What is LPI Soldermask?
LPI (Liquid Photo Imageable) soldermask is a type of protective coating applied to printed circuit boards (PCBs) to protect the copper traces from oxidation, prevent solder bridges, and provide electrical insulation. It is a photosensitive polymer that is applied as a liquid and then cured using UV light. LPI soldermask is the most widely used soldermask in the PCB industry due to its excellent performance, durability, and ease of application.
Advantages of LPI Soldermask
- High resolution and accuracy
- Excellent adhesion to the PCB surface
- Good chemical and heat resistance
- Provides excellent electrical insulation
- Available in various colors for easy identification
Silk Screen Printing: The Most Common LPI Soldermask Application Method
Silk screen printing, also known as screen printing, is the most common method for applying LPI soldermask to PCBs. This technique involves using a fine mesh screen to transfer the soldermask onto the PCB surface. The screen is coated with a photosensitive emulsion that hardens when exposed to UV light, creating a stencil of the desired soldermask pattern.
The Silk Screen Printing Process
-
Screen Preparation: A fine mesh screen is coated with a photosensitive emulsion and allowed to dry.
-
Artwork Creation: The soldermask artwork is created using CAD software, and a film positive or negative is generated.
-
Exposure: The film is placed on the emulsion-coated screen, and UV light is used to expose the emulsion. The areas exposed to UV light harden, while the unexposed areas remain soluble.
-
Developing: The screen is washed with water to remove the unexposed emulsion, leaving a stencil of the soldermask pattern on the screen.
-
Alignment: The PCB is aligned with the screen using registration marks to ensure accurate placement of the soldermask.
-
Printing: The LPI soldermask is applied to the screen and forced through the mesh onto the PCB surface using a squeegee.
-
Curing: The PCB with the applied soldermask is then placed in a UV oven to cure the soldermask, making it hard and durable.
Advantages of Silk Screen Printing for LPI Soldermask Application
- High throughput and efficiency
- Cost-effective for large production runs
- Consistent and repeatable results
- Ability to print on various PCB surfaces and materials
- Wide range of soldermask colors available
Factors Affecting Silk Screen Printing Quality
Several factors can impact the quality of silk screen printed LPI soldermask:
-
Screen Mesh Count: The number of threads per inch in the screen mesh affects the resolution and thickness of the applied soldermask. Higher mesh counts result in thinner and more precise soldermask layers.
-
Emulsion Thickness: The thickness of the photosensitive emulsion on the screen determines the depth of the stencil and the amount of soldermask deposited on the PCB. Thicker emulsions lead to thicker soldermask layers.
-
Squeegee Pressure and Angle: The pressure applied to the squeegee and its angle relative to the screen influence the amount of soldermask pushed through the mesh and the uniformity of the coating.
-
Soldermask Viscosity: The viscosity of the LPI soldermask affects its flow characteristics and the ease with which it passes through the screen mesh. Soldermasks with the appropriate viscosity ensure proper coverage and prevent defects like pinholes or uneven coating.
-
Curing Parameters: The UV exposure time, intensity, and temperature during the curing process impact the final properties of the soldermask, such as its hardness, adhesion, and resistance to chemicals and abrasion.
Comparison of Silk Screen Printing with Other LPI Soldermask Application Methods
While silk screen printing is the most common method for applying LPI soldermask, other techniques are also used in the PCB industry:
Spray Coating
Spray coating involves atomizing the LPI soldermask and spraying it onto the PCB surface using a spray gun. This method is suitable for low-volume production or prototypes, as it offers flexibility in coating complex shapes and reduces material waste. However, spray coating may result in a less uniform soldermask layer compared to silk screen printing.
Curtain Coating
Curtain coating is a high-speed, continuous process in which the LPI soldermask is poured onto the PCB surface as a thin, uniform curtain. The PCB is passed through the curtain, and the excess soldermask is removed using air knives. This method is suitable for high-volume production and provides excellent uniformity and thickness control. However, it requires specialized equipment and may not be cost-effective for smaller production runs.
Comparison Table
Method | Silk Screen Printing | Spray Coating | Curtain Coating |
---|---|---|---|
Throughput | High | Low | Very High |
Cost-effectiveness | High for large runs | Low | High for very large runs |
Uniformity | Excellent | Good | Excellent |
Thickness Control | Good | Fair | Excellent |
Flexibility | Moderate | High | Low |
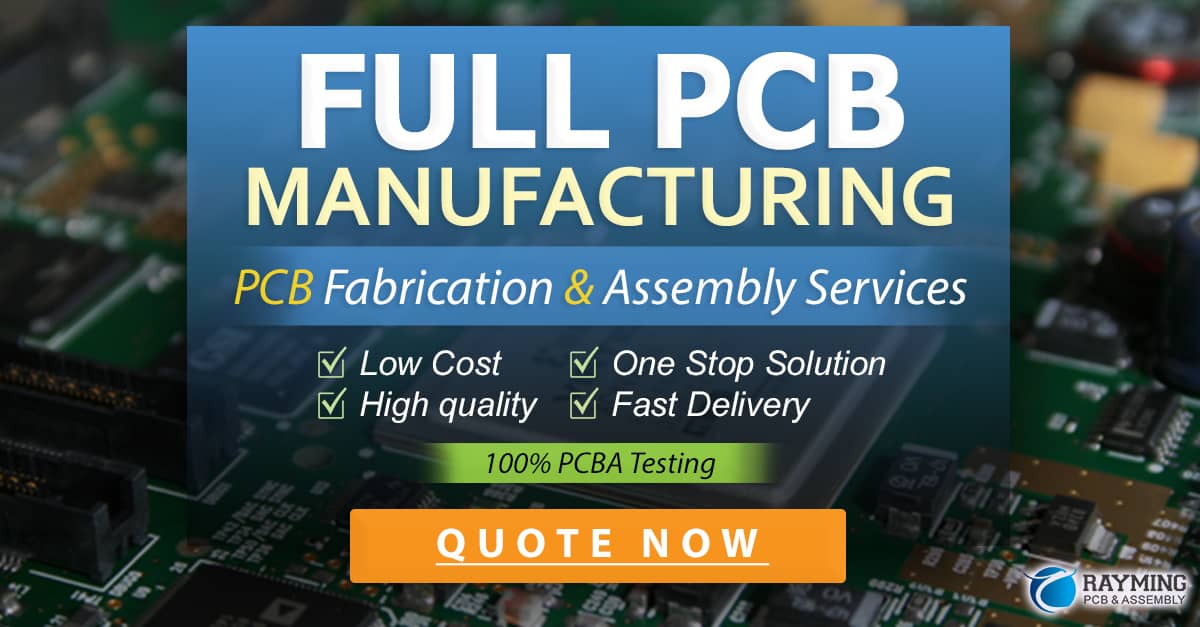
Best Practices for Silk Screen Printing LPI Soldermask
To ensure the best results when applying LPI soldermask using silk screen printing, follow these best practices:
- Use high-quality, compatible LPI soldermask materials from reputable suppliers
- Ensure proper screen tension and mesh count for the desired Soldermask Thickness and resolution
- Maintain consistent emulsion thickness and exposure times for repeatable results
- Control squeegee pressure, angle, and speed during printing to achieve uniform coverage
- Optimize curing parameters (UV exposure, temperature, and time) based on the soldermask manufacturer’s recommendations
- Implement strict quality control measures, including visual inspection and thickness measurements, to identify and correct defects promptly
Troubleshooting Common Issues in Silk Screen Printed LPI Soldermask
-
Pinholes or Voids: These defects can be caused by contamination, inadequate screen cleaning, or improper soldermask viscosity. Ensure thorough cleaning of screens and PCBs, and adjust the soldermask viscosity if needed.
-
Uneven Thickness: Uneven soldermask thickness can result from inconsistent squeegee pressure, worn squeegees, or improper screen tension. Replace worn squeegees, maintain proper screen tension, and ensure consistent squeegee pressure during printing.
-
Poor Adhesion: Poor adhesion of the soldermask to the PCB can be caused by surface contamination, incompatible soldermask materials, or inadequate curing. Clean the PCB surface thoroughly, use compatible soldermask materials, and ensure proper curing parameters are followed.
-
Misalignment: Misaligned soldermask patterns can occur due to incorrect screen registration or PCB movement during printing. Ensure accurate screen alignment using registration marks and secure the PCB during printing to prevent shifting.
-
Incomplete Curing: Incomplete curing of the soldermask can lead to poor performance and durability. Follow the soldermask manufacturer’s recommended curing parameters, and regularly maintain and calibrate the UV curing equipment.
Frequently Asked Questions (FAQ)
-
What is the typical thickness of LPI soldermask applied using silk screen printing?
The typical thickness of LPI soldermask applied using silk screen printing ranges from 0.5 to 2.0 mils (12.7 to 50.8 microns), depending on the screen mesh count and emulsion thickness used. -
Can silk screen printing be used to apply soldermask to both sides of a PCB simultaneously?
Yes, silk screen printing can be used to apply soldermask to both sides of a PCB simultaneously using a double-sided printing machine or by printing each side separately and carefully aligning the PCB during the second print. -
How does the color of the LPI soldermask affect its performance?
The color of the LPI soldermask does not directly affect its performance. However, different colors are used for easy identification of components, polarity, and other features on the PCB. Some colors, such as black or white, may offer better contrast for silk-screened text and symbols. -
What is the shelf life of LPI soldermask, and how should it be stored?
The shelf life of LPI soldermask varies depending on the manufacturer and formulation, but it typically ranges from 6 months to 1 year when stored properly. LPI soldermask should be stored in a cool, dry place away from direct sunlight and heat sources, as well as in tightly sealed containers to prevent contamination and evaporation of solvents. -
Can silk screen printed LPI soldermask be reworked or repaired if defects are found after curing?
Reworking or repairing silk screen printed LPI soldermask after curing is challenging and not always possible. Minor defects may be repaired using compatible soldermask materials and careful application techniques, followed by localized UV curing. However, extensive defects may require stripping the soldermask and reprinting, which can be time-consuming and costly. Prevention through proper process control and quality assurance is the best approach.
Conclusion
Silk screen printing is the most widely used method for applying LPI soldermask to PCBs, offering high throughput, cost-effectiveness, and consistent results. By understanding the silk screen printing process, factors affecting print quality, and best practices for implementation, PCB manufacturers can optimize their soldermask application process and ensure the production of high-quality, reliable circuit boards. Regular maintenance, quality control, and troubleshooting of common issues are essential for achieving the best results and maintaining the efficiency of the silk screen printing process.
0 Comments