What is a PCB Core?
A PCB core, also known as a substrate or base material, is the foundation of a printed circuit board (PCB). It is a thin, rigid board made from a dielectric material, typically fiberglass, that provides mechanical support and electrical insulation for the copper traces and components that make up the PCB. The core is usually coated with a thin layer of copper on one or both sides, which is etched to create the desired circuit pattern.
PCB cores come in various thicknesses and materials, depending on the specific requirements of the PCB design. The most common type of PCB core is FR-4, which is made from a flame-retardant epoxy resin reinforced with glass fibers. Other types of PCB cores include:
- CEM-1 and CEM-3: Composite epoxy materials with lower cost and performance compared to FR-4
- Polyimide: High-temperature resistant material for aerospace and military applications
- PTFE (Teflon): Low dielectric constant material for high-frequency applications
- Aluminum: Metal core for improved heat dissipation in power electronics
The choice of PCB core material depends on factors such as the operating temperature range, frequency, dielectric constant, loss tangent, and cost.
Properties of PCB Core Materials
Material | Dielectric Constant | Loss Tangent | Temperature Range (°C) | Cost |
---|---|---|---|---|
FR-4 | 4.2 – 4.8 | 0.02 – 0.03 | -50 to +130 | Low |
CEM-1 | 4.2 – 4.8 | 0.02 – 0.03 | -50 to +105 | Low |
CEM-3 | 4.2 – 4.8 | 0.02 – 0.03 | -50 to +105 | Low |
Polyimide | 3.4 – 3.8 | 0.002 – 0.01 | -269 to +400 | High |
PTFE | 2.1 – 2.5 | 0.0004 – 0.001 | -73 to +260 | High |
Aluminum | N/A | N/A | -50 to +150 | Medium |
What is Prepreg?
Prepreg, short for pre-impregnated, is a composite material used in the manufacturing of multi-layer PCBs. It consists of a reinforcement fabric, such as glass or aramid fibers, that is pre-impregnated with a partially cured thermosetting resin, typically epoxy. The prepreg is placed between the PCB core layers and subjected to heat and pressure, causing the resin to flow and bond the layers together, forming a solid, unified structure.
Prepregs are available in various types, each with different properties and applications. The most common types of prepregs used in PCB manufacturing are:
- FR-4 prepreg: Made from epoxy resin reinforced with glass fibers, similar to the FR-4 core material
- High Tg prepreg: Uses a resin with a higher glass transition temperature (Tg) for improved thermal stability and reliability
- Low Dk/Df prepreg: Has a lower dielectric constant (Dk) and dissipation factor (Df) for high-frequency applications
- Halogen-free prepreg: Uses a resin without halogenated flame retardants for environmental and safety reasons
The choice of prepreg material depends on the specific requirements of the PCB design, such as the operating temperature range, frequency, dielectric constant, loss tangent, and thermal expansion coefficient.
Properties of Common Prepreg Materials
Material | Dielectric Constant | Loss Tangent | Tg (°C) | CTE (ppm/°C) |
---|---|---|---|---|
FR-4 prepreg | 4.2 – 4.8 | 0.02 – 0.03 | 130-180 | 12-16 |
High Tg prepreg | 3.8 – 4.2 | 0.01 – 0.02 | >180 | 10-14 |
Low Dk/Df prepreg | 3.0 – 3.5 | 0.002 – 0.005 | 130-180 | 12-16 |
Halogen-free prepreg | 4.0 – 4.6 | 0.02 – 0.03 | 130-180 | 12-16 |
Key Differences between PCB Core and Prepreg Materials
- Composition:
- PCB core is a solid, rigid board made from a dielectric material, typically fiberglass, with a thin layer of copper on one or both sides.
-
Prepreg is a composite material consisting of a reinforcement fabric pre-impregnated with a partially cured thermosetting resin.
-
Function:
- PCB core serves as the foundation of the PCB, providing mechanical support and electrical insulation for the copper traces and components.
-
Prepreg is used to bond the PCB core layers together in multi-layer PCBs, forming a solid, unified structure.
-
Manufacturing Process:
- PCB cores are manufactured by laminating the dielectric material with copper foil and then etching the copper to create the desired circuit pattern.
-
Prepregs are made by impregnating the reinforcement fabric with a partially cured resin and then subjecting it to heat and pressure to bond the PCB layers together.
-
Availability:
- PCB cores are available in a wide range of materials, thicknesses, and copper weights to suit various applications.
-
Prepregs are available in different types, each with specific properties and applications, such as FR-4, high Tg, low Dk/Df, and halogen-free.
-
Cost:
- The cost of PCB cores varies depending on the material, thickness, and copper weight, with FR-4 being the most cost-effective option for general-purpose applications.
- Prepregs are generally more expensive than PCB cores due to the additional processing steps involved in their manufacturing.
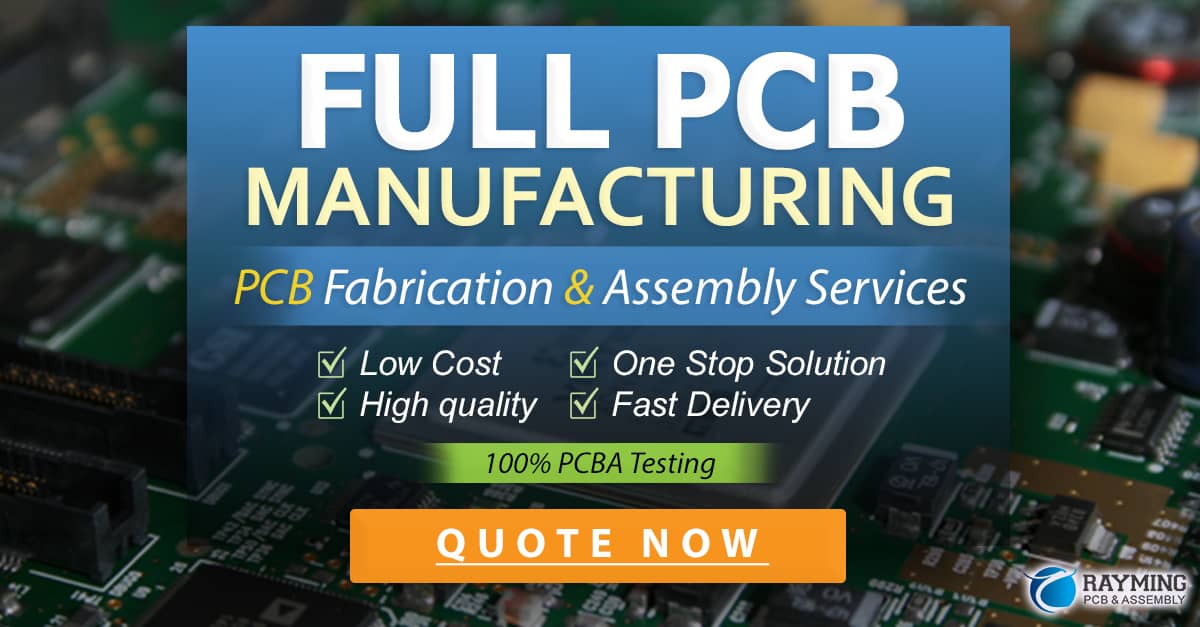
FAQ
-
Q: Can I use a different prepreg material than the PCB core material?
A: Yes, you can use different prepreg and core materials in the same PCB, as long as they are compatible and meet the design requirements. For example, you can use a low Dk/Df prepreg with an FR-4 core for high-frequency applications. -
Q: What is the purpose of using multiple prepreg layers in a PCB?
A: Multiple prepreg layers are used to achieve the desired thickness and dielectric properties of the PCB. They also help to distribute the resin evenly between the layers, ensuring a strong and reliable bond. -
Q: Can I use a PCB core without prepreg?
A: Yes, you can use a single-layer PCB core without prepreg for simple, low-cost applications. However, for multi-layer PCBs, prepreg is necessary to bond the layers together and achieve the desired thickness and dielectric properties. -
Q: How do I select the right PCB core and prepreg materials for my design?
A: When selecting PCB core and prepreg materials, consider factors such as the operating temperature range, frequency, dielectric constant, loss tangent, thermal expansion coefficient, and cost. Consult with your PCB manufacturer or material supplier for guidance on choosing the most suitable materials for your specific application. -
Q: What are the environmental and safety considerations when choosing PCB core and prepreg materials?
A: Some PCB core and prepreg materials may contain hazardous substances, such as halogenated flame retardants, which can pose environmental and health risks. To address these concerns, halogen-free and eco-friendly materials are available, such as halogen-free prepregs and PCB cores made from recycled materials. Always consider the environmental and safety aspects when selecting materials for your PCB design.
In conclusion, understanding the differences between PCB core and prepreg materials is crucial for designing and manufacturing reliable and high-performance printed circuit boards. By selecting the appropriate materials based on the specific requirements of your application, you can ensure the optimal performance, reliability, and cost-effectiveness of your PCB design.
0 Comments