What is Solder?
Solder is a fusible metal alloy that is used to create a permanent bond between two or more metal surfaces. It is typically composed of two or more metals, with the most common being tin and lead. The melting point of solder is lower than that of the metals being joined, allowing it to flow and fill the gaps between the surfaces, creating a strong and reliable joint.
Composition of Solder
The composition of solder varies depending on the specific application and the desired properties of the joint. The most common types of solder are:
-
Tin-lead solder: This is the most widely used type of solder, consisting of a mixture of tin and lead in various proportions. The most common ratio is 60% tin and 40% lead (60/40), which has a melting point of 183°C (361°F).
-
Lead-free solder: Due to environmental and health concerns, lead-free solders have been developed as an alternative to tin-lead solders. These solders typically consist of tin, silver, and copper (SAC) in various proportions. Common lead-free solder alloys include SAC305 (96.5% tin, 3% silver, and 0.5% copper) and SN100C (99.3% tin, 0.7% copper, and a small amount of nickel).
-
Other solder alloys: There are numerous other solder alloys designed for specific applications, such as high-temperature solders, indium-based solders for cryogenic applications, and bismuth-based solders for low-temperature applications.
Classification of Solder
Solder can be classified based on various criteria, such as composition, form, and application. Let’s explore each of these classifications in detail.
Classification by Composition
As mentioned earlier, solder can be classified based on its composition. The most common classifications are:
- Tin-lead solder
- Lead-free solder
- Other solder alloys
Tin-Lead Solder
Tin-lead solder has been the most widely used type of solder for decades due to its excellent wetting properties, low melting point, and good electrical conductivity. The most common tin-lead solder alloys and their melting points are:
Alloy | Tin (%) | Lead (%) | Melting Point (°C) |
---|---|---|---|
63/37 | 63 | 37 | 183 |
60/40 | 60 | 40 | 183-188 |
50/50 | 50 | 50 | 183-216 |
However, due to the toxicity of lead and its harmful effects on human health and the environment, the use of tin-lead solder has been restricted or banned in many countries, particularly in the electronics industry.
Lead-Free Solder
Lead-free solders have been developed as an alternative to tin-lead solders to address the environmental and health concerns associated with lead. The most common lead-free solder alloys and their melting points are:
Alloy | Composition | Melting Point (°C) |
---|---|---|
SAC305 | 96.5% Sn, 3% Ag, 0.5% Cu | 217-220 |
SAC387 | 95.5% Sn, 3.8% Ag, 0.7% Cu | 217-218 |
SN100C | 99.3% Sn, 0.7% Cu, 0.05% Ni | 227 |
SnCu | 99.3% Sn, 0.7% Cu | 227 |
SnAg | 96.5% Sn, 3.5% Ag | 221 |
Lead-free solders generally have higher melting points and different wetting properties compared to tin-lead solders, which can pose challenges in certain applications. However, they offer a more environmentally friendly and safer alternative.
Other Solder Alloys
There are numerous other solder alloys designed for specific applications, such as:
-
High-temperature solders: These solders have higher melting points and are used in applications where the joint will be exposed to elevated temperatures, such as in automotive and aerospace industries. Examples include gold-tin (Au-Sn) and gold-germanium (Au-Ge) solders.
-
Indium-based solders: These solders have low melting points and are used in cryogenic applications or for joining materials with different coefficients of thermal expansion. Examples include indium-tin (In-Sn) and indium-lead (In-Pb) solders.
-
Bismuth-based solders: These solders have low melting points and are used in low-temperature applications or for joining temperature-sensitive components. Examples include bismuth-tin (Bi-Sn) and bismuth-lead (Bi-Pb) solders.
Classification by Form
Solder can also be classified based on its physical form. The most common forms of solder are:
- Solder wire
- Solder paste
- Solder bar
- Solder preforms
Solder Wire
Solder wire is the most common form of solder used in hand soldering applications. It consists of a thin wire of solder alloy, typically with a rosin core that acts as a flux to help the solder flow and adhere to the metal surfaces. Solder wire is available in various diameters, alloy compositions, and flux types to suit different applications.
Solder Paste
Solder paste is a mixture of tiny solder particles suspended in a flux paste. It is used in surface mount technology (SMT) for soldering components onto printed circuit boards (PCBs). Solder paste is applied to the PCB using a stencil or syringe, and the components are then placed on top. The assembly is heated in a reflow oven, melting the solder particles and creating a permanent bond between the components and the PCB.
Solder Bar
Solder bar, also known as solder ingot, is a large, solid piece of solder alloy. It is typically used in wave soldering machines for soldering through-hole components onto PCBs. The solder bar is melted in a solder pot, and the PCB is passed over a wave of molten solder, which flows through the holes and creates a joint between the component leads and the PCB.
Solder Preforms
Solder preforms are pre-shaped pieces of solder designed for specific applications, such as soldering connectors, terminals, or heat sinks. They are available in various shapes, such as rings, washers, and discs, and can be placed directly onto the components before heating. Solder preforms provide a precise amount of solder and help ensure consistent joint quality.
Classification by Application
Solder can also be classified based on its intended application. Some common applications include:
- Electronics soldering
- Plumbing soldering
- Jewelry soldering
- Automotive soldering
Electronics Soldering
Electronics soldering involves joining electronic components, wires, and PCBs using solder. This application requires solder alloys with good electrical conductivity, wetting properties, and mechanical strength. Common solder alloys used in electronics include tin-lead (SnPb) and lead-free alloys such as SAC (tin-silver-copper) and SN100C.
Plumbing Soldering
Plumbing soldering involves joining copper pipes and fittings in water supply and heating systems. This application requires solder alloys with good wetting properties, mechanical strength, and corrosion resistance. Common solder alloys used in plumbing include tin-lead (SnPb) and lead-free alloys such as tin-silver (SnAg) and tin-copper (SnCu).
Jewelry Soldering
Jewelry soldering involves joining precious metal components, such as gold, silver, and platinum, to create intricate designs and settings. This application requires solder alloys with a lower melting point than the base metals, good wetting properties, and matching color. Common solder alloys used in jewelry include gold-based, silver-based, and platinum-based alloys.
Automotive Soldering
Automotive soldering involves joining electrical components and wiring in vehicles. This application requires solder alloys with good electrical conductivity, mechanical strength, and resistance to vibration and thermal cycling. Common solder alloys used in automotive applications include high-temperature alloys such as tin-silver-copper (SAC) and tin-zinc (SnZn).
Frequently Asked Questions (FAQ)
- What is the difference between soldering and welding?
-
Soldering involves joining metal surfaces using a filler metal (solder) with a melting point lower than that of the base metals. The base metals do not melt during the process. In contrast, welding involves melting and fusing the base metals together, often with the addition of a filler metal.
-
Can lead-free solder be used for all applications?
-
Lead-free solder can be used for most applications, but it may not be suitable for some specific cases. For example, in high-temperature applications or when joining certain materials, lead-based or other specialized solder alloys may be required.
-
What is flux, and why is it used in soldering?
-
Flux is a chemical compound that helps remove oxides and other contaminants from the metal surfaces during soldering. It promotes better wetting and adhesion of the solder to the base metals, ensuring a strong and reliable joint.
-
Can solder joints be inspected for quality?
-
Yes, solder joints can be inspected visually or using various testing methods, such as X-ray imaging, acoustic microscopy, or destructive testing. Visual inspection can reveal issues like insufficient solder, bridging, or poor wetting, while other methods can detect internal defects or assess the mechanical strength of the joint.
-
How can I choose the right solder for my application?
- Choosing the right solder depends on several factors, including the base materials being joined, the desired properties of the joint (e.g., electrical conductivity, mechanical strength, thermal stability), and the environmental conditions the joint will be exposed to. Consider consulting with a solder manufacturer or supplier to select the most suitable solder alloy for your specific application.
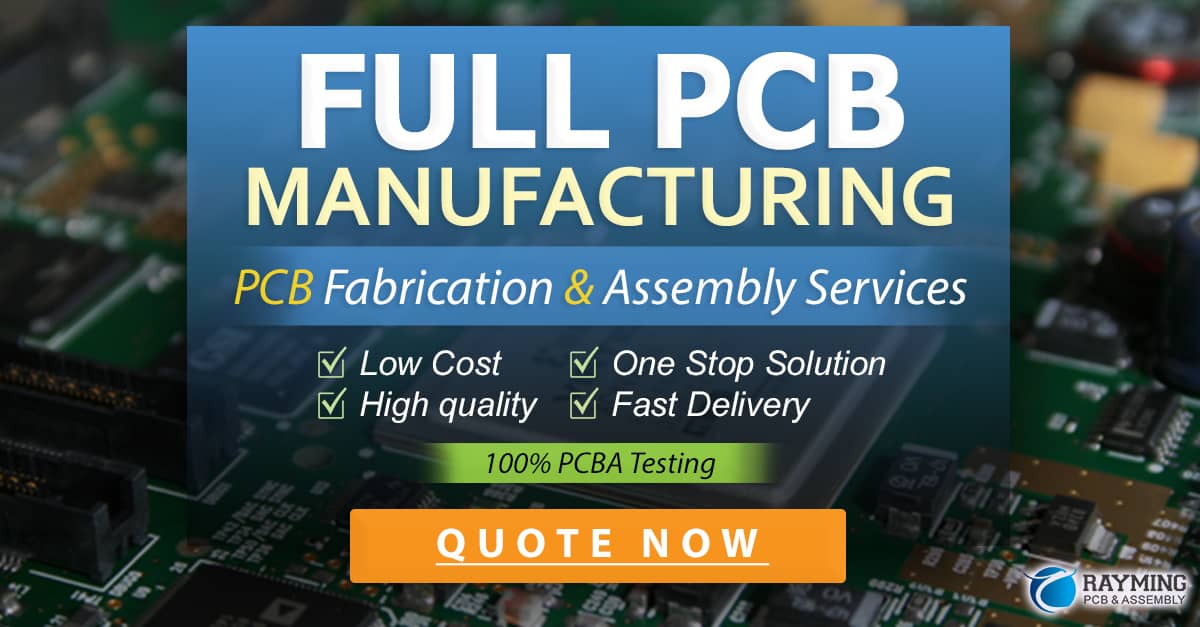
Conclusion
Solder is a versatile and essential material used in various industries for joining metal surfaces. It is available in different compositions, forms, and applications to suit specific requirements. Understanding the classification of solder based on these criteria is crucial for selecting the right solder for a given application and ensuring the quality and reliability of the soldered joint.
As environmental and health concerns drive the shift towards lead-free solders, it is important to stay informed about the latest developments in solder technology and adapt to new materials and processes. By choosing the appropriate solder and following best practices for soldering, manufacturers can create strong, reliable, and long-lasting soldered joints in a wide range of applications.
0 Comments