Introduction to Wave Soldering
Wave soldering is a process used in the manufacturing of printed circuit boards (PCBs) to solder electronic components to the board. It involves applying molten solder to the underside of the PCB, creating a wave that washes over the components and forms a reliable electrical and mechanical connection. Wave soldering is an efficient and cost-effective method for mass production of electronic assemblies.
In this comprehensive guide, we will dive deep into the world of wave soldering, exploring its principles, process, advantages, and best practices. Whether you are a beginner or an experienced professional in the electronics industry, this guide will provide you with valuable insights to optimize your wave soldering process and achieve high-quality results.
The Principles of Wave Soldering
Understanding the Soldering Process
Soldering is a process that involves joining two or more metal surfaces using a filler metal called solder. The solder is melted and flows into the joint, creating a strong bond between the surfaces. In wave soldering, the solder is applied in the form of a wave, ensuring that all the components on the PCB are soldered simultaneously.
The Role of Flux in Wave Soldering
Flux is a chemical compound that plays a crucial role in the wave soldering process. It serves three main purposes:
- Removing oxides and contaminants from the metal surfaces, ensuring a clean and reactive surface for soldering.
- Preventing oxidation during the soldering process by shielding the molten solder from the atmosphere.
- Improving the wetting and flow characteristics of the solder, allowing it to spread evenly and form a reliable joint.
Types of Solder Used in Wave Soldering
The choice of solder is an important consideration in wave soldering. The most commonly used solder alloys are:
- Tin-Lead (Sn-Pb): Traditional solder alloy with a typical composition of 63% tin and 37% lead. It offers good wetting properties and reliable joint formation.
- Lead-Free Solder: Due to environmental and health concerns, lead-free solder alloys have gained popularity. Common lead-free alloys include Tin-Silver-Copper (Sn-Ag-Cu or SAC) and Tin-Copper (Sn-Cu).
The selection of solder alloy depends on factors such as the PCB’s application, environmental regulations, and compatibility with the components being soldered.
The Wave Soldering Process
Preparing the PCB for Wave Soldering
Before the PCB can undergo wave soldering, it needs to be properly prepared. The preparation process typically involves the following steps:
- PCB Design: The PCB layout should be designed with wave soldering in mind, ensuring adequate clearance between components, proper hole sizes, and solder mask application.
- Component Placement: The electronic components are placed on the top side of the PCB, either manually or using automated pick-and-place machines.
- Flux Application: Flux is applied to the underside of the PCB, either through spraying, foaming, or using a fluxing wave.
- Preheating: The PCB is preheated to activate the flux and remove any moisture from the board and components.
The Wave Soldering Machine
A wave soldering machine consists of several key components:
- Solder Pot: A reservoir that holds the molten solder and maintains its temperature.
- Solder Pump: A pump that circulates the molten solder and creates the solder wave.
- Conveyor System: A mechanism that transports the PCB through the various stages of the wave soldering process.
- Fluxing System: A unit that applies flux to the underside of the PCB before soldering.
- Preheating System: A heating element that preheats the PCB to the desired temperature.
The Wave Soldering Cycle
The wave soldering cycle typically involves the following steps:
- Fluxing: The underside of the PCB is coated with flux to ensure proper soldering.
- Preheating: The PCB is preheated to activate the flux and remove moisture.
- Soldering: The PCB passes over the solder wave, allowing the molten solder to contact the components and form solder joints.
- Cooling: The soldered PCB is cooled to allow the solder joints to solidify.
- Cleaning: Any excess flux residue is removed from the PCB using appropriate cleaning methods.
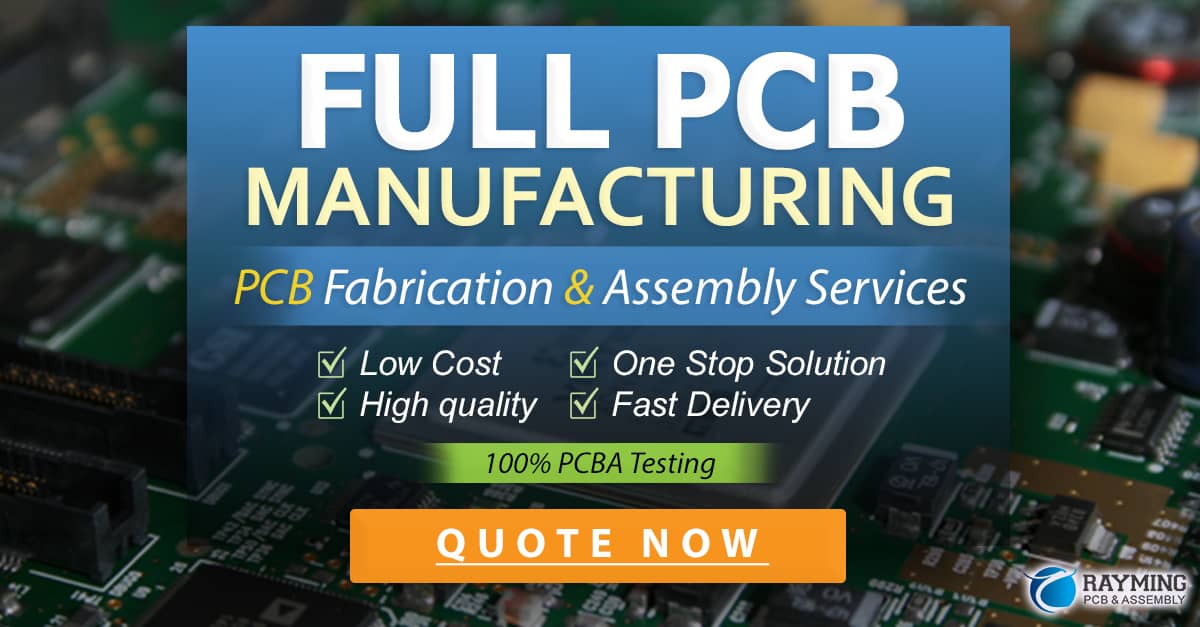
Advantages of Wave Soldering
Wave soldering offers several advantages over other soldering techniques:
- High Throughput: Wave soldering is a fast and efficient process, enabling the soldering of multiple PCBs in a short time.
- Consistency: The automated nature of wave soldering ensures consistent solder joint quality across a large number of PCBs.
- Cost-Effectiveness: Wave soldering is economical for mass production, as it reduces manual labor and minimizes the need for rework.
- Versatility: Wave soldering can accommodate a wide range of component types and sizes, making it suitable for various PCB designs.
Best Practices for Wave Soldering
To achieve optimal results in wave soldering, consider the following best practices:
- PCB Design: Ensure proper PCB design, including adequate clearance between components, appropriate hole sizes, and solder mask application.
- Flux Selection: Choose the right type of flux based on the PCB’s requirements, considering factors such as activity level, residue, and compatibility with the solder alloy.
- Preheat Settings: Optimize the preheat temperature and duration to activate the flux effectively and remove moisture without damaging the components.
- Solder Wave Height and Speed: Adjust the solder wave height and conveyor speed to ensure proper solder contact and minimize defects such as bridging or insufficient solder.
- Maintenance and Calibration: Regularly maintain and calibrate the wave soldering machine to ensure consistent performance and prevent issues such as solder contamination or uneven wave formation.
Troubleshooting Common Wave Soldering Defects
Despite following best practices, wave soldering defects can still occur. Some common defects and their potential causes include:
Defect | Potential Causes |
---|---|
Bridging | Excessive solder, incorrect wave height, improper preheat |
Insufficient Solder | Low solder wave height, incorrect conveyor speed, poor flux |
Solder Balls | Excessive flux, contaminated solder, incorrect preheat |
Lifted Components | Poor component placement, insufficient flux, incorrect preheat |
Solder Webbing | Excessive solder, incorrect wave height, improper drainage |
By identifying the root cause of the defect and making necessary adjustments to the process parameters, these issues can be minimized or eliminated.
Frequently Asked Questions (FAQ)
-
Q: What is the difference between wave soldering and reflow soldering?
A: Wave soldering is used for through-hole components and involves applying molten solder to the underside of the PCB. Reflow soldering, on the other hand, is used for surface-mount components and involves applying solder paste to the PCB pads and melting it in a reflow oven. -
Q: Can wave soldering be used for both lead-based and lead-free solders?
A: Yes, wave soldering can accommodate both lead-based and lead-free solder alloys. However, lead-free solders typically require higher soldering temperatures and may have different wetting characteristics compared to lead-based solders. -
Q: How do I select the right flux for my wave soldering process?
A: The choice of flux depends on factors such as the PCB’s surface finish, the solder alloy being used, and the desired level of residue. Consider the flux’s activity level, compatibility with the solder alloy, and the cleaning requirements of the PCB. -
Q: What is the optimal preheat temperature for wave soldering?
A: The optimal preheat temperature varies depending on the PCB design, component types, and flux used. Typically, the preheat temperature ranges from 80°C to 120°C. It is important to consult the flux manufacturer’s recommendations and conduct trials to determine the best preheat settings for your specific process. -
Q: How often should I perform maintenance on my wave soldering machine?
A: Regular maintenance is crucial for ensuring consistent performance and preventing issues in wave soldering. The frequency of maintenance depends on the machine’s usage and the manufacturer’s recommendations. Generally, it is advisable to perform daily, weekly, and monthly maintenance tasks, such as checking solder levels, cleaning the solder pot, and inspecting the conveyor system.
Conclusion
Wave soldering is a reliable and efficient method for soldering through-hole components on PCBs. By understanding the principles, process, and best practices of wave soldering, you can optimize your soldering process and achieve high-quality results consistently.
Remember to pay attention to PCB design, flux selection, preheat settings, and machine maintenance to minimize defects and ensure a smooth soldering process. With the knowledge gained from this ultimate guide, you are well-equipped to tackle wave soldering challenges and take your PCB Assembly to the next level.
0 Comments