What is Solder Mask?
Solder mask, also known as solder resist or solder stop mask, is a thin lacquer-like layer of polymer applied to the copper traces of a printed circuit board (PCB). Its primary purpose is to prevent solder from bridging between conductors and creating short circuits during the soldering process. Solder mask also provides protection against oxidation and corrosion, improves the durability of the PCB, and serves as an insulator.
Key Features of Solder Mask
- Prevents solder bridges and short circuits
- Protects against oxidation and corrosion
- Improves durability of the PCB
- Acts as an insulator
- Enhances the appearance of the PCB
Types of Solder Mask
There are two main types of solder mask: liquid photoimageable (LPI) and dry film photoimageable (DFPI).
Liquid Photoimageable (LPI) Solder Mask
LPI solder mask is the most commonly used type in the PCB industry. It is applied as a liquid polymer coating and then exposed to UV light through a photomask, which hardens the exposed areas. The unexposed areas are then removed during the development process, leaving the desired solder mask pattern on the PCB.
Advantages of LPI Solder Mask
- High resolution and accuracy
- Excellent adhesion to the PCB surface
- Good electrical insulation properties
- Available in various colors
- Cost-effective for high-volume production
Dry Film Photoimageable (DFPI) Solder Mask
DFPI solder mask is applied as a dry film laminate, which is then exposed to UV light through a photomask and developed, similar to the LPI process. DFPI is less common than LPI but offers some unique advantages.
Advantages of DFPI Solder Mask
- Consistent thickness across the PCB
- Faster application process compared to LPI
- Reduced exposure to harmful chemicals during application
- Suitable for high-density PCB designs
Solder Mask Application Process
The solder mask application process involves several steps to ensure proper coverage and adhesion to the PCB surface.
Step 1: Surface Preparation
Before applying the solder mask, the PCB surface must be cleaned and prepared to ensure proper adhesion. This typically involves a combination of chemical cleaning, micro-etching, and surface roughening.
Step 2: Solder Mask Application
The chosen type of solder mask (LPI or DFPI) is applied to the PCB surface. LPI is applied as a liquid coating using screen printing, spray coating, or Curtain Coating techniques. DFPI is laminated onto the PCB surface using a laminator.
Step 3: Exposure and Development
The applied solder mask is exposed to UV light through a photomask, which hardens the exposed areas. The unexposed areas are then removed during the development process, typically using a chemical developer.
Step 4: Curing
After development, the solder mask is cured using heat or UV light to fully harden the material and improve its mechanical and chemical properties.
Step 5: Inspection and Quality Control
The finished PCB is inspected for proper solder mask coverage, adhesion, and any defects. Quality control measures are implemented to ensure the PCB meets the required specifications.
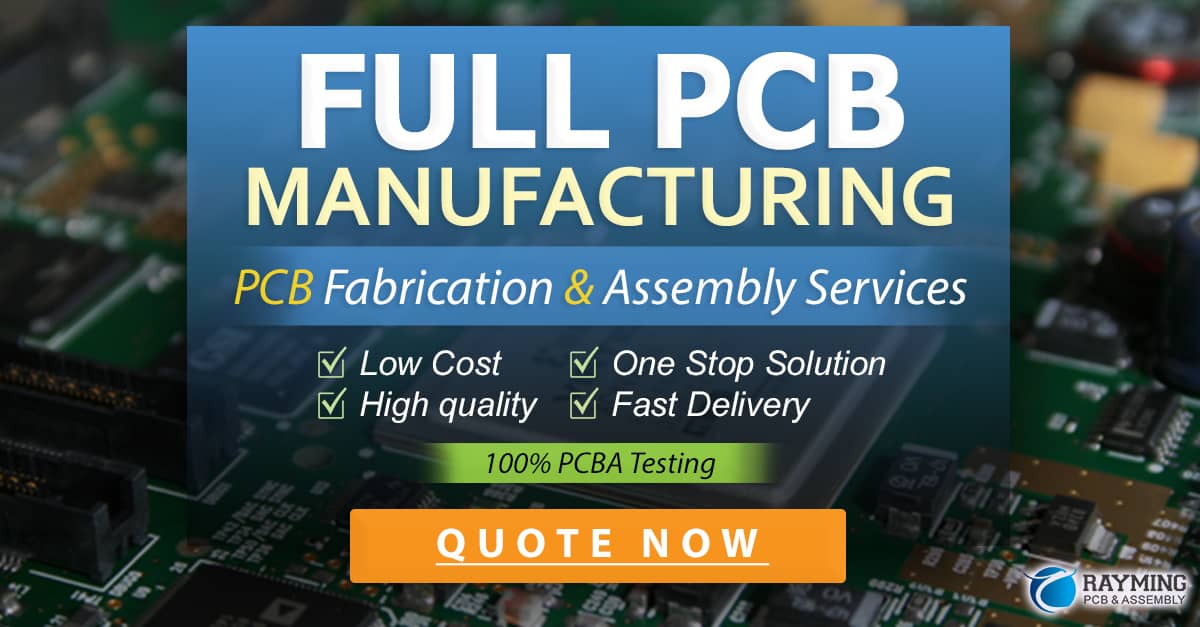
Solder Mask Colors and Their Significance
Solder mask is available in a variety of colors, each serving a specific purpose or indicating a particular characteristic of the PCB.
Color | Significance |
---|---|
Green | Most common color, provides good contrast for white silkscreen |
Blue | High-end PCBs, provides good contrast for white silkscreen |
Red | Indicates high-voltage or high-current areas |
Yellow | Indicates controlled impedance areas |
Black | Used for aesthetic purposes or to reduce light reflection |
White | Used for LED backlighting or as a reflective surface |
Solder Mask Design Considerations
When designing a PCB, several factors must be considered to ensure proper solder mask application and performance.
Solder Mask Clearance
Solder mask clearance refers to the distance between the edge of a pad or via and the solder mask opening. Adequate clearance is necessary to prevent solder mask from encroaching on the pad and interfering with solderability.
Recommended Solder Mask Clearance
Feature | Minimum Clearance |
---|---|
SMD Pads | 0.05 mm |
Through-hole Pads | 0.15 mm |
Vias | 0.10 mm |
Solder Mask Expansion
Solder mask expansion refers to the enlargement of solder mask openings to accommodate for registration tolerances and ensure proper coverage of the copper features.
Recommended Solder Mask Expansion
Feature | Minimum Expansion |
---|---|
SMD Pads | 0.05 mm |
Through-hole Pads | 0.10 mm |
Vias | 0.05 mm |
Solder Mask Thickness
The thickness of the solder mask layer affects its insulation properties, durability, and the ability to prevent solder bridging. The optimal thickness depends on the specific requirements of the PCB and the chosen solder mask material.
Typical Solder Mask Thickness
Solder Mask Type | Thickness Range |
---|---|
LPI | 0.015 – 0.040 mm |
DFPI | 0.025 – 0.050 mm |
Solder Mask Defects and Troubleshooting
Several common defects can occur during the solder mask application process, which can affect the performance and reliability of the PCB.
Solder Mask Peeling
Solder mask peeling occurs when the solder mask layer separates from the PCB surface, exposing the underlying copper. This can be caused by inadequate surface preparation, contamination, or incompatible materials.
Prevention and Troubleshooting
- Ensure proper surface cleaning and preparation
- Use compatible solder mask materials
- Optimize curing parameters
- Improve handling and storage conditions
Solder Mask Pinholes
Solder mask pinholes are small, unintended openings in the solder mask layer that expose the underlying copper. These can be caused by air bubbles, contamination, or inadequate solder mask coverage.
Prevention and Troubleshooting
- Ensure proper solder mask application techniques
- Optimize exposure and development parameters
- Implement adequate quality control measures
- Use vacuum lamination for DFPI solder mask
Solder Mask Discoloration
Solder mask discoloration refers to the unintended change in color of the solder mask layer, which can affect the appearance and legibility of the PCB. This can be caused by exposure to excessive heat, UV light, or chemical agents.
Prevention and Troubleshooting
- Use UV-stabilized solder mask materials
- Optimize curing parameters
- Avoid exposure to excessive heat or chemicals
- Implement proper storage and handling procedures
Frequently Asked Questions (FAQ)
1. What is the difference between solder mask and silkscreen?
Solder mask is a protective layer applied to the copper traces of a PCB to prevent solder bridging and provide insulation. Silkscreen, on the other hand, is a printed layer on top of the solder mask that provides text, logos, and other identifying information.
2. Can solder mask be applied to Flexible PCBs?
Yes, solder mask can be applied to flexible PCBs, but the choice of solder mask material and application process must be compatible with the flexible substrate. Specialized solder mask materials, such as polyimide or acrylic-based formulations, are often used for flexible PCBs.
3. How does solder mask affect the impedance of a PCB?
Solder mask can affect the impedance of a PCB by altering the dielectric constant of the surface layer. The thickness and dielectric properties of the solder mask material must be taken into account when designing Controlled Impedance PCBs.
4. Can solder mask be removed for rework or repair?
Yes, solder mask can be removed for rework or repair purposes using chemical or mechanical methods. However, the removal process must be carefully controlled to avoid damaging the underlying copper traces or components.
5. What is the shelf life of solder mask, and how should it be stored?
The shelf life of solder mask varies depending on the specific material and storage conditions. Generally, liquid solder mask has a shelf life of 6-12 months when stored in a cool, dry place away from direct sunlight. Dry film solder mask has a longer shelf life, typically 12-18 months, when stored under similar conditions. Always consult the manufacturer’s guidelines for specific storage and handling instructions.
0 Comments