What is a PTH PCB?
A Plated Through Hole (PTH) PCB is a type of printed circuit board that features holes that are electroplated with a conductive material, typically copper. These plated holes create electrical connections between the different layers of the PCB, allowing for the mounting and soldering of through-hole components. PTH PCBs offer several advantages over non-plated through hole boards, including improved mechanical strength, enhanced electrical conductivity, and better thermal dissipation.
Advantages of PTH PCBs
- Mechanical strength: The Plated Through Holes provide additional support for the mounted components, increasing the overall mechanical strength of the PCB.
- Electrical conductivity: The electroplated holes ensure a reliable electrical connection between the different layers of the PCB, reducing the risk of signal loss or interference.
- Thermal dissipation: The plated through holes help to dissipate heat generated by the components, preventing overheating and ensuring optimal performance.
The Manufacturing Process of PTH PCBs
The production of PTH PCBs involves several key steps, including drilling, electroless copper deposition, and electroplating. Each step plays a crucial role in ensuring the quality and reliability of the final product.
Step 1: Drilling
The first step in the manufacturing process is to drill the required holes in the PCB substrate. This is typically done using high-speed CNC drilling machines that can accurately create holes of various sizes and locations based on the PCB design files.
Step 2: Electroless Copper Deposition
After drilling, the PCB undergoes a process called electroless copper deposition. This involves chemically depositing a thin layer of copper onto the surface of the PCB, including the walls of the drilled holes. The electroless copper layer acts as a conductive seed layer for the subsequent electroplating process.
Step 3: Electroplating
The final step in creating PTH PCBs is electroplating. The PCB is immersed in an electrolytic solution containing copper ions, and an electrical current is applied. This causes the copper ions to be attracted to the conductive seed layer, forming a thicker layer of copper on the surface of the PCB and inside the holes. The electroplating process ensures a uniform and reliable electrical connection between the layers of the PCB.
Factors Affecting the Quality of PTH PCBs
Several factors can influence the quality and performance of PTH PCBs. Understanding these factors is essential for ensuring the production of high-quality boards that meet the required specifications.
Hole Size and Aspect Ratio
The size of the drilled holes and their aspect ratio (the ratio of the hole depth to its diameter) can significantly impact the quality of the plated through holes. Smaller holes with higher aspect ratios are more challenging to electroplate uniformly, which can lead to issues such as voids or incomplete plating.
Copper Thickness
The thickness of the electroplated copper layer is another critical factor in determining the quality and reliability of PTH PCBs. Insufficient copper thickness can result in poor electrical conductivity and reduced mechanical strength, while excessive thickness can cause issues with component fitting and solderability.
Plating Chemistry
The choice of plating chemistry and the control of the electroplating process parameters, such as temperature, pH, and current density, can also affect the quality of the plated through holes. Proper control of these factors is essential for achieving uniform and consistent plating results.
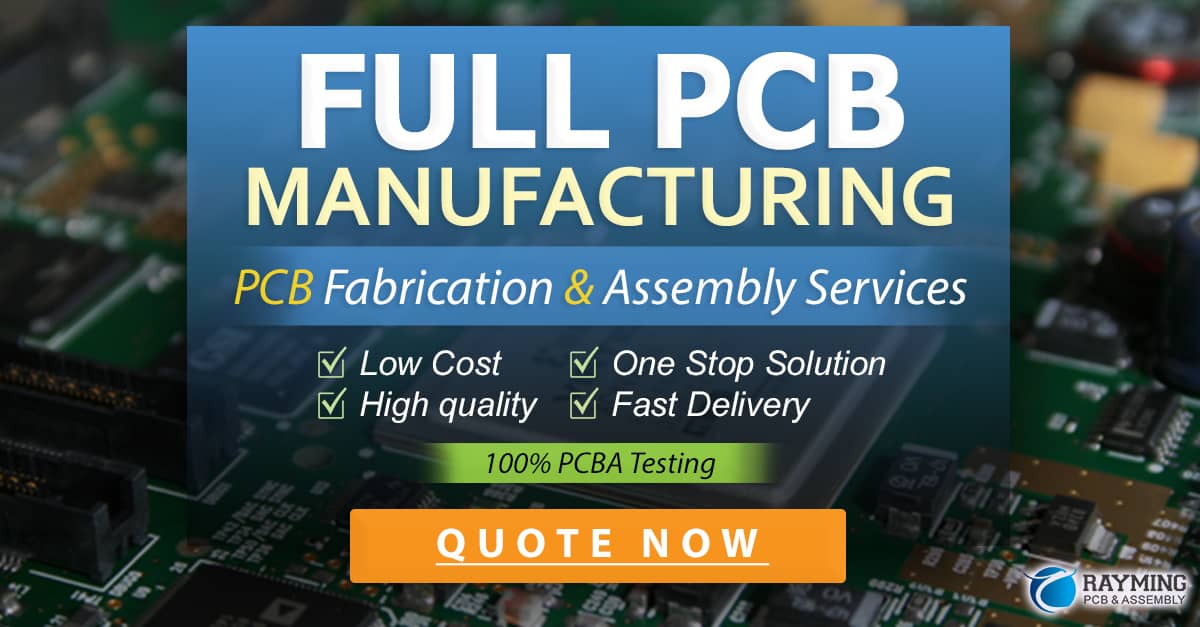
Applications of PTH PCBs
PTH PCBs find applications in a wide range of industries, including:
- Consumer electronics
- Automotive electronics
- Industrial control systems
- Medical devices
- Aerospace and defense
The versatility and reliability of PTH PCBs make them a popular choice for many electronic applications where robust electrical connections and mechanical strength are essential.
Comparing PTH and SMT PCBs
While PTH PCBs offer several advantages, Surface Mount Technology (SMT) PCBs have gained popularity in recent years due to their compact size and high component density. The following table compares some key aspects of PTH and SMT PCBs:
Aspect | PTH PCBs | SMT PCBs |
---|---|---|
Component mounting | Through holes | Surface mounted |
Board size | Larger | Smaller |
Component density | Lower | Higher |
Manufacturing cost | Higher | Lower |
Mechanical strength | Higher | Lower |
Thermal dissipation | Better | Worse |
Despite the growing popularity of SMT PCBs, PTH PCBs remain an essential technology for many applications, particularly those requiring high reliability and mechanical strength.
Future Trends in PTH PCB Technology
As the electronics industry continues to evolve, PTH PCB technology is also advancing to meet the changing requirements of modern applications. Some of the future trends in PTH PCB technology include:
-
Miniaturization: The demand for smaller and more compact electronic devices is driving the development of miniaturized PTH PCBs with smaller hole sizes and higher aspect ratios.
-
Advanced materials: The use of advanced substrate materials, such as high-frequency laminates and flexible substrates, is expanding the application range of PTH PCBs.
-
Hybrid designs: The combination of PTH and SMT technologies on a single PCB is becoming more common, allowing for the benefits of both technologies to be leveraged in a single design.
-
Improved manufacturing processes: Advancements in drilling, plating, and inspection technologies are enabling the production of higher-quality PTH PCBs with improved reliability and consistency.
By staying at the forefront of these trends, PCB manufacturers can continue to provide high-quality PTH PCBs that meet the evolving needs of the electronics industry.
Frequently Asked Questions (FAQ)
-
What is the difference between a PTH PCB and a non-plated through hole PCB?
A PTH PCB has holes that are electroplated with a conductive material, typically copper, which creates electrical connections between the layers of the PCB. A non-plated through hole PCB has holes that are not plated, and therefore, do not provide electrical connections between layers. -
Can PTH PCBs be used for high-frequency applications?
Yes, PTH PCBs can be used for high-frequency applications, provided that the appropriate substrate materials and design techniques are employed. The use of high-frequency laminates and careful control of the plating process can help to minimize signal loss and ensure optimal performance. -
What is the typical copper thickness for PTH PCBs?
The typical copper thickness for PTH PCBs ranges from 25 to 35 microns (1 to 1.4 mils). However, the specific thickness required may vary depending on the application and the design requirements of the PCB. -
How do PTH PCBs compare to SMT PCBs in terms of manufacturing cost?
PTH PCBs generally have a higher manufacturing cost compared to SMT PCBs due to the additional processes involved in creating the plated through holes, such as drilling and electroplating. However, the cost difference may be justified for applications that require the enhanced mechanical strength and reliability provided by PTH PCBs. -
Can PTH and SMT components be used together on the same PCB?
Yes, PTH and SMT components can be used together on the same PCB in a hybrid design. This allows for the benefits of both technologies to be leveraged in a single design, such as the mechanical strength of PTH components and the high component density of SMT components.
In conclusion, PTH PCBs remain a crucial technology in the electronics industry, offering several advantages over non-plated through hole boards. By understanding the manufacturing process, factors affecting quality, and future trends in PTH PCB technology, designers and manufacturers can ensure the production of high-quality, reliable PCBs that meet the demands of modern electronic applications.
0 Comments