What is PCB Burn-in Testing?
PCB burn-in testing is a reliability testing method used in printed circuit board (PCB) manufacturing to identify and eliminate early failures and defects in PCBs before they are shipped to customers. The goal is to stress the PCBs under elevated temperature, voltage, and/or current conditions for an extended period of time to accelerate aging and induce failures in marginal or defective components, solder joints, or the PCB itself.
Burn-in testing helps improve the reliability and quality of PCBs by weeding out infant mortality failures that may occur early in a product’s lifecycle. It is often performed on a sample basis as part of outgoing quality control, or on 100% of boards for critical applications where high reliability is essential, such as in aerospace, defense, medical devices, and automotive systems.
Why is PCB Burn-in Testing Important?
PCB burn-in testing is important for several reasons:
-
Identifies early failures: Burn-in testing can identify PCBs that may fail prematurely due to manufacturing defects, component quality issues, or design weaknesses. By stressing the PCBs under accelerated aging conditions, burn-in testing can induce failures that may otherwise occur early in the field, allowing these defective boards to be identified and removed before they reach the customer.
-
Improves reliability: By eliminating early failures, burn-in testing can significantly improve the reliability and quality of PCBs. This is especially important for critical applications where PCB failures can have serious consequences, such as in medical devices, aerospace systems, or automotive electronics.
-
Saves costs: While burn-in testing adds to the overall manufacturing cost, it can save significant costs in the long run by reducing warranty claims, field failures, and product returns. Early identification and removal of defective PCBs can also prevent costly product recalls and damage to the manufacturer’s reputation.
-
Meets customer requirements: Many customers, particularly in industries with high reliability requirements, may require burn-in testing as part of their quality assurance and acceptance criteria. Meeting these requirements is essential for winning and retaining business in these markets.
-
Provides performance data: Burn-in testing can provide valuable data on the performance and reliability of PCBs under stress conditions. This data can be used to improve product design, component selection, and manufacturing processes, leading to better quality and reliability in future products.
How is PCB Burn-in Testing Performed?
PCB burn-in testing typically involves the following steps:
-
Test planning: The first step is to develop a burn-in test plan based on the specific requirements of the PCB and its intended application. This plan should specify the test conditions (temperature, voltage, current, duration), sample size, acceptance criteria, and any special considerations or precautions.
-
Test setup: The next step is to set up the burn-in test equipment and environment. This may involve a temperature-controlled chamber or oven, power supplies, test fixtures, and monitoring equipment. The PCBs are loaded into the test fixtures and connected to the power supplies and monitoring equipment.
-
Burn-in stress: The PCBs are then subjected to the specified burn-in stress conditions for the required duration. This may involve elevated temperature (typically 125°C or higher), voltage (typically 1.5 times the rated voltage), and/or current (typically 1.5 times the rated current). The exact conditions and duration depend on the specific requirements of the PCB and its components.
-
Monitoring: During the burn-in stress, the PCBs are continuously monitored for any signs of failure or degradation. This may involve monitoring voltage, current, temperature, or other parameters using sensors or test equipment. Any abnormalities or failures are logged and investigated.
-
Post-stress testing: After the burn-in stress is complete, the PCBs are removed from the test fixtures and subjected to post-stress functional testing and visual inspection. This is to verify that the PCBs are still functioning correctly and meet all performance and quality requirements.
-
Data analysis: The burn-in test data is analyzed to determine the failure rate, failure modes, and any trends or patterns. This data is used to make decisions on whether the PCBs pass or fail the burn-in test, and to identify any areas for improvement in design or manufacturing.
-
Disposition: PCBs that pass the burn-in test are approved for shipment to the customer, while those that fail are rejected and analyzed further to determine the root cause of the failure. Corrective actions may be taken to address any design or manufacturing issues identified during the burn-in test.
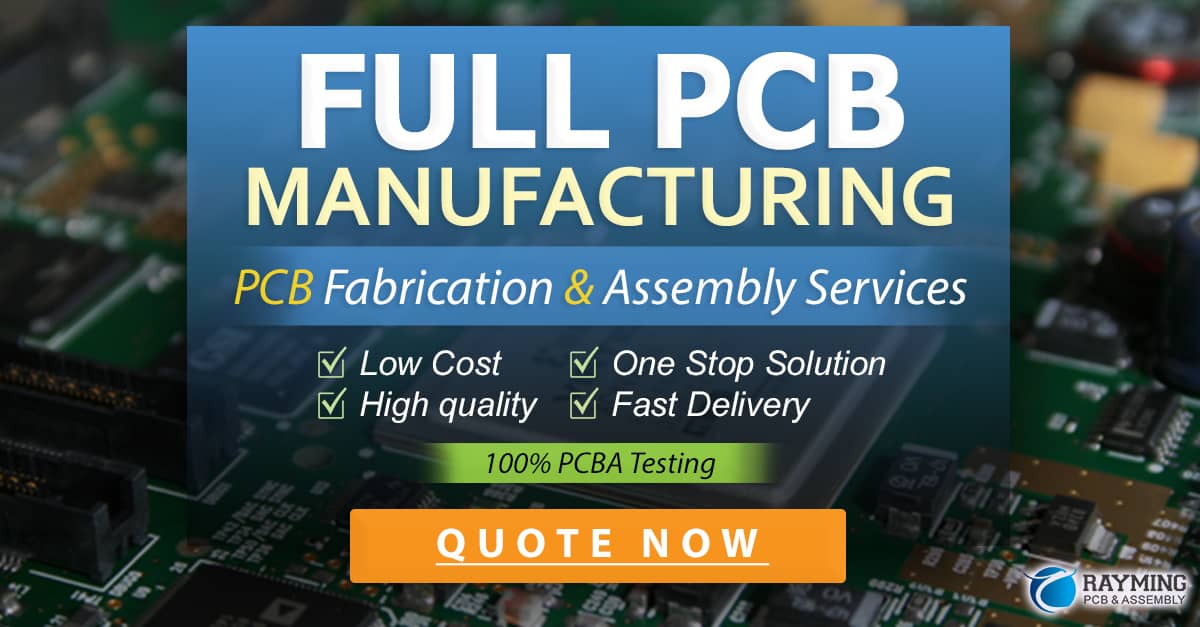
Types of PCB Burn-in Testing
There are several types of PCB burn-in testing, each with its own specific purpose and methodology:
1. Temperature Cycling Burn-in
Temperature cycling burn-in involves subjecting the PCBs to repeated cycles of high and low temperature extremes. The temperature range and cycle time are chosen to simulate the expected thermal stresses the PCB will experience in its intended application. Temperature cycling burn-in is effective at identifying failures related to thermal expansion and contraction, such as solder joint cracks, component failures, and delamination.
Parameter | Typical Value |
---|---|
High Temperature | 125°C to 150°C |
Low Temperature | -40°C to -55°C |
Cycle Time | 30 minutes to 1 hour |
Number of Cycles | 100 to 1000 |
2. Power Cycling Burn-in
Power cycling burn-in involves repeatedly powering the PCBs on and off at elevated temperature and voltage conditions. This type of burn-in is effective at identifying failures related to power-on stress, such as component overstress, power supply failures, and electromigration.
Parameter | Typical Value |
---|---|
Temperature | 125°C to 150°C |
Voltage | 1.2 to 1.5 times rated voltage |
Power Cycle Time | 5 minutes to 1 hour |
Number of Cycles | 100 to 1000 |
3. High Temperature Operating Life (HTOL) Burn-in
HTOL burn-in involves operating the PCBs at elevated temperature and voltage conditions for an extended period of time. This type of burn-in is effective at identifying failures related to long-term operational stress, such as component wear-out, electromigration, and dielectric breakdown.
Parameter | Typical Value |
---|---|
Temperature | 125°C to 150°C |
Voltage | 1.2 to 1.5 times rated voltage |
Duration | 48 to 1000 hours |
4. Highly Accelerated Stress Test (HAST) Burn-in
HAST burn-in involves subjecting the PCBs to a combination of high temperature, humidity, and voltage stress. This type of burn-in is effective at identifying failures related to moisture ingress, corrosion, and electrical leakage.
Parameter | Typical Value |
---|---|
Temperature | 130°C to 110°C |
Relative Humidity | 85% to 100% |
Voltage | 1.2 to 1.5 times rated voltage |
Duration | 96 to 264 hours |
Advantages and Disadvantages of PCB Burn-in Testing
Advantages
-
Early failure detection: Burn-in testing can identify and remove PCBs that are likely to fail early in their lifecycle, improving overall product reliability and quality.
-
Reduced warranty costs: By eliminating early failures, burn-in testing can reduce warranty claims and associated costs.
-
Improved customer satisfaction: Delivering PCBs with higher reliability and quality can lead to increased customer satisfaction and loyalty.
-
Compliance with industry standards: Burn-in testing can help PCB manufacturers meet industry standards and customer requirements for reliability and quality.
Disadvantages
-
Increased manufacturing costs: Burn-in testing adds to the overall manufacturing cost and time, which may impact profitability and time-to-market.
-
Potential for over-stress: If not properly designed and controlled, burn-in testing can over-stress the PCBs and introduce failures that would not occur under normal operating conditions.
-
Limited fault coverage: Burn-in testing may not detect all types of faults, particularly those that are intermittent or require specific stimuli to manifest.
-
False failures: Burn-in testing may sometimes identify false failures due to test setup issues or measurement errors, leading to unnecessary rejection of good PCBs.
Best Practices for PCB Burn-in Testing
To ensure effective and reliable PCB burn-in testing, consider the following best practices:
-
Develop a comprehensive test plan: Clearly define the test objectives, conditions, sample size, acceptance criteria, and any special considerations based on the specific requirements of the PCB and its intended application.
-
Use appropriate test equipment: Select test equipment that is capable of accurately applying and measuring the required stress conditions, and ensure that it is properly calibrated and maintained.
-
Control the test environment: Ensure that the burn-in test environment is properly controlled and monitored for temperature, humidity, and other factors that may affect the test results.
-
Monitor the PCBs continuously: Use sensors and test equipment to continuously monitor the PCBs for any signs of failure or degradation during the burn-in stress.
-
Perform post-stress testing: After the burn-in stress is complete, perform thorough functional testing and visual inspection to verify that the PCBs are still functioning correctly and meet all performance and quality requirements.
-
Analyze the test data: Carefully analyze the burn-in test data to identify any trends, patterns, or root causes of failures, and use this information to improve product design and manufacturing processes.
-
Document the results: Maintain clear and comprehensive documentation of the burn-in test results, including any failures, corrective actions, and process improvements.
Frequently Asked Questions (FAQ)
1. How long does PCB burn-in testing typically take?
The duration of PCB burn-in testing depends on the specific type of test and the requirements of the PCB and its intended application. Temperature cycling and power cycling burn-in tests typically run for 100 to 1000 cycles, with each cycle lasting from 30 minutes to 1 hour. HTOL burn-in tests can run from 48 to 1000 hours, while HAST burn-in tests typically run from 96 to 264 hours.
2. Is burn-in testing required for all PCBs?
Burn-in testing is not required for all PCBs, but it is often recommended or required for PCBs used in critical applications where high reliability is essential, such as in aerospace, defense, medical devices, and automotive systems. The decision to perform burn-in testing should be based on the specific requirements and risks associated with the PCB and its intended application.
3. Can burn-in testing damage the PCBs?
If not properly designed and controlled, burn-in testing can potentially over-stress the PCBs and introduce failures that would not occur under normal operating conditions. However, when performed correctly, burn-in testing should not damage the PCBs, but rather identify and remove those that are likely to fail early in their lifecycle.
4. How much does burn-in testing add to the overall manufacturing cost?
The cost of burn-in testing can vary widely depending on the type of test, the complexity of the PCB, and the volume of production. In general, burn-in testing can add anywhere from 10% to 50% to the overall manufacturing cost of a PCB. However, this cost should be weighed against the potential savings in warranty claims, field failures, and product returns that can result from early failure detection and removal.
5. Can burn-in testing be performed in-house or is it typically outsourced?
Burn-in testing can be performed either in-house or outsourced to a third-party testing service, depending on the capabilities and resources of the PCB manufacturer. In-house testing requires investment in specialized equipment, facilities, and trained personnel, which may not be feasible for all manufacturers. Outsourcing to a qualified testing service can provide access to state-of-the-art equipment and expertise, but may add to the overall cost and lead time. The decision to perform burn-in testing in-house or outsource should be based on a careful analysis of the costs, benefits, and risks associated with each option.
Conclusion
PCB burn-in testing is a critical reliability testing method used in PCB manufacturing to identify and eliminate early failures and defects before they reach the customer. By subjecting PCBs to elevated temperature, voltage, and/or current stress for an extended period of time, burn-in testing can induce failures that may otherwise occur early in the field, allowing these defective boards to be removed and improving the overall reliability and quality of the product.
There are several types of PCB burn-in testing, each with its own specific purpose and methodology, including temperature cycling, power cycling, HTOL, and HAST burn-in. While burn-in testing adds to the overall manufacturing cost and time, it can provide significant benefits in terms of reduced warranty costs, improved customer satisfaction, and compliance with industry standards and customer requirements.
To ensure effective and reliable PCB burn-in testing, manufacturers should follow best practices such as developing a comprehensive test plan, using appropriate test equipment, controlling the test environment, monitoring the PCBs continuously, performing post-stress testing, analyzing the test data, and documenting the results.
By implementing a robust PCB burn-in testing process, manufacturers can improve the reliability and quality of their products, reduce costs associated with early failures and warranty claims, and enhance their reputation and competitiveness in the marketplace.
0 Comments