Optimize PCB Design for Manufacturing
One of the most effective ways to reduce PCB assembly cost is by designing your boards with manufacturing in mind from the start. This approach, known as Design for Manufacturing (DFM), involves making design choices that simplify the assembly process and minimize the potential for errors or defects.
Keep the Board Size Small
Smaller PCBs require less material, are faster to assemble, and can often be panelized more efficiently, leading to lower overall costs. Consider the following tips:
- Use the smallest components that meet your performance requirements
- Minimize the number of layers in your PCB stack-up
- Opt for a smaller board size when possible
Use Standard Components and Footprints
Whenever possible, select components that are widely available and have standard footprints. This can help reduce sourcing costs and lead times, as well as simplify the assembly process. Some guidelines include:
- Choose components with standard packaging (e.g., 0603, 0805, SOIC, QFP)
- Avoid using custom or proprietary components unless absolutely necessary
- Use surface mount components instead of through-hole when possible
Minimize the Number of Unique Parts
Reducing the number of unique components on your PCB can simplify inventory management, reduce the risk of assembly errors, and lead to volume discounts from suppliers. Consider the following strategies:
- Consolidate components with similar functions or values
- Use generic parts instead of highly specialized components when possible
- Implement a part standardization program across product lines
Optimize Placement and Routing
Efficient component placement and routing can reduce assembly time and minimize the risk of defects. Some best practices include:
- Group similar components together to streamline the assembly process
- Provide adequate spacing between components for ease of soldering
- Use a gridded layout to simplify placement and inspection
- Route traces to minimize the number of vias and layer changes
Leverage Cost-Effective Sourcing Strategies
Sourcing components and materials strategically can have a significant impact on your overall PCB assembly costs. By developing strong supplier relationships, taking advantage of volume discounts, and staying informed about market trends, you can optimize your sourcing practices for maximum cost-efficiency.
Develop Strong Supplier Relationships
Building long-term relationships with reliable suppliers can lead to better pricing, improved lead times, and enhanced support. Consider the following tips:
- Communicate your requirements and expectations clearly
- Provide accurate forecasts to help suppliers plan their production
- Collaborate with suppliers to identify cost-saving opportunities
- Maintain open lines of communication to resolve issues quickly
Negotiate Volume Discounts
Purchasing components and materials in larger quantities can often result in significant cost savings. When planning your production runs, consider the following strategies:
- Consolidate orders across multiple products or projects
- Negotiate volume discounts with suppliers based on your anticipated demand
- Explore the possibility of blanket orders or long-term agreements
- Consider the trade-offs between volume discounts and inventory carrying costs
Stay Informed About Market Trends
Keeping track of market trends and pricing fluctuations can help you make informed sourcing decisions and take advantage of cost-saving opportunities. Some tips include:
- Monitor industry news and reports for insights on supply chain trends
- Attend trade shows and conferences to network with suppliers and peers
- Use online resources and tools to compare pricing and availability
- Consider the impact of global economic and political factors on your supply chain
Optimize Your Manufacturing Processes
Streamlining your PCB assembly processes can lead to significant cost savings by reducing cycle times, minimizing waste, and improving overall efficiency. By implementing lean manufacturing principles, investing in automation, and collaborating with your contract manufacturer, you can optimize your production for maximum cost-effectiveness.
Implement Lean Manufacturing Principles
Lean manufacturing focuses on eliminating waste, reducing variability, and continuously improving processes. Some key principles to consider include:
- Identify and eliminate non-value-added activities
- Implement just-in-time (JIT) inventory management
- Use visual management techniques to quickly identify problems
- Foster a culture of continuous improvement and employee engagement
Invest in Automation
Automating certain aspects of your PCB assembly process can reduce labor costs, improve consistency, and increase throughput. Consider the following opportunities for automation:
- Use automated optical inspection (AOI) systems to detect defects
- Implement automated material handling and storage solutions
- Explore the use of robotic assembly for high-volume production
- Invest in automated testing equipment to reduce manual testing time
Collaborate with Your Contract Manufacturer
Working closely with your contract manufacturer (CM) can help identify cost-saving opportunities and ensure a smooth production process. Some tips for effective collaboration include:
- Share your design files and requirements early in the process
- Involve your CM in design reviews to identify potential manufacturing issues
- Communicate your production forecasts and any changes in demand
- Establish clear quality expectations and metrics for evaluating performance
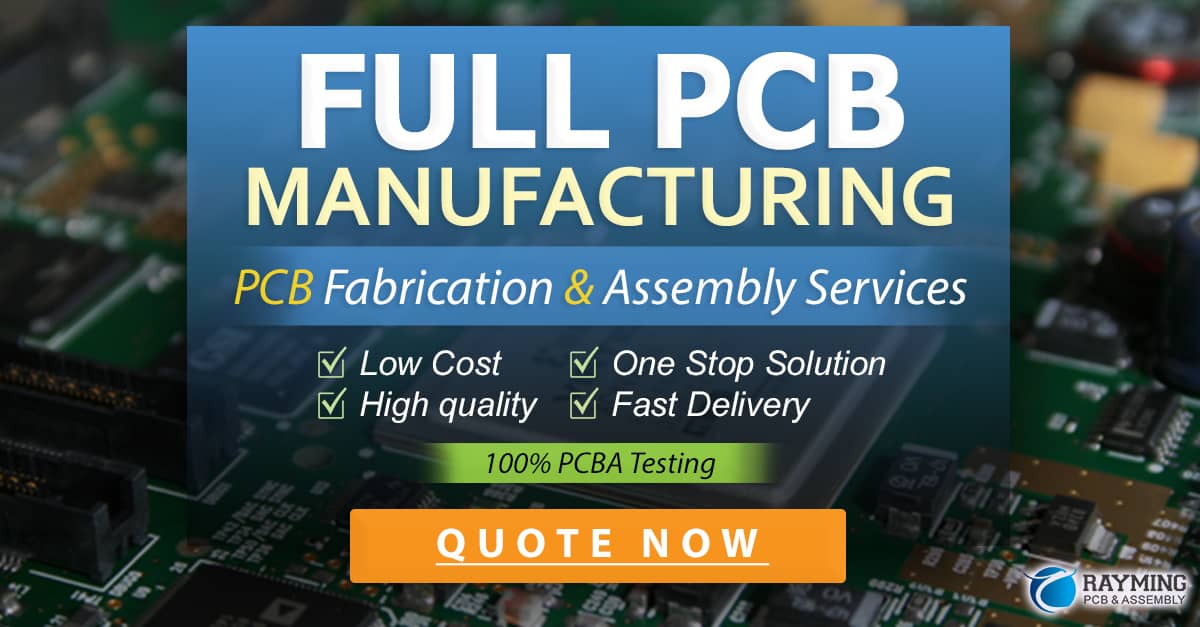
Frequently Asked Questions (FAQ)
1. What is Design for Manufacturing (DFM), and why is it important for reducing PCB assembly costs?
Design for Manufacturing (DFM) is an approach to PCB design that takes into account the manufacturing process from the start, making design choices that simplify assembly and minimize the potential for errors or defects. By implementing DFM principles, companies can reduce assembly costs, improve quality, and accelerate time-to-market.
2. How can I identify opportunities for component consolidation in my PCB design?
To identify opportunities for component consolidation, start by reviewing your bill of materials (BOM) and looking for components with similar functions or values. Consider using generic parts instead of highly specialized components when possible, and explore the possibility of implementing a part standardization program across product lines.
3. What are the benefits of building long-term relationships with PCB assembly suppliers?
Building long-term relationships with reliable PCB assembly suppliers can lead to several benefits, including better pricing, improved lead times, and enhanced support. By communicating your requirements clearly, providing accurate forecasts, and collaborating to identify cost-saving opportunities, you can foster strong supplier relationships that contribute to your overall cost-reduction efforts.
4. How can lean manufacturing principles be applied to PCB assembly?
Lean manufacturing principles can be applied to PCB assembly by focusing on eliminating waste, reducing variability, and continuously improving processes. Some key strategies include identifying and eliminating non-value-added activities, implementing just-in-time (JIT) inventory management, using visual management techniques to quickly identify problems, and fostering a culture of continuous improvement and employee engagement.
5. What role can automation play in reducing PCB assembly costs?
Automation can play a significant role in reducing PCB assembly costs by reducing labor costs, improving consistency, and increasing throughput. Some opportunities for automation include using automated optical inspection (AOI) systems to detect defects, implementing automated material handling and storage solutions, exploring the use of robotic assembly for high-volume production, and investing in automated testing equipment to reduce manual testing time.
Conclusion
Reducing PCB assembly costs is a critical objective for electronics manufacturers looking to remain competitive in today’s market. By optimizing PCB design for manufacturing, leveraging cost-effective sourcing strategies, and streamlining manufacturing processes, companies can achieve significant cost savings while maintaining high quality standards.
Implementing Design for Manufacturing (DFM) principles, such as keeping board sizes small, using standard components and footprints, minimizing unique parts, and optimizing placement and routing, can simplify the assembly process and reduce the potential for errors and defects.
Developing strong supplier relationships, negotiating volume discounts, and staying informed about market trends can help optimize sourcing practices for maximum cost-efficiency.
Finally, by embracing lean manufacturing principles, investing in automation, and collaborating closely with contract manufacturers, companies can further streamline their PCB assembly processes and drive down costs.
By adopting a comprehensive approach to PCB Cost-Cutting that encompasses design, sourcing, and manufacturing, electronics companies can position themselves for long-term success in an increasingly competitive landscape.
0 Comments