Types of Reflow Soldering Equipment
There are several types of reflow soldering equipment available in the market, each designed for specific applications and production volumes. The most common types include:
Convection Reflow Ovens
Convection reflow ovens are the most widely used type of reflow soldering equipment. They use forced air convection to heat the PCB and components, allowing for even heat distribution and consistent solder joint formation. These ovens are available in various sizes and configurations, ranging from small benchtop units to large, in-line systems for high-volume production.
Key features of convection reflow ovens include:
– Precise temperature control
– Multiple heating zones for optimal temperature profiling
– Adjustable conveyor speed for various PCB sizes and component densities
– Nitrogen atmosphere compatibility for improved solder joint quality
Infrared (IR) Reflow Ovens
Infrared reflow ovens use radiant heat from IR emitters to heat the PCB and components. This method allows for faster heating and cooling rates compared to convection ovens, making them suitable for applications requiring shorter cycle times. However, IR ovens may not provide as even heat distribution as convection ovens, which can lead to potential issues with larger or more complex PCBs.
Key features of IR reflow ovens include:
– Fast heating and cooling rates
– Compact design for smaller footprint
– Energy efficiency due to targeted heating
– Compatibility with various solder paste types
Vapor Phase Reflow Ovens
Vapor phase reflow ovens use a heated, inert fluid (typically a perfluoropolyether) to transfer heat to the PCB and components. The fluid vaporizes at a specific temperature, creating a saturated vapor that condenses on the PCB surface, providing a highly uniform and efficient heat transfer. This method eliminates the risk of overheating and ensures consistent solder joint quality, even for complex and high-density PCBs.
Key features of vapor phase reflow ovens include:
– Uniform heat transfer for consistent solder joint quality
– Minimal risk of overheating or damaging components
– Compatibility with lead-free and high-temperature solder alloys
– Reduced energy consumption compared to convection ovens
Factors to Consider When Choosing Reflow Soldering Equipment
When selecting reflow soldering equipment for your manufacturing process, consider the following factors:
- Production volume and throughput requirements
- PCB size and component density
- Solder paste type and alloy compatibility
- Temperature profiling capabilities
- Atmosphere control (air or nitrogen)
- Footprint and facility constraints
- Budget and total cost of ownership
Reflow Soldering Process Overview
The reflow soldering process consists of several key stages:
- Solder paste application: Solder paste is applied to the PCB pads using a stencil or screen printing process.
- Component placement: Surface mount components are placed onto the solder paste using pick-and-place machines or manual assembly methods.
- Preheating: The PCB is gradually heated to activate the solder paste flux and evaporate any solvents.
- Reflow: The PCB is heated to the solder alloy’s melting point, allowing the solder to flow and form a strong bond between the components and the board.
- Cooling: The PCB is cooled to solidify the solder joints, ensuring a strong and reliable connection.
Reflow Soldering Temperature Profile
A crucial aspect of the reflow soldering process is the temperature profile, which defines the heating and cooling rates, as well as the time spent at each stage. A typical reflow soldering temperature profile consists of four main stages:
- Preheat: The PCB is gradually heated to activate the flux and evaporate solvents. Typical preheat temperatures range from 150°C to 180°C, with a ramp rate of 1-3°C/second.
- Thermal soak: The PCB is held at a stable temperature (typically 150°C to 180°C) for 60-120 seconds to ensure even heat distribution and flux activation.
- Reflow: The PCB is heated to the solder alloy’s melting point (typically 220°C to 250°C for lead-free alloys) for 30-90 seconds to allow the solder to flow and form a strong bond.
- Cooling: The PCB is cooled at a controlled rate (typically 1-6°C/second) to solidify the solder joints and prevent thermal shock to the components.
The table below summarizes a typical lead-free reflow soldering temperature profile:
Stage | Temperature Range | Duration | Ramp Rate |
---|---|---|---|
Preheat | 150°C – 180°C | 60-120 sec | 1-3°C/sec |
Thermal Soak | 150°C – 180°C | 60-120 sec | 0-1°C/sec |
Reflow | 220°C – 250°C | 30-90 sec | 1-3°C/sec |
Cooling | 250°C – 25°C | 60-180 sec | 1-6°C/sec |
It’s essential to optimize the reflow soldering temperature profile for your specific PCB design, components, and solder paste to ensure high-quality solder joints and minimize the risk of defects.
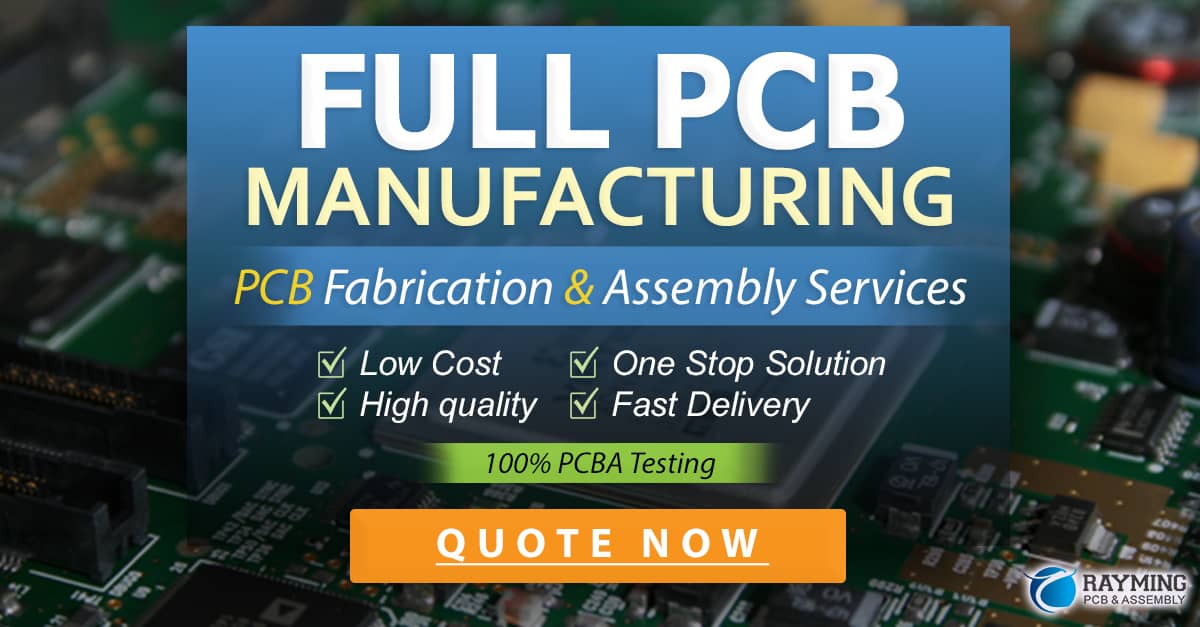
Reflow Soldering Defects and Troubleshooting
Despite the many advantages of reflow soldering, various defects can occur during the process. Some common reflow soldering defects include:
- Bridging: Solder bridging occurs when excess solder connects adjacent pads or components, creating a short circuit.
- Tombstoning: Also known as the “Manhattan effect,” tombstoning happens when a component stands up on one end due to uneven heating or solder paste application.
- Voiding: Solder voids are trapped pockets of gas within the solder joint, which can weaken the connection and reduce reliability.
- Insufficient wetting: Insufficient wetting occurs when the solder does not flow properly onto the component leads or PCB pads, resulting in a weak or incomplete bond.
- Overheating: Excessive temperatures during reflow can damage components or cause solder to oxidize, leading to poor joint quality.
To minimize the occurrence of these defects, consider the following troubleshooting tips:
- Ensure proper solder paste application and stencil design
- Optimize the reflow temperature profile for your specific PCB and components
- Use appropriate component placement and orientation techniques
- Maintain a clean and controlled environment to prevent contamination
- Regularly calibrate and maintain your reflow soldering equipment
Reflow Soldering Equipment Maintenance and Calibration
To ensure consistent performance and high-quality solder joints, it’s crucial to maintain and calibrate your reflow soldering equipment regularly. Some key maintenance and calibration tasks include:
- Cleaning: Regularly clean the oven chamber, conveyor, and sensors to prevent contamination and ensure accurate temperature readings.
- Temperature calibration: Use a calibrated temperature profiling system to verify and adjust the oven’s temperature settings, ensuring accurate and repeatable profiles.
- Conveyor maintenance: Inspect and lubricate the conveyor system to prevent jamming or uneven PCB transport.
- Heating element replacement: Replace worn or damaged heating elements to maintain consistent heating performance.
- Software updates: Keep your oven’s control software up to date to ensure optimal performance and compatibility with the latest process requirements.
By following a regular maintenance and calibration schedule, you can extend the life of your reflow soldering equipment and ensure consistent, high-quality solder joints.
Frequently Asked Questions (FAQ)
- What is the difference between convection and infrared reflow soldering?
-
Convection reflow soldering uses forced air to heat the PCB and components, providing even heat distribution. Infrared reflow soldering uses radiant heat from IR emitters, allowing for faster heating and cooling rates but potentially less even heat distribution.
-
Can I use the same reflow temperature profile for all PCBs and components?
-
No, it’s essential to optimize the reflow temperature profile for your specific PCB design, components, and solder paste. Different PCBs and components may have varying thermal requirements, and using an inappropriate profile can lead to defects or component damage.
-
How often should I calibrate my reflow soldering equipment?
-
The frequency of calibration depends on factors such as usage, environment, and manufacturer recommendations. As a general guideline, it’s a good practice to calibrate your reflow soldering equipment at least once every six months or as needed based on quality control data.
-
What are the benefits of using nitrogen in the reflow soldering process?
-
Using nitrogen in the reflow soldering process can help reduce oxidation, improve solder joint quality, and increase the shelf life of the solder paste. Nitrogen also helps to minimize solder balling and bridging defects.
-
How can I optimize my reflow soldering process to minimize defects?
- To minimize defects in your reflow soldering process, ensure proper solder paste application, optimize the temperature profile, use appropriate component placement techniques, maintain a clean environment, and regularly calibrate and maintain your equipment. Additionally, consider using solder paste inspection (SPI) and automated optical inspection (AOI) systems to detect and correct defects early in the process.
In conclusion, reflow soldering equipment plays a critical role in the manufacturing of high-quality electronic devices and components. By understanding the various types of equipment, their features, and the factors to consider when choosing the right solution for your production needs, you can optimize your reflow soldering process and ensure consistent, reliable solder joints. Regular maintenance, calibration, and process optimization are essential for minimizing defects and maximizing the performance of your reflow soldering equipment.
0 Comments