What is Wave Soldering?
Wave soldering is a traditional soldering method that has been widely used in the electronics industry for decades. It involves passing the PCB over a molten solder wave, allowing the solder to come into contact with the exposed leads and pads on the board. The solder then solidifies, creating a strong electrical and mechanical connection between the components and the PCB.
The Wave Soldering Process
The wave soldering process typically consists of the following steps:
- Flux application: A thin layer of flux is applied to the bottom side of the PCB to remove oxides and improve solder wettability.
- Preheating: The PCB is preheated to activate the flux and minimize thermal shock during soldering.
- Soldering: The PCB is passed over a molten solder wave, allowing the solder to come into contact with the exposed leads and pads.
- Cooling: The soldered PCB is cooled to allow the solder joints to solidify.
Advantages of Wave Soldering
- High throughput: Wave soldering is a fast process that can handle large volumes of PCBs in a short period.
- Cost-effective: Wave soldering is generally more affordable than other soldering methods, especially for high-volume production.
- Versatility: Wave soldering can accommodate a wide range of component types and sizes.
Disadvantages of Wave Soldering
- Limited precision: Wave soldering may not be suitable for PCBs with fine-pitch components or complex layouts.
- Thermal stress: The entire PCB is exposed to high temperatures during wave soldering, which can cause thermal stress on sensitive components.
- Solder bridging: Wave soldering may result in solder bridging between closely spaced leads or pads.
What is Selective Soldering?
Selective soldering is a more advanced and targeted approach to PCB Soldering. Unlike wave soldering, which exposes the entire board to molten solder, selective soldering focuses on specific areas or components on the PCB. This is achieved using a precisely controlled solder nozzle that dispenses solder only where needed.
The Selective Soldering Process
The selective soldering process typically involves the following steps:
- PCB loading: The PCB is loaded into the selective soldering machine, either manually or using an automated system.
- Flux application: Flux is applied to the specific areas or components that require soldering.
- Preheating: The targeted areas are preheated to activate the flux and ensure optimal solder joint formation.
- Soldering: The solder nozzle dispenses molten solder onto the desired locations, creating a strong bond between the components and the PCB.
- Cooling: The soldered areas are cooled to allow the solder joints to solidify.
Advantages of Selective Soldering
- Precision: Selective soldering offers high precision, making it ideal for PCBs with fine-pitch components or complex layouts.
- Reduced thermal stress: Since only specific areas are exposed to heat, selective soldering minimizes thermal stress on sensitive components.
- Flexibility: Selective soldering allows for the soldering of both through-hole and surface mount components on the same PCB.
- Reduced solder consumption: By targeting only the necessary areas, selective soldering reduces overall solder consumption.
Disadvantages of Selective Soldering
- Higher initial investment: Selective soldering machines are generally more expensive than wave soldering equipment.
- Lower throughput: Selective soldering is a slower process compared to wave soldering, as each component or area is soldered individually.
- Programming requirements: Selective soldering machines require precise programming to ensure accurate solder dispensing.
Wave vs Selective Soldering: A Comparison
To help you determine which soldering method is better suited for your PCB assembly needs, let’s compare wave and selective soldering based on several key factors:
Factor | Wave Soldering | Selective Soldering |
---|---|---|
Throughput | High | Low to Medium |
Precision | Low to Medium | High |
Component Compatibility | Mostly through-hole | Through-hole and surface mount |
Thermal Stress | High | Low |
Solder Consumption | High | Low |
Initial Investment | Low to Medium | High |
Flexibility | Limited | High |
Based on this comparison, wave soldering is generally more suitable for high-volume production of PCBs with mostly through-hole components and simple layouts. On the other hand, selective soldering is the better choice for PCBs with fine-pitch components, complex layouts, or a mix of through-hole and surface mount components.
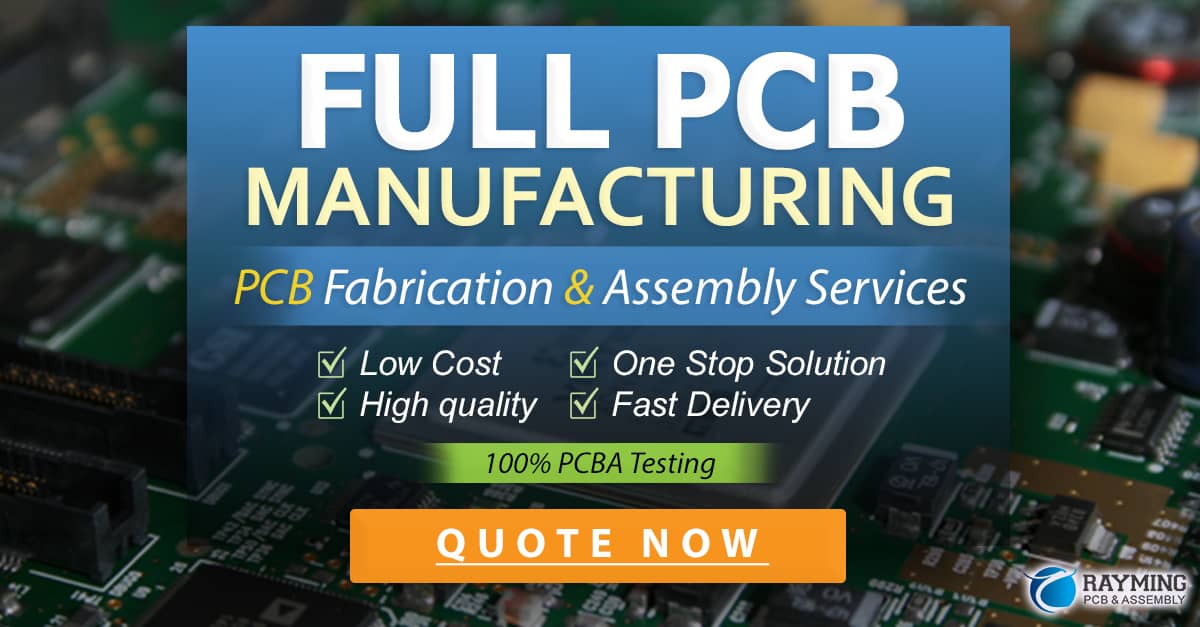
FAQ
-
Q: Can wave soldering handle surface mount components?
A: While wave soldering is primarily used for through-hole components, it can accommodate some surface mount components with proper fixturing and solder masking. -
Q: Is selective soldering suitable for high-volume production?
A: Although selective soldering is slower than wave soldering, modern selective soldering machines can achieve reasonable throughput rates, making them suitable for medium to high-volume production. -
Q: Can selective soldering eliminate the need for manual touch-up?
A: Selective soldering offers high precision and control, greatly reducing the need for manual touch-up. However, some complex PCBs may still require minor hand soldering. -
Q: Is it possible to combine wave and selective soldering in the same PCB assembly process?
A: Yes, some PCB assembly lines incorporate both wave and selective soldering stations to leverage the advantages of each method for different components or areas of the board. -
Q: Which soldering method is more environmentally friendly?
A: Selective soldering generally consumes less solder and energy compared to wave soldering, making it a more environmentally friendly option.
Conclusion
Choosing between wave and selective soldering for your PCB assembly process ultimately depends on your specific requirements, such as production volume, component types, board complexity, and budget. Wave soldering remains a cost-effective and efficient option for high-volume production of simple PCBs with mostly through-hole components. However, as electronics continue to miniaturize and become more complex, selective soldering offers the precision and flexibility needed to meet the demands of modern PCB designs.
By understanding the unique features, benefits, and drawbacks of each soldering method, you can make an informed decision that balances your production goals, product quality, and financial constraints. Whether you opt for the tried-and-true wave soldering or the advanced capabilities of selective soldering, the key is to work with an experienced PCB assembly partner who can guide you through the process and ensure the best possible outcome for your project.
0 Comments