Why are PCB Stiffeners Important?
PCB stiffeners are essential for several reasons:
-
Preventing Warping and Bending: PCBs are prone to warping and bending due to various factors such as thermal stress, mechanical stress, and moisture absorption. Stiffeners help maintain the flatness and dimensional stability of the PCB, ensuring proper functioning of the electronic components.
-
Enhancing Mechanical Strength: Stiffeners provide additional mechanical strength to the PCB, making it more resistant to physical damage, shock, and vibration. This is particularly important in applications where the device is subject to harsh environmental conditions or frequent handling.
-
Improving Thermal Management: Stiffeners can also act as heat sinks, helping to dissipate heat generated by electronic components on the PCB. By improving thermal management, stiffeners contribute to the overall reliability and longevity of the electronic device.
-
Facilitating Mounting and Assembly: PCB stiffeners often include features such as mounting holes, standoffs, and alignment pins, which simplify the process of mounting the PCB to the enclosure or other components of the device. This ensures proper alignment and secure attachment of the PCB within the system.
Types of PCB Stiffeners
There are several types of PCB stiffeners available, each with its own characteristics and applications:
1. Metal Stiffeners
Metal stiffeners are the most common type of PCB stiffeners. They are typically made from aluminum, stainless steel, or copper alloys. Metal stiffeners offer excellent mechanical strength, thermal conductivity, and dimensional stability. They are suitable for a wide range of applications, including:
- High-power electronic devices
- Aerospace and defense systems
- Automotive electronics
- Industrial control systems
Material | Thermal Conductivity (W/mK) | Coefficient of Thermal Expansion (ppm/°C) | Yield Strength (MPa) |
---|---|---|---|
Aluminum | 205 – 250 | 23.1 | 20 – 500 |
Stainless Steel | 16 – 24 | 10.1 – 17.3 | 215 – 1400 |
Copper | 385 – 400 | 16.5 | 33 – 400 |
2. Plastic Stiffeners
Plastic stiffeners are lightweight and cost-effective alternatives to metal stiffeners. They are typically made from high-performance thermoplastics such as polyethylene terephthalate (PET), polycarbonate (PC), or glass-reinforced epoxy (FR-4). Plastic stiffeners offer good electrical insulation, chemical resistance, and ease of fabrication. They are suitable for applications such as:
- Consumer electronics
- Medical devices
- Telecommunications equipment
- Portable devices
Material | Dielectric Constant | Dielectric Strength (kV/mm) | Tensile Strength (MPa) |
---|---|---|---|
PET | 3.0 – 3.2 | 17 – 21 | 55 – 75 |
PC | 2.8 – 3.1 | 15 – 67 | 55 – 75 |
FR-4 | 4.2 – 4.9 | 20 – 28 | 310 – 380 |
3. Composite Stiffeners
Composite stiffeners combine the advantages of both metal and plastic stiffeners. They typically consist of a metal core (e.g., aluminum) sandwiched between layers of high-performance thermoplastics (e.g., PET or PC). Composite stiffeners offer a balance of mechanical strength, thermal conductivity, and electrical insulation. They are suitable for applications that require a combination of these properties, such as:
- Automotive electronics
- Aerospace systems
- High-performance computing devices
- Telecommunications infrastructure
Material | Thermal Conductivity (W/mK) | Dielectric Constant | Tensile Strength (MPa) |
---|---|---|---|
Aluminum-PET | 0.3 – 0.5 | 3.0 – 3.2 | 60 – 80 |
Aluminum-PC | 0.3 – 0.5 | 2.8 – 3.1 | 60 – 80 |
Copper-FR4 | 0.5 – 0.7 | 4.2 – 4.9 | 320 – 400 |
Designing PCBs with Stiffeners
When designing PCBs with stiffeners, several factors should be considered to ensure optimal performance and reliability:
1. Material Selection
The choice of stiffener material depends on the specific requirements of the application, such as mechanical strength, thermal conductivity, electrical insulation, and cost. Metal stiffeners are suitable for applications that demand high mechanical strength and thermal conductivity, while plastic stiffeners are preferred for applications that require electrical insulation and lightweight construction. Composite stiffeners offer a balance of properties and are suitable for applications that require a combination of mechanical strength, thermal conductivity, and electrical insulation.
2. Dimensions and Placement
The dimensions and placement of the stiffener should be carefully designed to provide adequate support to the PCB without interfering with the electronic components or the overall functionality of the device. The stiffener should be positioned to evenly distribute the mechanical load across the PCB and to minimize warping and bending. In some cases, multiple stiffeners may be required to support larger or more complex PCBs.
3. Attachment Methods
Stiffeners can be attached to the PCB using various methods, such as adhesive bonding, mechanical fastening, or soldering. The choice of attachment method depends on the specific requirements of the application, such as the level of mechanical stress, thermal cycling, and environmental conditions. Adhesive bonding is a common method for attaching plastic and composite stiffeners, while mechanical fastening is often used for metal stiffeners.
4. Thermal Management
When designing PCBs with stiffeners, it is essential to consider the thermal management aspects of the system. Stiffeners can act as heat sinks, helping to dissipate heat generated by electronic components on the PCB. The thermal conductivity of the stiffener material and the contact area between the stiffener and the PCB play a crucial role in determining the effectiveness of the thermal management solution.
5. Manufacturing Considerations
The manufacturing process for PCBs with stiffeners should be carefully planned to ensure proper alignment, attachment, and compatibility with the overall assembly process. The stiffener should be designed with features such as mounting holes, standoffs, and alignment pins to facilitate the assembly process. The manufacturing tolerances and surface finish requirements should also be considered to ensure a reliable and consistent attachment between the stiffener and the PCB.
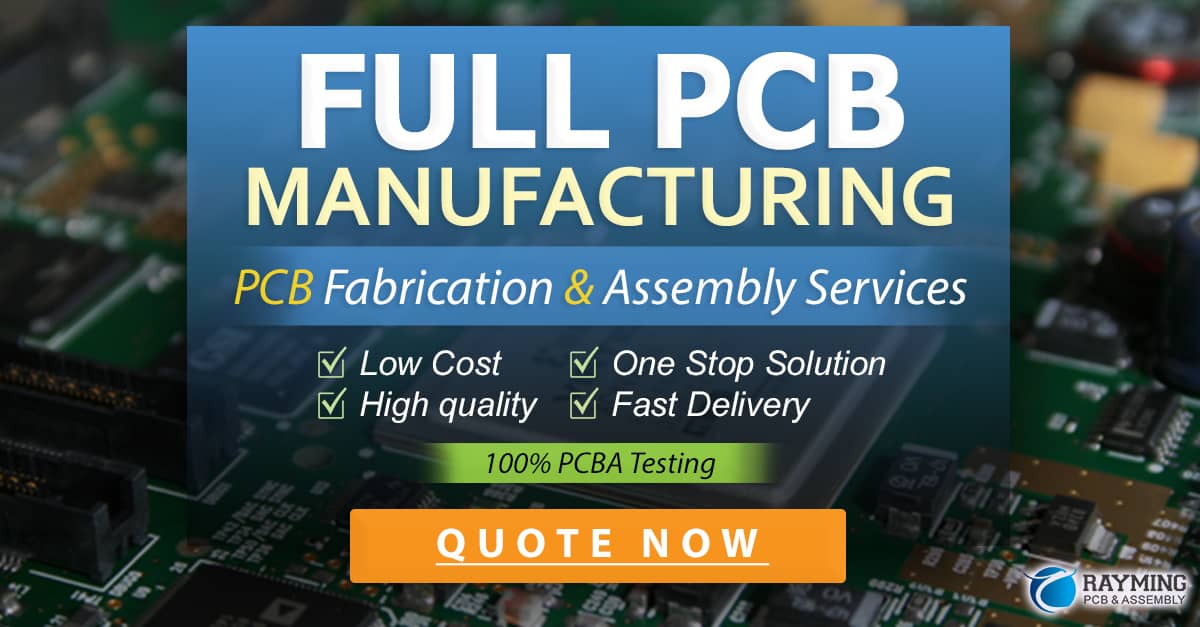
Applications of PCB Stiffeners
PCB stiffeners find applications in a wide range of industries and products, including:
-
Automotive Electronics: Stiffeners are used in automotive electronics to provide mechanical support and thermal management for PCBs in harsh environmental conditions, such as high temperatures, vibrations, and shocks.
-
Aerospace and Defense Systems: PCB stiffeners are essential in aerospace and defense applications, where high reliability, mechanical strength, and resistance to environmental factors are critical. Stiffeners help maintain the structural integrity of PCBs in systems such as avionics, radar, and communication equipment.
-
Industrial Control Systems: Stiffeners are used in industrial control systems to ensure the proper functioning and reliability of PCBs in environments with high levels of vibration, temperature fluctuations, and mechanical stress.
-
Medical Devices: PCB stiffeners are used in medical devices to provide mechanical support and ensure the reliable operation of electronic components in applications such as patient monitoring systems, diagnostic equipment, and surgical instruments.
-
Consumer Electronics: Stiffeners are used in consumer electronics to prevent warping and bending of PCBs in products such as smartphones, tablets, laptops, and gaming devices. They help maintain the structural integrity of the device and improve its overall durability.
Frequently Asked Questions (FAQ)
1. What materials are commonly used for PCB stiffeners?
PCB stiffeners are typically made from materials such as aluminum, stainless steel, copper alloys, polyethylene terephthalate (PET), polycarbonate (PC), and glass-reinforced epoxy (FR-4). The choice of material depends on the specific requirements of the application, such as mechanical strength, thermal conductivity, and electrical insulation.
2. How do PCB stiffeners help in thermal management?
PCB stiffeners can act as heat sinks, helping to dissipate heat generated by electronic components on the PCB. The thermal conductivity of the stiffener material and the contact area between the stiffener and the PCB determine the effectiveness of the thermal management solution. By improving thermal management, stiffeners contribute to the overall reliability and longevity of the electronic device.
3. What are the advantages of using composite PCB stiffeners?
Composite PCB stiffeners combine the advantages of both metal and plastic stiffeners. They typically consist of a metal core (e.g., aluminum) sandwiched between layers of high-performance thermoplastics (e.g., PET or PC). Composite stiffeners offer a balance of mechanical strength, thermal conductivity, and electrical insulation, making them suitable for applications that require a combination of these properties.
4. How are PCB stiffeners attached to the circuit board?
PCB stiffeners can be attached to the circuit board using various methods, such as adhesive bonding, mechanical fastening, or soldering. The choice of attachment method depends on the specific requirements of the application, such as the level of mechanical stress, thermal cycling, and environmental conditions. Adhesive bonding is a common method for attaching plastic and composite stiffeners, while mechanical fastening is often used for metal stiffeners.
5. In which industries are PCB stiffeners commonly used?
PCB stiffeners find applications in a wide range of industries, including automotive electronics, aerospace and defense systems, industrial control systems, medical devices, and consumer electronics. They are used to provide mechanical support, prevent warping and bending, improve thermal management, and ensure the reliable operation of electronic components in various environmental conditions.
Conclusion
PCB stiffeners are essential components in the design and manufacturing of reliable and durable electronic devices. They provide mechanical support, prevent warping and bending, improve thermal management, and ensure the proper functioning of electronic components in various environmental conditions. The choice of stiffener material, dimensions, placement, and attachment method depends on the specific requirements of the application, such as mechanical strength, thermal conductivity, electrical insulation, and cost.
By understanding the importance of PCB stiffeners and considering the key factors in their design and implementation, engineers and manufacturers can create electronic devices that are more reliable, durable, and resistant to environmental stresses. As the demand for high-performance and reliable electronic devices continues to grow across various industries, the use of PCB stiffeners will remain a critical aspect of PCB design and manufacturing.
0 Comments