Introduction to PCB SMT
Surface Mount Technology (SMT) has revolutionized the electronics manufacturing industry by offering numerous advantages over traditional through-hole mounting techniques. PCB SMT, which involves mounting components directly onto the surface of a printed circuit board (PCB), has become the preferred method for assembling electronic devices due to its efficiency, reliability, and cost-effectiveness. In this article, we will explore the various advantages of PCB SMT and how it has transformed the electronics industry.
PCB SMT Advantages
1. Miniaturization and Space Savings
One of the most significant advantages of PCB SMT is its ability to facilitate miniaturization and space savings. SMT components are much smaller than their through-hole counterparts, allowing for more compact and densely packed PCB designs. This is particularly important in today’s electronic devices, where consumers demand smaller, lighter, and more portable products.
Component Type | Size Comparison |
---|---|
Through-hole | Larger |
SMT | Smaller |
The smaller size of SMT components enables designers to create more complex and feature-rich devices in smaller form factors. This space-saving advantage is crucial in applications such as smartphones, wearables, and IoT devices, where every millimeter counts.
2. Increased Reliability and Durability
PCB SMT offers increased reliability and durability compared to through-hole mounting. SMT components have shorter leads and are directly soldered onto the PCB surface, resulting in stronger mechanical bonds and reduced susceptibility to vibration and thermal stress. This makes SMT assemblies more resilient and less likely to suffer from connection failures or component damage.
Additionally, SMT allows for the use of advanced packaging techniques, such as Ball Grid Array (BGA) and Quad Flat No-lead (QFN), which further enhance the reliability and durability of electronic assemblies. These packaging techniques provide better thermal dissipation, improved electrical performance, and greater resistance to environmental factors like moisture and dust.
3. Faster Assembly and Higher Throughput
SMT assembly processes are highly automated, allowing for faster assembly speeds and higher throughput compared to through-hole mounting. SMT pick-and-place machines can rapidly and accurately place components onto the PCB surface, significantly reducing the time required for manual insertion and soldering.
Assembly Method | Throughput Comparison |
---|---|
Through-hole | Lower |
SMT | Higher |
The increased automation in SMT assembly also leads to more consistent and reliable results, as human error is minimized. This higher throughput enables manufacturers to produce larger quantities of PCBs in shorter timeframes, meeting the growing demand for electronic devices in various industries.
4. Cost-Effectiveness and Reduced Material Usage
PCB SMT offers cost advantages over through-hole mounting due to several factors. First, SMT components are generally less expensive than their through-hole counterparts, as they require less material and are manufactured in larger quantities. Second, the automated nature of SMT assembly reduces labor costs and minimizes the need for manual intervention.
Moreover, SMT allows for the use of smaller PCBs, which translates to reduced material usage and lower production costs. The smaller footprint of SMT components also enables designers to optimize PCB layouts, further reducing material waste and improving overall cost-effectiveness.
5. Improved Electrical Performance
SMT components offer improved electrical performance compared to through-hole components. The shorter leads and direct surface mounting of SMT components reduce parasitic inductance and capacitance, resulting in better signal integrity and faster signal propagation. This is particularly important in high-frequency applications, such as wireless communication devices and high-speed digital circuits.
Additionally, SMT allows for the use of advanced PCB materials and manufacturing techniques, such as high-density interconnect (HDI) and embedded components, which further enhance the electrical performance of electronic assemblies. These advancements enable designers to create more sophisticated and high-performance devices that meet the demands of modern applications.
6. Design Flexibility and Innovation
PCB SMT offers greater design flexibility and enables innovation in electronic product development. The smaller size and improved performance of SMT components allow designers to create more complex and feature-rich devices with advanced functionalities. SMT also facilitates the integration of multiple components into a single package, such as system-on-chip (SoC) and multi-chip modules (MCM), enabling more compact and efficient designs.
Furthermore, SMT supports the use of flexible and rigid-Flex PCBs, which can be bent, folded, or shaped to fit into unique form factors. This design flexibility is crucial in applications such as wearables, medical devices, and automotive electronics, where space constraints and ergonomic considerations are paramount.
Frequently Asked Questions (FAQ)
1. What is the difference between through-hole and surface mount technology?
Through-hole technology involves inserting component leads through holes drilled in the PCB and soldering them on the opposite side. Surface mount technology, on the other hand, involves placing components directly onto the surface of the PCB and soldering them in place. SMT components are smaller, have shorter leads, and offer various advantages over through-hole components, such as space savings, improved reliability, and faster assembly.
2. Can through-hole and SMT components be used on the same PCB?
Yes, it is possible to use both through-hole and SMT components on the same PCB. This is known as a mixed-technology or hybrid assembly. Mixed-technology PCBs are commonly used when certain components, such as connectors or large power devices, are only available in through-hole packages or when a design requires the mechanical strength of through-hole mounting for specific components.
3. What are the challenges associated with PCB SMT?
While PCB SMT offers numerous advantages, it also presents some challenges. These include:
- Thermal management: SMT components generate more heat per unit area, requiring careful thermal design and management.
- Inspection and rework: SMT assemblies can be more difficult to inspect and rework due to the small size and close proximity of components.
- Moisture sensitivity: Some SMT components are moisture-sensitive and require proper handling and storage to prevent damage during the soldering process.
- Skilled operators: SMT assembly requires skilled operators and technicians to ensure proper process control and quality assurance.
4. How has PCB SMT impacted the electronics industry?
PCB SMT has revolutionized the electronics industry by enabling the production of smaller, more reliable, and more affordable electronic devices. The advantages of SMT, such as miniaturization, increased reliability, faster assembly, and cost-effectiveness, have driven the widespread adoption of this technology across various sectors, including consumer electronics, telecommunications, automotive, and medical devices. SMT has played a crucial role in the rapid advancement and proliferation of electronic products in our daily lives.
5. What are the future trends in PCB SMT?
The future of PCB SMT is driven by the continuous demand for smaller, more powerful, and more intelligent electronic devices. Some of the key trends shaping the future of PCB SMT include:
- Advanced packaging technologies: The adoption of advanced packaging techniques, such as 3D packaging, embedded components, and wafer-level packaging, will further enhance the miniaturization and performance of electronic assemblies.
- Increased automation and Industry 4.0: The integration of robotics, machine learning, and IoT technologies will lead to more intelligent and adaptive SMT assembly processes, improving efficiency and quality control.
- Sustainable and eco-friendly practices: There will be a growing emphasis on sustainable PCB design and manufacturing practices, including the use of lead-free solders, recyclable materials, and energy-efficient processes.
- 5G and IoT proliferation: The widespread deployment of 5G networks and the growth of the Internet of Things (IoT) will drive the demand for more complex and high-performance PCB assemblies, leveraging the advantages of SMT.
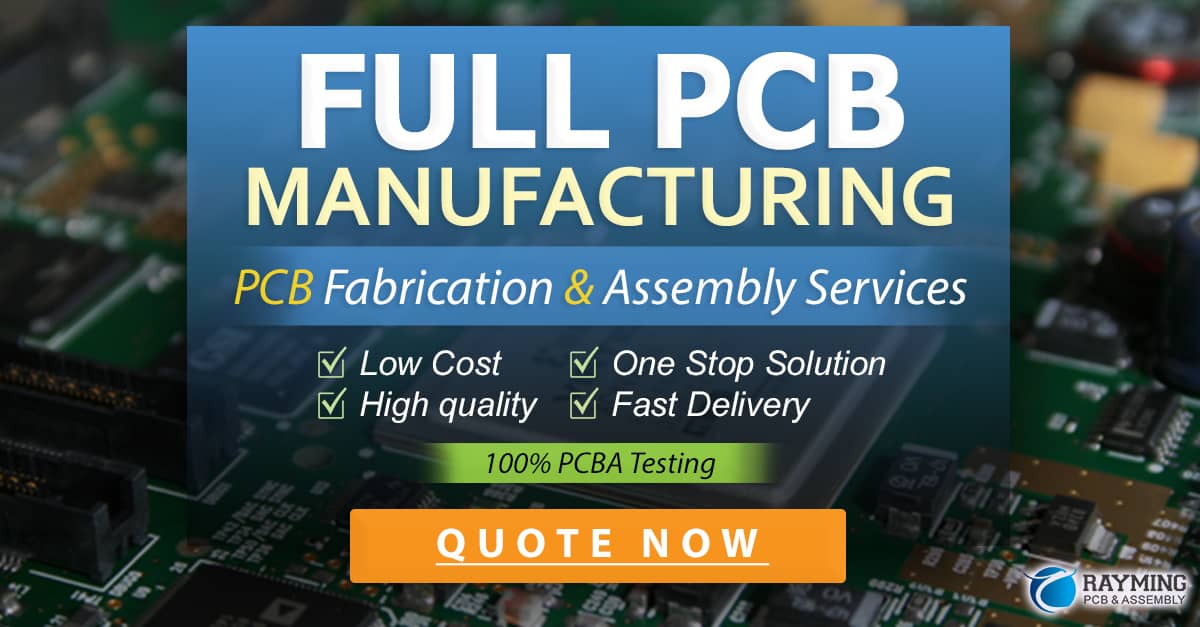
Conclusion
PCB SMT has emerged as the dominant technology in electronics manufacturing, offering a wide range of advantages over traditional through-hole mounting. From miniaturization and space savings to increased reliability, faster assembly, and cost-effectiveness, SMT has transformed the way electronic devices are designed and produced. As the electronics industry continues to evolve, PCB SMT will remain at the forefront, enabling the development of more advanced, efficient, and innovative products that shape our future.
0 Comments