Introduction to PCB Plating Methods
Printed Circuit Boards (PCBs) are the backbone of modern electronics, found in virtually every electronic device we use today. The manufacturing process of PCBs involves several critical steps, one of which is plating. PCB plating is the process of depositing a thin layer of metal onto the surface of the PCB to enhance its electrical conductivity, durability, and solderability. There are various PCB plating methods available, each with its own advantages and disadvantages. In this article, we will discuss the top 4 types of plating methods used in PCB manufacturing.
1. Electroplating
What is Electroplating?
Electroplating is one of the most common PCB plating methods used in the industry. It involves using an electric current to deposit a layer of metal onto the surface of the PCB. The PCB is submerged in an electrolyte solution containing dissolved metal ions, and an electric current is applied. The metal ions are attracted to the surface of the PCB, where they are reduced and deposited as a thin layer of metal.
Advantages of Electroplating
- Provides excellent adhesion between the metal layer and the PCB surface
- Offers good electrical conductivity
- Suitable for high-volume production
- Relatively low cost compared to other plating methods
Disadvantages of Electroplating
- Requires a conductive surface on the PCB
- May result in uneven plating thickness
- Can be time-consuming for thicker metal deposits
Common Metals Used in Electroplating
Metal | Advantages | Disadvantages |
---|---|---|
Copper | – Excellent electrical conductivity – Good solderability – Relatively low cost |
– Prone to oxidation – Requires additional protection layer |
Nickel | – Good barrier layer for copper – Provides good corrosion resistance |
– Higher cost than copper – May cause allergic reactions |
Gold | – Excellent corrosion resistance – High electrical conductivity – Ideal for high-reliability applications |
– High cost – Soft and prone to wear |
2. Electroless Plating
What is Electroless Plating?
Electroless plating, also known as chemical or auto-catalytic plating, is a method that deposits a metal layer onto the PCB surface without the use of an external electric current. Instead, it relies on a chemical reaction between the metal ions and a reducing agent in the plating solution. The PCB is submerged in the plating solution, and the metal ions are reduced and deposited onto the surface of the PCB.
Advantages of Electroless Plating
- Does not require a conductive surface on the PCB
- Provides even plating thickness
- Suitable for plating non-conductive surfaces
- Offers good corrosion resistance
Disadvantages of Electroless Plating
- Slower plating process compared to electroplating
- Higher cost than electroplating
- Limited metal options available
Common Metals Used in Electroless Plating
Metal | Advantages | Disadvantages |
---|---|---|
Electroless Nickel Immersion Gold (ENIG) | – Excellent solderability – Good corrosion resistance – Suitable for fine-pitch components |
– Higher cost than other methods – Gold layer may dissolve during soldering |
Electroless Nickel Electroless Palladium Immersion Gold (ENEPIG) | – Combines advantages of ENIG and ENIG – Ideal for high-frequency applications |
– High cost – Complex process control |
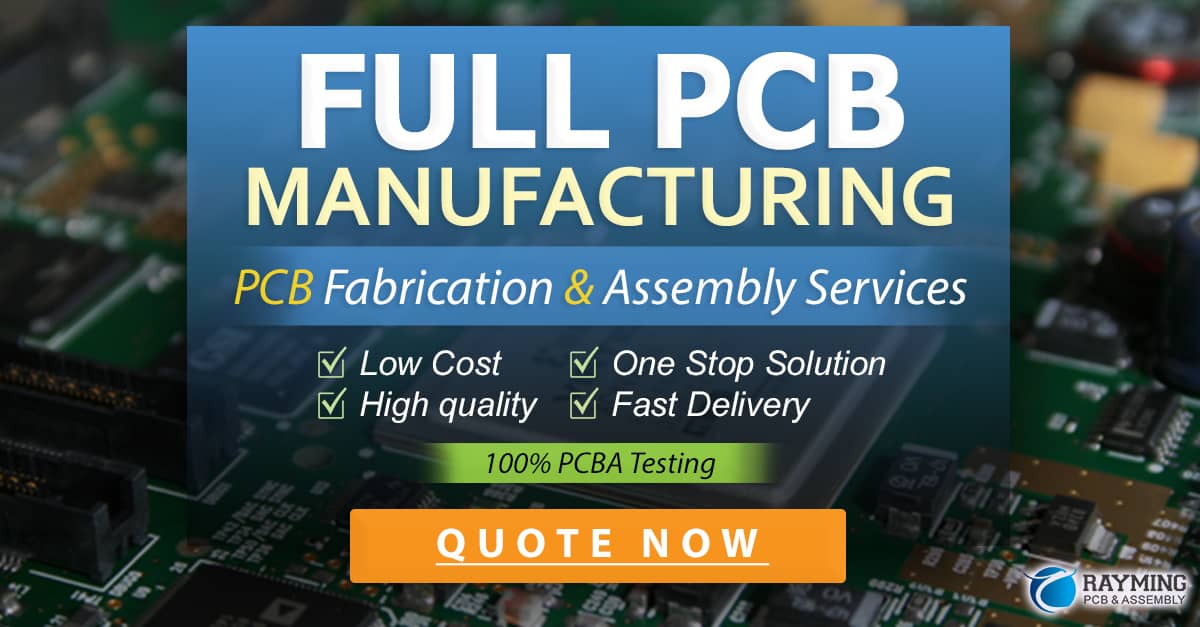
3. Immersion Plating
What is Immersion Plating?
Immersion plating is a simple and cost-effective PCB plating method that involves submerging the PCB in a plating solution containing metal ions. The metal ions are reduced and deposited onto the surface of the PCB through a displacement reaction, where the less noble metal on the PCB surface is replaced by the more noble metal ions in the solution.
Advantages of Immersion Plating
- Simple and cost-effective process
- Suitable for plating non-conductive surfaces
- Provides good solderability
- Fast plating process
Disadvantages of Immersion Plating
- Limited thickness of the metal deposit
- May result in uneven plating thickness
- Not suitable for high-reliability applications
Common Metals Used in Immersion Plating
Metal | Advantages | Disadvantages |
---|---|---|
Immersion Tin | – Good solderability – Relatively low cost |
– Prone to whisker formation – Limited shelf life |
Immersion Silver | – Excellent solderability – Good electrical conductivity |
– Prone to tarnishing – Higher cost than immersion tin |
4. Electrophoretic Deposition (EPD)
What is Electrophoretic Deposition?
Electrophoretic deposition (EPD) is a plating method that uses an electric field to deposit charged particles onto the surface of the PCB. The PCB is submerged in a solution containing charged particles, and an electric field is applied. The charged particles are attracted to the surface of the PCB, where they are deposited as a thin layer.
Advantages of Electrophoretic Deposition
- Provides uniform coating thickness
- Suitable for complex geometries and shapes
- Offers good insulation properties
- Fast deposition process
Disadvantages of Electrophoretic Deposition
- Requires a conductive surface on the PCB
- Limited metal options available
- Higher cost than other plating methods
Common Materials Used in Electrophoretic Deposition
Material | Advantages | Disadvantages |
---|---|---|
Polymer | – Good insulation properties – Suitable for protective coatings |
– Limited electrical conductivity – May require additional curing process |
Ceramic | – Excellent insulation properties – High temperature resistance |
– Brittle and prone to cracking – Higher cost than polymer materials |
Frequently Asked Questions (FAQ)
-
Q: What is the most common PCB plating method used in the industry?
A: Electroplating is the most common PCB plating method used in the industry due to its versatility, cost-effectiveness, and suitability for high-volume production. -
Q: Which PCB plating method is best for high-reliability applications?
A: Electroless plating, particularly Electroless Nickel Immersion Gold (ENIG) and Electroless Nickel Electroless Palladium Immersion Gold (ENEPIG), is often preferred for high-reliability applications due to its excellent corrosion resistance and good solderability. -
Q: Can immersion plating be used for high-reliability applications?
A: Immersion plating is generally not recommended for high-reliability applications due to its limited metal thickness and potential for uneven plating. It is more suitable for less demanding applications where cost is a primary concern. -
Q: What is the advantage of electrophoretic deposition over other plating methods?
A: Electrophoretic deposition offers the advantage of providing uniform coating thickness, even on complex geometries and shapes. It is particularly useful for applying insulating coatings to PCBs. -
Q: Which PCB plating method is the most cost-effective?
A: Immersion plating is generally the most cost-effective PCB plating method due to its simplicity and fast plating process. However, it may not be suitable for all applications, and other factors such as reliability and performance requirements should also be considered when selecting a plating method.
Conclusion
PCB plating is a crucial step in the manufacturing process of printed circuit boards, ensuring good electrical conductivity, durability, and solderability. The choice of plating method depends on various factors, including the specific application requirements, cost considerations, and production volume. Electroplating, electroless plating, immersion plating, and electrophoretic deposition are the top 4 types of PCB plating methods used in the industry, each with its own advantages and disadvantages. By understanding the characteristics and capabilities of each plating method, PCB manufacturers can select the most appropriate option for their specific needs, ensuring the highest quality and reliability of their products.
0 Comments