Introduction to PCB Milling
PCB milling is a process used in the fabrication of printed circuit boards (PCBs) where a specialized machine, called a PCB milling machine or a PCB Prototyping machine, is used to remove unwanted copper from a copper-clad board. This process is an alternative to traditional PCB Etching and is particularly useful for creating prototype PCBs or small-batch productions.
What is PCB Milling?
PCB milling is a subtractive process that involves the removal of copper from a copper-clad board using a rotating cutting tool, called an endmill or a router bit. The milling machine is controlled by a computer numerical control (CNC) system, which reads the design files (usually in Gerber or DXF format) and directs the movement of the cutting tool.
The milling process can be divided into two main categories:
-
Isolation milling: This process is used to create the electrical isolation between the copper traces on the PCB. The milling machine removes the unwanted copper, leaving only the desired traces.
-
Drilling: This process is used to create the holes required for through-hole components or vias. The milling machine uses a drill bit to create the holes at the specified locations.
Advantages of PCB Milling
PCB milling offers several advantages over traditional PCB etching:
-
Rapid prototyping: PCB milling allows for quick turnaround times, making it ideal for prototyping and testing new designs.
-
Cost-effective for small batches: For small-batch productions, PCB milling can be more cost-effective than traditional etching, as it eliminates the need for creating masks and using chemicals.
-
Environmentally friendly: PCB milling does not require the use of hazardous chemicals, making it a more environmentally friendly option compared to etching.
-
Versatility: PCB milling machines can work with a variety of materials, including FR4, aluminum, and even non-conductive materials like wood or plastic.
PCB Milling Equipment
To get started with PCB milling, you will need the following equipment:
PCB Milling Machine
A PCB milling machine is a CNC machine specifically designed for milling PCBs. These machines come in various sizes and configurations, ranging from desktop models for hobbyists and small businesses to large-scale industrial machines.
Some popular PCB milling machines include:
- Bantam Tools Desktop PCB Milling Machine
- Othermill Pro
- LPKF ProtoMat S Series
- BungardCCD/MTC
Software
To control the PCB milling machine and create the necessary design files, you will need specialized software. Some common software options include:
- Autodesk Eagle
- KiCad
- Altium Designer
- FlatCAM
Endmills and Drill Bits
Endmills and drill bits are the cutting tools used in PCB milling. Endmills are used for isolation milling, while drill bits are used for creating holes. These tools come in various sizes and materials, such as carbide and high-speed steel (HSS).
Copper-Clad Boards
Copper-clad boards are the base material for PCB milling. These boards consist of a non-conductive substrate (usually FR4) with a layer of copper on one or both sides. The thickness of the copper layer can vary, with common options being 1 oz (35 μm) and 2 oz (70 μm).
PCB Milling Process
The PCB milling process can be broken down into the following steps:
-
Design: Create the PCB design using the chosen software, ensuring that the design is compatible with the milling machine and the selected endmills and drill bits.
-
Material preparation: Cut the copper-clad board to the desired size and secure it to the milling machine bed.
-
Tool setup: Install the appropriate endmills and drill bits in the milling machine and calibrate the machine if necessary.
-
Milling: Start the milling process, which typically begins with isolation milling followed by drilling. The milling machine will follow the paths defined in the design files to remove the unwanted copper and create the holes.
-
Cleaning: After milling, remove the PCB from the machine and clean it to remove any debris or burrs.
-
Inspection: Inspect the PCB for any defects or errors, and make any necessary corrections or adjustments.
-
Assembly: Populate the PCB with components and solder them in place.
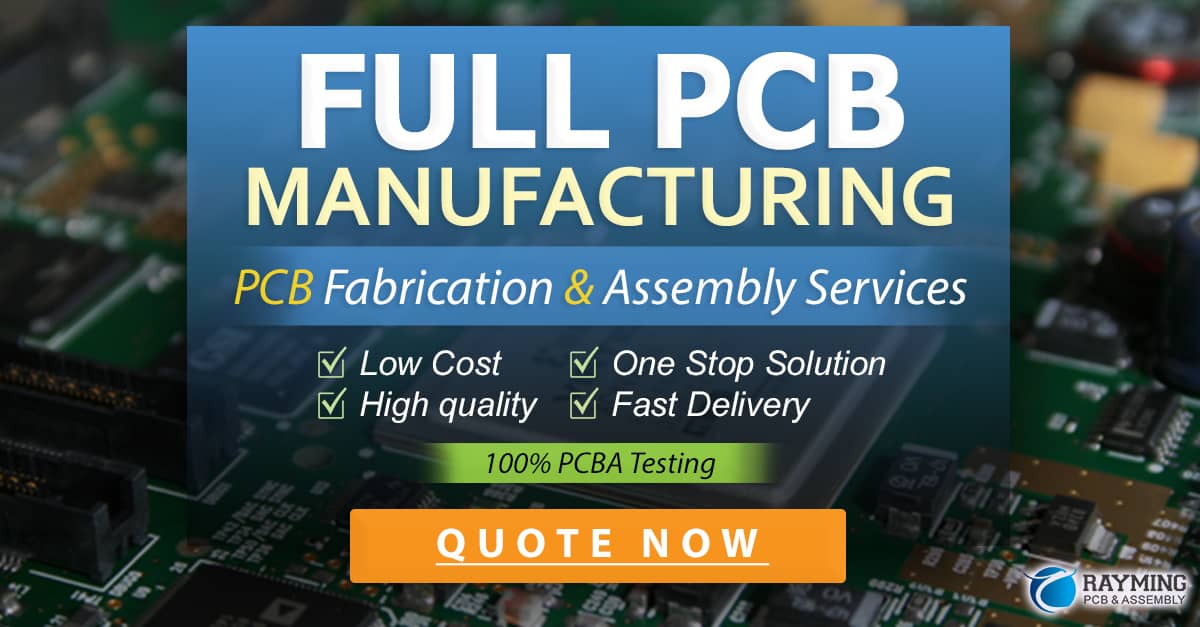
Tips for Successful PCB Milling
To ensure successful PCB milling, consider the following tips:
-
Choose the right tools: Select endmills and drill bits that are appropriate for your design and material. Consider factors such as the size of the traces, the required hole sizes, and the hardness of the copper-clad board.
-
Optimize your design: Design your PCB with milling in mind. Avoid very small traces or gaps, and ensure that your design is compatible with the capabilities of your milling machine.
-
Use a vacuum or dust collection system: PCB milling generates a significant amount of dust and debris. Use a vacuum or dust collection system to keep your workspace clean and prevent damage to the milling machine or the PCB.
-
Regularly maintain your milling machine: Keep your PCB milling machine in good condition by regularly cleaning and lubricating it according to the manufacturer’s recommendations.
-
Double-check your design files: Before starting the milling process, double-check your design files to ensure that they are correct and free of errors.
FAQ
1. What is the minimum trace width and gap size that can be achieved with PCB milling?
The minimum trace width and gap size achievable with PCB milling depend on the capabilities of the milling machine and the size of the endmills used. Typically, PCB milling can achieve trace widths and gap sizes as small as 0.1 mm (4 mil) with standard endmills, and even smaller with specialized tools.
2. Can PCB milling be used for multilayer boards?
Yes, PCB milling can be used for multilayer boards, but the process is more complex and time-consuming compared to single-layer boards. Multilayer boards require careful alignment and registration of the layers, as well as the creation of vias to connect the layers.
3. How does the cost of PCB milling compare to traditional etching?
For small-batch productions and prototyping, PCB milling can be more cost-effective than traditional etching. However, for larger production runs, etching is generally more economical due to the higher initial setup costs associated with milling.
4. Can PCB milling be used with materials other than FR4?
Yes, PCB milling machines can work with a variety of materials, including aluminum, copper, and even non-conductive materials like wood or plastic. However, the choice of material may affect the milling process and the quality of the final product.
5. What is the typical turnaround time for PCB milling?
The turnaround time for PCB milling depends on the complexity of the design and the capabilities of the milling machine. Simple single-layer boards can often be milled in a matter of hours, while more complex multilayer boards may take several days. However, PCB milling generally offers faster turnaround times compared to traditional etching, making it ideal for rapid prototyping.
Conclusion
PCB milling is a versatile and cost-effective method for fabricating prototype PCBs and small-batch productions. By understanding the equipment, process, and best practices involved in PCB milling, you can create high-quality custom circuit boards in-house, saving time and money compared to outsourcing the fabrication process.
As PCB milling technology continues to advance, it is becoming an increasingly popular choice for hobbyists, small businesses, and even larger companies looking to streamline their prototyping and small-batch production processes. With the right equipment, software, and skills, PCB milling can open up new possibilities for innovation and experimentation in the world of electronics design and fabrication.
0 Comments