- Select components based on performance, cost, and availability
- Design for manufacturability and assembly
- Incorporate design for reliability (DFR) principles
- Conduct thorough testing and validation at each stage of the design process
- Use simulation and analysis tools to optimize designs and reduce physical prototyping
- Collaborate closely with suppliers and manufacturing partners
- Document designs thoroughly and maintain version control
- Continuously monitor and improve the design based on field performance data
By following these best practices, designers can create electromechanical assemblies that are high-performing, reliable, and cost-effective.
Table: Electromechanical Assembly Design Checklist
Design Aspect | Considerations | Completed |
---|---|---|
Functionality | Define system purpose and desired outputs | ☐ |
Identify required sensors, actuators, and control systems | ☐ | |
Determine power requirements and management strategies | ☐ | |
Establish performance metrics | ☐ | |
Reliability | Define environmental conditions (temperature, humidity, etc.) | ☐ |
Consider vibration and shock resistance | ☐ | |
Incorporate EMI/ESD protection | ☐ | |
Evaluate corrosion and wear resistance | ☐ | |
Assess fatigue life and cyclic loading | ☐ | |
Size and Weight | Consider space limitations | ☐ |
Evaluate weight restrictions | ☐ | |
Address cooling and ventilation requirements | ☐ | |
Optimize ergonomics and user interaction | ☐ | |
Manufacturing | Select materials and ensure compatibility | ☐ |
Define tolerances and fits for mating parts | ☐ | |
Choose appropriate fastening and joining methods | ☐ | |
Consider automation and manual assembly processes | ☐ | |
Establish testing and quality control procedures | ☐ | |
Cost and Time | Evaluate component and material costs | ☐ |
Consider tooling and equipment investments | ☐ | |
Assess labor and overhead expenses | ☐ | |
Manage design and development timelines | ☐ | |
Address regulatory and certification requirements | ☐ | |
Scalability | Implement modular design approaches | ☐ |
Use standardized interfaces and connections | ☐ | |
Ensure firmware and software upgradeability | ☐ | |
Design for adaptability to different applications | ☐ | |
Compliance | Comply with RoHS and REACH regulations | ☐ |
Meet EMC and EMI standards | ☐ | |
Adhere to safety standards (UL, CE, CSA) | ☐ | |
Follow environmental regulations (WEEE, Battery Directives) | ☐ | |
Consider industry-specific standards | ☐ |
Frequently Asked Questions (FAQ)
-
Q: What is the difference between electromechanical assembly and electronic assembly?
A: Electromechanical assembly involves the integration of both electrical and mechanical components, such as PCBs, sensors, actuators, and housings, to create a functional system. In contrast, electronic assembly focuses primarily on the assembly of electrical components, such as PCBs and electronic devices, without significant mechanical elements. -
Q: What are the most critical factors to consider when designing an electromechanical assembly?
A: The most critical factors to consider include functionality and performance, reliability and durability, size and weight constraints, manufacturing and assembly processes, cost and time-to-market, scalability and flexibility, and environmental and regulatory compliance. Each of these factors must be carefully evaluated and balanced to create a successful electromechanical assembly. -
Q: How can I ensure the reliability and durability of an electromechanical assembly?
A: To ensure reliability and durability, designers should consider the environmental conditions and stresses the assembly will encounter, such as temperature, humidity, vibration, and shock. They should also incorporate EMI/ESD protection, evaluate corrosion and wear resistance, and assess fatigue life and cyclic loading. Designing for reliability helps to minimize downtime, maintenance costs, and premature failure. -
Q: What role does manufacturability play in electromechanical assembly design?
A: Designing for manufacturability is crucial in electromechanical assembly design. This involves selecting compatible materials, defining appropriate tolerances and fits for mating parts, choosing suitable fastening and joining methods, considering automation and manual assembly processes, and establishing testing and quality control procedures. By designing for manufacturability, designers can reduce production costs, improve yields, and ensure consistent quality. -
Q: How can I balance cost and performance when designing an electromechanical assembly?
A: Balancing cost and performance requires careful consideration of component and material costs, tooling and equipment investments, labor and overhead expenses, design and development timelines, and regulatory and certification requirements. Designers should use modular and standardized designs whenever possible, select components based on performance, cost, and availability, and continuously monitor and improve the design based on field performance data. Effective cost management and project planning are essential for delivering a competitive product within the desired budget and schedule.
Conclusion
Electromechanical assembly design is a complex process that requires careful consideration of various factors, including functionality, reliability, size and weight, manufacturing, cost, scalability, and compliance. By following best practices and using a systematic approach, designers can create electromechanical assemblies that meet the desired performance, reliability, and cost requirements.
Effective electromechanical assembly design requires close collaboration between mechanical, electrical, and manufacturing engineers, as well as continuous improvement based on field performance data. By staying up-to-date with the latest technologies, standards, and design methodologies, designers can create innovative and competitive electromechanical assemblies that drive business success.
0 Comments