Introduction to Turnkey PCB Electronics
Printed circuit boards (PCBs) are essential components in most modern electronic devices. A PCB serves as the structural framework to connect various electronic components using conductive pathways etched from copper sheets laminated onto a non-conductive substrate. The assembly of the PCB and electronic components is known as printed circuit board assembly (PCBA).
Turnkey PCB electronics manufacturing refers to contracting a single company to handle the full cycle of design, fabrication, assembly, and testing of custom PCBs and electronic devices. The turnkey manufacturer has all the required in-house capabilities and supply chain to deliver a complete, functional electronic product based on customer requirements.
Benefits of Using a Turnkey PCB Electronics Manufacturer
Choosing a turnkey electronics manufacturing partner offers several benefits compared to managing multiple vendors:
1. Simplified Logistics and Project Management
With a turnkey manufacturer, the entire production process is handled under one roof. The customer only needs to provide the product specifications, validate prototypes, and approve the final build. This greatly simplifies logistics and project management.
You avoid the hassle of sourcing components, managing contracts, and coordinating multiple vendors. The turnkey partner handles all aspects of procurement, planning, production, quality control, and delivery.
2. Faster Time-to-Market
Working with a single solutions provider results in much faster time-to-market for new electronics products.
There is no need to go through lengthy vendor selection and contracting processes. The turnkey manufacturer has established supply chains and can start production in parallel across multiple areas like PCB fabrication, component sourcing, assembly programming, etc.
Streamlined communication and alignment between design, engineering, sourcing, manufacturing, and testing teams shaves off months from product launch timelines. Quick turnaround of prototypes and fast ramp-up to mass production is enabled.
3. Lower Production Costs
Turnkey manufacturers enjoy greater economies of scale as they manufacture higher volumes across multiple customer projects. Their established global supply chain provides access to the most cost-competitive component sources.
Years of experience and process refinement lead to optimized production costs. These savings get passed down to the customer.
4. Better Quality and Reliability
Working with a single turnkey partner eliminates quality issues that often crop up when interfacing between multiple vendors. Responsibility for design, manufacturing, and testing lies with one highly experienced team.
Turnkey manufacturing facilities adhere to stringent quality standards required by the electronics industry. They utilize the latest automated assembly and testing equipment to minimize errors and defects. This results in highly reliable, field-proven products.
5. Flexible Support Across Product Lifecycle
A good turnkey partner provides complete support across the entire product lifecycle – from prototype development to mass production and post-production support.
They have the engineering expertise and manufacturing flexibility to handle evolving customer requirements during product enhancement and sustainment over years or decades.
Typical Process for Turnkey PCB Electronics Manufacturing
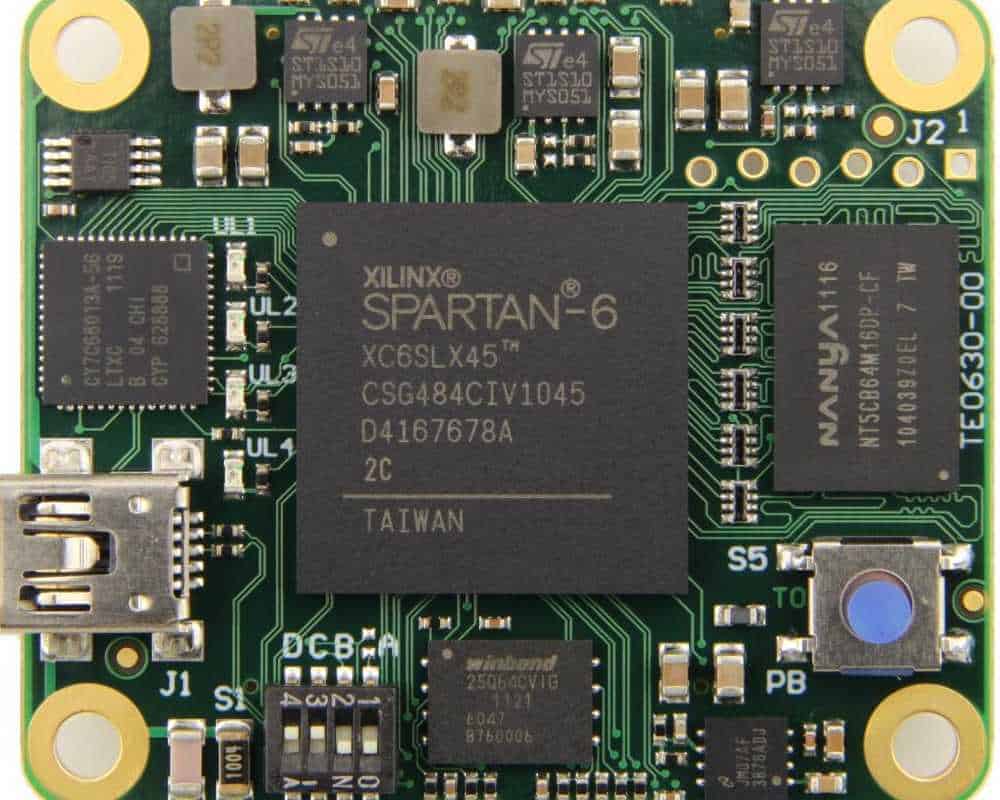
Here is an overview of the end-to-end process for turnkey electronics manufacturing:
1. Design Inputs
The customer provides detailed product design requirements, technical specifications, use cases, operating parameters, regulatory compliance needs, bill of materials, etc.
2. Concept Development
The turnkey partner develops an initial concept design to meet the customer’s product needs and specifications. This is iterated until the customer signs-off on the design.
3. Prototyping
Prototypes are fabricated to validate the product design. Multiple iterations refine the design for performance, reliability, manufacturability, and costs.
4. Testing and Certifications
The prototypes undergo extensive testing to confirm they meet all technical and regulatory requirements. Necessary certifications are obtained.
5. Pilot Production
A small pilot run validates the manufacturing processes, supply chain, assembly automation programs, test coverage, quality control, etc. prior to full production release.
6. Full Production Ramp-Up
The turnkey partner scales up production capacity to mass produce the finalized product for launch and sales.
7. Post-Production Support
The partner provides ongoing repairs, maintenance services, spare parts, and product upgrades over the entire lifecycle spanning years after launch.
Applications of Turnkey PCB Electronics Manufacturing
Turnkey PCB manufacturing services are critical across many industries such as:
- Consumer electronics – smartphones, wearables, home appliances, IoT devices.
- Industrial – sensors, instrumentation, robotics, control systems.
- Automotive – infotainment systems, ADAS, telematics, lighting.
- Medical – patient monitoring systems, digital health records, medical equipment.
- Aerospace – flight control systems, in-flight entertainment.
- Telecom infrastructure – routers, base stations, servers.
Any organization lacking specialized in-house electronics production capabilities can benefit greatly from turnkey manufacturing. It enables focus on innovation and accelerates bringing new smart electronic products to market.
Finding the Right Turnkey Electronics Manufacturing Partner
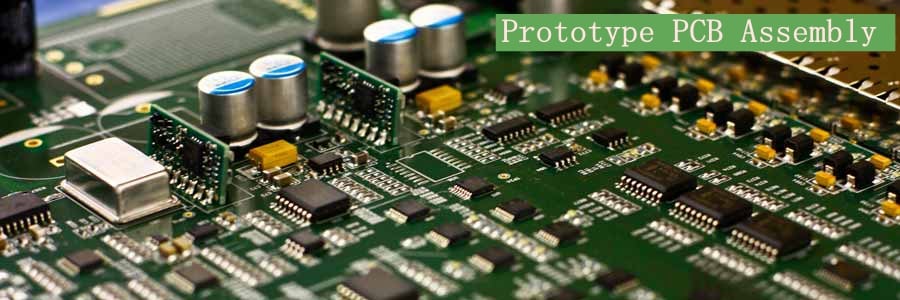
Choosing the right turnkey PCB manufacturing partner involves evaluating:
- Years of experience in electronics engineering and manufacturing. Look for at least 10-15 years minimum.
- Range of capabilities – full turnkey services from design to post-production support.
- Capacity and scalability to handle production volumes flexibly.
- End-to-end quality control and rigorous reliability testing. ISO certifications are a must.
- Use of the latest automated assembly and inspection technologies.
- Broad component sourcing channels and supplier relationships.
- Customer support and program management processes.
- Reasonable pricing, transparent cost structures.
- Geographic location and logistical capabilities aligned to your needs.
Visiting candidate turnkey partner facilities allows in-depth assessment of capabilities and culture fit. Reviewing their manufacturing quality certifications, customer success stories, and press coverage also provides insights.
Conclusion
Turnkey PCB electronics manufacturing provides innumerable benefits for organizations looking to develop custom electronic products without setting up specialized in-house infrastructure.
Choosing an experienced, well-equipped turnkey manufacturing partner can significantly cut time-to-market and costs while delivering much higher quality and reliability.
The turnkey model offers simplicity and convenience to focus innovation efforts on the product itself rather than production logistics. As electronics become ever more pervasive across consumer and industrial use cases, leveraging turnkey manufacturing ensures organizations can keep pace with demand for smart, connected technology.
Frequently Asked Questions
Q: What are the key differences when comparing turnkey PCB manufacturers?
A: The main factors differentiating turnkey PCB manufacturing partners include:
- Breadth and depth of in-house capabilities – Full turnkey services from design to post-production support or partial capabilities requiring third-party outsourcing.
- Capacity, scalability and locations – Volumes possible, ease of scaling globally aligned to customer needs.
- Technology sophistication – Use of cutting-edge automated assembly, inspection and testing.
- Quality certifications – Rigor of quality control processes. ISO 13485, ISO 9001, IATF 16949, AS 9100 certifications.
- Customer portfolio and success stories – Experience across different applications and industries.
- Cultural fit and customer service philosophy – Engineering collaboration approach.
Q: What are the pros and cons of working with a domestic vs offshore turnkey partner?
A:
Domestic Pros
- Easier communication/meetings given timezone alignment
- Faster product iteration with proximity
- ITAR compliance for defense products
- Supports local economy
Domestic Cons
- Typically higher production costs
- Limited exposure to global supply chain
Offshore Pros
- Significantly lower manufacturing costs
- Access to global component sources
- Available capacity for high-volume production
Offshore Cons
- Language barriers and timezone gaps
- Difficult to visit facilities frequently
- Potential IP protection concerns
Q: What can increase costs when working with a turnkey PCB manufacturer?
A: The main factors increasing turnkey PCB manufacturing costs include:
- Low production volumes – Lacks economies of scale.
- Numerous product revisions – Each design spin incurs NRE costs.
- Exotic components – High cost for hard-to-source components.
- Stringent quality requirements – Need for extra testing and inspections.
- Rush delivery demands – Overtime labor and expedited material costs.
- High-mix, low-volume production – Frequent changeovers hurt efficiency.
- Complex product assembly – Manual operations versus automation.
Q: How can turnkey PCB manufacturing costs be lowered?
A: Strategies to lower turnkey manufacturing costs:
- Design for manufacturing – Simplify layouts and component selections.
- Build higher volumes or aggregate demand across products.
- Standardize designs across product generations.
- Relax certain requirements that add costs but not value.
- Select turnkey partner’s standard materials and processes.
- Share long-term forecasts to enable optimization.
- Offer flexibility in delivery timelines.
- Use turnkey engineering support to optimize for cost.
Q: What are the most important contract terms when outsourcing to a turnkey manufacturer?
A: Key terms to define clearly in a turnkey electronics manufacturing contract include:
- Pricing structure – Unit costs, NREs, discounts.
- Quality processes and defect rate guarantees.
- Production capacity commitments over time.
- Lead time obligations.
- Inventory management expectations.
- Payment milestones and terms.
- Intellectual property, data security provisions.
- Warranties and post-production support.
- Regulatory compliance responsibility.
- Change order and obsolescence management.
- Supplier relationships and second sourcing rights.
- Termination, renewal, and expiration conditions.
0 Comments