What is PCB Solderability?
PCB solderability refers to the ability of a printed circuit board (PCB) to accept and form a reliable solder joint with electronic components. It is a crucial factor in determining the quality and reliability of the final assembled PCB. Solderability is influenced by various factors, including the surface finish of the PCB, the cleanliness of the board, and the storage conditions.
Factors Affecting PCB Solderability
Several factors can impact the solderability of a PCB:
-
Surface Finish: The surface finish of the PCB, such as HASL (Hot Air Solder Leveling), ENIG (Electroless Nickel Immersion Gold), or OSP (Organic Solderability Preservative), plays a significant role in solderability. Each surface finish has its own characteristics and affects the wetting and spreading of solder.
-
Cleanliness: Contaminants on the PCB surface, such as flux residue, dust, or oils, can hinder the formation of a proper solder joint. Ensuring a clean PCB surface is essential for good solderability.
-
Storage Conditions: Proper storage of PCBs is crucial to maintain their solderability. Exposure to moisture, high temperatures, or air pollutants can degrade the surface finish and affect solderability over time.
PCB Solderability Testing Methods
To ensure the solderability of PCBs, various testing methods are employed. These tests evaluate the ability of the PCB to form reliable solder joints and assess the quality of the surface finish. Here are some common PCB solderability testing methods:
1. Wetting Balance Test
The wetting balance test is a quantitative method that measures the wetting force and time of a solder joint. It involves dipping a coupon or test piece of the PCB into a solder bath and measuring the force exerted by the molten solder on the test piece. The wetting balance test provides insights into the wetting characteristics of the surface finish and helps determine the solderability of the PCB.
2. Dip and Look Test
The dip and look test is a qualitative method that involves dipping a PCB Test Coupon into a solder bath for a specified time and then visually inspecting the solder coverage and appearance. This test provides a quick assessment of the solderability of the PCB surface finish. The results are evaluated based on criteria such as the percentage of solder coverage, the presence of dewetting or non-wetting areas, and the overall appearance of the solder joint.
3. Edge Dip Test
The edge dip test is similar to the dip and look test but focuses on the solderability of the PCB edges. It involves dipping the edge of a PCB test coupon into a solder bath and visually inspecting the solder coverage and wetting along the edge. This test is particularly important for assessing the solderability of PCBs with edge connectors or Castellated Holes.
4. Solderability Testing with Test Coupons
Test coupons are specially designed PCB samples that mimic the characteristics of the actual PCB. They are used for solderability testing to evaluate the performance of the surface finish and the solder joint formation. Test coupons can be subjected to various solderability tests, such as the wetting balance test or the dip and look test, to assess the solderability of the PCB.
Interpreting Solderability Test Results
Interpreting the results of solderability tests is crucial for determining the quality and reliability of the PCB. Here are some key aspects to consider when interpreting solderability test results:
1. Wetting Force and Time
In the wetting balance test, the wetting force and time provide quantitative measurements of the solderability. A higher wetting force indicates better solderability, as it suggests a stronger interaction between the molten solder and the PCB surface. Similarly, a shorter wetting time indicates faster wetting and spreading of the solder, which is desirable for good solderability.
2. Solder Coverage and Appearance
In the dip and look test and the edge dip test, the solder coverage and appearance are visually inspected. Good solderability is characterized by uniform solder coverage, absence of dewetting or non-wetting areas, and a smooth and shiny solder joint. Any irregularities, such as incomplete coverage, rough or dull solder appearance, or the presence of voids, indicate potential solderability issues.
3. Comparison with Acceptance Criteria
Solderability test results are typically compared against predefined acceptance criteria or industry standards. These criteria specify the minimum requirements for wetting force, wetting time, solder coverage, and appearance. If the test results meet or exceed the acceptance criteria, the PCB is considered to have good solderability. However, if the results fall below the criteria, it indicates solderability issues that need to be addressed.
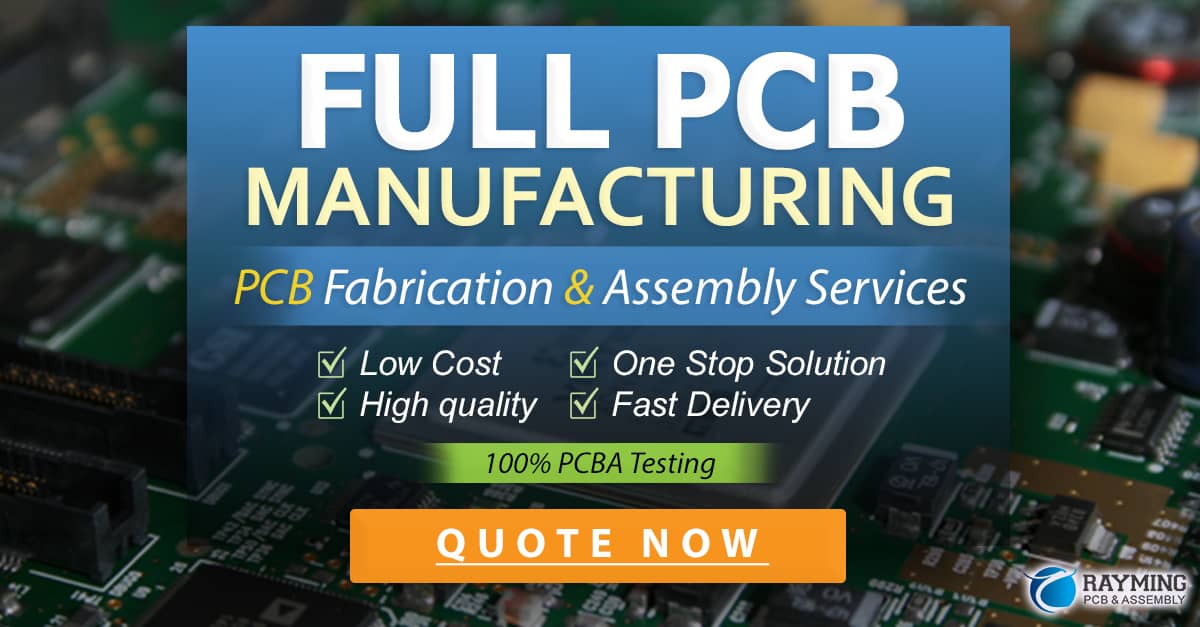
PCB Functionality Testing
In addition to solderability testing, PCB functionality testing is essential to ensure the proper operation of the assembled PCB. Functionality testing verifies that the PCB performs as intended and meets the specified requirements. Here are some common PCB functionality testing methods:
1. In-Circuit Testing (ICT)
In-circuit testing involves testing individual components and their interconnections on the PCB using specialized test probes. ICT verifies the presence, orientation, and value of components, as well as the integrity of the solder joints. It helps identify manufacturing defects, such as missing or incorrect components, shorts, or opens in the circuit.
2. Functional Testing
Functional testing evaluates the overall functionality of the assembled PCB by simulating its intended operation. It involves applying input signals and verifying the expected outputs. Functional testing ensures that the PCB performs according to the design specifications and meets the desired functionality.
3. Boundary Scan Testing
Boundary scan testing, also known as JTAG (Joint Test Action Group) testing, is a method that uses a standardized interface to test the interconnections between components on the PCB. It allows for the testing of internal nodes and paths that are not accessible by traditional test probes. Boundary scan testing is particularly useful for testing high-density PCBs with fine-pitch components.
Frequently Asked Questions (FAQ)
-
What is the importance of PCB solderability testing?
PCB solderability testing is crucial to ensure the reliability and quality of the solder joints between the PCB and electronic components. It helps identify any solderability issues that may lead to poor solder joint formation, which can cause failures or malfunctions in the final assembled product. -
How often should PCB solderability testing be performed?
PCB solderability testing should be performed during the initial qualification of a new PCB design or when there are changes in the manufacturing process, such as a change in the surface finish or solder paste. It is also recommended to periodically test the solderability of PCBs in production to monitor and maintain the quality of the solder joints. -
What are the most common surface finishes used for PCBs?
The most common surface finishes used for PCBs include: - HASL (Hot Air Solder Leveling)
- ENIG (Electroless Nickel Immersion Gold)
- OSP (Organic Solderability Preservative)
- Immersion Silver
-
Immersion Tin
-
Can PCB solderability be improved after manufacturing?
Once a PCB is manufactured, it is challenging to significantly improve its solderability. However, some measures can be taken to enhance solderability, such as proper storage to prevent contamination or oxidation, and thorough cleaning of the PCB surface prior to soldering. -
What are the consequences of poor PCB solderability?
Poor PCB solderability can lead to various issues, including: - Weak or unreliable solder joints
- Increased risk of solder joint failures
- Difficulty in assembling components onto the PCB
- Reduced manufacturing yield and increased rework
- Potential reliability issues in the final product
Conclusion
PCB solderability testing is a vital process in ensuring the quality and reliability of printed circuit boards. By evaluating the ability of the PCB to form reliable solder joints, solderability testing helps identify and address any issues related to the surface finish, cleanliness, or storage conditions. Various testing methods, such as the wetting balance test, dip and look test, and edge dip test, provide quantitative and qualitative assessments of PCB solderability.
In addition to solderability testing, PCB functionality testing is equally important to verify the proper operation of the assembled PCB. Methods like in-circuit testing, functional testing, and boundary scan testing help identify manufacturing defects and ensure that the PCB meets the specified functional requirements.
By implementing a comprehensive PCB solderability and functionality testing program, manufacturers can enhance the quality and reliability of their PCBs, reduce the risk of failures, and improve customer satisfaction. Regular testing, adherence to industry standards, and continuous monitoring of the manufacturing process are key to maintaining high standards in PCB production.
0 Comments