What Are PCB Stencils?
PCB stencils, also known as solder paste stencils, are thin metal sheets with precise openings that correspond to the pads on a printed circuit board (PCB). These stencils are used to apply solder paste onto the PCB pads before component placement and soldering. The stencil ensures that the correct amount of solder paste is deposited on each pad, which is crucial for achieving reliable solder joints and proper functioning of the electronic device.
Types of PCB Stencils
There are several types of PCB stencils available, each with its own advantages and disadvantages:
-
Laser-Cut Stencils: These stencils are made by cutting the openings using a high-precision laser. They offer excellent accuracy and durability, making them suitable for high-volume production.
-
Chemical-etched stencils: These stencils are created by chemically etching the openings into the metal sheet. They are less expensive than laser-cut stencils but may not be as accurate or durable.
-
Electroformed stencils: These stencils are made by electroplating nickel onto a photoresist-patterned substrate. They offer high accuracy and fine pitch capabilities, making them ideal for complex PCB designs.
Stencil Type | Advantages | Disadvantages |
---|---|---|
Laser-cut | High accuracy, durability | Higher cost |
Chemical-etched | Lower cost | Lower accuracy, less durable |
Electroformed | High accuracy, fine pitch capabilities | Higher cost, longer lead times |
The Importance of PCB Stencils in the Fabrication Process
Ensuring Proper Solder Paste Deposition
One of the most critical roles of PCB stencils is to ensure that the correct amount of solder paste is deposited on each pad. Too much solder paste can lead to bridging between adjacent pads, while too little solder paste can result in weak solder joints or open circuits. The stencil’s openings are precisely designed to match the size and shape of the PCB pads, allowing for the optimal amount of solder paste to be applied.
Maintaining Consistency and Repeatability
PCB stencils help maintain consistency and repeatability in the solder paste application process. By using a stencil, the same amount of solder paste is applied to each pad on every PCB, ensuring that the soldering process is uniform across all boards. This consistency is essential for high-volume production, where even small variations can lead to significant quality issues and increased manufacturing costs.
Enabling Fine Pitch Components
As electronic devices become smaller and more complex, PCBs must accommodate components with increasingly fine pitch (the distance between the leads or pads). PCB stencils play a crucial role in enabling the use of fine pitch components by allowing for precise solder paste deposition on the tiny pads. Without the use of stencils, it would be extremely difficult, if not impossible, to achieve reliable soldering of fine pitch components.
Improving Production Efficiency
PCB stencils also contribute to improved production efficiency by streamlining the solder paste application process. Without stencils, applying solder paste to PCB pads would be a time-consuming and labor-intensive task, requiring skilled operators and specialized equipment. By using stencils, the process can be automated, reducing the time and labor required for solder paste application and increasing overall production throughput.
Factors Affecting PCB Stencil Performance
Several factors can impact the performance of PCB stencils and, consequently, the quality of the solder paste deposition:
-
Stencil thickness: The thickness of the stencil determines the amount of solder paste deposited on the pads. Thicker stencils deposit more solder paste, while thinner stencils deposit less. Choosing the appropriate stencil thickness is crucial for achieving the desired solder joint quality.
-
Aperture size and shape: The size and shape of the stencil openings (apertures) must match the size and shape of the PCB pads. Incorrectly sized or shaped apertures can lead to insufficient or excessive solder paste deposition, resulting in soldering defects.
-
Stencil material: The choice of stencil material can affect its durability, accuracy, and ease of cleaning. Common stencil materials include stainless steel, nickel, and polyimide. Each material has its own advantages and disadvantages, and the selection depends on the specific requirements of the PCB Fabrication process.
-
Stencil cleaning and maintenance: Regular cleaning and maintenance of PCB stencils are essential for ensuring consistent performance and preventing solder paste contamination. Improper cleaning or lack of maintenance can lead to clogged apertures, uneven solder paste deposition, and reduced stencil life.
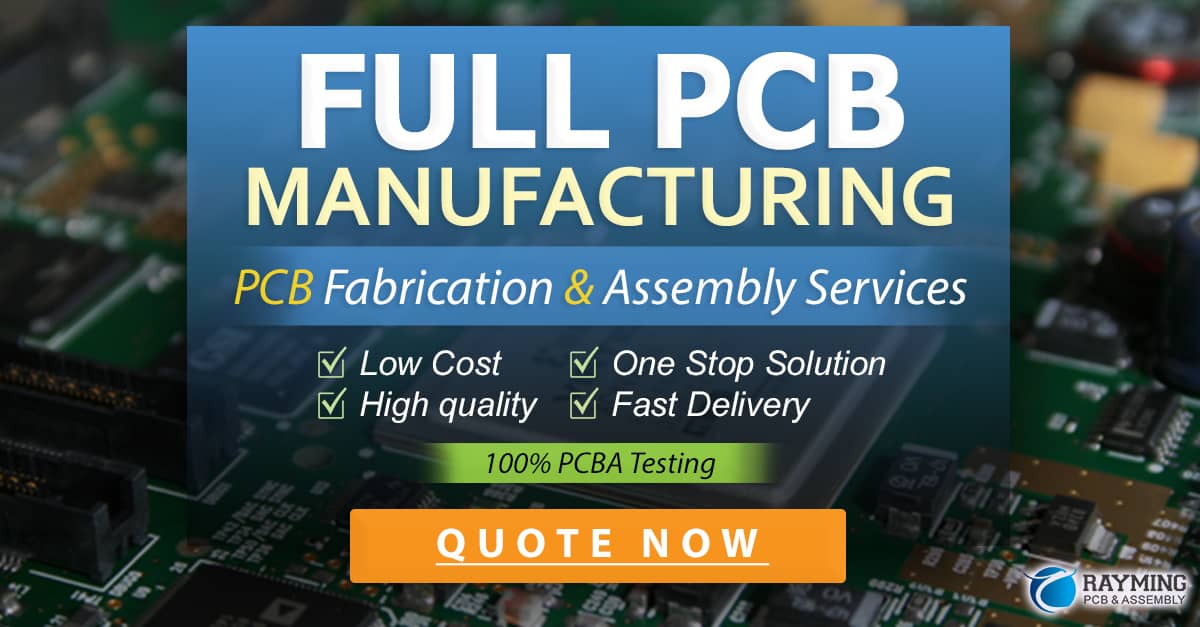
Best Practices for PCB Stencil Design and Usage
To optimize the performance of PCB stencils and ensure high-quality solder paste deposition, consider the following best practices:
-
Collaborate with your stencil manufacturer: Work closely with your stencil manufacturer to ensure that the stencil design is optimized for your specific PCB layout and manufacturing process. They can provide valuable advice on stencil thickness, aperture design, and material selection.
-
Use appropriate aperture design: Ensure that the stencil apertures are correctly sized and shaped to match the PCB pads. Consider factors such as pad size, shape, and pitch when designing the apertures. In some cases, custom aperture shapes may be necessary to achieve the desired solder paste deposition.
-
Implement proper stencil cleaning and maintenance: Establish a regular cleaning and maintenance schedule for your PCB stencils. Use appropriate cleaning solutions and methods to remove solder paste residue and prevent aperture clogging. Properly store stencils when not in use to prevent damage and contamination.
-
Monitor solder paste deposition quality: Regularly inspect the solder paste deposition quality to identify any issues related to the stencil or solder paste application process. Use automated solder paste inspection (SPI) systems to detect defects such as insufficient or excessive solder paste, bridging, or misalignment.
-
Optimize stencil and PCB design for manufacturability: When designing PCBs and stencils, consider the manufacturability of the final product. Follow design for manufacturing (DFM) guidelines to ensure that the PCB layout and stencil design are optimized for efficient and reliable production.
Frequently Asked Questions (FAQ)
-
What is the difference between a solder paste stencil and a solder mask?
A solder paste stencil is used to apply solder paste onto the PCB pads before component placement and soldering. In contrast, a solder mask is a protective layer applied to the PCB surface to prevent solder from adhering to non-pad areas during the soldering process. -
Can PCB stencils be reused?
Yes, PCB stencils can be reused multiple times if they are properly cleaned and maintained. However, the stencil’s life span depends on factors such as the material, thickness, and frequency of use. It is essential to inspect stencils regularly for signs of wear or damage and replace them when necessary. -
How do I choose the right stencil thickness for my PCB?
The choice of stencil thickness depends on several factors, including the size and pitch of the components, the desired solder joint profile, and the solder paste properties. As a general rule, thicker stencils are used for larger components and higher-volume solder joints, while thinner stencils are used for smaller components and finer pitch devices. Consult with your stencil manufacturer for guidance on selecting the appropriate thickness for your specific application. -
What are step stencils, and when are they used?
Step stencils, also known as multi-level stencils, have different thicknesses in different areas of the stencil. They are used when a PCB has components with varying heights or when different amounts of solder paste are required for different components. Step stencils allow for the deposition of the appropriate amount of solder paste for each component type, ensuring optimal solder joint quality. -
How can I prevent solder paste from sticking to the PCB stencil?
To prevent solder paste from sticking to the PCB stencil, consider the following tips: - Ensure that the stencil is properly cleaned and free of solder paste residue before use.
- Use a stencil with a smooth, polished surface to reduce solder paste adhesion.
- Apply a thin layer of stencil release agent or nano-coating to the stencil surface to prevent solder paste from sticking.
- Optimize the solder paste printing process parameters, such as squeegee pressure, speed, and angle, to minimize solder paste adhesion to the stencil.
Conclusion
PCB stencils play a critical role in the fabrication of high-quality printed circuit boards. They ensure proper solder paste deposition, maintain consistency and repeatability, enable the use of fine pitch components, and improve overall production efficiency. By understanding the importance of PCB stencils and following best practices for their design and usage, manufacturers can optimize their PCB Assembly processes and produce reliable, high-performance electronic devices.
As the electronics industry continues to evolve, with increasing demands for smaller, more complex devices, the role of PCB stencils will remain crucial. Advancements in stencil manufacturing technologies, such as the development of ultra-fine pitch stencils and the use of advanced materials, will help meet the challenges of future PCB fabrication requirements.
By partnering with experienced stencil manufacturers and staying up-to-date with the latest industry trends and best practices, PCB Manufacturers can ensure that their stencils continue to play a vital role in producing high-quality, reliable electronic products.
0 Comments