What is ESD and Why is it Important to Consider in PCB Design?
Electrostatic discharge (ESD) is a sudden flow of electricity between two electrically charged objects caused by contact, an electrical short, or dielectric breakdown. In the context of electronic devices and printed circuit boards (PCBs), ESD can cause significant damage to sensitive components, leading to device failure or reduced performance.
ESD is a common occurrence in everyday life, often experienced as a small shock when touching a doorknob or other conductive surface. However, even though these discharges may seem harmless to humans, they can generate voltages of several thousand volts, which can be devastating to electronic components.
In the manufacturing and handling of PCBs, ESD is a critical concern due to the increasing miniaturization of electronic components and the use of materials that are more susceptible to ESD damage. As a result, it is essential for PCB designers and manufacturers to understand the effects of ESD and implement appropriate protection measures to ensure the reliability and longevity of their products.
How ESD Affects PCBs and Electronic Components
Types of ESD Events
There are three main types of ESD events that can affect PCBs and electronic components:
-
Human Body Model (HBM): This model represents the discharge that occurs when a person becomes charged and touches a grounded object, such as a PCB. The HBM is the most common type of ESD event and can generate voltages up to 15,000 volts.
-
Charged Device Model (CDM): This model represents the discharge that occurs when a charged device, such as a PCB, comes into contact with a conductive surface at a different potential. CDM events can generate voltages up to 2,000 volts and are more localized than HBM events.
-
Machine Model (MM): This model represents the discharge that occurs between two machines or objects, such as a charged PCB and a grounded machine part. MM events can generate voltages up to 400 volts and are less common than HBM and CDM events.
Effects of ESD on Electronic Components
ESD events can cause various types of damage to electronic components, depending on the severity of the discharge and the susceptibility of the component. Some common effects of ESD on electronic components include:
-
Thermal damage: High-voltage ESD events can cause localized heating in electronic components, leading to the melting of materials and permanent damage to the device.
-
Dielectric breakdown: ESD can cause the breakdown of insulating materials, such as the gate oxide in MOSFET transistors, leading to increased leakage current and reduced performance.
-
Junction damage: ESD events can cause damage to the p-n junctions in semiconductor devices, such as diodes and transistors, leading to increased reverse current and reduced forward voltage.
-
Latent defects: In some cases, ESD events may not cause immediate failure of the device but can create latent defects that may lead to premature failure during operation.
The table below summarizes the typical voltage ranges and potential effects of the three main types of ESD events:
ESD Model | Voltage Range | Potential Effects |
---|---|---|
HBM | Up to 15,000 V | Thermal damage, dielectric breakdown, junction damage |
CDM | Up to 2,000 V | Localized thermal damage, dielectric breakdown |
MM | Up to 400 V | Thermal damage, dielectric breakdown |
ESD Susceptibility of Common Electronic Components
The susceptibility of electronic components to ESD damage varies depending on their design, materials, and manufacturing process. Some common electronic components and their relative ESD susceptibility are listed below:
Component Type | ESD Susceptibility |
---|---|
MOSFET transistors | High |
Bipolar transistors | Moderate |
Diodes | Moderate |
Resistors | Low |
Capacitors | Low |
Inductors | Low |
MOSFET transistors are particularly susceptible to ESD damage due to their thin gate oxide layer, which can easily break down under high-voltage stress. Bipolar transistors and diodes are moderately susceptible, while passive components like resistors, capacitors, and inductors are generally less susceptible to ESD damage.
ESD Protection Measures for PCBs
ESD-Safe Handling Procedures
To minimize the risk of ESD damage during PCB manufacturing and handling, it is essential to implement ESD-safe handling procedures. Some key practices include:
-
Grounding: All personnel, workstations, and tools should be properly grounded to prevent the buildup of static charges. This can be achieved using grounded wrist straps, conductive flooring, and grounded workbenches.
-
Ionization: Air ionizers can be used to neutralize static charges in the work environment, reducing the risk of ESD events.
-
Shielding: ESD-sensitive components and PCBs should be stored and transported in ESD-safe packaging, such as conductive bags or boxes, to shield them from external static fields.
-
Training: All personnel involved in handling ESD-sensitive components and PCBs should receive proper training on ESD-safe practices and be aware of the potential risks associated with ESD events.
On-Board ESD Protection Techniques
In addition to ESD-safe handling procedures, PCB designers can implement various on-board protection techniques to further reduce the risk of ESD damage. Some common on-board ESD protection techniques include:
-
Transient voltage suppression (TVS) diodes: TVS diodes are designed to clamp high-voltage transients to a safe level, protecting sensitive components from ESD damage. They are typically placed near the PCB’s input/output (I/O) connectors and power supply lines.
-
Grounding and shielding: Proper grounding and shielding techniques can help to divert ESD currents away from sensitive components and reduce the risk of damage. This can be achieved through the use of ground planes, guard rings, and shielded connectors.
-
ESD-resistant components: Selecting components with built-in ESD protection, such as ESD-resistant transistors or diodes, can help to reduce the overall susceptibility of the PCB to ESD damage.
-
Layout techniques: Proper PCB layout techniques, such as avoiding long, floating traces and minimizing the loop area of critical signal paths, can help to reduce the coupling of ESD energy into sensitive components.
The table below summarizes some common on-board ESD protection techniques and their benefits:
Protection Technique | Benefits |
---|---|
TVS diodes | Clamps high-voltage transients to a safe level |
Grounding and shielding | Diverts ESD currents away from sensitive components |
ESD-resistant components | Reduces overall susceptibility to ESD damage |
Layout techniques | Minimizes coupling of ESD energy into sensitive components |
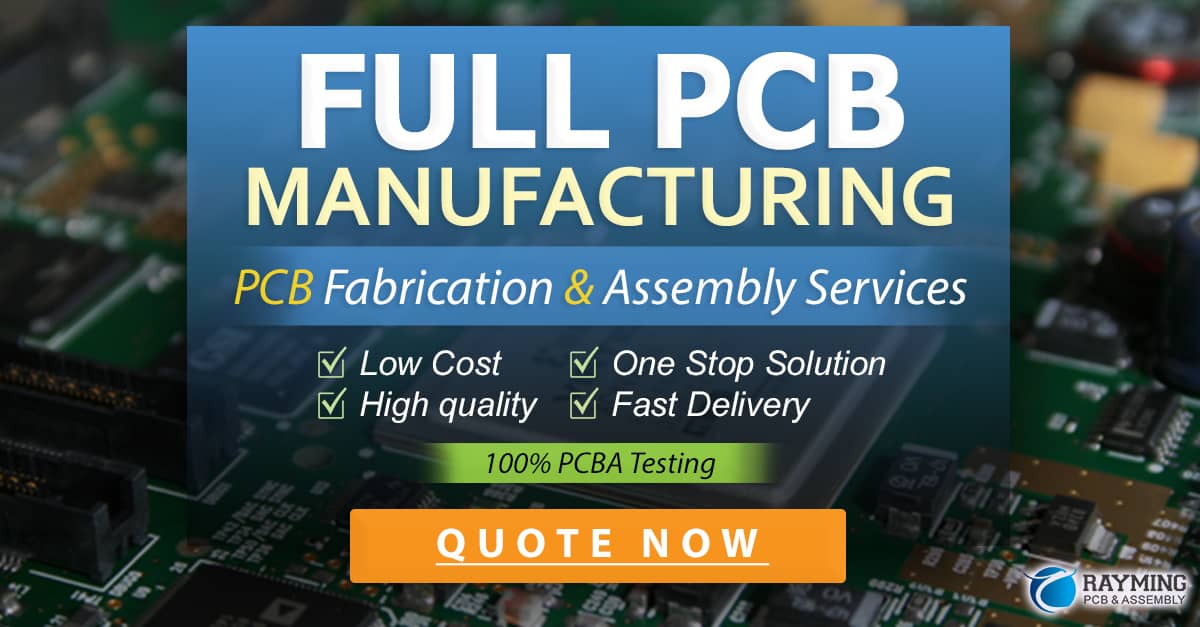
Testing and Verification of ESD Protection Measures
To ensure the effectiveness of ESD protection measures, it is essential to perform regular testing and verification of PCBs and electronic devices. Some common ESD testing methods include:
-
HBM testing: This method involves applying high-voltage pulses to the device under test (DUT) to simulate human body model ESD events. The DUT is then checked for any signs of damage or degraded performance.
-
CDM testing: This method involves charging the DUT to a high voltage and then discharging it through a grounded conductor to simulate charged device model ESD events. The DUT is then checked for any signs of damage or degraded performance.
-
System-level ESD testing: This method involves testing the entire electronic system, including the PCB and any connected peripherals, to ensure that it can withstand real-world ESD events without damage or malfunction.
Regular testing and verification of ESD protection measures can help to identify potential weaknesses in the design and ensure that the PCB and electronic device can withstand the expected level of ESD stress in their intended operating environment.
Frequently Asked Questions (FAQ)
- What is the difference between ESD and EMI?
-
ESD (Electrostatic Discharge) refers to the sudden flow of electricity between two objects at different electrical potentials, often resulting in high-voltage, short-duration pulses. EMI (Electromagnetic Interference) refers to the disruption of the normal operation of an electronic device due to electromagnetic fields generated by other devices or sources. While ESD is primarily a concern for the physical damage it can cause to electronic components, EMI is more concerned with the interference it can cause to the normal functioning of the device.
-
Can ESD damage occur even if I don’t feel a shock?
-
Yes, ESD damage can occur without any perceptible shock to humans. In many cases, ESD events that are below the human perception threshold can still cause damage to sensitive electronic components. This is why it is essential to implement ESD-safe handling procedures and use proper ESD protection equipment, even if you don’t feel any shocks during handling.
-
How can I tell if a component has been damaged by ESD?
-
ESD damage can manifest in various ways, depending on the type of component and the severity of the discharge. Some common signs of ESD damage include increased leakage current, reduced performance, or complete failure of the device. In some cases, latent defects caused by ESD may not be immediately apparent and may only manifest later during operation. To determine if a component has been damaged by ESD, it may be necessary to perform functional testing or use specialized ESD testing equipment.
-
Are all electronic components equally susceptible to ESD damage?
-
No, the susceptibility of electronic components to ESD damage varies depending on their design, materials, and manufacturing process. Components like MOSFET transistors, which have thin gate oxide layers, are particularly susceptible to ESD damage, while passive components like resistors and capacitors are generally less susceptible. It is essential to consider the ESD susceptibility of each component when designing ESD protection measures for a PCB.
-
Can ESD protection measures completely eliminate the risk of ESD damage?
- While ESD protection measures can significantly reduce the risk of ESD damage, it is not possible to completely eliminate the risk. There is always a chance that an extremely high-voltage ESD event or an unforeseen circumstance could cause damage, despite the presence of protection measures. However, by implementing a combination of ESD-safe handling procedures, on-board protection techniques, and regular testing and verification, the risk of ESD damage can be minimized to an acceptable level for most applications.
Conclusion
Electrostatic discharge (ESD) is a significant concern in the design, manufacturing, and handling of PCBs and electronic devices. With the increasing miniaturization of electronic components and the use of materials that are more susceptible to ESD damage, it is essential for PCB designers and manufacturers to understand the effects of ESD and implement appropriate protection measures.
By implementing ESD-safe handling procedures, on-board protection techniques, and regular testing and verification, the risk of ESD damage can be significantly reduced, ensuring the reliability and longevity of electronic devices. As technology continues to advance, it is crucial for the electronics industry to stay informed about the latest developments in ESD protection and to continuously improve their practices to meet the evolving challenges posed by ESD.
0 Comments