Introduction to SolderMask and Its Importance
SolderMask, also known as solder resist or solder stop mask, is a crucial component in the production of printed circuit boards (PCBs). It is a thin layer of polymer that is applied to the copper traces of a PCB to protect them from oxidation, prevent solder bridges, and provide electrical insulation. The use of SolderMask has revolutionized the PCB industry, enabling the production of high-density, reliable, and cost-effective circuit boards.
In this article, we will explore the advancements in SolderMask technology and how they have contributed to the progress of the PCB universe. We will discuss the different types of SolderMask, their properties, and their applications in various industries. Additionally, we will examine the latest trends and future prospects of SolderMask technology.
The Evolution of SolderMask Technology
Early Days of SolderMask
The concept of SolderMask dates back to the 1960s when PCBs were first introduced. Initially, PCBs were manufactured without any protective coating, which led to several issues such as oxidation, short circuits, and poor solderability. To address these problems, PCB Manufacturers began experimenting with various materials to create a protective layer on the copper traces.
One of the earliest forms of SolderMask was a screen-printed epoxy ink that was applied to the PCB surface. However, this method had several limitations, such as poor resolution, uneven coverage, and limited color options. Additionally, the epoxy ink was not very durable and could easily peel off during the soldering process.
Advancements in SolderMask Materials
Over the years, SolderMask technology has evolved significantly, with the development of new materials and application methods. One of the most significant advancements was the introduction of liquid photoimageable (LPI) SolderMask in the 1980s. LPI SolderMask is a photosensitive polymer that can be applied to the PCB surface using a screen printing or spraying method. Once applied, the LPI SolderMask is exposed to UV light through a photomask, which hardens the exposed areas while leaving the unexposed areas soluble. The soluble areas are then removed using a developer solution, leaving a precise and durable SolderMask pattern on the PCB surface.
LPI SolderMask offers several advantages over traditional epoxy ink, such as higher resolution, better adhesion, and improved durability. Additionally, LPI SolderMask is available in a wide range of colors, allowing for better visual inspection and branding of PCBs.
Another significant advancement in SolderMask technology was the development of dry film photoimageable (DFPI) SolderMask in the 1990s. DFPI SolderMask is a solid photosensitive film that is laminated onto the PCB surface using heat and pressure. Like LPI SolderMask, DFPI SolderMask is exposed to UV light through a photomask and developed to create the desired pattern.
DFPI SolderMask offers several advantages over LPI SolderMask, such as higher resolution, better thermal stability, and improved chemical resistance. Additionally, DFPI SolderMask is easier to apply and requires less equipment, making it a cost-effective option for smaller PCB manufacturers.
Comparison of SolderMask Materials
Material | Advantages | Disadvantages |
---|---|---|
Epoxy Ink | Low cost, easy to apply | Poor resolution, limited durability, limited color options |
Liquid Photoimageable (LPI) | High resolution, good adhesion, wide color range | Requires specialized equipment, longer processing time |
Dry Film Photoimageable (DFPI) | High resolution, good thermal stability, good chemical resistance | Higher cost, limited flexibility |
Properties and Characteristics of SolderMask
Electrical Insulation
One of the primary functions of SolderMask is to provide electrical insulation between the copper traces on a PCB. The SolderMask material must have a high dielectric strength to prevent current leakage and short circuits. The dielectric strength of SolderMask is typically measured in volts per mil (V/mil), with higher values indicating better insulation properties.
The dielectric strength of SolderMask varies depending on the material and thickness. LPI SolderMask typically has a dielectric strength of 1500-2000 V/mil, while DFPI SolderMask can have a dielectric strength of up to 2500 V/mil. The thickness of the SolderMask layer also affects its insulation properties, with thicker layers providing better insulation.
Thermal Stability
PCBs are often subjected to high temperatures during the soldering process and in operation. Therefore, the SolderMask material must have good thermal stability to prevent degradation and maintain its insulation properties. The glass transition temperature (Tg) and decomposition temperature (Td) are two important parameters that indicate the thermal stability of SolderMask.
The Tg of SolderMask is the temperature at which the material transitions from a rigid to a rubbery state. A higher Tg indicates better thermal stability and resistance to deformation at high temperatures. LPI SolderMask typically has a Tg of 130-150°C, while DFPI SolderMask can have a Tg of up to 180°C.
The Td of SolderMask is the temperature at which the material begins to decompose and lose its properties. A higher Td indicates better thermal stability and resistance to degradation at high temperatures. LPI SolderMask typically has a Td of 300-350°C, while DFPI SolderMask can have a Td of up to 400°C.
Chemical Resistance
PCBs are often exposed to various chemicals during the manufacturing process and in operation. Therefore, the SolderMask material must have good chemical resistance to prevent degradation and maintain its properties. The chemical resistance of SolderMask is typically evaluated using a variety of solvents and acids.
LPI SolderMask has good chemical resistance to most solvents and acids, but may be susceptible to some strong alkalis. DFPI SolderMask has excellent chemical resistance to a wide range of solvents and acids, making it suitable for use in harsh environments.
Mechanical Properties
The SolderMask material must have good mechanical properties to withstand the stresses and strains during the manufacturing process and in operation. The key mechanical properties of SolderMask include adhesion, flexibility, and hardness.
Adhesion refers to the ability of the SolderMask to bond to the copper traces and the PCB substrate. Good adhesion is essential to prevent delamination and ensure reliable performance. LPI SolderMask typically has good adhesion to copper and most PCB substrates, while DFPI SolderMask may require a surface treatment to improve adhesion.
Flexibility refers to the ability of the SolderMask to bend and flex without cracking or delaminating. Good flexibility is important for PCBs that are subjected to mechanical stress, such as those used in flexible electronics. LPI SolderMask has good flexibility, while DFPI SolderMask may be more brittle and less flexible.
Hardness refers to the ability of the SolderMask to resist scratching and abrasion. A harder SolderMask is more durable and resistant to damage during handling and assembly. LPI SolderMask typically has a hardness of 80-90 on the Shore D scale, while DFPI SolderMask can have a hardness of up to 95.
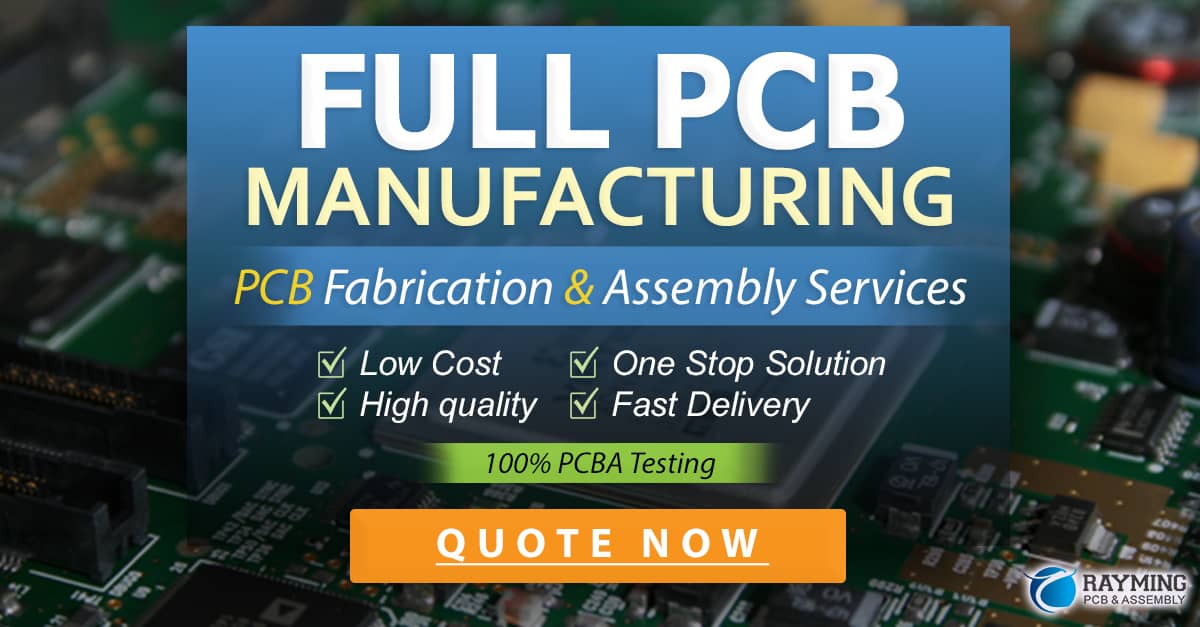
Applications of SolderMask in Various Industries
Consumer Electronics
The consumer electronics industry is one of the largest users of PCBs, and SolderMask plays a critical role in ensuring the reliability and performance of these products. From smartphones and laptops to televisions and gaming consoles, PCBs are used in a wide range of consumer electronics.
In consumer electronics, SolderMask is used to protect the copper traces from oxidation and prevent short circuits. Additionally, SolderMask is used to provide a high-contrast background for the component labels and markings, making it easier for assembly and repair.
Automotive Electronics
The automotive industry is another major user of PCBs, with modern vehicles containing hundreds of electronic components. PCBs are used in various automotive systems, such as engine control, infotainment, and advanced driver assistance systems (ADAS).
In automotive electronics, SolderMask must be able to withstand harsh environmental conditions, such as extreme temperatures, vibration, and exposure to chemicals. DFPI SolderMask is often used in automotive applications due to its excellent thermal stability and chemical resistance.
Medical Devices
PCBs are used in a wide range of medical devices, from diagnostic equipment to implantable devices. In medical applications, PCBs must meet stringent safety and reliability standards to ensure patient safety.
SolderMask is used in medical devices to provide electrical insulation and prevent short circuits. Additionally, SolderMask must be biocompatible and resistant to sterilization processes, such as autoclaving and gamma radiation. LPI SolderMask is often used in medical applications due to its good biocompatibility and ease of processing.
Aerospace and Defense
PCBs are used in various aerospace and defense applications, such as avionics, radar systems, and satellite communications. In these applications, PCBs must be able to withstand extreme environmental conditions, such as high altitudes, radiation, and electromagnetic interference (EMI).
SolderMask is used in aerospace and defense applications to provide electrical insulation and prevent short circuits. Additionally, SolderMask must be able to withstand the harsh environmental conditions and meet strict reliability standards. DFPI SolderMask is often used in aerospace and defense applications due to its excellent thermal stability and chemical resistance.
Latest Trends and Future Prospects of SolderMask Technology
Miniaturization and High-Density PCBs
One of the latest trends in PCB manufacturing is miniaturization and high-density packaging. As electronic devices become smaller and more complex, PCBs must be able to accommodate more components in a smaller space. This requires the use of finer pitch components and narrower traces, which can be challenging for traditional SolderMask materials.
To address this challenge, PCB manufacturers are developing new SolderMask materials with higher resolution and better electrical insulation properties. For example, some manufacturers are using photoimageable polyimide (PI) SolderMask, which offers higher resolution and better thermal stability than traditional LPI and DFPI SolderMask.
Environmentally Friendly SolderMask
Another trend in SolderMask technology is the development of environmentally friendly materials. Traditional SolderMask materials often contain hazardous chemicals, such as lead and halogenated compounds, which can be harmful to the environment and human health.
To address this concern, PCB manufacturers are developing new SolderMask materials that are free of hazardous chemicals and more environmentally friendly. For example, some manufacturers are using water-based LPI SolderMask, which has lower volatile organic compound (VOC) emissions than traditional solvent-based LPI SolderMask.
3D Printing of SolderMask
3D printing is another emerging trend in PCB manufacturing that could have significant implications for SolderMask technology. With 3D printing, it is possible to create complex 3D structures and patterns that are difficult or impossible to achieve with traditional manufacturing methods.
Some researchers are exploring the use of 3D printing to create SolderMask patterns directly on PCBs. This could enable the creation of more complex and customized SolderMask designs, as well as reduce the time and cost of SolderMask application.
Future Prospects
The future of SolderMask technology looks bright, with many exciting developments on the horizon. As electronic devices continue to become smaller, faster, and more complex, the demand for high-performance SolderMask materials will only increase.
One potential area of development is the use of nanomaterials in SolderMask. Nanomaterials, such as graphene and carbon nanotubes, have unique properties that could enhance the electrical insulation and thermal stability of SolderMask. However, more research is needed to understand the feasibility and cost-effectiveness of using nanomaterials in SolderMask.
Another potential area of development is the use of artificial intelligence (AI) and machine learning in SolderMask design and application. With AI, it may be possible to optimize SolderMask patterns for specific PCB designs and manufacturing processes, reducing the time and cost of SolderMask application while improving reliability and performance.
Frequently Asked Questions (FAQ)
What is SolderMask, and why is it important in PCB manufacturing?
SolderMask is a protective coating that is applied to the copper traces of a PCB to provide electrical insulation, prevent oxidation, and improve solderability. It is important because it ensures the reliability and performance of the PCB by preventing short circuits and other defects.
What are the different types of SolderMask materials?
The main types of SolderMask materials are liquid photoimageable (LPI) SolderMask, dry film photoimageable (DFPI) SolderMask, and traditional epoxy ink SolderMask. LPI and DFPI SolderMask are the most common types used in modern PCB manufacturing.
What are the key properties of SolderMask?
The key properties of SolderMask include electrical insulation, thermal stability, chemical resistance, and mechanical properties such as adhesion, flexibility, and hardness. These properties vary depending on the type of SolderMask material used.
What are some of the latest trends in SolderMask technology?
Some of the latest trends in SolderMask technology include the development of high-resolution materials for miniaturization and high-density PCBs, environmentally friendly materials that are free of hazardous chemicals, and the use of 3D printing for creating complex SolderMask patterns.
What are the future prospects for SolderMask technology?
The future prospects for SolderMask technology are promising, with potential developments in the use of nanomaterials, AI, and machine learning for optimizing SolderMask design and application. As electronic devices continue to evolve, the demand for high-performance SolderMask materials will likely increase.
Conclusion
SolderMask is a critical component in PCB manufacturing that has undergone significant advancements in recent years. From the early days of epoxy ink SolderMask to the latest developments in LPI and DFPI SolderMask, the technology has evolved to meet the changing needs of the electronics industry.
SolderMask plays a vital role in ensuring the reliability and performance of PCBs in various industries, from consumer electronics to aerospace and defense. Its key properties, such as electrical insulation, thermal stability, and chemical resistance, make it an essential material for protecting the copper traces and preventing defects.
As the electronics industry continues to evolve, so too will SolderMask technology. The latest trends, such as miniaturization, environmentally friendly materials, and 3D printing, offer exciting possibilities for the future of SolderMask. With ongoing research and development, we can expect to see even more innovative and high-performance SolderMask materials in the years to come.
0 Comments