What is Surface Mount Technology (SMT)?
Surface Mount Technology (SMT) is a method of mounting electronic components directly onto the surface of a Printed Circuit Board (PCB). SMT components are smaller than their Through Hole counterparts and have leads that are designed to be soldered directly onto the PCB pads. SMT has become increasingly popular in recent years due to its many advantages, including:
- Smaller component size, allowing for denser PCB layouts
- Faster assembly times, as components can be placed and soldered by automated machines
- Lower cost, due to reduced material usage and faster assembly
- Improved reliability, as SMT components have shorter leads and are less susceptible to mechanical stress
Advantages of Surface Mount Technology
-
Smaller Size: SMT components are much smaller than THT components, allowing for denser PCB layouts and smaller overall device sizes.
-
Faster Assembly: SMT components can be placed and soldered by automated machines, significantly reducing assembly times compared to manual THT assembly.
-
Lower Cost: Due to reduced material usage and faster assembly times, SMT is generally more cost-effective than THT, especially for high-volume production.
-
Improved Reliability: SMT components have shorter leads and are less susceptible to mechanical stress, resulting in improved reliability compared to THT components.
Disadvantages of Surface Mount Technology
-
Difficult Manual Assembly: Due to the small size of SMT components, manual assembly can be challenging and requires specialized tools and skills.
-
Limited Heat Dissipation: SMT components have less surface area in contact with the PCB, which can limit their ability to dissipate heat, especially for high-power components.
-
Rework Challenges: Reworking or replacing SMT components can be more difficult than THT components, as the process requires specialized equipment and skills.
What is Through Hole Technology (THT)?
Through Hole Technology (THT) is a method of mounting electronic components by inserting their leads through holes drilled in the PCB and soldering them on the opposite side. THT components are generally larger than SMT components and have longer leads. Although THT has been largely replaced by SMT in many applications, it still has its advantages, including:
- Easier manual assembly, as components are larger and more easily handled
- Better mechanical stability, as components are secured by their leads passing through the PCB
- Improved heat dissipation, as THT components have more surface area in contact with the PCB
Advantages of Through Hole Technology
-
Easier Manual Assembly: THT components are larger and more easily handled than SMT components, making manual assembly more straightforward and less prone to errors.
-
Better Mechanical Stability: THT components are secured by their leads passing through the PCB, providing better mechanical stability compared to SMT components.
-
Improved Heat Dissipation: THT components have more surface area in contact with the PCB, allowing for better heat dissipation, especially for high-power components.
-
Easier Rework: Reworking or replacing THT components is generally easier than SMT components, as the process can be done with basic soldering tools and skills.
Disadvantages of Through Hole Technology
-
Larger Size: THT components are larger than SMT components, resulting in less dense PCB layouts and larger overall device sizes.
-
Slower Assembly: THT components require manual insertion and soldering, which is slower than automated SMT assembly processes.
-
Higher Cost: Due to the larger size of THT components and slower assembly times, THT is generally more expensive than SMT, especially for high-volume production.
-
Reduced Reliability: THT components have longer leads and are more susceptible to mechanical stress, which can result in reduced reliability compared to SMT components.
Comparison Table: Surface Mount vs Through Hole
Feature | Surface Mount (SMT) | Through Hole (THT) |
---|---|---|
Component Size | Smaller | Larger |
PCB Density | Higher | Lower |
Assembly Speed | Faster (automated) | Slower (manual) |
Cost | Lower (high-volume) | Higher |
Reliability | Higher | Lower |
Heat Dissipation | Limited | Better |
Manual Assembly | Difficult | Easier |
Rework | Challenging | Easier |
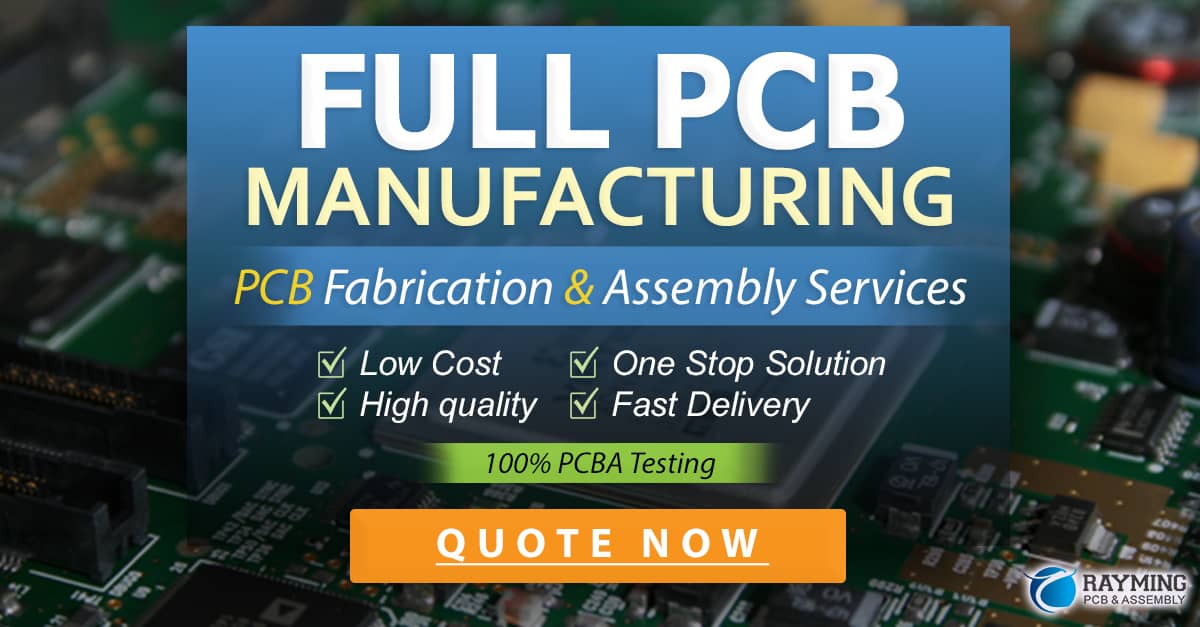
Choosing Between Surface Mount and Through Hole
When deciding between Surface Mount and Through Hole for your project, consider the following factors:
-
Production Volume: If you are producing a high volume of PCBs, SMT is generally more cost-effective due to faster assembly times and reduced material usage.
-
PCB Size: If you need to minimize the size of your PCB, SMT components are the better choice, as they allow for denser layouts.
-
Component Availability: Some components may only be available in one packaging type, which can influence your decision.
-
Assembly Process: If you plan to assemble the PCBs manually, THT components may be easier to work with. However, if you have access to automated assembly equipment, SMT is the more efficient choice.
-
Reliability Requirements: If your project requires high reliability, SMT components may be the better choice due to their improved resistance to mechanical stress.
-
Heat Dissipation: If your project includes high-power components that generate significant heat, THT components may be the better choice due to their improved heat dissipation capabilities.
Frequently Asked Questions (FAQ)
-
Q: Can SMT and THT components be used together on the same PCB?
A: Yes, it is possible to use both SMT and THT components on the same PCB. This is called a mixed-technology PCB and can be useful in situations where certain components are only available in one packaging type or when specific design requirements call for a combination of both technologies. -
Q: Are SMT components more expensive than THT components?
A: In general, individual SMT components are less expensive than their THT counterparts. However, the overall cost of an SMT PCB assembly can be higher than a THT assembly for low-volume production due to the initial setup costs of automated assembly equipment. -
Q: Can I solder SMT components by hand?
A: Yes, it is possible to solder SMT components by hand, but it requires more skill, precision, and specialized tools compared to soldering THT components. Hand soldering SMT components can be time-consuming and may not be practical for larger projects or high-volume production. -
Q: Are THT components becoming obsolete?
A: While SMT has largely replaced THT in many applications, THT components are still widely used and are not becoming obsolete. Some components are only available in THT packaging, and certain applications may require the specific advantages offered by THT, such as improved heat dissipation or mechanical stability. -
Q: Which technology is better for prototyping, SMT or THT?
A: For prototyping purposes, THT components are often preferred due to their ease of manual assembly and rework. However, if your prototype needs to closely resemble the final product or if you have access to automated SMT assembly equipment, using SMT components for prototyping can be advantageous.
Conclusion
Choosing between Surface Mount and Through Hole technologies for your electronics project depends on various factors, including production volume, PCB size, component availability, assembly process, reliability requirements, and heat dissipation needs. By understanding the advantages and disadvantages of each technology and carefully considering your project requirements, you can make an informed decision that balances cost, performance, and manufacturability.
In summary, SMT is generally the better choice for high-volume production, smaller PCB sizes, and improved reliability, while THT remains a viable option for manual assembly, high-power components, and easier rework. Ultimately, the best choice will depend on the specific needs of your project, and in some cases, a combination of both technologies may be the optimal solution.
0 Comments