Introduction to Surface Mount Soldering
Surface mount soldering is a technique used to attach surface-mount devices (SMDs) to printed circuit boards (PCBs). SMDs are electronic components that are designed to be mounted directly onto the surface of a PCB, rather than through holes like traditional through-hole components. Surface mount soldering requires precision, skill, and the right tools and techniques to achieve reliable connections between the SMDs and the PCB pads.
In this comprehensive guide, we will dive deep into the world of surface mount soldering, covering everything from the basics of soldering to advanced techniques for achieving professional results. Whether you are a beginner looking to learn the fundamentals or an experienced electronics enthusiast looking to refine your skills, this article will provide you with the knowledge and insights you need to master the art of surface mount soldering.
The Importance of Proper Solder Comprehension
Before we delve into the specifics of surface mount soldering, it’s crucial to understand the importance of proper solder comprehension. Soldering is not just about melting solder and making connections; it involves a complex interplay of heat, flux, and solder alloy that requires a deep understanding of the principles and techniques involved.
Proper solder comprehension involves:
– Understanding the properties and characteristics of different solder alloys
– Knowing how to select the right solder for a given application
– Mastering the techniques for applying heat and solder effectively
– Recognizing and troubleshooting common soldering issues
– Adhering to safety and environmental best practices
By developing a comprehensive understanding of soldering, you can ensure that your surface mount soldering projects are reliable, durable, and of the highest quality.
Essential Tools and Equipment for Surface Mount Soldering
To perform surface mount soldering effectively, you need the right tools and equipment. Here are some of the essential items you should have in your soldering toolkit:
Tool/Equipment | Description |
---|---|
Soldering Iron | A high-quality, temperature-controlled soldering iron with interchangeable tips |
Solder | A solder alloy suitable for surface mount soldering, such as lead-free solder |
Flux | A chemical compound that helps remove oxides and promote solder flow |
Tweezers | Precision tweezers for handling small SMDs |
Magnifying Glass | A magnifying glass or microscope for inspecting solder joints |
Solder Wick | A braided copper wire used for removing excess solder |
Solder Paste | A mixture of solder powder and flux used for reflow soldering |
Hot Air Rework Station | A tool that uses heated air to reflow solder and remove SMDs |
Having the right tools and equipment is essential for achieving professional-quality solder joints and ensuring the success of your surface mount soldering projects.
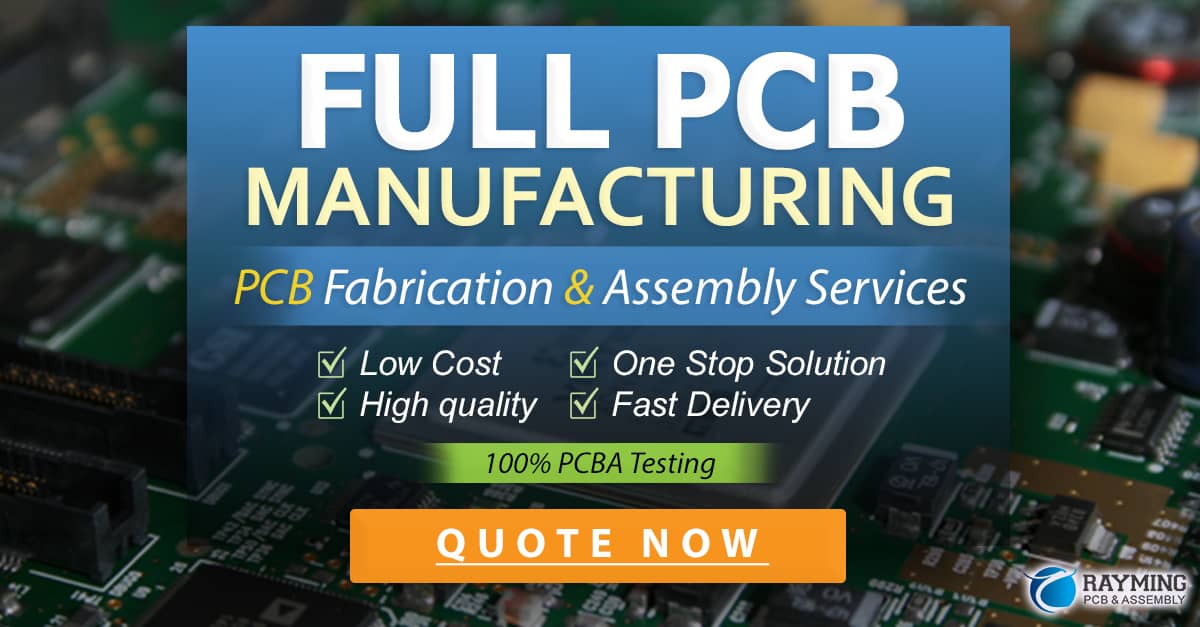
Surface Mount Device (SMD) Types and Packages
SMDs come in a wide variety of types and packages, each with its own characteristics and soldering requirements. Here are some of the most common SMD types and packages:
SMD Type | Description | Package Examples |
---|---|---|
Resistors | Passive components that resist the flow of electric current | 0402, 0603, 0805, 1206 |
Capacitors | Passive components that store electric charge | 0402, 0603, 0805, 1206 |
Inductors | Passive components that store energy in a magnetic field | 0402, 0603, 0805, 1206 |
Diodes | Semiconductor devices that allow current to flow in one direction | SOD-123, SOD-323, SOD-523 |
Transistors | Semiconductor devices used for amplification and switching | SOT-23, SOT-223, SOT-323 |
Integrated Circuits (ICs) | Complex semiconductor devices that perform specific functions | SOIC, TSSOP, QFP, BGA |
Understanding the different SMD types and packages is crucial for selecting the appropriate soldering techniques and tools, as well as for properly designing and assembling PCBs.
Soldering Techniques for Surface Mount Devices
There are several techniques for soldering SMDs to PCBs, each with its own advantages and considerations. Here are the most common surface mount soldering techniques:
Hand Soldering
Hand soldering is the most basic and versatile technique for soldering SMDs. It involves using a soldering iron to apply heat and solder to the PCB pads and SMD leads. Hand soldering requires a steady hand, good eye-hand coordination, and practice to achieve consistent results.
Tips for successful hand soldering:
– Use a soldering iron with a fine tip appropriate for the size of the SMD
– Apply a small amount of solder to one pad, then position the SMD and apply heat to the lead and pad simultaneously
– Add more solder as needed to create a proper solder joint
– Avoid applying too much heat or solder, which can cause bridging or damage to the SMD
Reflow Soldering
Reflow soldering is a technique that uses solder paste and controlled heat to solder SMDs to PCBs. The process involves applying solder paste to the PCB pads, placing the SMDs on top of the paste, and then exposing the assembly to a controlled heat profile in a reflow oven.
Advantages of reflow soldering:
– Allows for the simultaneous soldering of multiple SMDs
– Provides consistent and reliable solder joints
– Suitable for high-volume production
Considerations for reflow soldering:
– Requires specialized equipment, such as a solder paste stencil and reflow oven
– Demands precise control over the reflow temperature profile to avoid damaging the SMDs or PCB
– Requires careful handling and storage of solder paste to maintain its properties
Wave Soldering
Wave soldering is a technique primarily used for through-hole components but can also be used for certain SMDs. In wave soldering, the PCB is passed over a molten solder wave, which selectively solders the component leads to the PCB pads.
Advantages of wave soldering:
– Fast and efficient for soldering a large number of components
– Provides a strong mechanical connection between the components and PCB
Considerations for wave soldering:
– Not suitable for all SMD types and packages
– Requires proper design of the PCB and component placement to ensure successful soldering
– Can cause thermal shock to sensitive components if not controlled properly
Solder Joint Inspection and Quality Control
Creating reliable solder joints is essential for the proper functioning and longevity of electronic devices. Inspecting and evaluating the quality of solder joints is a critical step in the soldering process. Here are some key factors to consider when inspecting solder joints:
Visual Inspection
Visual inspection is the first step in evaluating Solder Joint Quality. Use a magnifying glass or microscope to closely examine the solder joints for the following characteristics:
- Proper solder joint shape and size
- Adequate solder coverage of the PCB pad and SMD lead
- Absence of solder bridges, excess solder, or insufficient solder
- Smooth and shiny solder surface, indicating good wetting and flow
Mechanical Testing
Mechanical testing involves applying physical stress to the solder joints to assess their strength and durability. Common mechanical tests include:
- Pull testing: Applying a controlled force to the SMD to test the solder joint’s tensile strength
- Shear testing: Applying a lateral force to the SMD to test the solder joint’s shear strength
- Vibration testing: Subjecting the PCB to vibration to evaluate the solder joints’ resistance to fatigue and cracking
Electrical Testing
Electrical testing is used to verify the electrical continuity and resistance of the solder joints. This can be done using a multimeter or specialized testing equipment. Electrical testing helps identify any open circuits, short circuits, or high-resistance solder joints that may affect the device’s performance.
By combining visual inspection, mechanical testing, and electrical testing, you can ensure that your solder joints meet the required quality standards and will provide reliable performance in the final application.
Common Soldering Defects and How to Avoid Them
Despite best efforts, soldering defects can occur during the surface mount soldering process. Identifying and understanding these defects is crucial for troubleshooting and preventing future issues. Here are some common soldering defects and tips on how to avoid them:
Solder Bridges
Solder bridges occur when excess solder connects adjacent PCB pads or SMD leads, causing a short circuit. To avoid solder bridges:
– Use a soldering iron with a fine tip and precise temperature control
– Apply the appropriate amount of solder, avoiding excess
– Ensure proper spacing between components and pads on the PCB
Cold Solder Joints
Cold solder joints occur when the solder fails to properly melt and flow, resulting in a weak and unreliable connection. To prevent cold solder joints:
– Ensure the soldering iron is at the correct temperature for the solder alloy used
– Apply heat to both the PCB pad and SMD lead simultaneously
– Use a clean soldering iron tip and fresh solder
Tombstoning
Tombstoning, also known as drawbridging, occurs when an SMD stands up on one end due to uneven heating or surface tension. To minimize the risk of tombstoning:
– Use solder paste with the appropriate viscosity and particle size
– Ensure even heating of the PCB pads and SMD leads
– Properly align and place the SMD on the PCB pads
Insufficient Solder Coverage
Insufficient solder coverage occurs when there is not enough solder to create a proper joint between the PCB pad and SMD lead. To ensure adequate solder coverage:
– Apply enough solder to create a concave fillet between the pad and lead
– Use solder paste with the appropriate volume and stencil thickness
– Preheat the PCB and components to improve solder flow
By understanding and addressing these common soldering defects, you can improve the quality and reliability of your surface mount soldering projects.
Safety and Environmental Considerations in Surface Mount Soldering
Surface mount soldering involves working with high temperatures, chemicals, and potentially hazardous materials. Prioritizing safety and environmental considerations is essential to protect yourself and minimize ecological impact. Here are some key safety and environmental considerations:
Personal Protective Equipment (PPE)
Always wear appropriate PPE when performing surface mount soldering:
– Safety glasses to protect your eyes from solder splashes and fumes
– Heat-resistant gloves to prevent burns and skin contact with hot surfaces
– A well-ventilated workspace or fume extraction system to minimize exposure to solder fumes
Handling Solder and Flux
Solder and flux can contain harmful substances, such as lead and rosin. To minimize risks:
– Use lead-free solder whenever possible to reduce environmental impact
– Avoid skin contact with solder and flux, and wash hands thoroughly after soldering
– Properly dispose of solder waste and cleaning materials in accordance with local regulations
Electrical Safety
Surface mount soldering involves working with electrical components and powered equipment. To ensure electrical safety:
– Always disconnect power before soldering or handling components
– Use grounded soldering irons and equipment to prevent electric shock
– Avoid touching exposed metal parts of the soldering iron or components while powered
Environmental Responsibility
Minimize the environmental impact of your surface mount soldering activities by:
– Using lead-free solder and eco-friendly cleaning solutions
– Properly recycling or disposing of electronics waste, including PCBs and components
– Conserving energy by turning off soldering equipment when not in use
By prioritizing safety and environmental considerations, you can ensure a responsible and sustainable approach to surface mount soldering.
Frequently Asked Questions (FAQ)
1. What is the difference between surface mount soldering and through-hole soldering?
Surface mount soldering involves attaching SMDs directly to the surface of a PCB, while through-hole soldering involves inserting component leads through holes in the PCB and soldering them on the opposite side. Surface mount soldering allows for smaller components and higher component density compared to through-hole soldering.
2. Do I need a special soldering iron for surface mount soldering?
While a standard soldering iron can be used for surface mount soldering, using a soldering iron with a fine tip and precise temperature control will make the process easier and more accurate. Many soldering irons designed for surface mount soldering also feature interchangeable tips to accommodate different SMD sizes and types.
3. How do I choose the right solder for surface mount soldering?
When selecting solder for surface mount soldering, consider factors such as the alloy composition, melting temperature, and diameter of the solder wire. Lead-free solder alloys, such as Sn96.5Ag3.0Cu0.5 (SAC305), are commonly used for surface mount soldering due to their favorable melting point and environmental compliance. Choose a solder diameter appropriate for the size of the SMDs and PCB pads you are working with.
4. Can I use solder paste for hand soldering SMDs?
While solder paste is primarily used for reflow soldering, it can also be used for hand soldering SMDs. Applying a small amount of solder paste to the PCB pad before placing the SMD can help with component alignment and solder joint formation. However, be aware that solder paste has a limited shelf life and requires proper storage and handling to maintain its properties.
5. How can I improve my surface mount soldering skills?
Improving your surface mount soldering skills requires practice, patience, and continuous learning. Some tips for improving your skills include:
– Practicing on scrap PCBs or soldering practice kits
– Watching tutorials and reading guides from experienced professionals
– Investing in high-quality tools and equipment
– Seeking feedback and advice from other electronics enthusiasts or professionals
– Continuously challenging yourself with more complex projects and techniques
By dedicating time and effort to refining your surface mount soldering skills, you can achieve professional-level results and tackle increasingly sophisticated electronics projects.
Conclusion
Surface mount soldering is a critical skill for anyone involved in electronics design, prototyping, or manufacturing. By developing a comprehensive understanding of soldering principles, techniques, and best practices, you can create reliable, high-quality solder joints that ensure the proper functioning and longevity of your electronic devices.
This guide has covered a wide range of topics, from the fundamentals of surface mount soldering to advanced techniques, safety considerations, and troubleshooting common issues. By applying the knowledge and insights provided in this article, you can confidently approach surface mount soldering projects and achieve professional results.
Remember, mastering surface mount soldering is an ongoing process that requires practice, patience, and a commitment to continuous learning. As you gain experience and refine your skills, you will be able to tackle increasingly complex projects and contribute to the exciting world of electronics innovation.
0 Comments