Introduction to Vias and Tented Vias
Vias are an essential component in printed circuit board (PCB) design, allowing electrical connections between different layers of a multi-layer PCB. A via consists of a drilled hole that is electroplated with a conductive material, typically copper, to create an electrical pathway. Tented vias are a specific type of via where the hole is covered, or “tented,” with solder mask on one or both sides of the PCB.
Types of Vias
There are several types of vias used in PCB design:
Via Type | Description |
---|---|
Through Hole Via | A via that goes through all layers of the PCB |
Blind Via | A via that connects an outer layer to an inner layer, but does not go through the entire board |
Buried Via | A via that connects inner layers without reaching either outer layer |
Microvia | A small via, typically less than 0.15mm in diameter, used for high-density interconnects |
Tented Via | A via covered with solder mask on one or both sides of the PCB |
Advantages of Tented Vias
Tented vias offer several advantages over non-tented vias in PCB design and manufacturing:
1. Improved Solder Mask Coverage
By covering the via with solder mask, tented vias provide better protection against solder bridging and short circuits during the soldering process. This is particularly important for vias located close to SMD pads, as the solder mask tent prevents solder from flowing into the via hole.
2. Enhanced Mechanical Strength
Tented vias add mechanical strength to the PCB by reinforcing the area around the via. This is especially beneficial for vias located in high-stress areas, such as near connectors or in boards subjected to vibration or physical stress.
3. Increased Copper Tear-out Resistance
Tenting Vias can help prevent copper tear-out, a phenomenon where the copper plating inside the via barrel separates from the PCB due to thermal or mechanical stress. By covering the via with solder mask, the copper barrel is better supported and less likely to separate from the board.
4. Improved Electrical Insulation
Solder mask is an electrical insulator, so tenting vias provides an additional layer of insulation between the via and the surrounding components. This can help prevent short circuits and improve the overall electrical reliability of the PCB.
5. Better Aesthetics
Tented vias create a cleaner, more uniform appearance on the PCB surface by hiding the via holes beneath the solder mask. This can be particularly important for boards with a high number of vias or those used in consumer-facing products.
Disadvantages of Tented Vias
While tented vias offer many benefits, there are also some potential drawbacks to consider:
1. Increased Manufacturing Complexity
Tenting vias adds an extra step to the PCB manufacturing process, as the solder mask must be applied over the via holes. This can increase production time and cost, especially for boards with a high number of vias.
2. Potential for Solder Mask Defects
If the solder mask is not applied correctly, it can lead to defects such as pinholes, bubbles, or thin spots in the solder mask tent. These defects can compromise the protective benefits of tenting and potentially lead to reliability issues.
3. Difficulty in Probing and Testing
Tented vias can make it more challenging to probe and test the PCB during manufacturing and troubleshooting, as the via holes are covered by solder mask. This may require specialized probing techniques or the use of test points to access the necessary signals.
4. Reduced Heat Dissipation
In some cases, tenting vias can reduce the heat dissipation capabilities of the via, as the solder mask acts as a thermal insulator. This can be a concern for high-power or high-frequency applications where efficient heat transfer is critical.
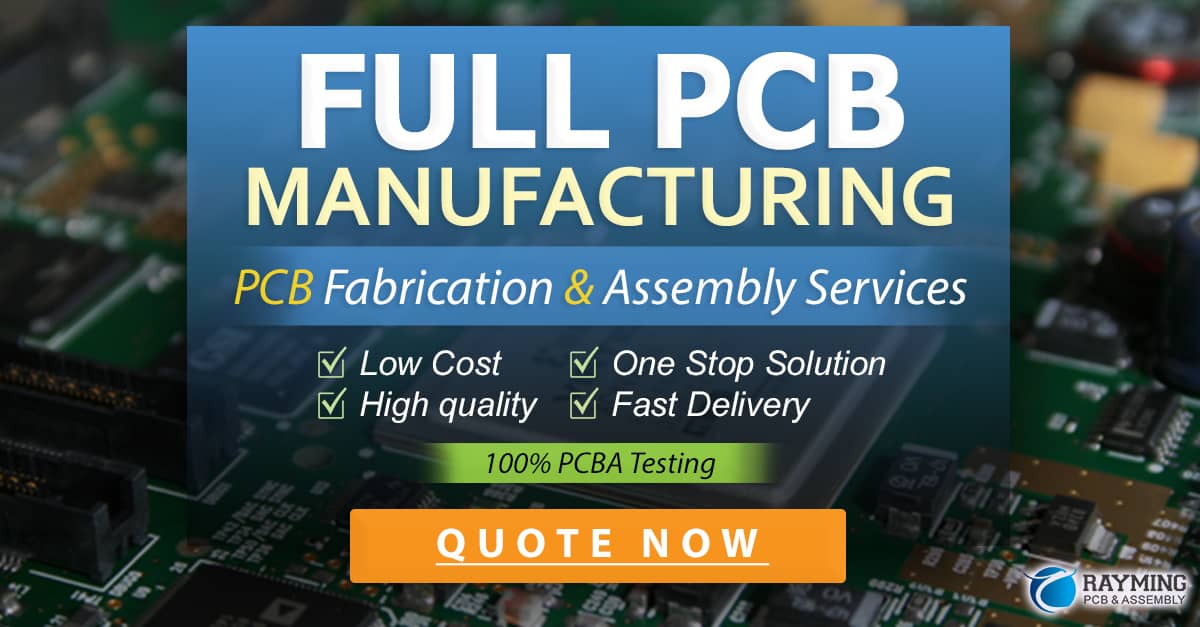
Tented Via Design Considerations
When incorporating tented vias into a PCB design, there are several factors to consider:
1. Solder Mask Clearance
Ensure that there is sufficient clearance between the via and the surrounding solder mask to allow for proper tenting. The solder mask clearance should be specified in the PCB design software and communicated to the manufacturer.
2. Via Size and Aspect Ratio
The size and aspect ratio of the via can affect the reliability of the solder mask tent. Smaller vias with higher aspect ratios (hole depth to diameter ratio) can be more challenging to tent consistently. Work with your PCB manufacturer to determine the optimal via size and aspect ratio for your design.
3. Solder Mask Material
The choice of solder mask material can impact the performance and reliability of tented vias. Some solder mask materials may be more prone to defects or have different thermal and mechanical properties. Consult with your PCB manufacturer to select the best solder mask material for your application.
4. Via Placement
When placing tented vias, consider their proximity to other components, traces, and copper features. Ensure that there is sufficient clearance to prevent short circuits and allow for proper solder mask coverage.
5. Manufacturing Capabilities
Verify that your PCB manufacturer has the capability and experience to produce tented vias consistently and reliably. Discuss your requirements and any specific concerns with the manufacturer early in the design process.
Tented Vias in High-Frequency PCBs
Tented vias can be particularly beneficial in high-frequency PCB designs, such as those used in RF and microwave applications. In these designs, vias can act as unwanted antennas, radiating electromagnetic energy and causing signal integrity issues.
By tenting the vias, the solder mask helps to suppress this radiation and minimize the antenna effect. This can lead to improved signal integrity, reduced crosstalk, and better overall performance of the high-frequency circuit.
However, it’s important to note that tenting vias in high-frequency designs may also have some drawbacks. The solder mask material can have a higher dielectric constant than air, which can affect the impedance of the via and lead to signal reflections. Additionally, the solder mask can introduce losses at higher frequencies, which may need to be accounted for in the design.
To mitigate these issues, high-frequency PCB designers may use specialized solder mask materials with lower dielectric constants or employ other techniques, such as back-drilling, to remove the unused portion of the via stub.
Tented Vias in Flex and Rigid-Flex PCBs
Tented vias can also be used in flexible and rigid-flex PCB designs, offering similar benefits as in rigid PCBs. In these applications, tented vias can help improve the mechanical integrity of the via, especially in areas subjected to bending or flexing.
However, the use of tented vias in flex and rigid-flex designs requires careful consideration of the solder mask material and the flexibility requirements of the board. The solder mask must be able to withstand the repeated bending and flexing without cracking or delaminating from the via.
Specialized flexible solder mask materials, such as polyimide or acrylic-based masks, are often used in these applications to ensure the reliability and durability of the tented vias.
Tented Vias vs. Plugged Vias
Another method for covering via holes is via plugging, which involves filling the via with a non-conductive material, such as epoxy or resin. Plugged vias offer some of the same benefits as tented vias, such as improved solder mask coverage and increased mechanical strength.
However, there are some key differences between tented and plugged vias:
Characteristic | Tented Vias | Plugged Vias |
---|---|---|
Material | Solder mask | Epoxy or resin |
Process | Applied during solder mask stage | Separate via filling process |
Electrical Insulation | Good | Excellent |
Mechanical Strength | Good | Excellent |
Cost | Lower | Higher |
Manufacturability | Easier | More complex |
The choice between tented and plugged vias depends on the specific requirements of the PCB design, such as the level of electrical insulation and mechanical strength needed, as well as the manufacturing capabilities and cost constraints.
FAQ
1. Can tented vias be used in high-current applications?
Yes, tented vias can be used in high-current applications, but the via size and copper plating thickness must be designed to handle the required current. The solder mask tent does not significantly affect the current-carrying capacity of the via.
2. How does the solder mask thickness affect the reliability of tented vias?
A thicker solder mask can provide better coverage and protection for the via, but it may also increase the stress on the via during thermal cycling. The optimal solder mask thickness depends on the specific PCB design and manufacturing process.
3. Can tented vias be used in PCBs with surface finishes like ENIG or OSP?
Yes, tented vias can be used with various surface finishes, including ENIG (electroless nickel immersion gold) and OSP (organic solderability preservative). However, the compatibility of the solder mask and surface finish materials should be verified with the PCB manufacturer.
4. Are there any specific design rules for tented vias?
Design rules for tented vias may vary depending on the PCB manufacturer and the specific application. Generally, the via size, solder mask clearance, and aspect ratio should be discussed with the manufacturer to ensure optimal results. Some manufacturers may have specific guidelines or limitations for tented vias.
5. How can I specify tented vias in my PCB design files?
Tented vias are typically specified in the solder mask layer of the PCB design files. Most PCB design software packages have options to define the solder mask clearance and via tenting requirements. Consult your design software documentation and work with your PCB manufacturer to ensure the correct specification of tented vias in your design files.
Conclusion
Tented vias are a valuable technique in PCB design, offering numerous benefits such as improved solder mask coverage, enhanced mechanical strength, and better electrical insulation. By carefully considering the design requirements and manufacturing process, PCB designers can effectively incorporate tented vias to improve the reliability and performance of their boards.
As with any PCB design decision, it’s essential to work closely with your PCB manufacturer to ensure that your tented via requirements are clearly communicated and that the manufacturer has the capability and expertise to deliver high-quality results.
By understanding the advantages, disadvantages, and design considerations associated with tented vias, PCB designers can make informed decisions and create more robust, reliable, and high-performing printed circuit boards.
0 Comments