Materials Used in Flex PCB Manufacturing
The materials used in the manufacturing of flex PCBs play a significant role in determining the overall cost. Some of the common materials used include:
Polyimide (PI) Substrate
Polyimide is the most widely used substrate material for flex PCBs due to its excellent thermal stability, chemical resistance, and mechanical properties. The thickness of the PI substrate can vary from 25μm to 125μm, with thicker substrates being more expensive.
Copper Foil
Copper foil is used for creating conductive traces on the flex PCB. The thickness of the copper foil can range from 9μm to 70μm, with thicker foils being more expensive. Additionally, the type of copper foil (electrodeposited or rolled annealed) can also affect the price.
Adhesives
Adhesives are used to bond the copper foil to the PI substrate. The type of adhesive used (acrylic, epoxy, or pressure-sensitive) and its thickness can impact the cost of the flex PCB.
Coverlay
Coverlay is a protective layer applied to the flex PCB to insulate and protect the exposed copper traces. The material and thickness of the coverlay can affect the overall price.
Manufacturing Process Complexity
The complexity of the manufacturing process is another significant factor that affects the price of flex PCBs. Some of the aspects that contribute to the complexity include:
Number of Layers
Flex PCBs can be single-sided, double-sided, or multi-layered. As the number of layers increases, the manufacturing process becomes more complex and time-consuming, resulting in higher costs.
Circuit Density
The circuit density refers to the number of components and traces per unit area on the flex PCB. Higher circuit densities require more precise manufacturing techniques, leading to increased costs.
Minimum Feature Size
The minimum feature size refers to the smallest width of the copper traces and the spacing between them. Smaller feature sizes require advanced manufacturing equipment and processes, which can drive up the cost.
Hole Drilling and Routing
The number, size, and position of holes and cutouts on the flex PCB can also impact the manufacturing complexity and, consequently, the price.
Order Quantity and Lead Time
The order quantity and lead time are two interrelated factors that can significantly influence the price of flex PCBs.
Order Quantity
Flex PCB manufacturers often offer volume discounts for larger order quantities. This is because the setup costs for the manufacturing process can be spread across more units, reducing the per-unit cost. The following table provides an example of how order quantity can affect the price:
Order Quantity | Price per Unit |
---|---|
1-50 | $10.00 |
51-100 | $8.50 |
101-500 | $7.00 |
501-1000 | $5.50 |
1001+ | $4.00 |
Lead Time
Lead time is the duration between placing an order and receiving the finished product. Shorter lead times often come with a premium price, as manufacturers need to prioritize and expedite the production process. On the other hand, longer lead times may allow for more cost-effective production planning and resource allocation, resulting in lower prices.
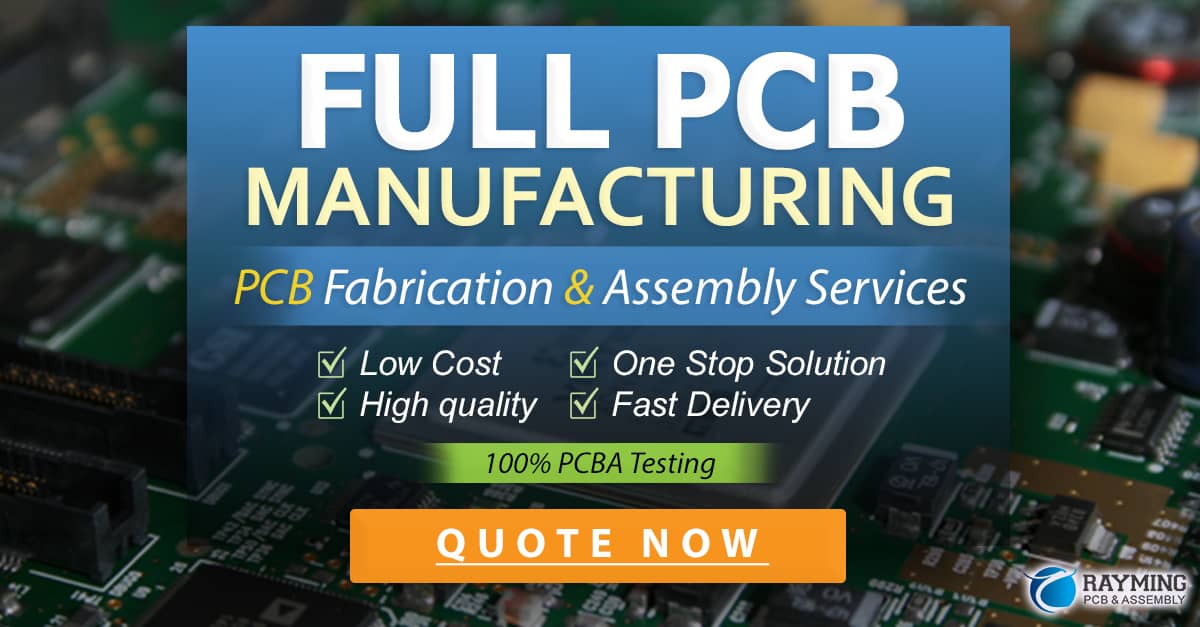
Quality Control and Testing
Quality control and testing procedures are essential to ensure the reliability and functionality of flex PCBs. However, these processes can also contribute to the overall cost.
Visual Inspection
Visual inspection is the first line of quality control, where the flex PCBs are checked for any visible defects or irregularities. This process is relatively inexpensive but is crucial for identifying potential issues early in the manufacturing process.
Automated Optical Inspection (AOI)
AOI uses high-resolution cameras and advanced software to detect surface-level defects on the flex PCBs. This process is more expensive than visual inspection but offers higher accuracy and consistency.
Electrical Testing
Electrical testing is performed to verify the electrical continuity, insulation resistance, and other performance characteristics of the flex PCBs. This process requires specialized equipment and skilled technicians, which can add to the overall cost.
Environmental Testing
Environmental testing involves subjecting the flex PCBs to various stress factors, such as temperature, humidity, and vibration, to assess their durability and reliability under different operating conditions. This type of testing can be expensive but is necessary for applications where the flex PCBs will be exposed to harsh environments.
Design Complexity and Customization
The design complexity and level of customization required for a flex PCB can also have a significant impact on the price.
Standard vs. Custom Designs
Standard flex PCB designs are pre-engineered and readily available, making them more cost-effective than custom designs. Custom designs, on the other hand, are tailored to specific requirements and may involve additional engineering efforts, resulting in higher costs.
Dimensions and Shape
The dimensions and shape of the flex PCB can affect the manufacturing complexity and material usage. Larger and more complex shapes may require more advanced manufacturing techniques and result in higher costs.
Component Integration
The level of component integration on the flex PCB can also influence the price. Higher component densities and the use of advanced components, such as fine-pitch ball grid arrays (BGAs) or chip-scale packages (CSPs), can increase the manufacturing complexity and cost.
Geographic Location and Shipping
The geographic location of the flex PCB manufacturer and the shipping requirements can also impact the overall cost.
Labor and Overhead Costs
Labor and overhead costs vary significantly across different regions. Countries with lower labor costs, such as China and India, may offer more competitive pricing for flex PCBs compared to countries with higher labor costs, such as the United States and Europe.
Shipping and Logistics
The cost of shipping and logistics can also add to the overall price of flex PCBs, especially for international orders. Factors such as shipping distance, mode of transportation, and customs duties can all influence the final cost.
Frequently Asked Questions (FAQ)
-
Q: What is the typical lead time for flex PCB manufacturing?
A: The lead time for flex PCB manufacturing can vary depending on the complexity of the design, order quantity, and manufacturing capabilities of the supplier. Typical lead times range from 2 to 6 weeks, but expedited options may be available for an additional cost. -
Q: Can I get a discount for ordering a large quantity of flex PCBs?
A: Yes, most flex PCB manufacturers offer volume discounts for larger order quantities. The specific discount structure may vary depending on the manufacturer and the size of the order. -
Q: How does the number of layers affect the price of flex PCBs?
A: As the number of layers in a flex PCB increases, the manufacturing process becomes more complex and time-consuming, resulting in higher costs. Multi-layer flex PCBs are generally more expensive than single or double-sided flex PCBs. -
Q: What is the minimum feature size for flex PCBs?
A: The minimum feature size for flex PCBs can vary depending on the manufacturer’s capabilities. Typically, the minimum trace width and spacing range from 50μm to 100μm, but some advanced manufacturers may offer even smaller feature sizes. -
Q: Are there any additional costs associated with custom flex PCB designs?
A: Yes, custom flex PCB designs often involve additional engineering efforts, such as design review, prototyping, and testing, which can result in higher costs compared to standard designs. However, the benefits of a custom design, such as improved performance and functionality, may outweigh the additional costs in the long run.
In conclusion, the price of flex PCBs is influenced by a combination of factors, including materials, manufacturing process complexity, order quantity, lead time, quality control, design complexity, geographic location, and shipping. By understanding these factors and working closely with a reliable flex PCB manufacturer, you can optimize your design and production process to achieve the best balance between cost and performance for your specific application.
0 Comments