Surface mount technology (SMT) has revolutionized the electronics manufacturing industry over the past few decades. One of the key materials used in SMT assembly is solder paste. Solder paste is a homogenous mixture of tiny solder alloy particles suspended in flux. When heated during the soldering process, the flux removes oxides and facilitates alloy melting and bonding to form solder joints. Selecting the right solder paste is critical for producing high-quality and reliable solder joints in SMT assembly. This article provides an overview of the main types of solder pastes used in SMT and their properties, applications, and selection criteria.
Types of Solder Paste
There are three main types of solder paste used in SMT assembly:
Lead-Based Solder Paste
Lead-based solder pastes contain lead (Pb) as the main alloying element. The most common lead-based solder alloy used is the eutectic 63Sn/37Pb, which has a melting point of 183°C. Lead-based solder pastes have excellent solderability and provide strong, reliable solder joints. However, due to environmental legislation, lead-free solder pastes are now more commonly used.
Lead-Free Solder Paste
Lead-free solder pastes contain alloys based on tin (Sn), silver (Ag), copper (Cu), bismuth (Bi), zinc (Zn), indium (In), and other elements. Common lead-free solder alloys include:
- SAC alloys: Sn/Ag/Cu alloys with melting points around 217 – 220°C
- SAC305: 96.5Sn/3Ag/0.5Cu alloy with melting point 217°C
- SAC387: 95.5Sn/3.8Ag/0.7Cu alloy with melting point 217°C
- Sn/Ag: 99Sn/1Ag alloy with melting point 221°C
- Sn/Cu: 99.3Sn/0.7Cu alloy with melting point 227°C
- Sn/Zn: 91Sn/9Zn alloy with melting point 198°C
- Sn/Bi: 97Sn/3Bi alloy with melting point 139°C
Lead-free solder pastes meet environmental legislation requirements and provide good solder joint reliability. However, they tend to require higher soldering temperatures than lead-based pastes.
No-Clean Solder Paste
No-clean solder pastes contain flux residues that do not need to be removed after soldering. Most modern solder pastes used for SMT are no-clean formulations. No-clean flux chemistry includes:
- Rosin-based: Most common no-clean flux, leaves benign tacky resin residues.
- Water-soluble: Residues can be removed with water post-soldering.
- Organic acid-based: Similar performance to rosin but higher activity, suitable for difficult applications.
No-clean solder pastes improve manufacturing efficiency since a separate cleaning step is not required after soldering.
Solder Paste Properties
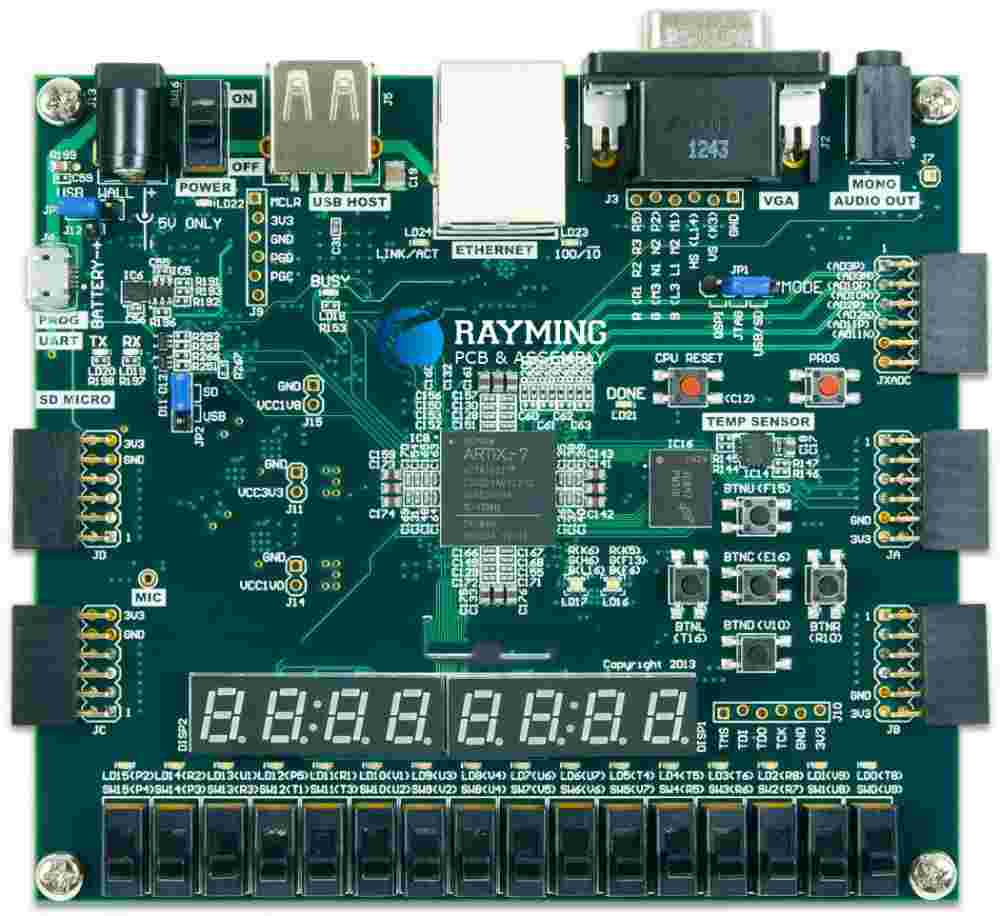
Key properties to consider when selecting a solder paste include:
- Metal Content: Proportion of solder alloy particles in the paste, typically 88-92% for standard pastes.
- Alloy Composition: Solder alloy type (lead-based, SAC, Sn/Ag etc). Determines melting point.
- Particle Size: Diameter of suspended solder particles, typically 25-45 μm. Smaller particles improve soldering of fine features.
- Flux Type and Activity Level: Determines oxide removal capability and residues.
- Viscosity: Thixotropic flow behavior. Affects stencil printing performance.
- Slump Resistance: Ability to maintain shape after printing. Important for small deposits.
- Tackiness: Stickiness/adhesion of the paste to surfaces. Affects solder balling.
- Shelf Life: Time paste can be stored before use. 6-9 months typical at refrigerated temperatures.
Solder Paste Applications
Different solder paste types are used for different SMT assembly applications:
Application | Typical Solder Paste Used |
---|---|
General SMT assembly | No-clean SAC305 |
Fine pitch components | SAC305 with small particles (25-30 μm) |
Large components/high reliability | High silver content SAC alloy (e.g. SAC387) |
Rework/repair | Low melting point alloy (Sn/Bi) |
High temperature assembly | High melting point alloy (Sn/Cu or Sn/Ag) |
Wire bonding | Fine particle size for bonding pads |
Solder Paste Selection Criteria
Key factors to consider when selecting a solder paste include:
- Soldering Process Temperature: Match the paste melting point to the equipment profile
- Alloy Compatibility: Avoid tin whiskering with pure tin finishes
- Component Types: Choose particle size and tackiness for the components used
- PCB Finish: Match the paste to the board finish (OSP, Immersion Silver etc).
- Product Reliability Requirements: Select paste accordingly (e.g. high-reliability alloys)
- Environmental Considerations: Lead-free paste required for RoHS compliance
- Residue Cleaning: No-clean paste if cleaning is not possible
- Printing Equipment: Match rheological properties to the printer
- Cost: Balance performance and cost
Proper solder paste selection, screening through prototyping, evaluation of print and reflow performance, and review of solder joint quality is key to a successful SMT process. Solder paste manufacturers provide extensive technical resources to guide paste selection.
Typical Solder Paste Recipes
Solder paste products consist of a specific solder alloy powder combined with a particular flux formulation. Here are some typical solder paste compositions from leading manufacturers:
Manufacturer | Product Name | Description |
---|---|---|
Indium | Indium8.9HFA | Halogen-free no-clean flux, SAC305 alloy, Type 3 powder |
Kester | 24-7068-8853 | No-clean flux, Sn/Ag/Cu alloy, Type 4 powder |
Alpha | OM-539 | No-clean flux, 63Sn/37Pb alloy, Type 3 powder |
AIM | NC-771-92C-M | No-clean flux, SAC 305 alloy, Type 4 powder |
Chip Quik | SMDLTLFP | Low temperature lead-free no-clean flux, Sn/Bi alloy |
The product datasheets provide detailed specifications on metal load, particle size distribution, viscosity, slump resistance, tackiness, and other parameters.
Solder Paste Printing Process

Understanding the solder paste printing process is important for high-quality assembly. Key aspects include:
Stencil Design: Laser-cut stainless steel stencils with appropriate aperture design for each component pad. Electropolishing improves paste release.
Paste Preparation: Cooling to room temperature and homogenizing avoids separation.
Printing: Pneumatic squeegees deposit a uniform layer of paste through the stencil apertures onto the PCB pads. Fine adjustability for optimal print speed, pressure, separation speed, and snap-off distance.
Inspection: Automated optical inspection after print checks for insufficient or excessive paste deposits, clogged apertures, smearing, etc.
Reflow Profile: Time-temperature profile with ramp-up to 30-60 sec above the solder melting point, then controlled cooling. Peak temperatures 230-260°C for lead-free.
Cleaning: For no-clean paste, residues do not need to be removed. For other pastes, cleaning agents include DI water, alcohol, or saponifiers.
Proper paste printing maximizes solder joint quality and reliability.
Defects Related to Solder Paste
Common solder paste-related defects include:
- Insufficient Print Deposit: Low paste volume on pads due to issues like clogged stencil apertures, low snap-off, or high print speed.
- Solder Balling/Splattering: Expulsion of molten solder from excessive paste deposits creating solder balls on the board.
- Solder Beading: Paste coalescence into long beads rather than discrete dots. Caused by high tackiness or improper separation speed.
- Solder Bridging: Shorting between adjacent pads/leads due to excess paste or improper stencil design.
- Voiding: Gas bubbles trapped in the solder joint, impairing strength and thermal conduction.
- Solder Starvation: Incomplete/weak joint formation due to insufficient solder volume.
- Tombstoning: Upright standing of small components due to uneven heating and soldering.
Thorough inspection and analysis of defects guides corrective actions like adjusting the stencil, printer settings, paste formulation, and reflow profile. This optimizes the process and product quality.
Solder Paste Handling
Proper solder paste handling and storage prolongs shelf life and prevents defects:
- Store paste at 2-10°C in sealed jars/cartridges away from sunlight. Allow to reach room temperature before use.
- Do not remove worked paste from stencil and mix back into unused paste to avoid contaminating the fresh paste.
- Avoid introducing contaminants like oils, solvents, metals, paper/plastic fibers which affect paste properties.
- Use paste within the recommended shelf life period based on manufacturer’s data. First-in-first-out (FIFO) stock rotation.
- Ensure air-tight sealing of jars/cartridges during storage to prevent drying or oxidation of paste.
- Measure and record paste viscosity, slump resistance and tackiness periodically to identify changes over time.
- Do not refreeze paste after thawing since this damages the suspension stability.
Proper handling and controlled processes are key to maximizing solder paste life and minimizing defects.
FQA
What are the main types of solder paste used in SMT assembly?
The three main types of solder paste are lead-based, lead-free, and no-clean formulations. Lead-based pastes contain Pb/Sn alloys but are being phased out due to environmental legislation. Lead-free pastes use alloys like SAC, Sn/Ag, Sn/Cu, and Sn/Bi. Most modern solder pastes are no-clean types with benign flux residues that do not require post-solder cleaning.
What solder alloy is most commonly used in SMT solder paste?
The lead-free SAC305 alloy (96.5Sn/3Ag/0.5Cu) is the most commonly used solder paste alloy for SMT assembly. It provides a good combination of solderability, joint strength, creep resistance, and thermal fatigue performance. Other popular alloys are SAC387, Sn/Ag, and Sn/Cu.
How does solder paste particle size affect sprinting performance?
Smaller solder particles of 25-30 microns are preferred for printing fine pitch components as they can deposit smaller volumes and penetrate between close lead spacings. Larger particles around 45 microns are used for standard pitch printing. Ultra-fine 15-20 micron powder may be used for microelectronic assemblies.
What causes solder balling defects?
Solder balling or splattering is caused by excessive paste deposition which forms molten solder balls during reflow. It can be mitigated by adjusting stencil aperture size, printer pressure settings, and by using a solder paste with appropriate viscosity and tackiness for the application.
Why is no-clean solder paste preferred for SMT production?
No-clean paste eliminates the need to wash flux residues after soldering since the benign residues are designed to not impact performance or reliability. This improves efficiency and throughput in high-volume SMT lines. Most modern lead-free solder pastes are no-clean types.
0 Comments