Introduction to Solder Mask Breakoff
Solder mask, also known as solder resist or solder stop, is a thin layer of polymer applied to the surface of a printed circuit board (PCB) to protect the copper traces from oxidation and prevent solder bridges from forming during the soldering process. The solder mask also provides electrical insulation and helps to improve the reliability and durability of the PCB.
However, solder mask bridges can sometimes break off, causing various issues such as short circuits, reduced electrical insulation, and decreased reliability of the PCB. In this article, we will explore the reasons behind solder mask bridge breakoff and discuss ways to prevent it.
What is a Solder Mask Bridge?
A solder mask bridge is a thin strip of solder mask that spans across two or more copper pads or traces on a PCB. The purpose of the solder mask bridge is to prevent solder from flowing between the pads or traces during the soldering process, which could cause short circuits or other issues.
Why is Solder Mask Bridge Integrity Important?
The integrity of the solder mask bridge is crucial for several reasons:
-
Electrical Insulation: The solder mask bridge provides electrical insulation between the copper pads or traces, preventing short circuits and ensuring proper functioning of the PCB.
-
Solder Control: The solder mask bridge helps to control the flow of solder during the soldering process, preventing solder bridges from forming between adjacent pads or traces.
-
Reliability: A well-formed and intact solder mask bridge contributes to the overall reliability and durability of the PCB.
Causes of Solder Mask Bridge Breakoff
There are several factors that can contribute to the breakoff of solder mask bridges. Let’s explore some of the most common causes:
Mechanical Stress
Mechanical stress is one of the primary reasons for solder mask bridge breakoff. This stress can be caused by various factors, such as:
-
Handling: Improper handling of the PCB during manufacturing, assembly, or transportation can lead to mechanical stress on the solder mask bridges, causing them to break off.
-
Vibration: Exposure to excessive vibration can cause the solder mask bridges to crack or break off, especially if the PCB is not properly supported or secured.
-
Thermal Expansion: Differences in the thermal expansion coefficients of the PCB substrate, copper traces, and solder mask can lead to mechanical stress on the solder mask bridges during temperature changes.
Insufficient Solder Mask Adhesion
Poor adhesion between the solder mask and the PCB substrate can also contribute to solder mask bridge breakoff. Factors that can affect solder mask adhesion include:
-
Surface Contamination: Contaminants such as dust, dirt, or oils on the PCB surface can prevent the solder mask from properly adhering to the substrate.
-
Inadequate Surface Preparation: Improper cleaning or lack of surface roughening before applying the solder mask can result in poor adhesion.
-
Incompatible Materials: Using incompatible solder mask materials or not following the manufacturer’s recommended application process can lead to adhesion issues.
Solder Mask Material Defects
Defects in the solder mask material itself can also contribute to bridge breakoff. These defects may include:
-
Voids or Bubbles: The presence of voids or bubbles in the solder mask can weaken the bridge and make it more susceptible to breakoff.
-
Incorrect Curing: Improper curing of the solder mask, such as insufficient curing time or incorrect curing temperature, can result in a weakened or brittle solder mask bridge.
-
Contamination: Contaminants in the solder mask material, such as particles or foreign substances, can compromise the integrity of the solder mask bridge.
PCB Design Issues
Certain aspects of the PCB design can also contribute to solder mask bridge breakoff:
-
Insufficient Solder Mask Thickness: If the solder mask is too thin, it may not provide adequate strength to withstand mechanical stress or protect the underlying copper traces.
-
Improper Pad or Trace Spacing: Inadequate spacing between copper pads or traces can make it difficult for the solder mask to form a strong bridge, increasing the risk of breakoff.
-
Sharp Corners or Edges: Sharp corners or edges on the copper pads or traces can create stress concentrations that make the solder mask bridge more susceptible to cracking or breaking.
Prevention of Solder Mask Bridge Breakoff
To minimize the occurrence of solder mask bridge breakoff, several preventive measures can be taken:
Proper Handling and Storage
-
Handling Guidelines: Establish and follow proper handling guidelines for PCBs during manufacturing, assembly, and transportation to minimize mechanical stress on the solder mask bridges.
-
Packaging: Use appropriate packaging materials and methods to protect the PCBs from damage during storage and transportation.
-
Environmental Control: Store PCBs in a controlled environment with stable temperature and humidity levels to reduce the risk of thermal stress and moisture-related issues.
Improved Solder Mask Adhesion
-
Surface Preparation: Ensure that the PCB surface is thoroughly cleaned and properly prepared before applying the solder mask to improve adhesion.
-
Material Selection: Choose solder mask materials that are compatible with the PCB substrate and have good adhesion properties.
-
Application Process: Follow the manufacturer’s recommended application process, including curing times and temperatures, to achieve optimal adhesion.
Enhanced Solder Mask Material Quality
-
Material Selection: Select high-quality solder mask materials from reputable suppliers to minimize the risk of defects or contamination.
-
Quality Control: Implement strict quality control measures to identify and reject solder mask materials with defects or inconsistencies.
-
Proper Storage: Store solder mask materials according to the manufacturer’s recommendations to maintain their quality and performance.
Optimized PCB Design
-
Solder Mask Thickness: Ensure that the solder mask is applied at an appropriate thickness to provide adequate strength and protection.
-
Pad and Trace Spacing: Design the PCB with sufficient spacing between copper pads and traces to allow for a strong and stable solder mask bridge.
-
Smooth Corners and Edges: Avoid sharp corners and edges on copper pads and traces to reduce stress concentrations and minimize the risk of solder mask bridge breakoff.
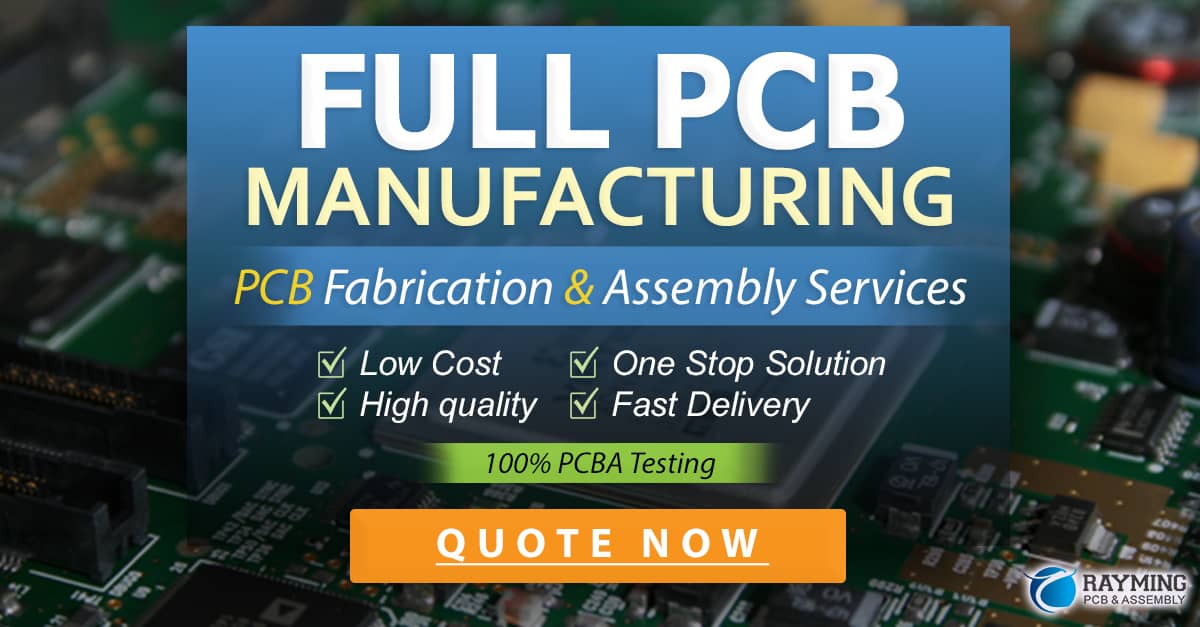
FAQs
-
What is a solder mask bridge?
A solder mask bridge is a thin strip of solder mask that spans across two or more copper pads or traces on a PCB to prevent solder from flowing between them during the soldering process. -
Why is solder mask bridge integrity important?
Solder mask bridge integrity is crucial for providing electrical insulation, controlling solder flow, and ensuring the reliability and durability of the PCB. -
What are the main causes of solder mask bridge breakoff?
The main causes of solder mask bridge breakoff include mechanical stress, insufficient solder mask adhesion, solder mask material defects, and PCB design issues. -
How can solder mask bridge breakoff be prevented?
Solder mask bridge breakoff can be prevented by proper handling and storage of PCBs, improving solder mask adhesion, enhancing solder mask material quality, and optimizing PCB design. -
What are the consequences of solder mask bridge breakoff?
The consequences of solder mask bridge breakoff can include short circuits, reduced electrical insulation, and decreased reliability of the PCB, potentially leading to performance issues or failures.
Conclusion
Solder mask bridge breakoff is a common issue that can have significant impacts on the performance and reliability of printed circuit boards. By understanding the causes of solder mask bridge breakoff, such as mechanical stress, insufficient adhesion, material defects, and PCB design issues, manufacturers can take proactive steps to prevent its occurrence.
Implementing proper handling and storage procedures, improving solder mask adhesion, ensuring high-quality solder mask materials, and optimizing PCB design are all effective strategies for minimizing the risk of solder mask bridge breakoff. By addressing these factors, manufacturers can produce PCBs with greater reliability, durability, and overall quality, ultimately leading to improved product performance and customer satisfaction.
0 Comments