Introduction to Flux Removers
Flux removers are essential tools in the electronics industry for cleaning and maintaining circuit boards and electronic components. They are used to remove flux residues left behind after soldering processes. Flux is a chemical agent that helps prevent oxidation and improve the flow of solder during the soldering process. However, the remnants of flux can cause corrosion, interfere with electrical conductivity, and degrade the performance of electronic devices over time. This is where flux removers come into play.
What is Flux?
Flux is a chemical compound that is applied to the surface of metals before soldering. Its primary purpose is to prevent oxidation and improve the wetting and flow of solder. There are different types of fluxes used in electronics manufacturing:
Flux Type | Description |
---|---|
Rosin | Made from pine tree sap, it is the most common type of flux used in electronics. It comes in various activities (mild, activated, highly activated) depending on the strength required for the application. |
Water-Soluble | As the name suggests, this type of flux is soluble in water and can be easily cleaned using water or a mild detergent solution. It is often used in wave soldering processes. |
No-Clean | This type of flux leaves minimal residue and does not require cleaning after soldering. It is commonly used in surface mount technology (SMT) assembly. |
While flux plays a crucial role in the soldering process, it leaves behind residues that can be harmful to electronic devices if not properly removed.
Why is Flux Removal Important?
Flux removal is a critical step in the electronics manufacturing process for several reasons:
-
Corrosion Prevention: Flux residues are acidic and can cause corrosion of metal surfaces over time. This can lead to damaged components, short circuits, and device failures.
-
Improved Conductivity: Flux residues can interfere with the electrical conductivity of contacts and connectors. Removing these residues ensures optimal signal transmission and device performance.
-
Enhanced Reliability: Properly cleaned electronic assemblies have higher reliability and longer lifespans compared to those with flux residues left behind.
-
Aesthetics: Flux residues can be unsightly and give the impression of poor workmanship. Removing these residues results in a cleaner, more professional-looking end product.
-
Compliance with Standards: Many industries, such as aerospace, military, and medical devices, have strict cleanliness requirements for electronic assemblies. Proper flux removal helps meet these standards.
Types of Flux Removers
There are several types of flux removers available, each with its own advantages and applications. The choice of flux remover depends on the type of flux used, the substrate material, and the cleaning method employed.
Solvent-Based Flux Removers
Solvent-based flux removers are the most common type used in the electronics industry. They are effective at dissolving and removing a wide range of flux residues. These removers typically contain a blend of organic solvents, such as alcohols, esters, and hydrocarbons.
Advantages of solvent-based flux removers:
– Fast-acting and efficient at removing flux residues
– Compatible with most types of fluxes and substrate materials
– Can be used in manual or automated cleaning processes
Disadvantages of solvent-based flux removers:
– Flammable and require proper ventilation and safety precautions
– May attack some plastics and sensitive components
– Disposal of spent solvents can be costly and environmentally challenging
Some examples of solvent-based flux removers include isopropyl alcohol (IPA), denatured alcohol, and specialized formulations like MG Chemicals 4140 Flux Remover.
Aqueous Flux Removers
Aqueous flux removers are water-based solutions that are effective at removing water-soluble fluxes. They often contain surfactants, detergents, and other additives to enhance their cleaning performance.
Advantages of aqueous flux removers:
– Non-flammable and generally safer to use compared to solvent-based removers
– Environmentally friendly and easier to dispose of
– Can be used in ultrasonic and batch cleaning processes
Disadvantages of aqueous flux removers:
– Limited effectiveness on non-water-soluble fluxes
– May require longer cleaning times and elevated temperatures
– Can promote corrosion if not properly rinsed and dried
Examples of aqueous flux removers include Kyzen Aquanox A4520 and Zestron FA+.
Aerosol Flux Removers
Aerosol flux removers are pressurized cans that dispense the cleaning solvent as a fine mist or spray. They are convenient for spot cleaning and hard-to-reach areas on circuit boards.
Advantages of aerosol flux removers:
– Easy to use and portable
– Precise application for targeted cleaning
– Quick-drying and residue-free
Disadvantages of aerosol flux removers:
– Limited capacity compared to bulk containers
– Flammable propellants and solvents require proper ventilation
– Not suitable for large-scale cleaning operations
Examples of aerosol flux removers include Chemtronics Flux-Off and MG Chemicals Super Flux Remover.
Flux Removal Methods
There are several methods for removing flux residues from electronic assemblies, each with its own advantages and considerations.
Manual Cleaning
Manual cleaning involves using a brush, swab, or wipe to apply the flux remover and scrub the surface of the board or component. This method is suitable for small-scale cleaning tasks and hard-to-reach areas.
Advantages of manual cleaning:
– Low initial investment in equipment
– Flexibility to clean specific areas or components
– Suitable for prototypes and low-volume production
Disadvantages of manual cleaning:
– Labor-intensive and time-consuming
– Inconsistent results depending on operator skill
– Risk of damage to delicate components
Ultrasonic Cleaning
Ultrasonic cleaning uses high-frequency sound waves to agitate a cleaning solution, creating microscopic bubbles that implode and release energy to dislodge contaminants from surfaces. This method is effective for removing stubborn flux residues and cleaning intricate geometries.
Advantages of ultrasonic cleaning:
– Thorough and consistent cleaning results
– Suitable for batch processing of multiple boards or components
– Can penetrate hard-to-reach areas and cavities
Disadvantages of ultrasonic cleaning:
– Higher initial equipment costs
– Potential for damage to sensitive components due to cavitation
– Requires post-cleaning rinsing and drying steps
Spray Cleaning
Spray cleaning involves using a pressurized spray system to apply the flux remover onto the surface of the board or component. This method is efficient for larger-scale cleaning operations and can be automated for consistency.
Advantages of spray cleaning:
– Fast and efficient cleaning of large surface areas
– Can be automated for high-volume production
– Consistent and repeatable results
Disadvantages of spray cleaning:
– Higher initial equipment costs
– Requires proper ventilation and containment of overspray
– May not effectively clean hard-to-reach areas or cavities
Vapor Degreasing
Vapor degreasing is a cleaning method that uses the vapors of a boiling solvent to condense on the surface of the board or component, dissolving and removing flux residues. This method is highly effective and leaves minimal residue.
Advantages of vapor degreasing:
– Thorough and consistent cleaning results
– Minimal residue and fast drying times
– Can clean complex geometries and cavities
Disadvantages of vapor degreasing:
– High initial equipment costs
– Requires the use of specialized solvents
– Potential for solvent emissions and environmental concerns
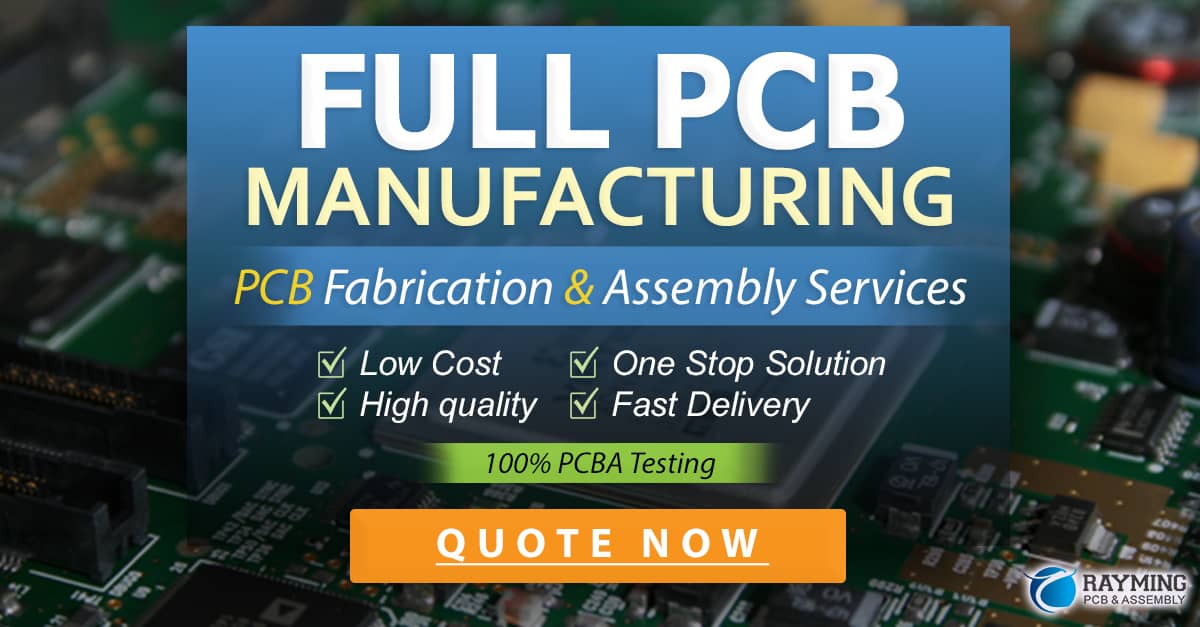
Choosing the Right Flux Remover
Selecting the appropriate flux remover depends on several factors:
-
Type of Flux: Consider the type of flux used in the soldering process (rosin, water-soluble, no-clean) and choose a remover that is compatible and effective.
-
Substrate Material: Ensure that the flux remover is safe to use on the specific substrate material (PCB, components, plastics) without causing damage or degradation.
-
Cleaning Method: Choose a flux remover that is suitable for the intended cleaning method (manual, ultrasonic, spray, vapor degreasing) and compatible with the available equipment.
-
Environmental and Safety Considerations: Consider the environmental impact and safety requirements of the flux remover, such as flammability, toxicity, and disposal regulations.
-
Cost and Availability: Evaluate the cost and availability of the flux remover, considering factors such as consumption rate, shelf life, and supplier reliability.
Best Practices for Flux Removal
To ensure effective and safe flux removal, follow these best practices:
-
Read and Follow Manufacturer’s Instructions: Always read and adhere to the manufacturer’s guidelines for the specific flux remover, including recommended dilution ratios, application methods, and safety precautions.
-
Use Appropriate Personal Protective Equipment (PPE): Wear suitable gloves, eye protection, and respiratory protection when handling flux removers to minimize exposure to chemicals.
-
Ensure Proper Ventilation: Work in a well-ventilated area or use a fume extraction system to prevent the accumulation of solvent vapors and ensure a safe working environment.
-
Avoid Excessive Cleaning: Overcleaning or using excessively aggressive flux removers can damage components or substrate materials. Use the mildest effective cleaning method and remover.
-
Properly Dispose of Waste: Follow local regulations for the proper disposal of spent flux removers and contaminated cleaning materials to minimize environmental impact.
FAQ
-
What is the difference between flux and solder paste?
Flux is a chemical compound used to prevent oxidation and improve the flow of solder during the soldering process. Solder paste is a mixture of powdered solder and flux used in surface mount assembly for attaching components to the circuit board. -
Can I use isopropyl alcohol to remove flux residues?
Isopropyl alcohol (IPA) is a common solvent used for removing flux residues, especially for rosin-based fluxes. However, it may not be effective for all types of fluxes, and its use should be verified for compatibility with the specific flux and substrate materials. -
How often should I clean my soldering iron tip?
Soldering iron tips should be cleaned frequently to remove flux residues and prevent oxidation. It is recommended to clean the tip before each use, during prolonged soldering sessions, and after completing the soldering task. -
Can I reuse spent flux remover?
It is not recommended to reuse spent flux remover as it may have accumulated contaminants and lost its effectiveness over time. Always use fresh flux remover for optimal cleaning results and to avoid potential contamination of the cleaned surface. -
Are there any eco-friendly alternatives to traditional flux removers?
Yes, there are several eco-friendly alternatives available, such as water-based flux removers and biodegradable solvents. These options minimize the environmental impact and often have lower toxicity compared to traditional solvent-based flux removers.
Conclusion
Flux removers are essential tools in the electronics industry for maintaining the cleanliness, performance, and reliability of electronic assemblies. They remove flux residues left behind after soldering processes, preventing corrosion, improving conductivity, and enhancing the overall quality of the end product.
Choosing the right flux remover depends on factors such as the type of flux, substrate material, cleaning method, environmental and safety considerations, and cost. It is important to follow best practices, including adhering to manufacturer’s instructions, using appropriate personal protective equipment, ensuring proper ventilation, avoiding excessive cleaning, and properly disposing of waste.
By understanding the types of flux removers, cleaning methods, and best practices, electronics manufacturers can effectively remove flux residues and ensure the production of high-quality, reliable electronic devices.
0 Comments