Understanding the Importance of Proper PCB Component Placement
When designing a printed circuit board (PCB), component placement is a crucial aspect that can significantly impact the board’s performance, reliability, and manufacturability. Proper PCB component placement guidelines help ensure optimal signal integrity, minimize electromagnetic interference (EMI), and facilitate efficient assembly processes. In this comprehensive guide, we will explore the top circuit board component placement guidelines to help you create high-quality and reliable PCBs.
The Benefits of Following PCB Placement Guidelines
Following well-established PCB placement guidelines offers several key benefits:
- Improved signal integrity: Proper component placement reduces signal distortion and crosstalk, ensuring clean and accurate signal transmission.
- Enhanced thermal management: Strategic component placement promotes efficient heat dissipation, preventing overheating and extending the lifespan of components.
- Minimized electromagnetic interference (EMI): Careful placement of sensitive components and proper routing techniques minimize EMI, ensuring compliance with electromagnetic compatibility (EMC) standards.
- Increased manufacturability: Adhering to placement guidelines simplifies the assembly process, reduces the risk of assembly errors, and improves overall production efficiency.
Key Considerations for Optimal Component Placement
When placing components on a PCB, several key factors should be taken into account to ensure optimal performance and reliability.
Signal Integrity and Crosstalk
Signal integrity is a critical consideration in PCB design. Improper component placement can lead to signal distortion, reflections, and crosstalk, which can degrade the overall performance of the circuit. To maintain signal integrity:
- Place sensitive components, such as high-speed devices and analog circuits, away from noisy components like power supplies and digital circuits.
- Keep critical signal traces as short as possible to minimize signal loss and distortion.
- Use ground planes and proper shielding techniques to reduce crosstalk between adjacent signals.
Thermal Management
Effective thermal management is essential to ensure the longevity and reliability of components on a PCB. When placing components:
- Identify heat-generating components, such as power transistors and voltage regulators, and place them in areas with adequate airflow and heat dissipation capabilities.
- Provide sufficient spacing between heat-generating components to prevent thermal coupling and overheating.
- Consider using thermal vias and heat sinks to enhance heat dissipation for high-power components.
Electromagnetic Compatibility (EMC)
Ensuring electromagnetic compatibility is crucial to prevent interference with other electronic devices and comply with EMC regulations. To minimize EMI:
- Separate sensitive analog circuits from noisy digital circuits to prevent interference.
- Place decoupling capacitors close to the power pins of integrated circuits (ICs) to suppress high-frequency noise.
- Use proper grounding techniques, such as star grounding or ground planes, to provide a low-impedance return path for high-frequency currents.
Manufacturability and Assembly
Designing a PCB with manufacturability and assembly in mind can significantly streamline the production process and reduce costs. Consider the following guidelines:
- Adhere to the minimum spacing and clearance requirements specified by the PCB manufacturer to ensure proper fabrication and assembly.
- Place components in a logical and accessible manner to facilitate automated pick-and-place assembly processes.
- Use standardized component packages and orientations to simplify the assembly process and reduce the risk of errors.
Component Placement Techniques for Specific Applications
Different types of circuits and applications may require specific component placement techniques to achieve optimal performance.
Power Supply Circuits
When placing components in power supply circuits:
- Place the power input connector close to the edge of the board to minimize the length of high-current traces.
- Position voltage regulators and power transistors close to the power input to minimize voltage drop and power loss.
- Use wide traces for high-current paths to reduce resistance and improve efficiency.
High-Speed Digital Circuits
For high-speed digital circuits, such as those involving microprocessors and memory devices:
- Place the microprocessor or central processing unit (CPU) at the center of the board to minimize trace lengths and signal delays.
- Position memory devices close to the processor to reduce signal propagation delays and improve system performance.
- Use controlled impedance traces and termination techniques to maintain signal integrity at high frequencies.
Analog and Mixed-Signal Circuits
When designing analog and mixed-signal circuits:
- Separate analog and digital grounds to prevent digital noise from interfering with sensitive analog signals.
- Place analog components away from digital circuits and power supply noise sources.
- Use guard rings or shielding techniques to isolate sensitive analog circuits from external noise sources.
RF and Wireless Circuits
For radio frequency (RF) and wireless applications:
- Place RF components, such as antennas and filters, away from other components to minimize interference.
- Use controlled impedance traces and matching networks to ensure proper impedance matching and signal transmission.
- Implement proper grounding and shielding techniques to reduce EMI and ensure compliance with wireless regulations.
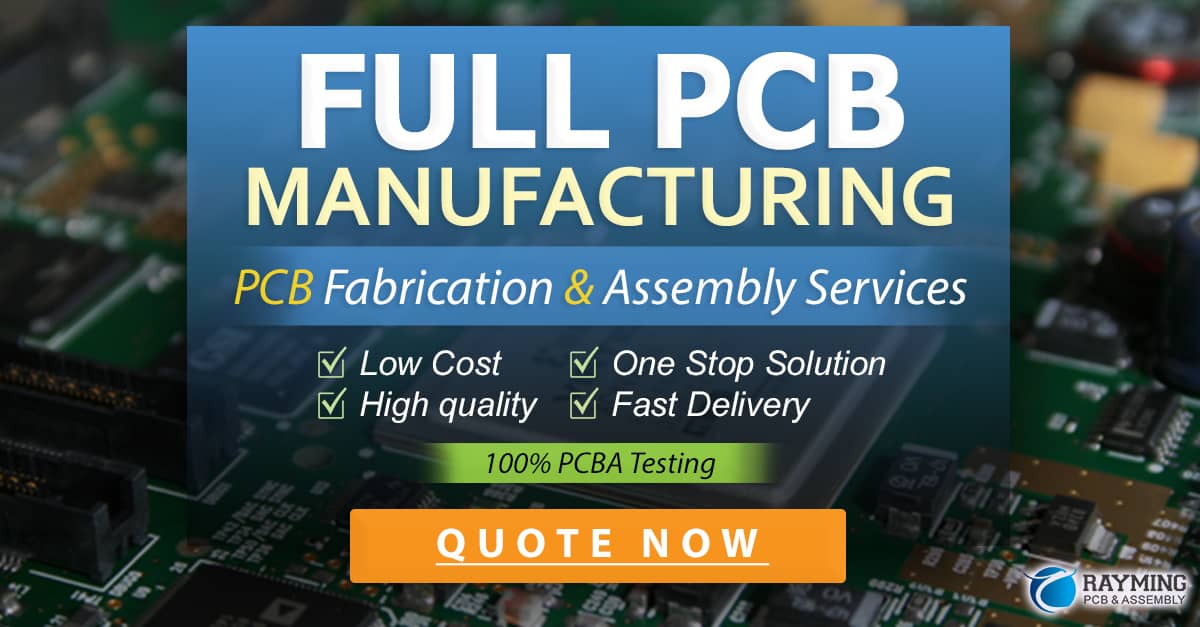
PCB Layout Tools and Automation
Modern PCB design software offers powerful tools and automation features that can significantly simplify the component placement process.
Placement Automation
Many PCB design tools provide automatic component placement capabilities based on predefined rules and constraints. These tools can:
- Optimize component placement for signal integrity, thermal management, and manufacturability.
- Automatically route traces between components based on specified design rules.
- Perform design rule checks (DRC) to ensure compliance with manufacturing guidelines and constraints.
Thermal Analysis
Advanced PCB design software often includes thermal analysis tools that can simulate the thermal behavior of a PCB design. These tools can:
- Identify potential thermal hotspots and areas of concern.
- Optimize component placement and copper distribution to improve heat dissipation.
- Predict the temperature rise of components under various operating conditions.
Signal Integrity Simulation
Signal integrity simulation tools can help designers analyze and optimize the signal quality of high-speed circuits. These tools can:
- Simulate the behavior of signals propagating through the PCB.
- Identify potential signal integrity issues, such as reflections, crosstalk, and signal loss.
- Optimize trace routing and termination strategies to minimize signal distortion and ensure reliable data transmission.
Best Practices for PCB Component Placement
To ensure a successful PCB design, consider the following best practices for component placement:
- Start with a well-organized schematic: A clean and well-structured schematic is the foundation for efficient PCB component placement.
- Define placement constraints: Clearly specify placement constraints, such as component orientation, spacing requirements, and height restrictions, to guide the placement process.
- Use a modular approach: Divide the PCB into functional blocks or modules, and place components within each block based on their interconnections and signal flow.
- Minimize trace lengths: Keep critical signal traces as short as possible to reduce signal loss, distortion, and propagation delays.
- Optimize for manufacturability: Consider the capabilities and limitations of the PCB manufacturing process when placing components, and adhere to the manufacturer’s guidelines.
- Conduct thorough design reviews: Perform regular design reviews to catch potential placement issues early in the design process and make necessary adjustments.
Frequently Asked Questions (FAQ) about PCB Placement Guidelines
1. What is the most important factor to consider when placing components on a PCB?
The most important factor to consider when placing components on a PCB depends on the specific application and requirements of the circuit. However, in general, signal integrity is often the top priority. Proper component placement is crucial to minimize signal distortion, crosstalk, and interference, ensuring reliable and accurate signal transmission throughout the circuit.
2. How can I ensure proper thermal management when placing components on a PCB?
To ensure proper thermal management when placing components on a PCB, follow these guidelines:
– Identify heat-generating components and place them in areas with adequate airflow and heat dissipation capabilities.
– Provide sufficient spacing between heat-generating components to prevent thermal coupling and overheating.
– Use thermal vias and heat sinks to enhance heat dissipation for high-power components.
– Conduct thermal simulations to identify potential hotspots and optimize component placement accordingly.
3. What are some techniques to minimize electromagnetic interference (EMI) in PCB designs?
To minimize EMI in PCB designs, consider the following techniques:
– Separate sensitive analog circuits from noisy digital circuits to prevent interference.
– Place decoupling capacitors close to the power pins of integrated circuits (ICs) to suppress high-frequency noise.
– Use proper grounding techniques, such as star grounding or ground planes, to provide a low-impedance return path for high-frequency currents.
– Implement shielding techniques, such as metal enclosures or guard traces, to isolate sensitive circuits from external noise sources.
4. How can I simplify the assembly process through proper component placement?
To simplify the assembly process through proper component placement, follow these guidelines:
– Adhere to the minimum spacing and clearance requirements specified by the PCB manufacturer to ensure proper fabrication and assembly.
– Place components in a logical and accessible manner to facilitate automated pick-and-place assembly processes.
– Use standardized component packages and orientations to simplify the assembly process and reduce the risk of errors.
– Group components with similar heights and placement requirements to optimize the assembly process.
5. What are the benefits of using PCB layout automation tools for component placement?
Using PCB layout automation tools for component placement offers several benefits:
– Automated placement optimization based on predefined rules and constraints, ensuring optimal signal integrity, thermal management, and manufacturability.
– Automatic trace routing between components, saving time and effort in manual routing.
– Design rule checks (DRC) to ensure compliance with manufacturing guidelines and constraints, reducing the risk of design errors and manufacturing issues.
– Thermal analysis and simulation capabilities to identify potential thermal issues and optimize component placement for better heat dissipation.
– Signal integrity simulation tools to analyze and optimize signal quality in high-speed circuits, minimizing signal distortion and ensuring reliable data transmission.
Conclusion
Proper PCB component placement is a critical aspect of designing reliable, high-performance electronic circuits. By following the guidelines and best practices outlined in this article, you can optimize your PCB designs for signal integrity, thermal management, electromagnetic compatibility, and manufacturability. Consider the specific requirements of your application, leverage the power of PCB layout automation tools, and conduct thorough design reviews to ensure a successful PCB design. By prioritizing component placement and adhering to industry standards and guidelines, you can create PCBs that meet your performance goals and stand the test of time.
0 Comments