Introduction to PCB Fabrication
Printed Circuit Board (PCB) fabrication is a crucial process in the electronics industry. It involves the creation of a board that connects electronic components together to form a functional circuit. PCBs are used in a wide range of applications, from simple electronic devices to complex industrial equipment.
Two-layer PCBs are the most common type of PCBs used in electronic devices. They consist of two layers of conductive material, typically copper, separated by an insulating layer. The conductive layers are etched with the desired circuit pattern, and the components are soldered onto the board to complete the circuit.
Advantages of Two-Layer PCBs
Two-layer PCBs offer several advantages over other types of PCBs:
- Low cost: Two-layer PCBs are relatively inexpensive to manufacture compared to multi-layer PCBs.
- Simple design: Two-layer PCBs have a simple design, making them easier to manufacture and test.
- Reliable: Two-layer PCBs are reliable and durable, making them suitable for a wide range of applications.
PCB Fabrication Process
The PCB fabrication process involves several steps, each of which is critical to ensuring the quality and reliability of the final product.
Step 1: Design
The first step in the PCB fabrication process is the design phase. This involves creating a schematic diagram of the circuit and then converting it into a PCB layout. The PCB layout is a graphical representation of the physical arrangement of the components on the board.
Step 2: Printing
Once the PCB layout is complete, it is printed onto a film or paper using a high-resolution printer. The printed image is used to create a photomask, which is a transparent sheet with the circuit pattern printed on it.
Step 3: Etching
The next step is to transfer the circuit pattern from the photomask onto the copper layers of the PCB. This is done using a process called etching. The PCB is coated with a light-sensitive material called photoresist, and then exposed to light through the photomask. The areas of the photoresist that are exposed to light become soluble and can be washed away, leaving the desired circuit pattern on the copper layers.
Step 4: Drilling
After the etching process, holes are drilled into the PCB to allow for the installation of components. The holes are typically drilled using a computer-controlled drilling machine to ensure accuracy and precision.
Step 5: Plating
The drilled holes are then plated with a conductive material, typically copper, to ensure a good electrical connection between the layers of the PCB.
Step 6: Solder Mask Application
A solder mask is a protective coating that is applied to the PCB to prevent short circuits and protect the copper traces from damage. The solder mask is typically green in color and is applied using a silkscreen printing process.
Step 7: Silkscreen Printing
The final step in the PCB fabrication process is silkscreen printing. This involves printing text and symbols onto the PCB to identify components and provide other important information.
PCB Material Selection
The choice of material for a two-layer PCB depends on several factors, including the intended application, the required electrical properties, and the environmental conditions in which the PCB will be used.
FR-4
FR-4 is the most commonly used material for two-layer PCBs. It is a composite material made from woven fiberglass and epoxy resin. FR-4 has good electrical insulation properties, high mechanical strength, and excellent thermal stability.
CEM-1
CEM-1 is another popular material for two-layer PCBs. It is a composite material made from a mixture of woven fiberglass and paper, impregnated with epoxy resin. CEM-1 is less expensive than FR-4 but has lower mechanical strength and thermal stability.
Polyimide
Polyimide is a high-performance material used in applications that require high temperature resistance and excellent electrical insulation properties. Polyimide PCBs are typically used in aerospace and military applications.
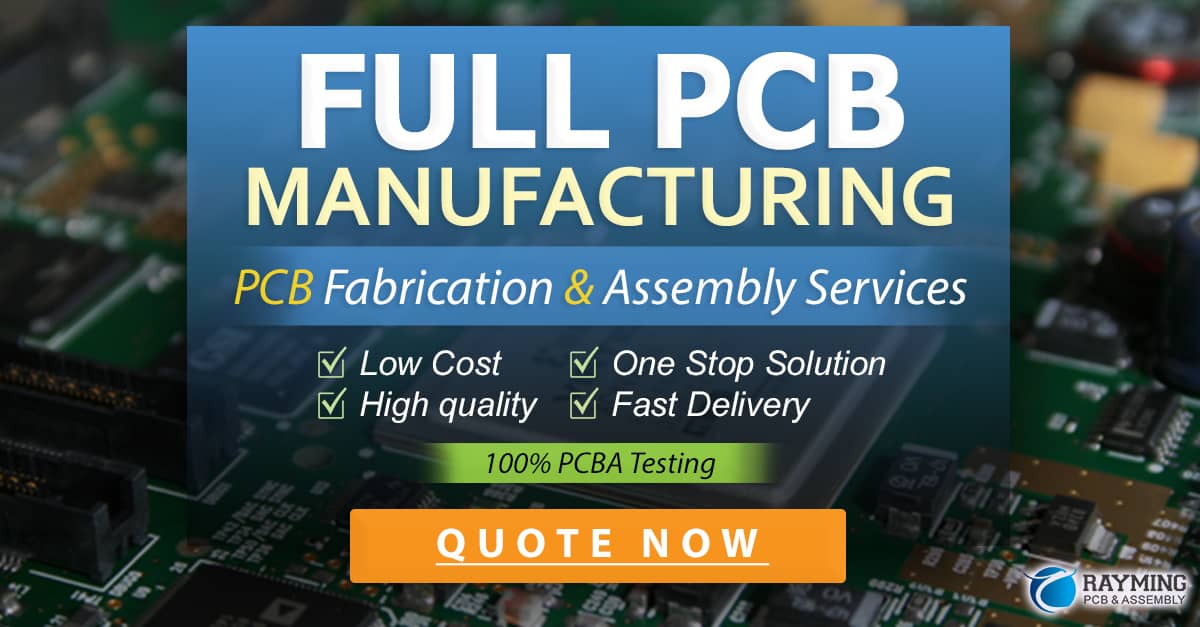
PCB Design Considerations
When designing a two-layer PCB, there are several important considerations to keep in mind:
Trace Width and Spacing
The width and spacing of the copper traces on the PCB are critical to ensuring good electrical performance and reliability. The trace width should be selected based on the current carrying capacity required for the circuit, while the spacing between traces should be sufficient to prevent short circuits and crosstalk.
Component Placement
The placement of components on the PCB is also important to ensure good electrical performance and reliability. Components should be placed in a way that minimizes the length of the copper traces and reduces the risk of interference between components.
Grounding and Shielding
Proper grounding and shielding are essential to ensure good electrical performance and reduce the risk of electromagnetic interference (EMI). The PCB should be designed with a solid ground plane and appropriate shielding to minimize EMI.
PCB Testing and Inspection
Once the PCB fabrication process is complete, the PCB must undergo testing and inspection to ensure that it meets the required specifications and is free from defects.
Visual Inspection
The first step in PCB testing and inspection is a visual inspection. This involves examining the PCB under a microscope or magnifying glass to check for defects such as scratches, cracks, or missing components.
Electrical Testing
Electrical testing involves testing the PCB to ensure that it functions as intended. This may involve using specialized test equipment to measure the electrical properties of the PCB, such as resistance, capacitance, and inductance.
Functional Testing
Functional testing involves testing the PCB in its intended application to ensure that it performs as expected. This may involve using the PCB in a prototype or final product and verifying that it meets the required specifications.
Common PCB Defects
Despite the best efforts of PCB manufacturers, defects can sometimes occur during the fabrication process. Some of the most common PCB defects include:
Short Circuits
Short circuits occur when two or more conductive traces on the PCB come into contact with each other, causing an unintended electrical connection. Short circuits can be caused by a variety of factors, including improper etching, drilling, or soldering.
Open Circuits
Open circuits occur when there is a break in the conductive path on the PCB, preventing electrical current from flowing through the circuit. Open circuits can be caused by factors such as broken traces, damaged components, or improper soldering.
Solder Bridges
Solder bridges occur when excess solder flows between two or more conductive traces on the PCB, creating an unintended electrical connection. Solder bridges can be caused by factors such as improper soldering technique or excess solder paste.
PCB Fabrication Standards
To ensure the quality and reliability of PCBs, several industry standards have been developed. These standards provide guidelines for PCB design, fabrication, and testing.
IPC Standards
The IPC (Association Connecting Electronics Industries) is a global trade association that develops standards for the electronics industry. The IPC has developed several standards related to PCB fabrication, including:
- IPC-6012: Qualification and Performance Specification for Rigid Printed Boards
- IPC-A-600: Acceptability of Printed Boards
- IPC-TM-650: Test Methods Manual
UL Standards
Underwriters Laboratories (UL) is a global safety certification company that develops standards for a wide range of products, including PCBs. The UL has developed several standards related to PCB fabrication, including:
- UL 94: Standard for Safety of Flammability of Plastic Materials for Parts in Devices and Appliances
- UL 796: Standard for Safety of Printed-Wiring Boards
FAQs
Q1: What is the difference between a two-layer PCB and a multi-layer PCB?
A1: A two-layer PCB has two layers of conductive material, typically copper, separated by an insulating layer. A multi-layer PCB has more than two layers of conductive material, separated by insulating layers. Multi-layer PCBs are used in applications that require higher density and complexity than two-layer PCBs.
Q2: What is the purpose of the solder mask on a PCB?
A2: The solder mask is a protective coating that is applied to the PCB to prevent short circuits and protect the copper traces from damage. The solder mask also provides a surface for silkscreen printing of text and symbols.
Q3: What is the difference between FR-4 and CEM-1 PCB materials?
A3: FR-4 is a composite material made from woven fiberglass and epoxy resin, while CEM-1 is a composite material made from a mixture of woven fiberglass and paper, impregnated with epoxy resin. FR-4 has higher mechanical strength and thermal stability than CEM-1, but is also more expensive.
Q4: What is the purpose of electrical testing in PCB fabrication?
A4: Electrical testing involves testing the PCB to ensure that it functions as intended. This may involve using specialized test equipment to measure the electrical properties of the PCB, such as resistance, capacitance, and inductance. Electrical testing helps to identify any defects or issues with the PCB before it is used in a final product.
Q5: What are some common causes of short circuits on a PCB?
A5: Short circuits can be caused by a variety of factors, including improper etching, drilling, or soldering. Other causes may include damage to the PCB during handling or assembly, or contamination of the PCB surface with conductive materials such as dust or moisture.
Conclusion
Two-layer PCB fabrication is a complex process that involves several critical steps, from design to testing and inspection. By understanding the basics of PCB fabrication, including material selection, design considerations, and common defects, designers and manufacturers can ensure the quality and reliability of their products.
Adherence to industry standards such as IPC and UL is also important to ensure consistency and safety in PCB fabrication. By following best practices and using appropriate materials and techniques, PCB manufacturers can produce high-quality, reliable products that meet the needs of their customers.
Step | Description |
---|---|
1 | Design |
2 | Printing |
3 | Etching |
4 | Drilling |
5 | Plating |
6 | Solder Mask Application |
7 | Silkscreen Printing |
Material | Description |
---|---|
FR-4 | Composite material made from woven fiberglass and epoxy resin |
CEM-1 | Composite material made from a mixture of woven fiberglass and paper, impregnated with epoxy resin |
Polyimide | High-performance material used in applications that require high temperature resistance and excellent electrical insulation properties |
0 Comments