Introduction to Rigid-Flex PCBs
Rigid-Flex PCBs are a unique type of printed circuit board that combines the benefits of both rigid and flexible PCBs. These boards consist of multiple layers of flexible and rigid substrates that are laminated together to form a single circuit board. The flexible portions of the board allow for bending and folding, while the rigid portions provide structural support and stability.
Rigid-flex PCBs offer several advantages over traditional rigid PCBs, including:
- Reduced weight and size
- Improved reliability and durability
- Increased design flexibility
- Reduced assembly time and cost
Applications of Rigid-flex PCBs
Rigid-flex PCBs are used in a wide range of applications, including:
- Medical devices
- Aerospace and defense systems
- Automotive electronics
- Consumer electronics
- Industrial automation
Choosing the Right Rigid-flex PCB Manufacturer
When it comes to choosing a rigid-flex PCB manufacturer, there are several factors to consider. Here are some key considerations:
Experience and Expertise
Look for a manufacturer with extensive experience in designing and fabricating rigid-flex PCBs. They should have a proven track record of delivering high-quality boards for a variety of applications.
Quality Control
Choose a manufacturer that has strict quality control measures in place to ensure that every board meets or exceeds industry standards. They should use state-of-the-art equipment and follow best practices for PCB manufacturing.
Technical Support
Look for a manufacturer that offers comprehensive technical support throughout the design and manufacturing process. They should be able to provide guidance on material selection, design optimization, and testing procedures.
Certifications
Choose a manufacturer that holds relevant industry certifications, such as ISO 9001, UL, and RoHS. These certifications demonstrate a commitment to quality and compliance with industry standards.
Pricing
While price should not be the sole deciding factor, it is important to choose a manufacturer that offers competitive pricing without compromising on quality. Look for a manufacturer that provides transparent pricing and can work within your budget constraints.
Top Rigid-flex PCB Manufacturers
Here are some of the top rigid-flex PCB manufacturers in the industry:
1. TTM Technologies
TTM Technologies is a leading global manufacturer of PCBs, including rigid-flex boards. With over 25 years of experience, they have a proven track record of delivering high-quality boards for a variety of applications.
2. Flex PCB
Flex PCB is a specialized manufacturer of flexible and rigid-flex PCBs. They offer a wide range of services, including design, prototyping, and volume production.
3. Printed Circuits
Printed Circuits is a full-service PCB manufacturer that specializes in rigid-flex boards. They have over 40 years of experience and offer a range of services, including design, fabrication, and assembly.
4. Epec Engineered Technologies
Epec Engineered Technologies is a global provider of PCBs, including rigid-flex boards. They offer a range of services, including design, prototyping, and volume production.
5. Cirexx International
Cirexx International is a leading manufacturer of rigid-flex PCBs. They offer a range of services, including design, fabrication, and assembly, and have a proven track record of delivering high-quality boards for a variety of applications.
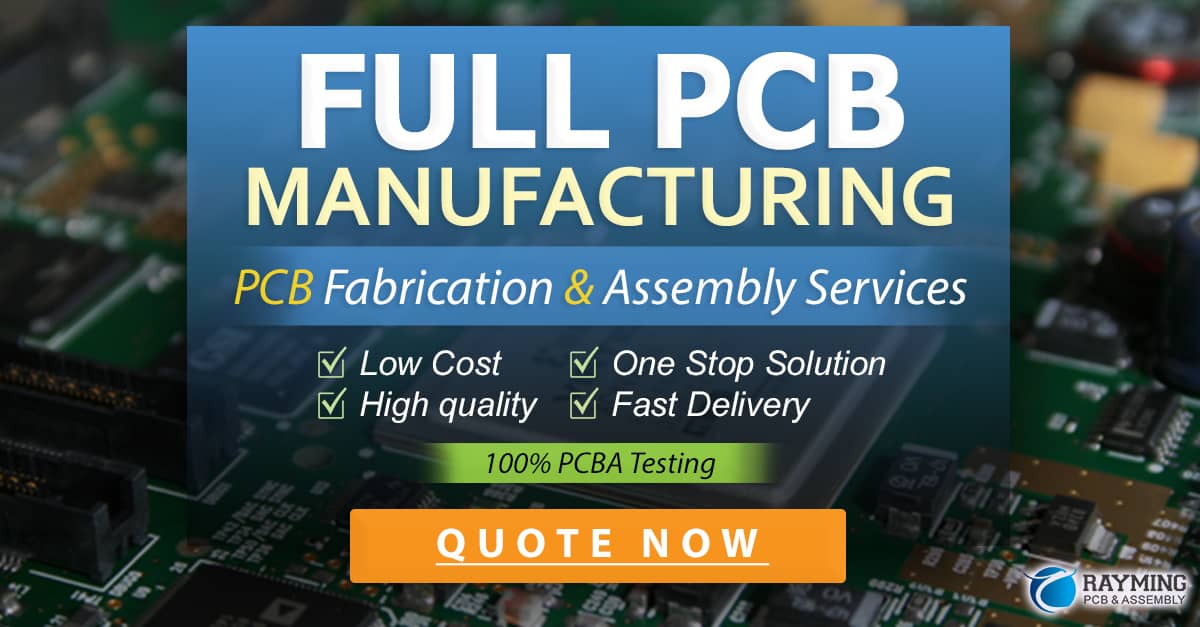
Designing Rigid-flex PCBs
Designing rigid-flex PCBs requires a different approach than designing traditional rigid PCBs. Here are some key considerations:
Material Selection
Choosing the right materials is critical for ensuring the performance and reliability of rigid-flex PCBs. Common materials include polyimide, polyester, and FR-4.
Bend Radius
The bend radius is the minimum radius that a flexible portion of the board can be bent without causing damage. It is important to design the board with the appropriate bend radius to ensure reliability and durability.
Stiffener Placement
Stiffeners are used to provide support and stability to the flexible portions of the board. It is important to place stiffeners in the appropriate locations to ensure the board remains flat and stable during use.
Coverlay
Coverlay is a protective layer that is applied to the flexible portions of the board to provide insulation and protection against damage. It is important to choose the appropriate coverlay material and thickness for the application.
Via Placement
Vias are used to connect different layers of the board. In rigid-flex PCBs, it is important to place vias in the appropriate locations to ensure reliable connections between the flexible and rigid portions of the board.
Manufacturing Rigid-flex PCBs
Manufacturing rigid-flex PCBs requires specialized equipment and processes. Here are some key steps in the manufacturing process:
Lamination
The flexible and rigid substrates are laminated together using heat and pressure to form a single circuit board.
Drilling
Holes are drilled through the board to accommodate components and vias.
Plating
The holes are plated with copper to provide electrical connectivity between the layers of the board.
Patterning
The copper layers are patterned using photolithography to create the desired circuit pattern.
Solder Mask
A solder mask is applied to the board to protect the copper traces and prevent short circuits.
Surface Finish
A surface finish, such as ENIG or OSP, is applied to the board to protect the copper traces and improve solderability.
Testing Rigid-flex PCBs
Testing is a critical step in the manufacturing process to ensure that the board meets the required specifications and performs as expected. Here are some common testing methods:
Continuity Testing
Continuity testing is used to verify that all the connections on the board are intact and that there are no open circuits.
Resistance Testing
Resistance testing is used to measure the resistance of the copper traces and ensure that they meet the required specifications.
Isolation Testing
Isolation testing is used to ensure that there are no short circuits between adjacent traces or layers of the board.
Functional Testing
Functional testing is used to verify that the board performs as expected under real-world conditions.
Advantages of Rigid-flex PCBs
Rigid-flex PCBs offer several advantages over traditional rigid PCBs, including:
Reduced Weight and Size
Rigid-flex PCBs can be designed to be thinner and lighter than traditional rigid PCBs, making them ideal for applications where weight and size are critical factors.
Improved Reliability and Durability
The flexible portions of rigid-flex PCBs allow for bending and folding without causing damage to the board, improving reliability and durability.
Increased Design Flexibility
Rigid-flex PCBs allow for greater design flexibility, enabling designers to create boards that can fit into tight spaces or conform to complex shapes.
Reduced Assembly Time and Cost
Rigid-flex PCBs can reduce assembly time and cost by eliminating the need for connectors and cables between different parts of the board.
Disadvantages of Rigid-flex PCBs
While rigid-flex PCBs offer many advantages, there are also some disadvantages to consider:
Higher Cost
Rigid-flex PCBs are typically more expensive than traditional rigid PCBs due to the specialized materials and manufacturing processes required.
Longer Lead Times
The manufacturing process for rigid-flex PCBs is more complex than for traditional rigid PCBs, which can result in longer lead times.
Limited Supplier Options
Not all PCB manufacturers have the capabilities to produce rigid-flex PCBs, which can limit supplier options and increase costs.
FAQs
Q1: What is a rigid-flex PCB?
A: A rigid-flex PCB is a type of printed circuit board that combines the benefits of both rigid and flexible PCBs. It consists of multiple layers of flexible and rigid substrates that are laminated together to form a single circuit board.
Q2: What are the advantages of using rigid-flex PCBs?
A: Rigid-flex PCBs offer several advantages, including reduced weight and size, improved reliability and durability, increased design flexibility, and reduced assembly time and cost.
Q3: What are some common applications for rigid-flex PCBs?
A: Rigid-flex PCBs are used in a wide range of applications, including medical devices, aerospace and defense systems, automotive electronics, consumer electronics, and industrial automation.
Q4: How do I choose the right rigid-flex PCB manufacturer?
A: When choosing a rigid-flex PCB manufacturer, consider factors such as experience and expertise, quality control, technical support, certifications, and pricing.
Q5: What are some common testing methods for rigid-flex PCBs?
A: Common testing methods for rigid-flex PCBs include continuity testing, resistance testing, isolation testing, and functional testing.
Conclusion
Rigid-flex PCBs offer a unique combination of flexibility and rigidity that makes them ideal for a wide range of applications. When choosing a rigid-flex PCB manufacturer, it is important to consider factors such as experience, quality control, technical support, certifications, and pricing.
By working with a reputable manufacturer and following best practices for design and manufacturing, you can ensure that your rigid-flex PCBs meet the required specifications and perform as expected. With their many advantages, rigid-flex PCBs are a valuable tool for designers and engineers looking to create innovative and reliable electronic products.
0 Comments