Types of PCB Test Points
There are several types of PCB test points, each with its own specific purpose and design. Some of the most common types include:
Through-hole Test Points
Through-hole test points are small, plated holes drilled into the PCB. They allow direct access to specific signals or components using test probes or clips. These test points are often labeled on the PCB Silkscreen for easy identification.
Surface Mount Test Points
Surface mount test points are flat, exposed pads on the surface of the PCB. They provide access to signals or components for testing purposes without requiring holes to be drilled through the board. Surface mount test points are typically smaller than through-hole test points and are well-suited for high-density PCB designs.
Edge Connector Test Points
Edge connector test points are exposed pads or fingers located along the edge of a PCB. They are commonly used in PCBs that plug into a connector or socket, such as memory modules or expansion cards. Edge connector test points allow testing of the PCB without requiring it to be fully installed in the target system.
Bed-of-Nails Test Points
Bed-of-nails test points are used in automated testing systems where spring-loaded probes, arranged in a specific pattern (the “bed-of-nails”), make contact with designated test points on the PCB. This type of testing allows for quick and efficient testing of multiple points on the PCB simultaneously.
Importance of PCB Test Points
PCB test points serve several important functions throughout the life cycle of a PCB:
Manufacturing Quality Control
During PCB manufacturing, test points enable quick verification of the board’s functionality and help identify any defects or issues early in the production process. This quality control step helps reduce waste and improve overall manufacturing efficiency.
Troubleshooting and Debugging
When a PCB malfunctions, test points provide technicians with easy access to key signals and components, facilitating the troubleshooting and debugging process. By measuring voltages, currents, or waveforms at specific test points, technicians can isolate faults and identify the root cause of the problem more efficiently.
Performance Verification
Test points allow engineers to verify the performance of a PCB under various conditions. By monitoring signals at test points, engineers can ensure that the PCB operates within specified parameters and meets the required performance criteria.
In-system Programming and Calibration
Some PCBs include test points specifically designed for in-system programming (ISP) or calibration. These test points provide access to programming interfaces or calibration signals, allowing technicians to update firmware, adjust settings, or calibrate the PCB without removing it from the target system.
Designing PCB Test Points
When designing a PCB, it is important to consider the placement and layout of test points to ensure accessibility and minimize any potential impact on the board’s performance. Some key factors to consider include:
Accessibility
Test points should be easily accessible using standard test probes or clips. They should be placed in locations that do not interfere with other components or require special tools to access.
Signal Integrity
The placement of test points should not adversely affect the signal integrity of the PCB. Test points should be located away from sensitive traces or components to minimize any potential signal disturbances.
Labeling and Documentation
Test points should be clearly labeled on the PCB silkscreen and documented in the PCB schematic and layout files. This documentation helps technicians quickly identify and locate the appropriate test points during testing or troubleshooting.
Electrical Characteristics
When selecting test points, designers must consider the electrical characteristics of the signals being measured. Test points should be sized appropriately to accommodate the expected currents and voltages, and they should not introduce significant loading or distortion to the signals being measured.
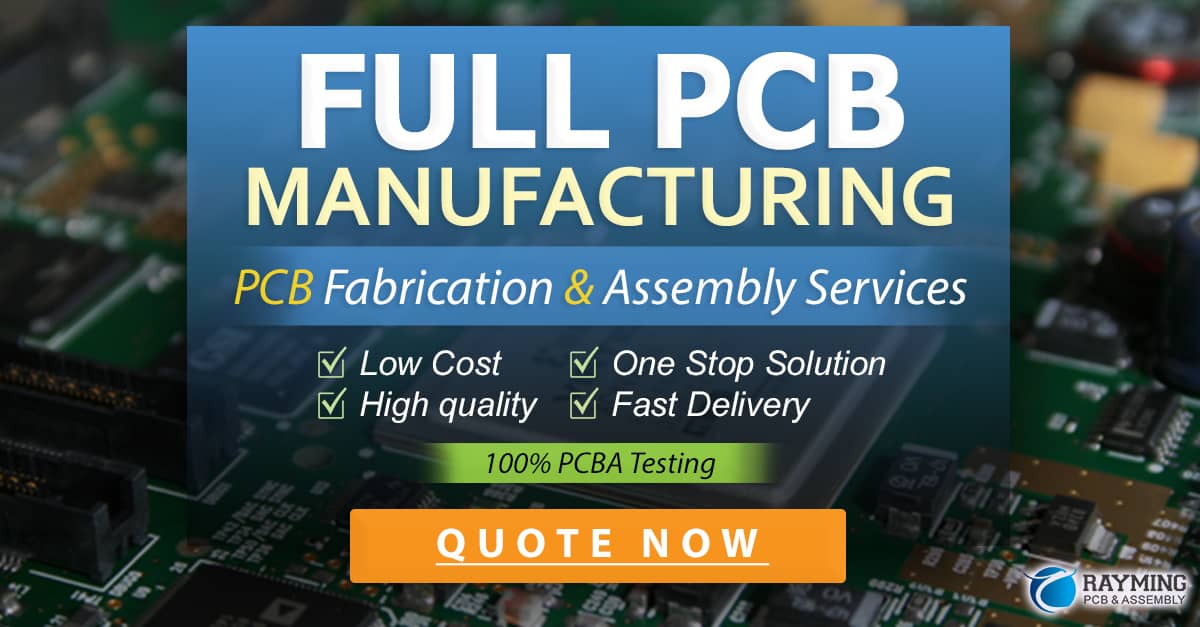
PCB Test Point Placement Strategies
Effective test point placement is crucial for ensuring efficient testing and troubleshooting of PCBs. Some common strategies for test point placement include:
Critical Signal Monitoring
Place test points on critical signals that are essential for the proper functioning of the PCB. These signals may include power supply rails, clock signals, reset lines, or key data buses.
Boundary Scan Chain
For complex PCBs with high component densities, designers may implement a boundary scan chain using test points. Boundary scan is a testing methodology that allows access to individual components on the PCB through a serial interface, enabling efficient testing and debugging.
Functional Block Isolation
Place test points at the boundaries of functional blocks within the PCB design. This strategy allows technicians to isolate and test specific sections of the PCB independently, making it easier to identify and resolve issues.
Power Distribution Network
Include test points at key locations in the power distribution network, such as voltage regulator outputs, power supply inputs, and ground points. These test points enable technicians to verify proper power delivery and identify any power-related issues.
Table – PCB Test Point Comparison
Test Point Type | Accessibility | Signal Integrity Impact | Size | Typical Use Cases |
---|---|---|---|---|
Through-hole | High | Low | Larger | General-purpose testing, power supply monitoring |
Surface Mount | Medium | Low to Medium | Smaller | High-density PCBs, signal probing |
Edge Connector | High | Low | Medium | PCBs with edge connectors, memory modules |
Bed-of-Nails | High | Low | Varies | Automated testing, high-volume production |
Frequently Asked Questions
1. What is the difference between a test point and a test pad?
A test point refers to any designated location on a PCB used for testing purposes, while a test pad specifically refers to a surface mount test point that is typically flat and exposed on the surface of the PCB.
2. How do I choose the right size for my test points?
The size of your test points should be based on the electrical characteristics of the signals being measured, the available space on the PCB, and the accessibility requirements for testing. Consult your PCB manufacturer or design guidelines for recommendations on test point sizes for your specific application.
3. Can test points affect the signal integrity of my PCB?
Yes, poorly placed test points can introduce signal disturbances or loading effects that may impact the performance of your PCB. To minimize these effects, place test points away from sensitive traces or components and consider the electrical characteristics of the signals being measured.
4. How many test points should I include on my PCB?
The number of test points required depends on the complexity of your PCB, the critical signals that need to be monitored, and the testing and troubleshooting requirements. As a general rule, include test points for all critical signals and at the boundaries of functional blocks to facilitate efficient testing and debugging.
5. Are there any industry standards for PCB test point design?
While there are no universally adopted standards for PCB test point design, many companies and organizations have developed their own internal guidelines and best practices. Some relevant standards, such as IPC-2221 and IPC-7351, provide guidance on PCB design and land pattern recommendations that can be applied to test point design.
In conclusion, PCB test points are essential elements in the design, manufacturing, and maintenance of printed circuit boards. They provide convenient access to critical signals and components, enabling efficient testing, troubleshooting, and performance verification. By carefully considering the placement, accessibility, and electrical characteristics of test points, PCB designers can optimize their designs for improved manufacturing quality control, easier debugging, and better overall system performance.
0 Comments