Introduction to Glass-Laminate PCBs
Printed circuit boards (PCBs) are the backbone of modern electronics. They provide the interconnections and mounting points for components in devices ranging from smartphones to industrial equipment. The performance and reliability of a PCB depends heavily on the materials used in its construction.
One of the most critical materials in a PCB is the laminate – the insulating layer that provides mechanical support and electrical isolation between conductive layers. The most common type of laminate used in PCBs is made from woven glass fabric impregnated with an epoxy resin. These glass-laminate PCBs offer several advantages over other laminate materials.
Benefits of Woven Glass Laminates
Woven glass laminates provide a number of benefits for PCB performance and manufacturability:
- High mechanical strength and stiffness
- Good electrical insulation properties
- Low dielectric constant and dissipation factor
- Excellent dimensional stability
- Compatible with standard PCB fabrication processes
- Relatively low cost compared to other high-performance laminates
The combination of strong mechanical and electrical properties makes woven glass laminates an ideal choice for a wide range of PCB applications. The woven glass fabric provides reinforcement to resist bending and improve handleability, while the epoxy resin offers good insulation and chemical resistance.
Impact on PCB Electrical Performance
The electrical performance of a PCB is critical in most applications. Woven glass laminates play an important role in determining key electrical parameters of the finished board.
Dielectric Constant and Loss
The dielectric constant (Dk) of a laminate is a measure of how much the material concentrates electric fields. A lower Dk allows electromagnetic waves to propagate faster through the material. The dissipation factor or loss tangent (Df) quantifies how much energy is lost as signals travel through the laminate. Lower losses enable higher frequency operation.
Typical woven glass laminates have dielectric constants in the range of 4.2 to 4.8 and dissipation factors of 0.015 to 0.025 at 1 MHz. This is lower than most other PCB laminate materials like paper-phenolic (Dk 4.5-5.5, Df 0.03-0.05) and similar to high-performance laminates like PTFE composites (Dk 2.1-2.8, Df 0.001-0.002).
The relatively low Dk and Df of glass laminates make them suitable for many RF and high-speed digital applications up to several gigahertz. However, very high frequency and low-loss applications may require more specialized laminates.
Impedance Control
Controlling the impedance of PCB traces is important for maintaining signal integrity, especially at high frequencies. The characteristic impedance of a trace depends on its geometry as well as the Dk of the surrounding laminate.
Woven glass laminates are commonly used to fabricate controlled impedance PCBs. The consistent Dk of glass allows trace widths and spacings to be designed to achieve a target impedance, typically 50-100 ohms. Specialized impedance test coupons and time-domain reflectometry (TDR) measurements are used to validate impedance on prototype and production boards.
Glass laminate PCBs can typically maintain impedance within +/-10% of the target value. Tighter tolerances down to +/-5% or lower are possible with good design and process control. Impedance variations across a panel are typically limited to +/-2% due to the uniformity of the glass fabric.
Signal Integrity and EMI
In addition to impedance control, woven glass laminates also influence other aspects of signal integrity and electromagnetic interference (EMI) in PCBs. The transition between the glass fabric and the epoxy resin can cause discontinuities that affect signal propagation at very high frequencies. The fiber weave pattern can also induce anisotropy in the dielectric constant, leading to polarization effects.
Despite these challenges, glass laminates perform well enough for most applications below 10 GHz. Specialized weaves and resins can help extend glass into higher frequency ranges. Using spread-glass styles and thin laminates helps mitigate the impact of the glass fabric on signal integrity.
From an EMI perspective, woven glass laminates provide reasonably good shielding effectiveness. The glass fabric attenuates radiated emissions and provides a barrier to external electromagnetic fields. Coupling between PCB layers is also reduced compared to laminates without shielding. For applications with stringent EMI requirements, additional shielding measures like metal enclosures may still be necessary.
Mechanical Properties and Reliability
In addition to enabling good electrical performance, woven glass laminates also play a critical role in the mechanical reliability of PCBs. The laminate material must withstand manufacturing processes and provide long-term stability in the end-use environment.
Strength and Stiffness
The woven glass fabric in the laminate is the primary source of mechanical reinforcement. The interlocking fibers provide high tensile and flexural strength to resist deformation under stress. Typical glass laminates have flexural strength of 400-600 MPa, significantly higher than unreinforced epoxy (~100 MPa).
The mechanical stiffness or rigidity of the laminate is quantified by its elastic modulus. A higher modulus indicates greater resistance to bending and deflection. Woven glass laminates have elastic moduli in the range of 15-25 GPa, compared to only 3-5 GPa for neat epoxy. This allows glass PCBs to maintain their shape and prevent damage to mounted components.
The high strength and stiffness of glass laminates enables the fabrication of thin PCBs down to 0.2-0.5 mm in thickness. This is important for space-constrained designs like smartphones and wearables. However, very thin laminates can be more susceptible to warpage, so careful design and material selection is necessary.
Thermal Stability
PCBs are subjected to thermal stresses during assembly processes like soldering as well as in the end-use environment. The laminate must maintain its dimensions and properties over the expected temperature range.
The glass transition temperature (Tg) is a key metric for the thermal stability of a laminate. Above Tg, the polymer matrix softens and its mechanical properties degrade rapidly. Standard FR-4 glass epoxy laminates have Tg values of 130-140°C, suitable for lead-free solder assembly and most consumer electronics applications.
For more demanding automotive, aerospace, and industrial applications, high-Tg laminates with Tg up to 180-200°C are available. These laminates use specialized epoxy blends and curing agents to achieve better thermal resistance. The woven glass fabric also constrains the expansion and softening of the resin to further improve high-temperature performance.
The coefficient of thermal expansion (CTE) quantifies how much a material expands with increasing temperature. Mismatches in CTE between the PCB and its components can cause thermal stresses that lead to solder joint failures and delamination. Woven glass laminates have CTEs in the range of 12-16 ppm/°C, relatively close to that of copper (17 ppm/°C) and most electronic components. This helps minimize CTE mismatch and improves reliability.
Dimensional Stability
Dimensional stability refers to a laminate’s ability to maintain its size and shape over time and under environmental stresses. Changes in dimensions can cause misalignment of features like drilled holes and placed components, leading to assembly issues and field failures.
Woven glass laminates have excellent dimensional stability due to the restraining effect of the glass fabric. The rigid fibers limit resin movement and prevent creep or stress relaxation over time. Typical glass laminates exhibit linear dimensional change of less than 0.1% after thermal stress exposures.
In addition to thermal stability, glass laminates also resist moisture absorption and swelling. The epoxy matrix is inherently hydrophobic, and the glass fibers do not absorb significant water. Typical moisture absorption rates are 0.1-0.3% by weight, much lower than other laminates like polyimide (~2%). This helps maintain flatness and prevents issues like measling or delamination in humid environments.
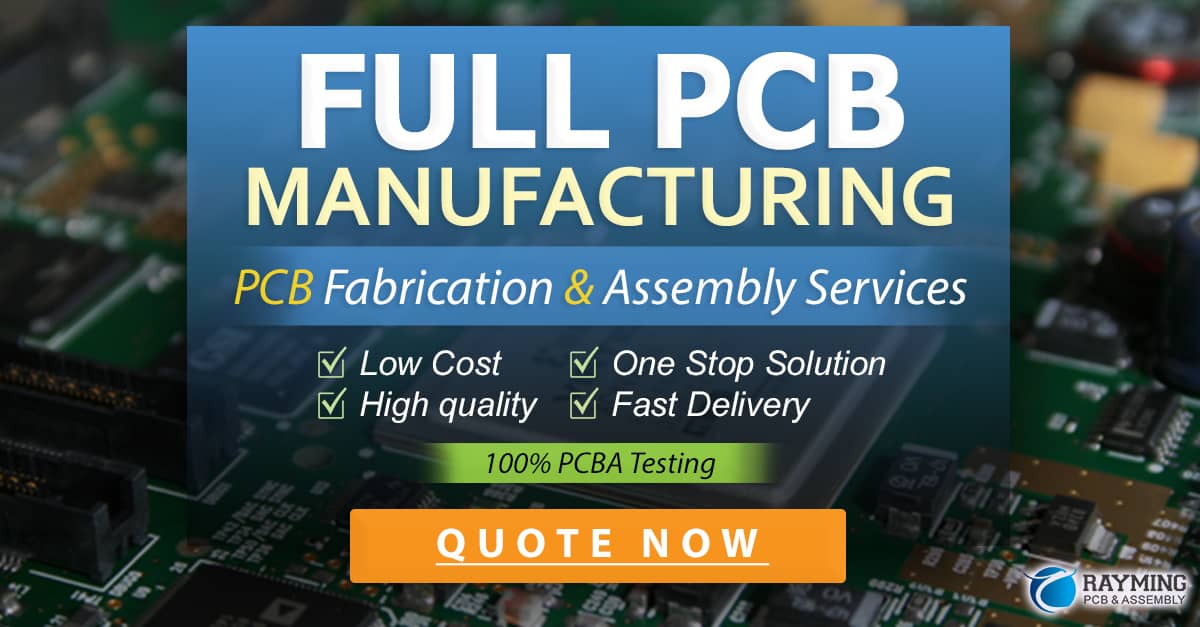
Manufacturing Considerations
The choice of laminate material also impacts PCB manufacturing processes and yields. Woven glass laminates are compatible with standard PCB fabrication methods and offer good processability.
Drilling and Routing
Mechanical drilling is used to create holes for through-hole components, vias, and tooling pins in PCBs. The woven glass fabric in the laminate is abrasive and can cause rapid wear of drill bits. Carbide-tipped drills and high-speed steel (HSS) drills with diamond coatings are commonly used to improve tool life.
Routing or milling is used to create slots, pockets, and cutouts in the PCB. The glass fabric can cause splintering and burring at the edges of routed features. Using downcut spiral router bits and optimizing speeds and feeds helps minimize damage. Laser cutting is an alternative method that can produce cleaner edges in glass laminates.
Copper Plating and Etching
The copper conductive layers in a PCB are typically formed by electroplating or foil lamination followed by subtractive etching. The glass laminate acts as a barrier to prevent copper migration and provide adhesion to the copper surfaces.
The surface roughness and porosity of the laminate affects the adhesion and coverage of the copper. Excessively smooth surfaces can cause delamination, while overly rough surfaces can lead to overetching and trace width variation. Woven glass laminates have a natural surface texture that provides good mechanical interlocking with the copper.
The dielectric properties of the laminate also influence the impedance and current-carrying capacity of the copper traces. Higher Dk laminates require wider traces to achieve the same impedance, which can limit routing density. The thermal conductivity of the laminate affects how efficiently heat is dissipated from the traces, impacting current limits.
Solder Mask and Silkscreen
Solder mask is a polymer coating applied over the copper traces to protect against oxidation and prevent solder bridging. The mask material must adhere well to the laminate surface and maintain its integrity during soldering.
Woven glass laminates are compatible with both liquid photoimageable (LPI) and dry film solder masks. The surface texture of the laminate provides good adhesion for the mask. However, the glass fibers can cause scattering and resolution limits for fine-pitch designs. Using filled or planarized laminates can improve solder mask performance.
Silkscreen is used to print component designators, test points, and other markings on the PCB surface. The ink must adhere to the laminate and resist abrasion and solvents. Epoxy or acrylic inks are commonly used for silkscreen on glass laminates. The surface energy and texture of the laminate can affect ink wetting and resolution, so proper cleaning and treatment is important.
Frequently Asked Questions
Q: What is the difference between FR-4 and G-10 glass epoxy laminates?
A: FR-4 (Flame Retardant 4) is the most common grade of glass epoxy laminate used for PCBs. It is made with a brominated epoxy resin that provides flame retardancy. G-10 is a similar grade that uses a non-brominated epoxy resin. Both use woven glass fabric reinforcement and have similar mechanical and electrical properties. The main difference is that FR-4 is self-extinguishing while G-10 is not rated for flammability.
Q: Can glass laminates be used for flexible or rigid-flex PCBs?
A: Standard woven glass laminates are not suitable for flexible circuits due to the rigidity of the glass fabric. However, there are specialized glass laminates available for rigid-flex constructions. These use very thin glass fabrics or non-woven glass mats that provide some flexibility. The epoxy resin is also formulated for improved ductility. These laminates are commonly used for the rigid sections of rigid-flex boards, while polyimide or other flexible materials are used for the flex portions.
Q: How does the glass weave style affect PCB performance?
A: The weave style refers to the pattern in which the glass fibers are interlaced. Common styles are plain, twill, and satin. The weave style affects the surface texture, resin content, and dimensional stability of the laminate. In general, tighter weaves like plain provide better stability and smoother surfaces, while looser weaves like satin have higher resin content and better drapeability. The choice of weave style depends on the specific electrical, mechanical, and manufacturability requirements of the PCB design.
Q: What are the limitations of glass laminates for high-frequency PCBs?
A: While glass laminates are suitable for many RF and high-speed digital applications, they do have some limitations at very high frequencies (>10 GHz). The glass fabric can cause non-uniformities in the dielectric constant and lead to signal integrity issues like skew and dispersion. The roughness of the copper-laminate interface can also increase conductor losses. For these applications, specialized laminates like PTFE or low-Dk ceramics may be necessary to maintain performance.
Q: How do glass laminates compare to other PCB materials in terms of cost?
A: Woven glass epoxy laminates are one of the most cost-effective options for PCBs. The raw materials (glass fabric and epoxy resin) are relatively inexpensive and widely available. The manufacturing processes for glass PCBs are also well-established and efficient. In comparison, high-performance laminates like PTFE or polyimide can cost several times more than glass due to the specialized materials and processing required. However, for very high-volume applications, the cost difference may be less significant.
Conclusion
Woven glass laminates are a critical component of modern PCBs. They provide the necessary mechanical support, electrical insulation, and dimensional stability for a wide range of electronic applications. The unique properties of glass-reinforced epoxy enable PCBs that are strong, reliable, and cost-effective.
While glass laminates have some limitations for very high-frequency or high-temperature applications, they remain the material of choice for the vast majority of PCB designs. Advances in materials and processing continue to push the boundaries of what is possible with glass laminates.
As electronic devices become ever more complex and interconnected, the demand for high-quality PCBs will only continue to grow. Woven glass laminates will undoubtedly play a critical role in meeting this demand and enabling the next generation of electronic innovations.
0 Comments