Introduction to Rogers PCB
Rogers PCB, also known as Rogers Printed Circuit Board, is a high-performance material used in the manufacturing of printed circuit boards (PCBs). These PCBs are designed to meet the demanding requirements of various industries, including telecommunications, aerospace, defense, and automotive. Rogers PCBs offer superior electrical properties, excellent thermal management, and high reliability compared to traditional FR-4 PCBs.
What is Rogers Material?
Rogers Corporation, founded in 1832, is a global leader in engineered materials solutions. They have developed a range of advanced materials for use in PCBs, including:
- Rogers RO4000 Series
- Rogers RO3000 Series
- Rogers RT/duroid Series
- Rogers CLTE Series
These materials exhibit exceptional properties, such as low dielectric constant, low dissipation factor, and high thermal conductivity, making them ideal for high-frequency applications.
Advantages of Rogers PCB
1. Low Dielectric Constant and Dissipation Factor
Rogers PCB materials have a low dielectric constant (Dk) and dissipation factor (Df), which are essential for high-frequency applications. A low Dk ensures faster signal propagation, while a low Df minimizes signal loss and heat generation. This results in improved signal integrity and reduced signal distortion.
2. High Thermal Conductivity
Rogers PCBs offer excellent thermal conductivity, which helps in efficiently dissipating heat generated by electronic components. This is particularly important in high-power applications where heat management is critical. The high thermal conductivity of Rogers PCBs prevents overheating and enhances the reliability and longevity of the electronic devices.
3. Dimensional Stability
Rogers materials maintain their dimensional stability over a wide temperature range. This is crucial for applications that are exposed to extreme temperature variations, such as aerospace and defense systems. The dimensional stability of Rogers PCBs ensures consistent performance and minimizes the risk of failure due to thermal stress.
4. High Frequency Performance
Rogers PCBs are designed to excel in high-frequency applications, such as 5G networks, radar systems, and satellite communications. The low dielectric constant and dissipation factor of Rogers materials enable faster signal propagation and reduced signal loss, making them ideal for high-frequency designs.
Applications of Rogers PCB
1. Telecommunications
Rogers PCBs are widely used in the telecommunications industry, especially in 5G infrastructure. The high-frequency performance and low signal loss of Rogers materials make them suitable for designing antennas, filters, and power amplifiers in 5G base stations and mobile devices.
2. Aerospace and Defense
In the aerospace and defense sectors, Rogers PCBs are employed in radar systems, satellite communications, and avionics. The dimensional stability and high reliability of Rogers materials ensure consistent performance in harsh environments and extreme temperature conditions.
3. Automotive
Rogers PCBs find applications in the automotive industry, particularly in advanced driver assistance systems (ADAS) and autonomous vehicles. The low dielectric constant and high thermal conductivity of Rogers materials enable the design of high-frequency radar sensors and vehicle-to-everything (V2X) communication modules.
4. Medical Devices
Rogers PCBs are used in various medical devices, such as MRI machines, wireless patient monitoring systems, and implantable devices. The low signal loss and high reliability of Rogers materials ensure accurate data transmission and patient safety.
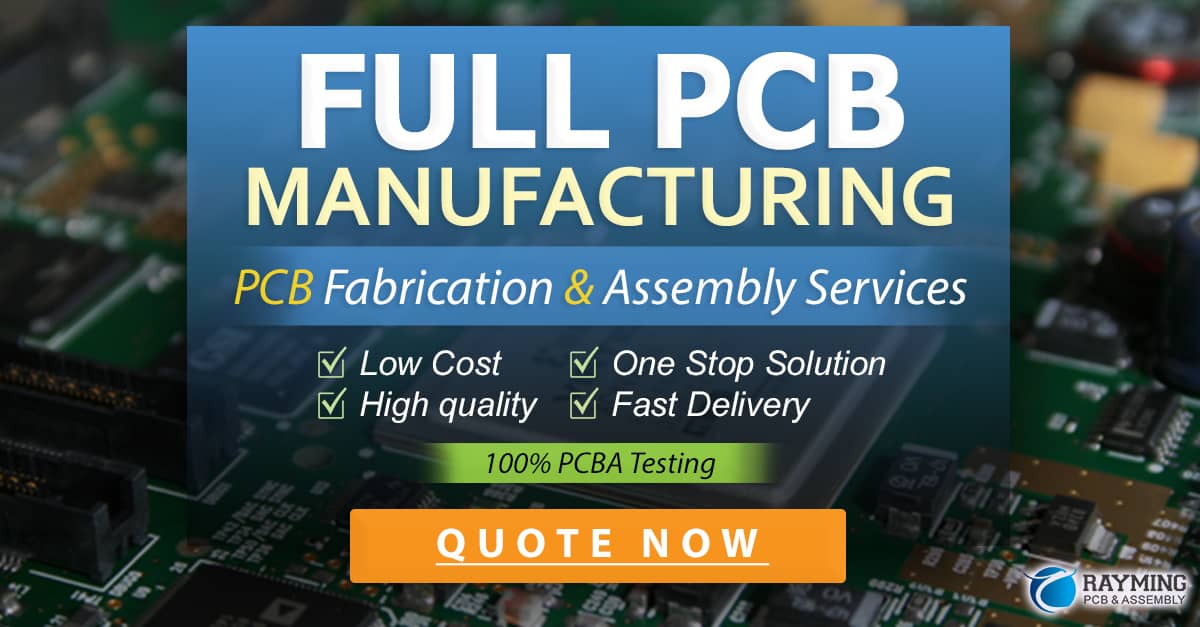
Choosing the Right Rogers PCB Material
When selecting a Rogers PCB material for your application, consider the following factors:
-
Dielectric Constant (Dk): Choose a material with a suitable Dk value based on your design requirements. Lower Dk values are preferred for high-frequency applications.
-
Dissipation Factor (Df): Opt for a material with a low Df to minimize signal loss and heat generation.
-
Thermal Conductivity: Consider the thermal management needs of your application and select a material with appropriate thermal conductivity.
-
Frequency Range: Ensure that the chosen Rogers material is suitable for the desired frequency range of your application.
-
Cost: Evaluate the cost implications of using Rogers PCBs compared to traditional FR-4 PCBs and assess the benefits in terms of performance and reliability.
Manufacturing Considerations for Rogers PCB
When manufacturing Rogers PCBs, there are several key considerations to keep in mind:
1. Controlled Impedance
Rogers PCBs often require controlled impedance design to ensure proper signal integrity. This involves precisely controlling the width and spacing of the traces to achieve the desired characteristic impedance. Manufacturers must have the expertise and equipment to handle controlled impedance requirements.
2. Lamination Process
The lamination process for Rogers PCBs is more complex compared to traditional FR-4 PCBs. Rogers materials require specific lamination parameters, such as pressure, temperature, and time, to ensure proper bonding and avoid delamination. Manufacturers must follow the recommended lamination guidelines provided by Rogers Corporation.
3. Drilling and Routing
Drilling and routing of Rogers PCBs demand special attention due to the unique properties of the materials. High-speed drilling and routing techniques are employed to minimize heat generation and prevent damage to the material. Proper tool selection and parameters are crucial for achieving clean and accurate holes and edges.
4. Surface Finish
The choice of surface finish for Rogers PCBs depends on the application requirements. Common surface finishes include ENIG (Electroless Nickel Immersion Gold), HASL (Hot Air Solder Leveling), and Immersion Silver. Each surface finish has its advantages and considerations in terms of solderability, durability, and cost.
Frequently Asked Questions (FAQ)
1. What are the main differences between Rogers PCBs and FR-4 PCBs?
Rogers PCBs offer superior electrical properties compared to FR-4 PCBs. They have a lower dielectric constant and dissipation factor, which results in faster signal propagation and reduced signal loss. Rogers PCBs also have higher thermal conductivity, enabling better heat dissipation. Additionally, Rogers materials maintain dimensional stability over a wide temperature range, making them suitable for applications exposed to extreme conditions.
2. Can Rogers PCBs be used for multilayer designs?
Yes, Rogers PCBs can be used for multilayer designs. Rogers Corporation offers a range of materials suitable for multilayer PCBs, such as the RO4000 series and the RO3000 series. These materials can be laminated together to create complex multilayer structures while maintaining the desired electrical and thermal properties.
3. Are Rogers PCBs more expensive than traditional FR-4 PCBs?
Yes, Rogers PCBs are generally more expensive than FR-4 PCBs due to the advanced materials and specialized manufacturing processes involved. However, the higher cost is justified by the superior performance, reliability, and longevity offered by Rogers PCBs in demanding applications. The cost-benefit analysis should consider the specific requirements and long-term benefits of using Rogers PCBs in a given application.
4. How do I select the appropriate Rogers PCB material for my application?
To select the appropriate Rogers PCB material, consider factors such as the desired dielectric constant, dissipation factor, thermal conductivity, and frequency range of your application. Consult the datasheet provided by Rogers Corporation for each material to determine its suitability for your specific requirements. It is also advisable to discuss your application needs with a Rogers PCB manufacturer or a technical expert to ensure the optimal material selection.
5. What are the challenges in manufacturing Rogers PCBs?
Manufacturing Rogers PCBs presents several challenges compared to traditional FR-4 PCBs. Controlled impedance design, complex lamination processes, specialized drilling and routing techniques, and Surface Finish Selection are some of the key considerations. Manufacturers must have the necessary expertise, equipment, and processes in place to handle Rogers materials effectively and ensure the desired performance and reliability of the final product.
Conclusion
Rogers PCBs offer a range of advanced materials that excel in high-frequency, high-reliability applications across various industries. With their low dielectric constant, low dissipation factor, high thermal conductivity, and dimensional stability, Rogers PCBs enable the design of high-performance electronic systems. When selecting a Rogers PCB material and manufacturing partner, it is essential to consider the specific application requirements, material properties, and manufacturing capabilities to ensure the optimal outcome. By leveraging the benefits of Rogers PCBs, designers can push the boundaries of performance and reliability in demanding applications such as telecommunications, aerospace, defense, automotive, and medical devices.
Property | Rogers PCB | FR-4 PCB |
---|---|---|
Dielectric Constant (Dk) | Low (2.2-4.5) | Higher (4.4) |
Dissipation Factor (Df) | Low (<0.005) | Higher (0.02) |
Thermal Conductivity | High | Lower |
Dimensional Stability | High | Lower |
High-Frequency Performance | Excellent | Good |
Cost | Higher | Lower |
0 Comments