Introduction to ENIG and ENEPIG Surface Finishes
In the world of printed circuit board (PCB) manufacturing, the choice of surface finish plays a crucial role in ensuring the reliability, solderability, and longevity of the final product. Two popular surface finishes that have gained significant attention in recent years are Electroless Nickel Immersion Gold (ENIG) and Electroless Nickel Electroless Palladium Immersion Gold (ENEPIG). While both finishes involve the deposition of nickel and gold layers, they differ in their manufacturing processes and the presence of an additional palladium layer in ENEPIG.
In this article, we will delve into the differences between ENIG and ENEPIG, exploring their characteristics, advantages, disadvantages, and applications. By the end of this comprehensive guide, you will have a clear understanding of these two surface finishes and be able to make an informed decision when selecting the most suitable option for your PCB projects.
What is ENIG?
ENIG, short for Electroless Nickel Immersion Gold, is a widely used surface finish in the PCB industry. It involves the deposition of a thin layer of gold over a nickel layer on the exposed copper pads of a PCB. The process begins with the electroless deposition of a nickel layer, typically ranging from 3 to 6 microns in thickness. This nickel layer acts as a barrier, preventing the diffusion of copper into the subsequent gold layer.
Once the nickel layer is in place, the PCB undergoes an immersion gold process, where a thin layer of gold, usually 0.05 to 0.2 microns thick, is deposited onto the nickel surface. The gold layer provides excellent oxidation resistance, solderability, and electrical conductivity.
What is ENEPIG?
ENEPIG, which stands for Electroless Nickel Electroless Palladium Immersion Gold, is a more advanced surface finish compared to ENIG. It incorporates an additional layer of palladium between the nickel and gold layers, enhancing the overall performance and reliability of the PCB.
The ENEPIG process begins similarly to ENIG, with the electroless deposition of a nickel layer. However, instead of directly applying the gold layer, an electroless palladium layer, typically 0.05 to 0.2 microns thick, is deposited onto the nickel surface. This palladium layer serves as a barrier between the nickel and gold layers, preventing the formation of nickel oxidation and providing better adhesion for the subsequent gold layer.
Finally, an immersion gold layer, usually 0.05 to 0.1 microns thick, is deposited onto the palladium surface. The gold layer offers excellent solderability, corrosion resistance, and electrical conductivity.
Differences between ENIG and ENEPIG
Manufacturing Process
One of the primary differences between ENIG and ENEPIG lies in their manufacturing processes. While both finishes involve the deposition of nickel and gold layers, ENEPIG includes an additional step of depositing a palladium layer between the nickel and gold layers.
The manufacturing process for ENIG consists of the following steps:
1. Cleaning and preparation of the PCB surface
2. Electroless deposition of the nickel layer
3. Immersion gold deposition
On the other hand, the ENEPIG process involves these steps:
1. Cleaning and preparation of the PCB surface
2. Electroless deposition of the nickel layer
3. Electroless deposition of the palladium layer
4. Immersion gold deposition
The additional palladium layer in ENEPIG contributes to its enhanced performance and reliability compared to ENIG.
Solderability
Both ENIG and ENEPIG offer excellent solderability, ensuring strong and reliable solder joints. However, ENEPIG has a slight advantage over ENIG in terms of solderability.
The presence of the palladium layer in ENEPIG provides better wettability and solder joint strength compared to ENIG. The palladium layer acts as a barrier, preventing the formation of nickel oxide, which can adversely affect solderability. Additionally, the palladium layer promotes better adhesion between the solder and the surface finish, resulting in stronger and more reliable solder joints.
ENIG, while still offering good solderability, may be more susceptible to the formation of nickel oxide, especially if the gold layer is too thin or if the PCB is exposed to elevated temperatures for extended periods.
Shelf Life
The shelf life of a PCB refers to the duration for which it can be stored before its solderability and performance start to degrade. ENEPIG has a longer shelf life compared to ENIG, making it a preferred choice for PCBs that require extended storage periods.
The palladium layer in ENEPIG acts as a barrier, preventing the diffusion of nickel into the gold layer and the formation of nickel oxide. This barrier effect helps maintain the solderability and performance of the PCB over a longer period.
In contrast, ENIG may be more prone to degradation over time, especially if the gold layer is thin or if the PCB is exposed to harsh environmental conditions. The formation of nickel oxide can lead to reduced solderability and weaker solder joints.
Cost
When it comes to cost, ENIG is generally more affordable than ENEPIG. The additional palladium layer in ENEPIG contributes to its higher cost compared to ENIG.
The cost difference between ENIG and ENEPIG can vary depending on factors such as the PCB manufacturer, the volume of production, and the specific requirements of the project. However, on average, ENEPIG can be 10% to 20% more expensive than ENIG.
It is essential to consider the cost-benefit analysis when choosing between ENIG and ENEPIG. While ENEPIG may have a higher upfront cost, its enhanced performance, reliability, and longer shelf life may justify the investment in the long run, particularly for high-reliability applications.
Compatibility with Different PCB Materials
Both ENIG and ENEPIG are compatible with a wide range of PCB materials, including FR-4, high-frequency laminates, and flexible substrates. However, there are some considerations to keep in mind when selecting the surface finish based on the PCB material.
ENIG is generally suitable for most PCB materials and is widely used in various applications. It offers good adhesion to different substrates and provides a reliable surface finish for soldering components.
ENEPIG, with its additional palladium layer, offers enhanced compatibility with high-frequency and high-speed PCB materials. The palladium layer helps maintain signal integrity and reduces signal loss, making ENEPIG a preferred choice for high-performance applications.
When working with flexible PCBs, both ENIG and ENEPIG can be used, but ENEPIG may have an advantage due to its better adhesion and flexibility. The palladium layer in ENEPIG helps prevent cracking and delamination of the surface finish during flexing and bending.
Applications of ENIG and ENEPIG
ENIG Applications
ENIG is widely used in various PCB applications, including:
-
Consumer electronics: ENIG is commonly used in consumer electronic devices such as smartphones, tablets, and laptops due to its good solderability and affordability.
-
Automotive electronics: ENIG is suitable for automotive applications that require reliable solder joints and good corrosion resistance.
-
Industrial electronics: ENIG is used in industrial control systems, sensors, and automation equipment, where reliable soldering and good shelf life are essential.
-
Medical devices: ENIG is employed in medical devices that require good solderability and biocompatibility.
ENEPIG Applications
ENEPIG, with its enhanced performance and reliability, is preferred in high-end and demanding applications, such as:
-
High-frequency and high-speed applications: ENEPIG is an excellent choice for PCBs used in high-frequency and high-speed applications, such as 5G communication devices, radar systems, and high-speed data transmission equipment.
-
Aerospace and defense: ENEPIG is widely used in aerospace and defense applications that require high reliability, long shelf life, and resistance to harsh environmental conditions.
-
Automotive safety systems: ENEPIG is employed in critical automotive safety systems, such as airbag control modules and anti-lock braking systems, where reliable solder joints and long-term performance are crucial.
-
Medical implantable devices: ENEPIG is suitable for medical implantable devices that require biocompatibility, high reliability, and long-term stability.
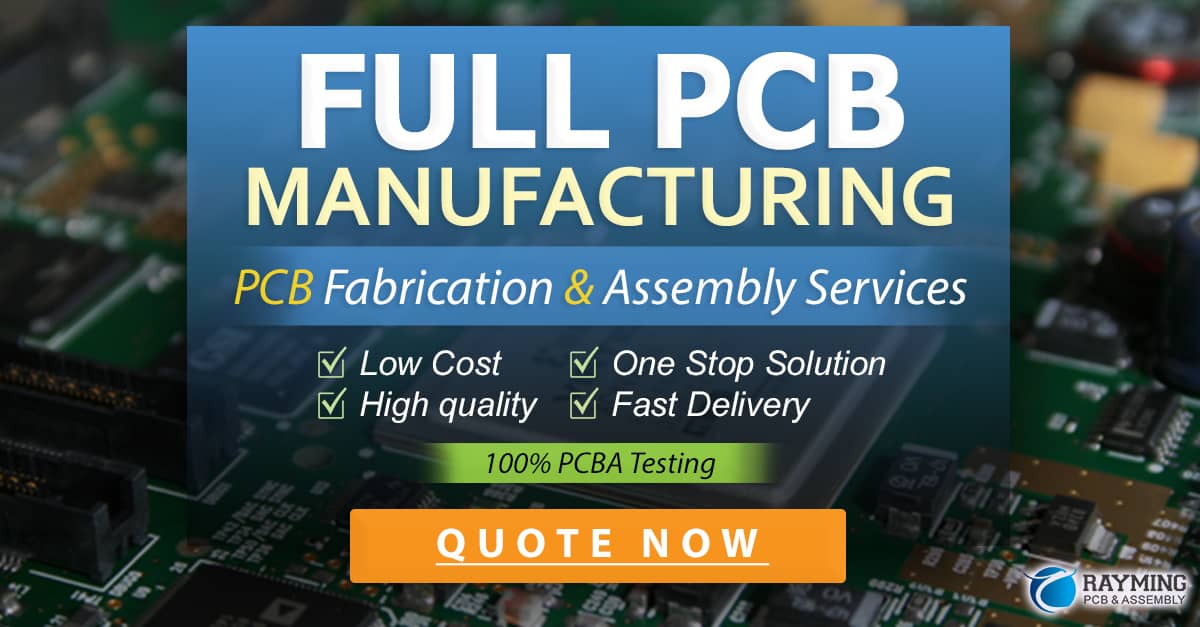
Advantages and Disadvantages of ENIG and ENEPIG
Advantages of ENIG
-
Cost-effective: ENIG is generally more affordable than ENEPIG, making it a popular choice for cost-sensitive applications.
-
Good solderability: ENIG offers good solderability, ensuring reliable solder joints and easy assembly of components.
-
Wide compatibility: ENIG is compatible with a wide range of PCB materials and is suitable for various applications.
-
Flat surface: ENIG provides a flat and uniform surface finish, which is beneficial for fine-pitch components and high-density PCB designs.
Disadvantages of ENIG
-
Limited shelf life: ENIG may have a shorter shelf life compared to ENEPIG, especially if the gold layer is thin or if the PCB is exposed to harsh environmental conditions.
-
Potential for nickel oxide formation: ENIG is more susceptible to the formation of nickel oxide, which can adversely affect solderability and solder joint strength.
-
Black pad syndrome: ENIG is more prone to black pad syndrome, a defect characterized by the formation of a brittle intermetallic compound between the nickel and gold layers, leading to weak solder joints.
Advantages of ENEPIG
-
Enhanced solderability: ENEPIG offers excellent solderability due to the presence of the palladium layer, which promotes better wettability and stronger solder joints.
-
Longer shelf life: ENEPIG has a longer shelf life compared to ENIG, as the palladium layer prevents the formation of nickel oxide and maintains solderability over extended storage periods.
-
Improved reliability: ENEPIG provides better reliability and performance, particularly in high-frequency and high-speed applications, due to the palladium layer’s ability to maintain signal integrity and reduce signal loss.
-
Compatibility with high-performance materials: ENEPIG is highly compatible with high-frequency and high-speed PCB materials, making it a preferred choice for demanding applications.
Disadvantages of ENEPIG
-
Higher cost: ENEPIG is generally more expensive than ENIG due to the additional palladium layer and the more complex manufacturing process.
-
Longer processing time: The ENEPIG process involves an additional step of palladium deposition, which can increase the overall processing time compared to ENIG.
-
Potential for palladium corrosion: In some cases, the palladium layer in ENEPIG may be susceptible to corrosion, particularly in harsh environmental conditions or when exposed to certain chemicals.
Comparison Table: ENIG vs. ENEPIG
Characteristic | ENIG | ENEPIG |
---|---|---|
Layers | Nickel, Gold | Nickel, Palladium, Gold |
Solderability | Good | Excellent |
Shelf Life | Limited | Longer |
Cost | Lower | Higher |
Compatibility | Wide range of PCB materials | Highly compatible with high-frequency and high-speed materials |
Applications | Consumer electronics, automotive, industrial, medical devices | High-frequency and high-speed applications, aerospace, defense, automotive safety systems, medical implantable devices |
Advantages | Cost-effective, good solderability, wide compatibility, flat surface | Enhanced solderability, longer shelf life, improved reliability, compatibility with high-performance materials |
Disadvantages | Limited shelf life, potential for nickel oxide formation, black pad syndrome | Higher cost, longer processing time, potential for palladium corrosion |
Frequently Asked Questions (FAQ)
-
Q: Can ENIG and ENEPIG be used for both leaded and lead-free soldering?
A: Yes, both ENIG and ENEPIG are suitable for leaded and lead-free soldering processes. They offer good solderability and compatibility with different solder alloys. -
Q: Is ENEPIG always the better choice compared to ENIG?
A: Not necessarily. The choice between ENIG and ENEPIG depends on the specific requirements of the application, such as performance, reliability, cost, and shelf life. ENIG may be sufficient for many applications, while ENEPIG is preferred for high-end and demanding applications. -
Q: Can ENIG and ENEPIG be used for wire bonding?
A: Yes, both ENIG and ENEPIG are suitable for wire bonding applications. The gold layer in both finishes provides a compatible surface for wire bonding processes, ensuring reliable electrical connections. -
Q: How does the thickness of the gold layer affect the performance of ENIG and ENEPIG?
A: The thickness of the gold layer plays a crucial role in the performance of both ENIG and ENEPIG. A thicker gold layer provides better oxidation resistance and longer shelf life, but it can also increase the cost. A thinner gold layer may be more cost-effective but may have a shorter shelf life and be more susceptible to oxidation. -
Q: Are there any environmental concerns associated with ENIG and ENEPIG processes?
A: Both ENIG and ENEPIG processes involve the use of chemicals and materials that may have environmental implications. PCB manufacturers must follow proper handling, disposal, and recycling practices to minimize the environmental impact. Compliance with local and international environmental regulations is essential when implementing these surface finishes.
Conclusion
In conclusion, ENIG and ENEPIG are two popular surface finishes used in the PCB industry, each with its own unique characteristics, advantages, and disadvantages. ENIG, with its cost-effectiveness and wide compatibility, is suitable for a broad range of applications, while ENEPIG, with its enhanced performance, reliability, and longer shelf life, is preferred for high-end and demanding applications.
When selecting between ENIG and ENEPIG, it is essential to consider factors such as the specific requirements of the application, performance expectations, cost constraints, and shelf life needs. By understanding the differences between these two surface finishes and their suitability for various applications, PCB designers and manufacturers can make informed decisions and choose the most appropriate option for their projects.
As technology continues to advance and the demand for high-performance PCBs grows, the use of ENIG and ENEPIG will likely remain prevalent in the industry. Continuous research and development efforts may lead to further improvements in these surface finishes, addressing their limitations and enhancing their performance in future applications.
0 Comments