What is a PCB Annular Ring?
A PCB annular ring, also known as a pad or land, is a circular copper area surrounding a drilled hole on a printed circuit board (PCB). These rings provide electrical connections between the components mounted on the PCB and the copper traces that carry signals across the board. The annular ring plays a crucial role in ensuring the reliability and integrity of the electrical connections within the PCB.
Key Features of PCB Annular Rings
- Size: The size of the annular ring is determined by the diameter of the drilled hole and the width of the copper ring surrounding it.
- Material: Annular rings are typically made of copper, the same material used for the conductive traces on the PCB.
- Plating: To enhance the electrical conductivity and protect against corrosion, annular rings are often plated with materials such as gold, silver, or tin.
Importance of PCB Annular Rings
Electrical Connectivity
The primary function of a PCB annular ring is to provide a reliable electrical connection between the component leads and the copper traces on the board. The ring ensures that there is sufficient contact area for the electrical current to flow through, minimizing resistance and preventing signal loss.
Mechanical Stability
In addition to electrical connectivity, annular rings also contribute to the mechanical stability of the components mounted on the PCB. The rings help to distribute the mechanical stress around the drilled hole, reducing the risk of cracks or damage to the board during the assembly process or when the PCB is subjected to vibrations or shocks.
Manufacturing Process
The presence of annular rings is crucial during the PCB manufacturing process, particularly during the drilling and plating stages. The rings act as a buffer zone, allowing for slight misalignments or variations in the drilling process without compromising the electrical connections. This tolerance is essential for maintaining high yields and reducing manufacturing defects.
Designing PCB Annular Rings
Factors to Consider
When designing PCB annular rings, several factors must be taken into account to ensure optimal performance and reliability:
- Hole size: The diameter of the drilled hole determines the minimum size of the annular ring. The ring must be large enough to accommodate the hole and provide sufficient contact area for electrical connectivity.
- Copper thickness: The thickness of the copper layer on the PCB affects the current-carrying capacity of the annular ring. Thicker copper layers allow for larger currents to flow through the ring without causing excessive heating or damage.
- Clearance: Adequate clearance must be maintained between the annular ring and adjacent copper features, such as traces or other rings, to prevent short circuits or signal interference.
- Thermal considerations: In high-power applications, the annular rings must be designed to dissipate heat efficiently to prevent thermal damage to the PCB or components.
Design Guidelines
To ensure the optimal performance of PCB annular rings, follow these design guidelines:
- Adhere to the minimum annular ring size specified by the PCB manufacturer or industry standards, such as IPC-2221.
- Maintain a consistent annular ring size across the entire PCB to ensure uniform electrical and mechanical properties.
- Use appropriate copper thicknesses based on the current requirements of the components and the overall PCB design.
- Incorporate thermal relief patterns, such as spokes or teardrops, to improve heat dissipation around the annular rings in high-power applications.
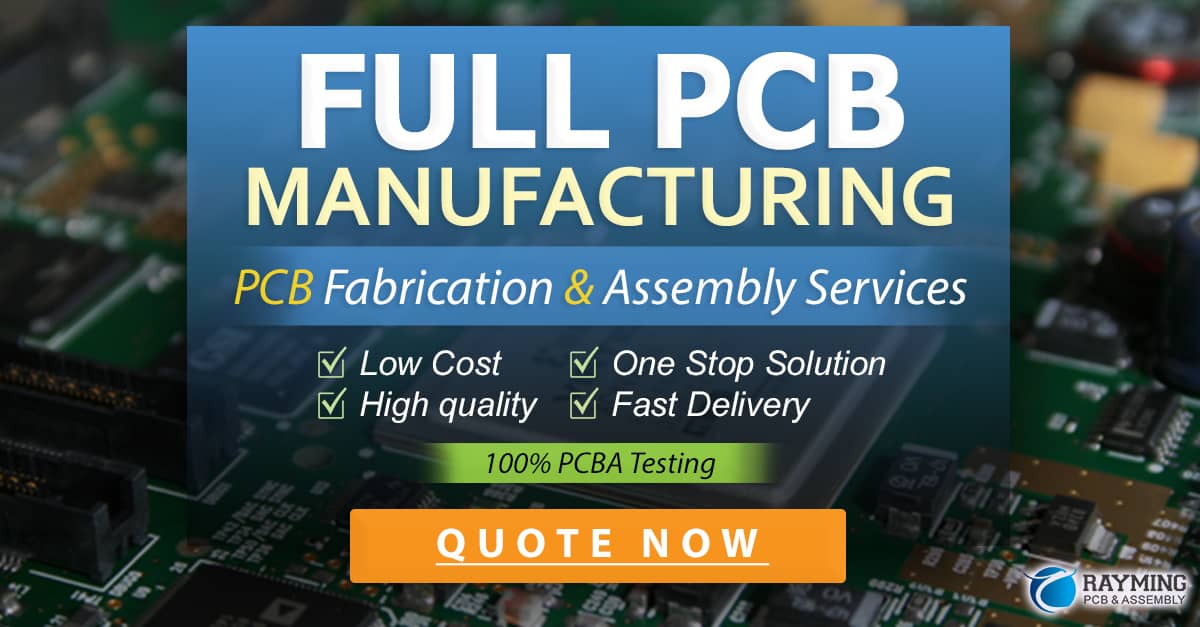
Common Issues and Solutions
Insufficient Annular Ring Size
If the annular ring is too small, it may not provide adequate electrical connectivity or mechanical stability. This can lead to signal loss, intermittent connections, or even component failure. To avoid this issue, ensure that the annular ring size meets the minimum requirements specified by the PCB manufacturer or industry standards.
Overplating or Underplating
Inconsistencies in the plating process can result in annular rings that are either overplated or underplated. Overplating can cause the rings to be too thick, leading to difficulties in component assembly or soldering. Underplating, on the other hand, can result in thin, fragile rings that are prone to damage or poor electrical connectivity. To mitigate these issues, work closely with the PCB manufacturer to ensure that the plating process is well-controlled and consistently monitored.
Misalignment or Breakouts
During the drilling process, misalignments or breakouts can occur, resulting in damaged or incomplete annular rings. These defects can compromise the electrical and mechanical integrity of the PCB. To minimize the risk of misalignments or breakouts, use accurate drilling equipment, employ proper drilling techniques, and incorporate sufficient tolerances in the PCB design.
Testing and Inspection
To ensure the quality and reliability of PCB annular rings, regular testing and inspection should be carried out throughout the manufacturing process and before the final assembly.
Visual Inspection
Visual inspection is the first line of defense against annular ring defects. Trained operators or automated optical inspection (AOI) systems can quickly identify issues such as incomplete rings, breakouts, or overplating. Visual inspection should be performed after the drilling, plating, and etching processes to catch any defects early in the manufacturing cycle.
Electrical Testing
Electrical testing is essential to verify the continuity and resistance of the annular rings. Common testing methods include:
- Continuity testing: This test checks for electrical continuity between the annular ring and the corresponding copper trace. It helps to identify open circuits or high-resistance connections.
- Insulation resistance testing: This test measures the resistance between adjacent annular rings or between the ring and the PCB substrate. It helps to detect short circuits or leakage paths.
- High-potential (hipot) testing: This test applies a high voltage between the annular ring and the PCB substrate to check for insulation breakdown or leakage currents.
Microsectioning
In some cases, destructive testing methods like microsectioning may be necessary to assess the quality of the annular rings. Microsectioning involves cutting a cross-section of the PCB and examining the annular rings under a microscope. This technique allows for the evaluation of plating thickness, hole wall quality, and the presence of any internal defects.
Best Practices for PCB Annular Ring Design and Manufacturing
To optimize the performance and reliability of PCB annular rings, consider the following best practices:
- Collaborate closely with the PCB manufacturer throughout the design and manufacturing process to ensure that the annular ring specifications are clearly communicated and adhered to.
- Use industry-standard design tools and CAD software to create accurate and efficient PCB layouts that incorporate appropriate annular ring sizes and clearances.
- Employ robust design for manufacturing (DFM) techniques to minimize the risk of defects and improve the overall quality of the PCB.
- Implement strict quality control measures, including regular testing and inspection, to catch any issues early in the manufacturing process and prevent defective PCBs from reaching the final assembly stage.
- Stay up-to-date with the latest industry standards and guidelines, such as IPC-2221 and IPC-6012, to ensure that your PCB designs and manufacturing processes are in line with best practices and customer requirements.
Frequently Asked Questions (FAQ)
-
What is the minimum annular ring size required for a PCB?
The minimum annular ring size depends on various factors, such as the PCB material, copper thickness, and the specific requirements of the application. Generally, the minimum annular ring size is determined by the PCB manufacturer or industry standards, such as IPC-2221. Consult with your PCB manufacturer to determine the appropriate minimum annular ring size for your design. -
Can annular rings be repaired if they are damaged during the manufacturing process?
In some cases, minor defects in the annular rings can be repaired using techniques such as manual soldering or conductive epoxy filling. However, these repairs should be considered temporary and may not provide the same level of reliability as a properly manufactured annular ring. If the damage is extensive or affects multiple annular rings, it is usually recommended to scrap the affected PCB and produce a new one. -
How do I choose the appropriate copper thickness for my PCB annular rings?
The copper thickness for your PCB annular rings should be selected based on the current-carrying requirements of your components and the overall PCB design. Thicker copper layers allow for higher current-carrying capacity but may increase the cost and complexity of the manufacturing process. Consult with your PCB manufacturer and refer to industry standards to determine the appropriate copper thickness for your application. -
What are thermal relief patterns, and when should they be used in annular ring design?
Thermal relief patterns, such as spokes or teardrops, are design features that help to dissipate heat around the annular rings in high-power applications. These patterns create a balance between electrical conductivity and thermal dissipation, preventing excessive heat buildup that could damage the PCB or components. Thermal relief patterns should be used when the components mounted on the PCB generate significant amounts of heat or when the PCB is exposed to high-temperature environments. -
How can I ensure the consistency and quality of the annular rings on my PCBs?
To ensure the consistency and quality of the annular rings on your PCBs, follow these steps: - Collaborate closely with your PCB manufacturer and communicate your requirements clearly.
- Use industry-standard design tools and adhere to best practices for PCB layout and design.
- Implement strict quality control measures, including regular testing and inspection.
- Stay up-to-date with industry standards and guidelines to ensure compliance and consistency.
- Consider using automated inspection systems, such as AOI, to detect defects early in the manufacturing process.
Conclusion
PCB annular rings play a critical role in ensuring the reliability, performance, and longevity of electronic devices. By understanding the importance of annular rings, implementing best practices for design and manufacturing, and adhering to industry standards, you can create high-quality PCBs that meet the demands of your applications. Remember to collaborate closely with your PCB manufacturer, employ rigorous testing and inspection techniques, and stay informed about the latest advancements in PCB technology to stay ahead of the curve in this ever-evolving industry.
0 Comments