Introduction to RoHS 2 and Its Importance for PCB Manufacturing
The Restriction of Hazardous Substances Directive (RoHS) is a European Union directive that restricts the use of certain hazardous substances in electrical and electronic equipment (EEE). The original RoHS directive, also known as RoHS 1, was implemented in 2006 and restricted the use of six hazardous materials: lead (Pb), mercury (Hg), cadmium (Cd), hexavalent chromium (Cr6+), polybrominated biphenyls (PBB), and polybrominated diphenyl ether (PBDE).
In 2011, the European Union updated the directive to RoHS 2 (2011/65/EU), which expanded the scope of the original directive and added new substance restrictions. The aim of RoHS 2 is to reduce the environmental impact of EEE and promote the development of eco-friendly alternatives.
For printed circuit board (PCB) manufacturers, producing RoHS 2 compliant products is crucial to meet the legal requirements and maintain market access in the European Union and other countries that have adopted similar regulations. This article will provide a comprehensive guide on how to produce RoHS 2 compliant PCB products.
Understanding the Requirements of RoHS 2 for PCB Manufacturing
To produce RoHS 2 compliant PCBs, manufacturers must adhere to the following requirements:
- Restricted substances and their maximum concentration values (MCVs):
Substance | Maximum Concentration Value (MCV) |
---|---|
Lead (Pb) | 0.1% by weight |
Mercury (Hg) | 0.1% by weight |
Cadmium (Cd) | 0.01% by weight |
Hexavalent Chromium (Cr6+) | 0.1% by weight |
Polybrominated Biphenyls (PBB) | 0.1% by weight |
Polybrominated Diphenyl Ether (PBDE) | 0.1% by weight |
Bis(2-Ethylhexyl) phthalate (DEHP) | 0.1% by weight |
Butyl benzyl phthalate (BBP) | 0.1% by weight |
Dibutyl phthalate (DBP) | 0.1% by weight |
Diisobutyl phthalate (DIBP) | 0.1% by weight |
-
Exemptions: RoHS 2 provides exemptions for certain applications where the use of restricted substances is essential and no suitable alternatives are available. PCB Manufacturers must ensure that any exemptions claimed are valid and properly documented.
-
Due diligence and documentation: PCB manufacturers must exercise due diligence to ensure that their products comply with RoHS 2 requirements. This includes obtaining declarations of conformity and technical documentation from suppliers, conducting risk assessments, and maintaining records to demonstrate compliance.
Strategies for Producing RoHS 2 Compliant PCBs
To produce RoHS 2 compliant PCBs, manufacturers can implement the following strategies:
1. Material Selection and Sourcing
Selecting RoHS 2 compliant materials is the first step in producing compliant PCBs. This involves:
- Using lead-free solder and surface finishes
- Choosing RoHS 2 compliant laminates, such as halogen-free or low-halogen materials
- Sourcing components and materials from reliable suppliers who provide RoHS 2 compliance documentation
2. Process Control and Optimization
Manufacturers must optimize their production processes to minimize the risk of contamination and ensure consistent RoHS 2 compliance. This includes:
- Implementing lead-free soldering processes and controlling process parameters (e.g., temperature, time, and flux selection)
- Segregating RoHS 2 compliant and non-compliant materials to prevent cross-contamination
- Regularly monitoring and maintaining production equipment to ensure proper functionality and minimize the risk of contamination
3. Testing and Verification
To verify RoHS 2 compliance, PCB manufacturers can employ various testing methods:
- X-ray fluorescence (XRF) spectrometry: A non-destructive technique that can quickly analyze the elemental composition of materials and identify the presence of restricted substances
- Inductively coupled plasma (ICP) spectrometry: A more accurate but destructive method that involves dissolving the sample in an acid solution and analyzing the elemental composition
- Supplier declarations and certifications: Obtaining and verifying compliance documentation from suppliers to ensure the materials used in PCB production are RoHS 2 compliant
4. Documentation and Traceability
Maintaining proper documentation and traceability is essential for demonstrating RoHS 2 compliance. PCB manufacturers should:
- Keep records of material sourcing, testing results, and supplier declarations
- Implement a traceability system to track materials and components throughout the production process
- Provide RoHS 2 compliance documentation to customers upon request
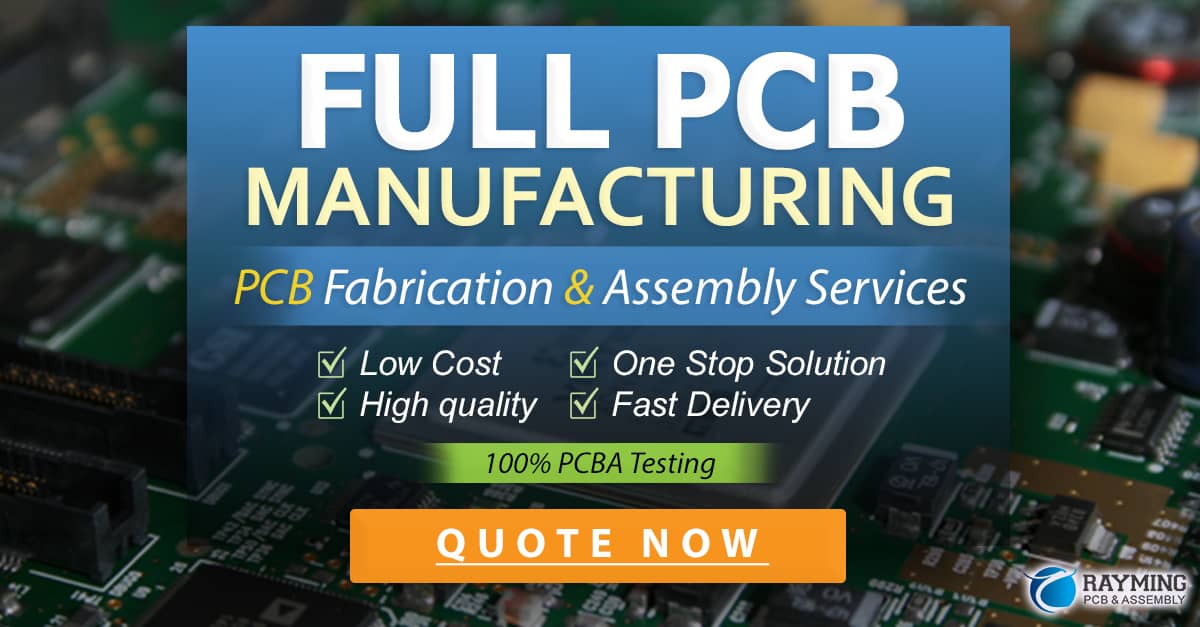
Challenges and Best Practices in Implementing RoHS 2 Compliance
Implementing RoHS 2 compliance in PCB manufacturing can present several challenges:
-
Ensuring supplier compliance: PCB manufacturers must rely on their suppliers to provide RoHS 2 compliant materials and accurate documentation. Establishing strong supplier relationships and conducting regular audits can help mitigate this challenge.
-
Managing exemptions: Keeping track of the various exemptions and their expiration dates can be complex. PCB manufacturers should regularly review and update their exemption management processes to ensure ongoing compliance.
-
Balancing performance and compliance: Some RoHS 2 compliant materials may have different performance characteristics compared to their non-compliant counterparts. PCB manufacturers must work closely with their customers to select suitable materials that meet both performance and compliance requirements.
Best practices for overcoming these challenges include:
- Developing a comprehensive RoHS 2 compliance policy and training employees on its implementation
- Collaborating with customers and suppliers to identify and address compliance challenges proactively
- Continuously monitoring regulatory updates and adapting compliance strategies accordingly
- Investing in advanced testing equipment and data management systems to streamline compliance processes
Frequently Asked Questions (FAQ)
- What is the difference between RoHS 1 and RoHS 2?
-
RoHS 1 (2002/95/EC) restricted the use of six hazardous substances in EEE. RoHS 2 (2011/65/EU) expanded the scope of the directive, added four new substance restrictions (phthalates), and introduced new requirements for due diligence and documentation.
-
Are all PCBs required to be RoHS 2 compliant?
-
Not all PCBs are required to be RoHS 2 compliant. The directive applies to EEE placed on the market in the European Union. However, many countries have adopted similar regulations, and some customers may require RoHS 2 compliance even if not legally mandated.
-
How can PCB manufacturers ensure their suppliers provide RoHS 2 compliant materials?
-
PCB manufacturers should establish strong relationships with their suppliers, communicate their compliance requirements clearly, and conduct regular audits to verify supplier compliance. Obtaining and verifying supplier declarations and certifications is also essential.
-
What are the consequences of non-compliance with RoHS 2?
-
Non-compliance with RoHS 2 can result in legal penalties, product recalls, and damage to a company’s reputation. In the European Union, non-compliant products may be prohibited from being placed on the market or face fines.
-
How often should PCB manufacturers review and update their RoHS 2 compliance strategies?
- PCB manufacturers should regularly review and update their RoHS 2 compliance strategies to ensure they remain current with regulatory changes and industry best practices. An annual review is generally recommended, but more frequent updates may be necessary if significant changes occur in regulations or supply chain.
Conclusion
Producing RoHS 2 compliant PCBs is essential for manufacturers to meet legal requirements, maintain market access, and contribute to environmental sustainability. By understanding the requirements of RoHS 2, implementing effective compliance strategies, and staying informed about regulatory updates, PCB manufacturers can successfully navigate the challenges of RoHS 2 compliance and deliver high-quality, eco-friendly products to their customers.
As the global focus on environmental protection continues to grow, the importance of RoHS 2 compliance in PCB manufacturing will only increase. By proactively addressing compliance challenges and continuously improving their processes, PCB manufacturers can position themselves as leaders in the industry and contribute to a more sustainable future.
0 Comments