Introduction to PCBs
Printed Circuit Boards (PCBs) are the backbone of modern electronics. They are used in almost every electronic device, from smartphones and computers to medical equipment and aerospace technology. PCBs are flat boards made of insulating material, such as fiberglass, with conductive tracks, pads, and other features etched onto the surface. These boards are used to mechanically support and electrically connect electronic components using conductive pathways, tracks, or signal traces etched from copper sheets laminated onto a non-conductive substrate.
Types of PCBs
There are several types of PCBs, each with its own unique features and applications. The most common types of PCBs include:
-
Single-sided PCBs: These have conductive tracks on one side of the board only. They are the simplest and most cost-effective PCBs.
-
Double-sided PCBs: These have conductive tracks on both sides of the board, allowing for more complex circuits and higher component density.
-
Multi-layer PCBs: These have multiple layers of conductive tracks separated by insulating layers. They are used for complex, high-density applications.
-
Flexible PCBs: These are made from flexible materials, such as polyimide, and can be bent or folded to fit into tight spaces.
-
Rigid-Flex PCBs: These combine rigid and flexible sections, allowing for more design freedom and improved reliability.
What are HDI PCBs?
High Density Interconnect (HDI) PCBs are a type of PCB that offers higher wiring density than traditional PCBs. They are characterized by their fine lines and spaces, small vias, and capture pads. HDI PCBs allow for more complex circuits to be built on smaller boards, making them ideal for applications where space is limited, such as smartphones, wearables, and medical devices.
Features of HDI PCBs
HDI PCBs have several features that set them apart from traditional PCBs:
-
Fine lines and spaces: HDI PCBs have trace widths and spaces of 100 microns or less, compared to 200 microns or more for traditional PCBs.
-
Micro vias: HDI PCBs use small, laser-drilled vias with diameters of 150 microns or less, compared to 250 microns or more for traditional PCBs.
-
Blind and buried vias: HDI PCBs often use blind and buried vias, which are vias that do not go through the entire board. This allows for more efficient use of board space and reduces signal interference.
-
Sequential lamination: HDI PCBs are often built using sequential lamination, where layers are added one at a time, allowing for more complex designs and better signal integrity.
Benefits of HDI PCBs
HDI PCBs offer several benefits over traditional PCBs:
-
Miniaturization: HDI PCBs allow for smaller, more compact designs, which is essential for many modern applications.
-
Increased functionality: With higher wiring density, HDI PCBs can accommodate more components and more complex circuits in a smaller space.
-
Improved signal integrity: The smaller features and reduced layer count of HDI PCBs result in shorter signal paths and reduced crosstalk, improving signal integrity.
-
Lower power consumption: The shorter signal paths in HDI PCBs result in lower resistance and capacitance, which reduces power consumption.
-
Higher reliability: HDI PCBs have fewer interconnects and shorter signal paths, which reduces the risk of failures and improves reliability.
Applications of HDI PCBs
HDI PCBs are used in a wide range of applications, including:
-
Consumer electronics: Smartphones, tablets, wearables, and other portable devices.
-
Medical devices: Implantable devices, diagnostic equipment, and wearable health monitors.
-
Automotive electronics: Advanced driver assistance systems (ADAS), infotainment systems, and electric vehicle power management.
-
Aerospace and defense: Avionics, satellite communications, and military equipment.
-
Industrial automation: Robotics, machine vision systems, and process control equipment.
Designing HDI PCBs
Designing HDI PCBs requires specialized knowledge and tools. Some key considerations when designing HDI PCBs include:
Design Rules
HDI PCBs have tighter design rules than traditional PCBs, with smaller feature sizes and more stringent requirements for clearances and tolerances. Designers must carefully adhere to these rules to ensure manufacturability and reliability.
Layer Stack-up
The layer stack-up of an HDI PCB is critical to its performance. Designers must carefully consider the number and arrangement of layers, the materials used, and the via structure to optimize signal integrity and manufacturability.
Signal Integrity
With the smaller features and higher wiring density of HDI PCBs, signal integrity becomes a critical concern. Designers must use advanced simulation and analysis tools to ensure that signals maintain their integrity across the board.
Thermal Management
The high component density of HDI PCBs can lead to increased heat generation. Designers must consider thermal management strategies, such as the use of thermal vias, heat spreaders, and high thermal conductivity materials.
Manufacturing Considerations
HDI PCBs require specialized manufacturing processes, such as laser drilling and sequential lamination. Designers must work closely with their manufacturing partners to ensure that their designs are optimized for these processes and can be reliably manufactured at scale.
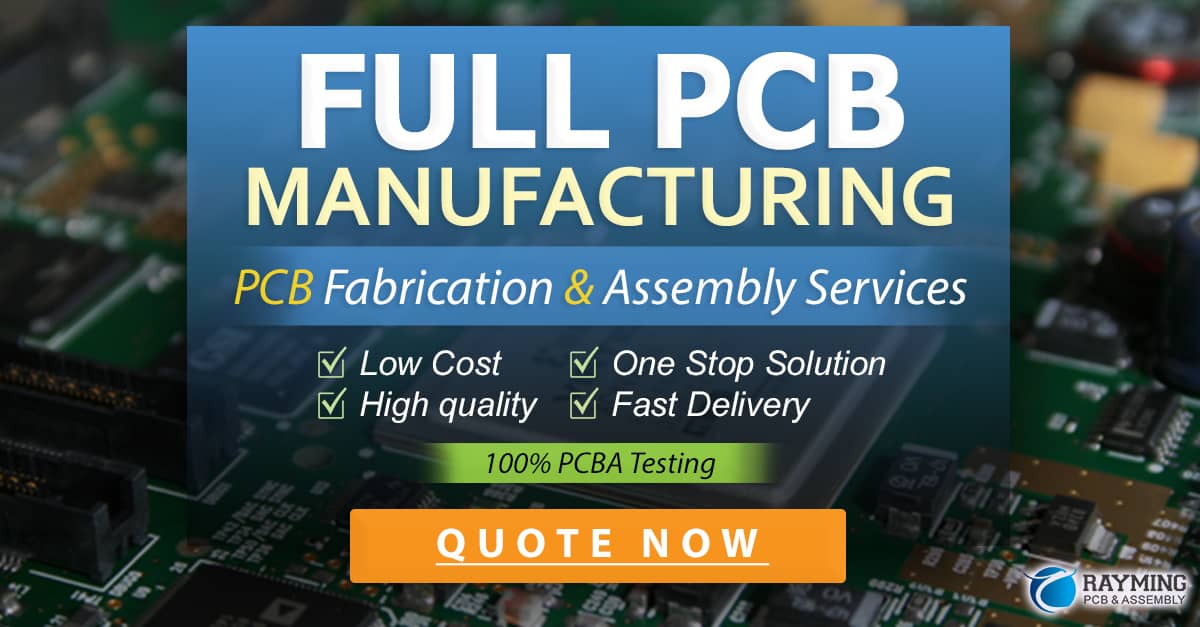
Manufacturing HDI PCBs
Manufacturing HDI PCBs requires specialized equipment and processes. Some key steps in the HDI PCB manufacturing process include:
Laser Drilling
HDI PCBs use small, laser-drilled vias to connect layers. These vias are typically drilled using UV or CO2 lasers, which can create holes as small as 50 microns in diameter.
Sequential Lamination
HDI PCBs are often built using sequential lamination, where layers are added one at a time. This allows for the creation of blind and buried vias and enables more complex designs.
Plating
After the layers are laminated, the vias are plated with copper to create electrical connections between layers. This is typically done using electroless copper plating, followed by electrolytic copper plating.
Patterning
The outer layers of the PCB are patterned using photolithography and etching processes. This creates the fine lines and spaces that are characteristic of HDI PCBs.
Solder Mask and Silkscreen
A solder mask is applied to the board to protect the copper traces and prevent solder bridging. A silkscreen layer is then added to provide labeling and identification of components.
Testing and Inspection
HDI PCBs undergo rigorous testing and inspection to ensure that they meet the required specifications and are free of defects. This includes electrical testing, visual inspection, and automated optical inspection (AOI).
Challenges and Future Trends
While HDI PCBs offer many benefits, they also present some challenges and opportunities for future development.
Cost
HDI PCBs are more expensive to manufacture than traditional PCBs due to the specialized equipment and processes required. However, as demand for HDI PCBs continues to grow, economies of scale are expected to drive down costs over time.
Supply Chain
The specialized materials and equipment used in HDI PCB manufacturing can create Supply Chain Challenges, particularly during periods of high demand or disruption. Manufacturers and designers must work closely with their suppliers to ensure a stable and reliable supply of materials and components.
Emerging Technologies
New technologies are emerging that could further enhance the capabilities of HDI PCBs. For example, embedded components, such as resistors and capacitors, can be integrated directly into the PCB, reducing the need for surface-mounted components and enabling even greater miniaturization.
Sustainability
As with all electronics manufacturing, sustainability is an increasingly important consideration for HDI PCBs. Manufacturers are exploring ways to reduce waste, increase recycling, and use more environmentally friendly materials and processes.
Frequently Asked Questions (FAQ)
-
What is the difference between HDI PCBs and traditional PCBs?
HDI PCBs have finer features, such as smaller vias, narrower traces, and tighter spacing, compared to traditional PCBs. This allows for higher wiring density and more complex designs in a smaller form factor. -
What are the advantages of using HDI PCBs?
The main advantages of HDI PCBs are miniaturization, increased functionality, improved signal integrity, lower power consumption, and higher reliability. -
What are some common applications for HDI PCBs?
HDI PCBs are commonly used in consumer electronics, medical devices, automotive electronics, aerospace and defense, and industrial automation. -
What are the key considerations when designing HDI PCBs?
When designing HDI PCBs, key considerations include design rules, layer stack-up, signal integrity, thermal management, and manufacturing considerations. -
What are some of the challenges and future trends for HDI PCBs?
Some challenges for HDI PCBs include cost, supply chain issues, and sustainability concerns. Future trends include the integration of emerging technologies, such as embedded components, and a focus on environmentally friendly materials and processes.
Conclusion
HDI PCBs offer a powerful solution for the demands of modern electronics, enabling higher wiring density, improved signal integrity, and greater miniaturization. While they present some challenges in terms of design, manufacturing, and cost, the benefits of HDI PCBs make them an increasingly attractive option for a wide range of applications.
As technologies continue to evolve and new applications emerge, HDI PCBs are poised to play a central role in shaping the future of electronics. By understanding the capabilities, challenges, and opportunities presented by HDI PCBs, designers and manufacturers can unlock new possibilities and drive innovation in their products and services.
Feature | Traditional PCBs | HDI PCBs |
---|---|---|
Trace width/spacing | ≥ 200 μm | ≤ 100 μm |
Via diameter | ≥ 250 μm | ≤ 150 μm |
Via type | Through-hole | Blind, buried, micro |
Layers | Fewer | More |
Density | Lower | Higher |
Applications | General purpose | High-density, high-performance |
Table 1: Comparison of key features between traditional PCBs and HDI PCBs.
In summary, HDI PCBs represent a significant advancement in PCB technology, offering a range of benefits that make them the perfect choice for demanding, high-performance applications. As the electronics industry continues to evolve, HDI PCBs will undoubtedly play a crucial role in enabling the next generation of innovative products and services.
0 Comments