Introduction to Halogen-Free PCBs
Printed Circuit Boards (PCBs) are essential components in modern electronics, providing a platform for electrical connections and mechanical support for various components. In recent years, there has been a growing trend towards the use of halogen-free PCBs due to their environmental and health benefits. This article will explore the concept of halogen-free PCBs, their advantages, and their applications in the electronics industry.
What are Halogens?
Halogens are a group of chemical elements that include fluorine (F), chlorine (Cl), bromine (Br), iodine (I), and astatine (At). These elements are highly reactive and can form strong bonds with other elements, making them useful in various industrial applications. However, halogens can also be harmful to the environment and human health when released into the atmosphere or ingested.
Traditional PCBs and Halogen Content
Traditionally, PCBs have been manufactured using materials that contain halogens, particularly bromine and chlorine. These halogens are used as flame retardants to improve the fire resistance of the PCBs. The most common halogenated flame retardants used in PCBs are:
- Polybrominated Biphenyls (PBBs)
- Polybrominated Diphenyl Ethers (PBDEs)
- Tetrabromobisphenol A (TBBPA)
While these flame retardants effectively reduce the risk of fire, they can have negative impacts on the environment and human health when the PCBs are disposed of or recycled improperly.
The Rise of Halogen-Free PCBs
Environmental and Health Concerns
The use of halogenated flame retardants in PCBs has come under scrutiny due to their potential environmental and health risks. When halogenated PCBs are incinerated or disposed of in landfills, the halogens can be released into the atmosphere, contaminating the air, water, and soil. These halogens can also bioaccumulate in the food chain, leading to potential health risks for humans and wildlife.
Moreover, exposure to halogenated flame retardants has been linked to various health issues, such as:
- Endocrine disruption
- Neurodevelopmental disorders
- Cancer
- Thyroid dysfunction
As a result, there has been a growing demand for halogen-free alternatives in the electronics industry.
Regulatory Requirements
In response to the environmental and health concerns associated with halogenated flame retardants, various regulatory bodies have implemented restrictions on the use of these substances in electronic products. For example:
- The European Union’s Restriction of Hazardous Substances (RoHS) Directive limits the use of certain halogenated flame retardants in electronic and electrical equipment.
- The Waste Electrical and Electronic Equipment (WEEE) Directive aims to reduce the environmental impact of electronic waste by promoting recycling and the use of safer materials.
- The Registration, Evaluation, Authorization, and Restriction of Chemicals (REACH) regulation requires manufacturers to disclose information on the use of hazardous substances in their products.
These regulations have driven the development and adoption of halogen-free PCBs in the electronics industry.
Characteristics of Halogen-Free PCBs
Materials Used in Halogen-Free PCBs
Halogen-free PCBs are manufactured using materials that do not contain halogens, particularly bromine and chlorine. Instead, they use alternative flame retardants that are less harmful to the environment and human health. Some common materials used in halogen-free PCBs include:
- Phosphorus-based flame retardants
- Nitrogen-based flame retardants
- Metal hydroxides (e.g., aluminum hydroxide, magnesium hydroxide)
- Inorganic fillers (e.g., silica, clay)
These alternative flame retardants provide comparable fire resistance to halogenated flame retardants while minimizing the environmental and health risks associated with halogens.
Advantages of Halogen-Free PCBs
Halogen-free PCBs offer several advantages over traditional PCBs containing halogenated flame retardants:
-
Reduced environmental impact: Halogen-free PCBs do not release harmful halogens into the environment when disposed of or recycled, minimizing air, water, and soil pollution.
-
Improved human health: By eliminating exposure to halogenated flame retardants, halogen-free PCBs reduce the risk of health issues associated with these substances, such as endocrine disruption and neurodevelopmental disorders.
-
Compliance with regulations: Using halogen-free PCBs helps manufacturers comply with increasingly stringent environmental and health regulations, such as RoHS, WEEE, and REACH.
-
Enhanced recyclability: Halogen-free PCBs are easier to recycle, as they do not require special handling or disposal methods to prevent the release of harmful halogens.
-
Improved reliability: Some studies have shown that halogen-free PCBs may have better long-term reliability compared to halogenated PCBs, as the alternative flame retardants can be less prone to degradation over time.
Challenges and Considerations
While halogen-free PCBs offer numerous benefits, there are some challenges and considerations to keep in mind when adopting this technology:
-
Higher material costs: Halogen-free materials may be more expensive than traditional halogenated materials, which can increase the overall cost of PCB manufacturing.
-
Process adjustments: Switching to halogen-free materials may require adjustments to the manufacturing process, such as changes in lamination temperatures and pressures, to ensure optimal performance.
-
Compatibility with components: Some components may not be compatible with halogen-free PCB materials, requiring careful selection and testing to ensure proper functionality.
-
Limited availability: Not all PCB manufacturers offer halogen-free options, which may limit the availability and sourcing options for halogen-free PCBs.
Despite these challenges, the benefits of halogen-free PCBs often outweigh the drawbacks, making them an increasingly popular choice in the electronics industry.
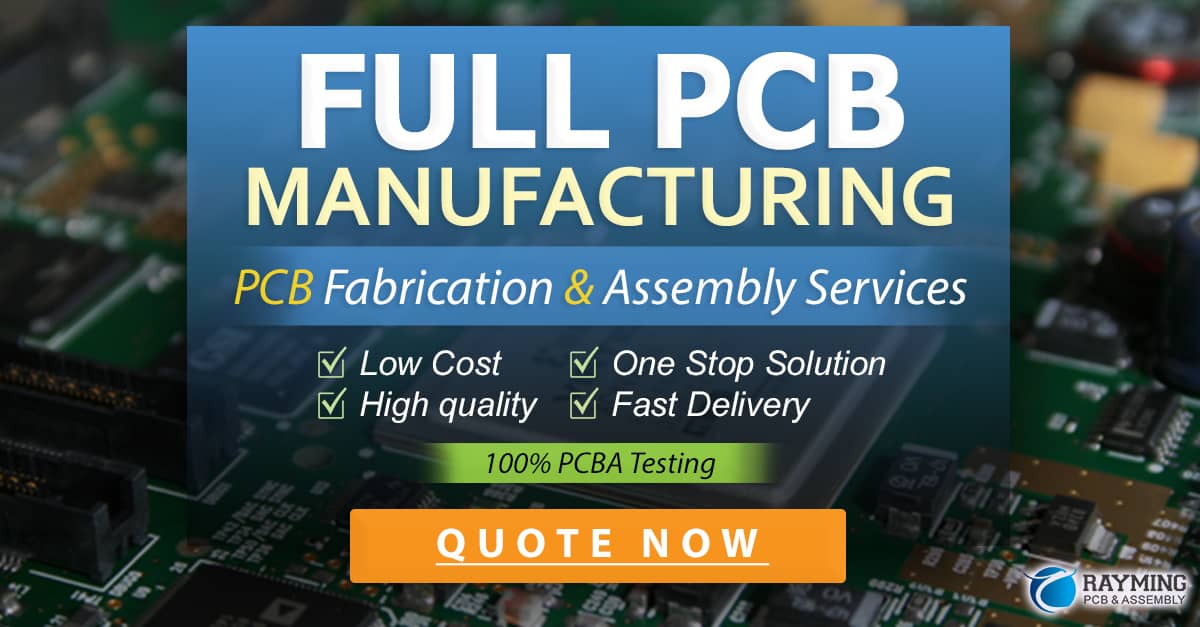
Applications of Halogen-Free PCBs
Halogen-free PCBs are used in a wide range of electronic applications, particularly in industries where environmental and health considerations are a priority. Some common applications include:
-
Consumer electronics: Smartphones, tablets, laptops, and other consumer devices are increasingly using halogen-free PCBs to comply with environmental regulations and meet consumer demand for eco-friendly products.
-
Automotive electronics: The automotive industry is adopting halogen-free PCBs for various electronic systems, such as infotainment, navigation, and advanced driver assistance systems (ADAS), to reduce the environmental impact of vehicles.
-
Medical devices: Halogen-free PCBs are used in medical devices to minimize the risk of exposure to harmful substances for patients and healthcare professionals.
-
Industrial equipment: Industrial applications, such as process control systems, automation equipment, and power electronics, are using halogen-free PCBs to improve environmental sustainability and comply with regulations.
-
Aerospace and defense: The aerospace and defense industries are adopting halogen-free PCBs to reduce the environmental impact of their products and meet strict safety and performance requirements.
As the demand for environmentally friendly and health-conscious electronic products continues to grow, the use of halogen-free PCBs is expected to expand across various industries.
Frequently Asked Questions (FAQ)
-
What are the main differences between halogen-free and traditional PCBs?
Halogen-free PCBs use alternative flame retardants that do not contain halogens (bromine and chlorine), while traditional PCBs use halogenated flame retardants. Halogen-free PCBs offer reduced environmental impact, improved human health, and better recyclability compared to traditional PCBs. -
Are halogen-free PCBs more expensive than traditional PCBs?
Yes, halogen-free PCBs can be more expensive than traditional PCBs due to the higher cost of halogen-free materials. However, the long-term benefits of using halogen-free PCBs, such as improved environmental sustainability and compliance with regulations, can outweigh the initial cost difference. -
Can halogen-free PCBs be used in all electronic applications?
Halogen-free PCBs can be used in a wide range of electronic applications, but some components may not be compatible with halogen-free materials. It is essential to carefully select and test components to ensure proper functionality when using halogen-free PCBs. -
How do halogen-free PCBs contribute to environmental sustainability?
Halogen-free PCBs reduce the environmental impact of electronic products by eliminating the release of harmful halogens into the environment when the products are disposed of or recycled. This helps minimize air, water, and soil pollution and promotes better recyclability of electronic waste. -
Are there any performance differences between halogen-free and traditional PCBs?
In general, halogen-free PCBs offer comparable performance to traditional PCBs. Some studies have even suggested that halogen-free PCBs may have better long-term reliability due to the reduced degradation of alternative flame retardants compared to halogenated flame retardants.
Conclusion
Halogen-free PCBs are an increasingly important technology in the electronics industry, offering numerous environmental and health benefits compared to traditional PCBs containing halogenated flame retardants. By using alternative materials that do not contain halogens, halogen-free PCBs minimize the release of harmful substances into the environment, improve human health, and promote better recyclability of electronic waste.
As regulations and consumer demand for eco-friendly products continue to drive the adoption of halogen-free PCBs, it is essential for manufacturers to carefully consider the challenges and benefits of this technology when designing and producing electronic products. By embracing halogen-free PCBs, the electronics industry can contribute to a more sustainable future while meeting the evolving needs of consumers and regulatory requirements.
0 Comments