Introduction
Surface mount technology (SMT) has revolutionized the electronics manufacturing industry over the past few decades. SMT enables the mounting of electronic components directly onto the surface of printed circuit boards (PCBs) without the need for through-hole connections. The use of SMT has brought tremendous advantages in electronics manufacturing in terms of improved efficiency, quality, and reliability. This article explores the key benefits of SMT in manufacturing and its evolving role in enabling advanced PCB assembly and electronics production.
Reduced Size and Weight
One of the most significant advantages of SMT is the reduced size and weight of components packaged for surface mounting. SMT components are designed without leads or connecting wires, allowing for a more compact footprint. This size reduction allows SMT to facilitate miniaturization and portability of modern electronic devices.
The following table compares the size differences between through-hole and SMT components:
Component | Through-Hole Size | SMT Size |
---|---|---|
Resistor | 6.5mm x 3.2mm x 2.5mm | 1.5mm x 0.8mm x 0.5mm |
Capacitor | 5mm x 2.5mm | 0805 package (2mm x 1.25mm) |
Transistor | 10mm x 10mm x 6mm | SOT-23 package (3mm x 1.5mm) |
As evident from the table, SMT components take up a fraction of the space compared to their through-hole counterparts. This size reduction allows for greater component density on PCBs, enabling further miniaturization and functionality improvements in electronic devices.
Improved Reliability
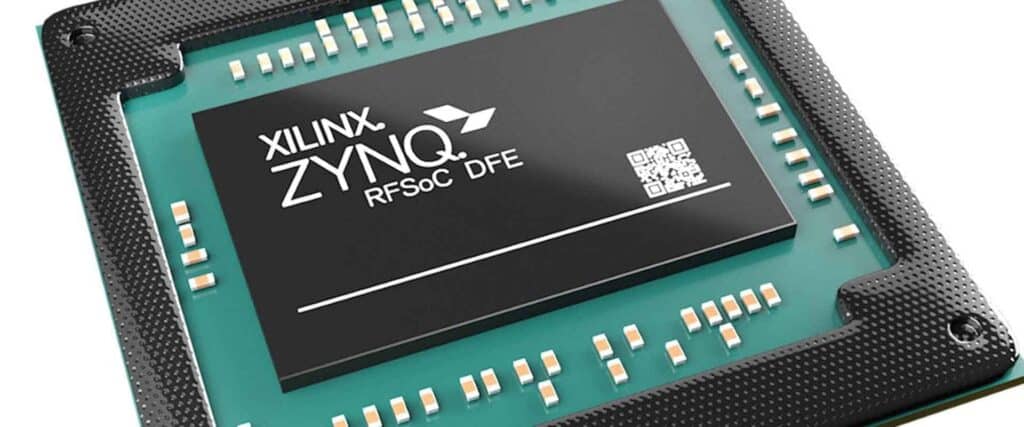
SMT improves reliability through:
- Reduced Failure Points: The lack of leads and soldered through-hole connections eliminates potential failure points.
- Less Handling: Automated SMT assembly involves less human handling and contact than manual through-hole assembly.
- Superior Solder Joints: SMT reflow soldering ensures uniform and consistent solder joints.
- Component Protection: The direct attachment of components onto surfaces reduces mechanical stresses and damage.
Together, these factors result in SMT assemblies demonstrating higher resistance to vibration, shock, thermal cycling, and mechanical stress. Field failure rates of SMT assemblies have proven to be an order of magnitude lower compared to through-hole assemblies.
Higher Production Speeds
SMT enables a high degree of automation in PCB assembly, significantly increasing manufacturing throughput and efficiency. Key advantages include:
- Component Placement: High-speed SMT pick-and-place machines can precisely place tens of thousands of components per hour. This is drastically faster than manual insertion.
- Soldering: Reflow soldering ovens can simultaneously solder hundreds to thousands of joints in minutes, compared to hand soldering each joint individually.
- Inspection: Automated optical inspection (AOI) can quickly scan assembled boards for defects.
This reduction in assembly time allows manufacturers to scale up production capacity to meet demands. High-mix, low-volume flexible manufacturing is also facilitated by fast changeovers between SMT assembly programs.
Improved Process Control and Yields
The automation of SMT assembly enables advanced process control and feedback capabilities. Key elements include:
- Precise pick-and-place machines ensure accurate and consistent component positioning, virtually eliminating placement defects.
- Reflow profiling allows optimization of thermal profiles for reliable soldering. In-line inspection points can provide feedback for profile adjustments.
- AOI systems immediately flag component and soldering defects.
Together, these capabilities minimize process variability and dramatically improve yields compared to manual assembly. As volumes scale up, statistical process control can be implemented to further optimize the entire assembly process.
Facilitating Advanced Packaging and Miniaturization
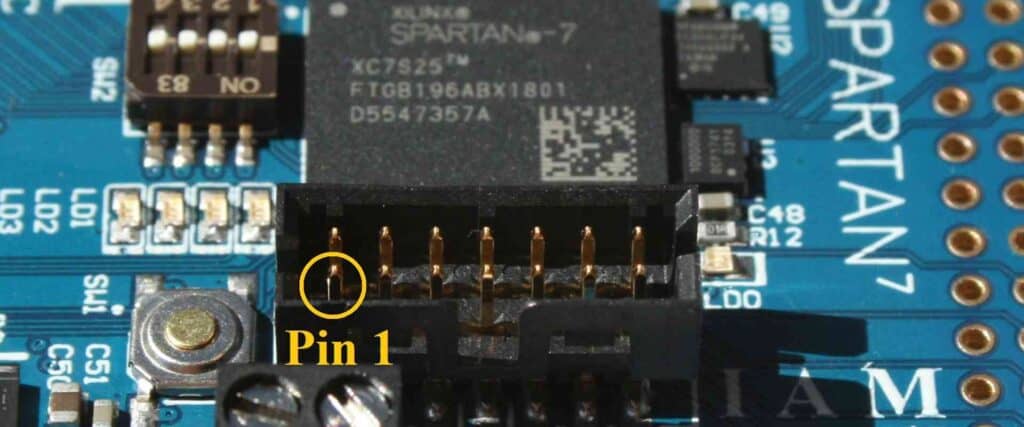
Continued advancements in SMT technology and packaging techniques have enabled higher component densities and more complex PCB assemblies. Some key developments include:
- Fine-pitch components: Chips and passive components with finer terminal spacing allow for greater PCB area utilization.
- Ball grid arrays (BGAs): BGA packages allow leads to be arrayed under the component, enabling high I/O counts in small footprints.
- Chip-scale and wafer-level packaging: Dies are packaged at the wafer level in a footprint close to the die size before singulation.
- 3D packaging: Technologies like package-on-package (PoP) allow vertical stacking of ICs in a single footprint.
These and other emerging packaging methods rely extensively on SMT for assembly, facilitating continual electronics miniaturization.
Enabling Modern Electronics Manufacturing
The transition from through-hole assembly to SMT has transformed electronics manufacturing over the past several decades. SMT underpins nearly all modern electronics production due to its advantages in efficiency, quality, and reliability. As volumes have scaled, automated SMT lines have become essential for cost-effective manufacturing. At the same time, the technology has proven flexible enough to enable prototyping and low-volume production.
Continual improvements in SMT equipment, materials, and processes will help drive next-generation miniaturization and performance improvements. SMT will continue to be a foundational technology enabling cutting-edge electronic product development and deployment worldwide. Adoption of SMT principles and best practices will be key for any manufacturer looking to leverage the latest advances in electronics manufacturing.
Frequently Asked Questions
What are the main SMT equipment types used in assembly?
The core SMT assembly equipment includes:
- SMT pick-and-place machines for automated component population
- SMT solder paste printers for paste deposition
- Reflow ovens for soldering components
- Inspection systems such as AOI and x-ray for quality control
How are component packages designed for SMT?
Common SMT component packages include:
- Chip-scale packages like QFNs and LGAs
- Standard rectangular passive component sizes like 0201, 0402, etc
- BGAs with solder ball grids under ICs
- Specialty packages like wafer-level CSP
Packages are designed with terminals/pads on the underside for surface soldering.
What are some key SMT materials used?
Key SMT materials include:
- Solder paste – provides flux and solder alloy for solder joints
- Solder masks – insulate and protect soldered traces
- Solder resists – coatings that avoid shorts between joints
How can manufacturers ramp up SMT capabilities?
Important steps in building SMT capabilities:
- Invest in SMT equipment and optimize processes
- Develop expertise in SMT materials, design, assembly, inspection
- Implement ERP/MES systems to manage production
- Leverage SMT contract manufacturers if needed
How does SMT reduce environmental impact?
SMT improves sustainability through:
- Reduced materials usage from miniaturization
- Reduction in leaded solder use
- Recoverability of precious metals from ICs
- Energy savings from smaller/lighter products
0 Comments