Introduction to QFN Packaging
Quad Flat No-lead (QFN) packaging is a popular surface-mount technology (SMT) used in the electronics industry for its compact size, excellent thermal and electrical performance, and cost-effectiveness. QFN packages are leadless, meaning they do not have external leads extending from the package body. Instead, the electrical contacts are located on the bottom surface of the package, allowing for a smaller footprint and improved signal integrity.
QFN packages are widely used in various applications, including consumer electronics, automotive systems, industrial control, and telecommunications. They are particularly suitable for devices that require high-density interconnects, such as microcontrollers, sensors, power management ICs, and RF modules.
Types of QFN Packaging
There are several types of QFN packaging, each with unique features and benefits. Some of the most common types include:
Standard QFN (SQFN)
The Standard QFN (SQFN) is the most basic and widely used type of QFN packaging. It features a square or rectangular package body with a flat, exposed pad on the bottom surface for improved Thermal dissipation. The package size typically ranges from 2×2 mm to 12×12 mm, with a varying number of pins depending on the application requirements.
Dual-Row QFN (DRQFN)
Dual-Row QFN (DRQFN) packages have two rows of pins on the bottom surface, allowing for a higher pin count within a given package size. This type of QFN packaging is suitable for applications that require a large number of I/O connections, such as complex mixed-signal devices or high-speed communication ICs.
Thermally Enhanced QFN (TEQFN)
Thermally Enhanced QFN (TEQFN) packages are designed to improve heat dissipation and thermal performance. They feature a larger exposed pad on the bottom surface, which can be connected to the PCB’s ground plane or other heat-sinking structures. TEQFN packages are ideal for power-intensive applications, such as power management ICs or high-performance processors.
Wettable Flank QFN (WFQFN)
Wettable Flank QFN (WFQFN) packages have a unique feature that allows for improved solder joint inspection. The package’s side walls are partially plated with a wettable material, enabling solder to climb up the side of the package during the reflow process. This creates a visible solder fillet that can be easily inspected using automated optical inspection (AOI) systems, ensuring better manufacturing quality and reliability.
Punch-Type QFN (PQFN)
Punch-Type QFN (PQFN) packages are manufactured using a stamping process, which results in a more precise and consistent lead frame structure. This type of QFN packaging offers improved mechanical stability and better control over the package dimensions, making it suitable for applications that require tight tolerances or high reliability.
QFN Assembly Process
The assembly process for QFN packages involves several steps, including:
-
Solder Paste Printing: Solder paste is applied to the PCB’s contact pads using a stencil printing process. The stencil ensures that the correct amount of solder paste is deposited on each pad.
-
Component Placement: The QFN package is placed onto the PCB using a pick-and-place machine. The machine aligns the package with the contact pads and places it with high precision.
-
Reflow Soldering: The PCB with the placed QFN package is passed through a reflow oven, where the solder paste melts and forms a permanent connection between the package and the PCB. The reflow profile is carefully controlled to ensure optimal solder joint formation and to prevent thermal damage to the components.
-
Inspection: After the reflow process, the assembLED PCB undergoes inspection to verify the quality of the solder joints and the overall assembly. This can be done using various methods, such as automated optical inspection (AOI), X-ray inspection, or electrical testing.
QFN Assembly Challenges and Best Practices
While QFN packages offer numerous benefits, they also present some challenges during the assembly process. Some of these challenges include:
-
Solder Joint Voiding: QFN packages with large exposed pads are prone to solder joint voiding, which can affect the thermal and electrical performance of the device. To minimize voiding, it is essential to optimize the solder paste printing process, use an appropriate reflow profile, and consider using solder preforms or vacuum soldering techniques.
-
Package Warpage: QFN packages can experience warpage due to the mismatch in the Coefficient of Thermal Expansion (CTE) between the package and the PCB. Warpage can lead to poor solder joint formation or even package cracking. To mitigate this issue, it is crucial to select a compatible PCB material, use a symmetrical package design, and control the reflow profile to minimize thermal stress.
-
Tombstoning: Tombstoning, also known as the “Manhattan effect,” occurs when a QFN package stands up on one end during the reflow process. This is usually caused by an imbalance in the solder joint formation or uneven heating. To prevent tombstoning, ensure that the solder paste is evenly distributed, the package is correctly aligned, and the reflow profile is optimized.
To ensure successful QFN assembly, consider the following best practices:
- Use a stencil thickness that matches the package’s lead pitch and size to achieve the optimal solder paste volume.
- Ensure accurate component placement using a high-precision pick-and-place machine.
- Optimize the reflow profile based on the package’s thermal requirements and the PCB’s characteristics.
- Implement appropriate inspection methods to verify the quality of the solder joints and the overall assembly.
- Follow the package manufacturer’s guidelines for PCB design, land pattern dimensions, and assembly processes.
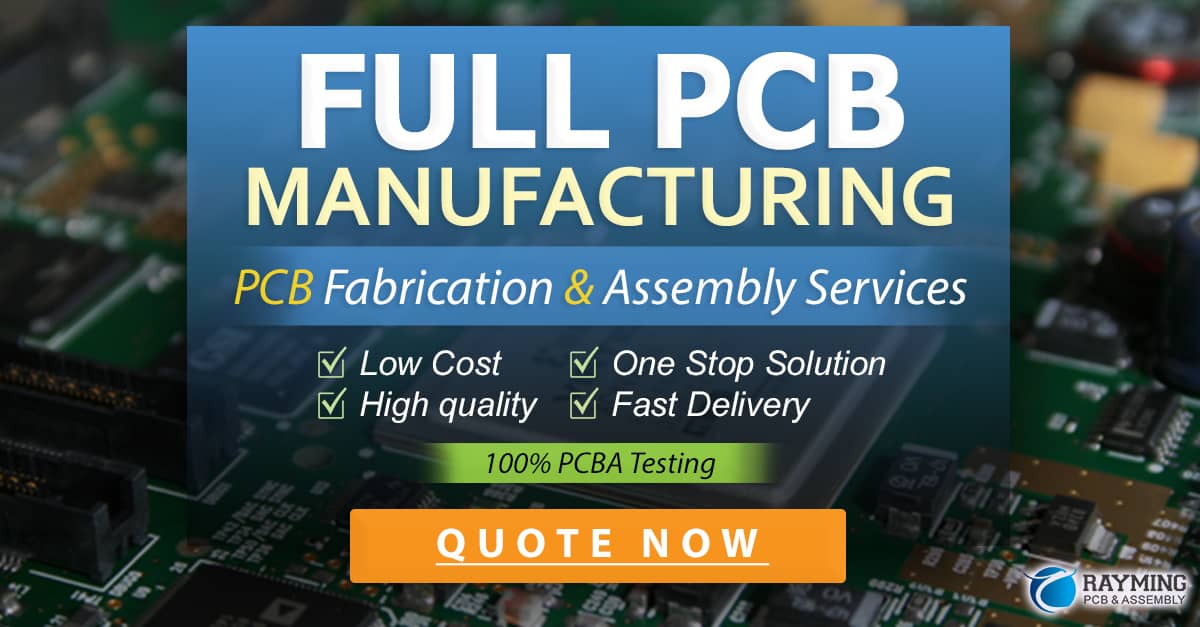
Benefits of QFN Packaging
QFN packaging offers several advantages over other SMT package types, making it an attractive choice for many applications. Some of the key benefits include:
Compact Size
QFN packages have a small footprint and low profile, enabling higher component density on PCBs. This makes them ideal for space-constrained applications, such as mobile devices, wearables, and IoT sensors.
Excellent Thermal Performance
The exposed pad on the bottom surface of QFN packages provides an efficient thermal path for heat dissipation. This helps to improve the device’s thermal performance, leading to better reliability and longer product life.
Superior Electrical Performance
QFN packages have short lead lengths and a low profile, which minimizes parasitic inductance and capacitance. This results in improved signal integrity, reduced electromagnetic interference (EMI), and better high-frequency performance.
Cost-Effectiveness
QFN packages are generally less expensive than other SMT package types due to their simple construction and efficient use of materials. Additionally, their compact size allows for smaller PCBs, further reducing the overall system cost.
Compatibility with High-Volume Manufacturing
QFN packages are well-suited for high-volume, automated manufacturing processes. They can be easily assembled using standard SMT equipment and processes, ensuring consistent quality and reliability.
FAQs
-
Q: What is the difference between QFN and QFP packages?
A: QFN (Quad Flat No-lead) packages have contacts on the bottom surface of the package, while QFP (Quad Flat Package) packages have leads extending from the sides of the package. QFN packages are typically smaller and have better thermal and electrical performance compared to QFP packages. -
Q: Can QFN packages be soldered using hand soldering techniques?
A: While it is possible to hand solder QFN packages, it is not recommended due to their small size and close lead pitch. QFN packages are designed for automated SMT Assembly processes, which ensure consistent and reliable solder joint formation. -
Q: How does the exposed pad on QFN packages improve thermal performance?
A: The exposed pad on the bottom surface of QFN packages acts as a thermal conductor, allowing heat to be efficiently transferred from the device to the PCB. This helps to dissipate heat more effectively, improving the device’s thermal performance and overall reliability. -
Q: What are the common challenges faced during QFN assembly, and how can they be addressed?
A: Common challenges in QFN assembly include solder joint voiding, package warpage, and tombstoning. These challenges can be addressed by optimizing the solder paste printing process, selecting compatible PCB materials, ensuring accurate component placement, and implementing an appropriate reflow profile. -
Q: Are QFN packages suitable for high-frequency applications?
A: Yes, QFN packages are well-suited for high-frequency applications due to their low profile and reduced parasitic inductance and capacitance. These characteristics help to maintain signal integrity and minimize electromagnetic interference (EMI), making QFN packages a popular choice for RF and high-speed communication devices.
Conclusion
QFN packaging has become increasingly popular in the electronics industry due to its numerous benefits, including compact size, excellent thermal and electrical performance, and cost-effectiveness. With various types of QFN packages available, designers can select the most suitable option based on their specific application requirements.
To ensure successful QFN assembly, it is essential to understand the challenges involved and follow best practices for solder paste printing, component placement, and reflow soldering. By optimizing the assembly process and implementing appropriate inspection methods, manufacturers can achieve high-quality, reliable QFN assemblies that meet the demands of today’s electronic devices.
As the electronics industry continues to evolve, QFN packaging is expected to play a crucial role in enabling the development of smaller, more efficient, and high-performance devices. By staying up-to-date with the latest advancements in QFN technology and assembly techniques, designers and manufacturers can leverage the full potential of this versatile packaging solution.
Type of QFN Packaging | Key Features | Typical Applications |
---|---|---|
Standard QFN (SQFN) | – Square or rectangular package body – Flat, exposed pad on the bottom surface – Package size: 2×2 mm to 12×12 mm |
– General-purpose ICs – Sensors – Power management devices |
Dual-Row QFN (DRQFN) | – Two rows of pins on the bottom surface – Higher pin count within a given package size |
– Complex mixed-signal devices – High-speed communication ICs |
Thermally Enhanced QFN (TEQFN) | – Larger exposed pad on the bottom surface – Improved heat dissipation and thermal performance |
– Power management ICs – High-performance processors |
Wettable Flank QFN (WFQFN) | – Partially plated side walls with a wettable material – Allows for improved solder joint inspection |
– Applications requiring high manufacturing quality and reliability |
Punch-Type QFN (PQFN) | – Manufactured using a stamping process – More precise and consistent lead frame structure – Improved mechanical stability |
– Applications requiring tight tolerances or high reliability |
0 Comments