In the world of Printed Circuit Board (PCB) design and manufacturing, thickness is a crucial parameter that significantly impacts various aspects of the board’s performance, reliability, and application suitability. PCBs are available in a range of standard thicknesses, each with its own advantages and limitations. Understanding these standard thicknesses and their implications is essential for designers and manufacturers to make informed decisions and ensure optimal performance and functionality of their electronic devices.
Overview of PCB Thicknesses
PCB thicknesses are typically measured in mils or millimeters, with 1 mil being equivalent to 0.001 inches or 0.0254 millimeters. The thickness of a PCB is determined by the combined thickness of the base material (substrate) and the copper layers, including any additional coatings or solder masks applied. The most common standard PCB thicknesses range from 0.6 mm (23.6 mils) to 3.2 mm (126 mils), with variations in between.
Factors Influencing PCB Thickness Selection
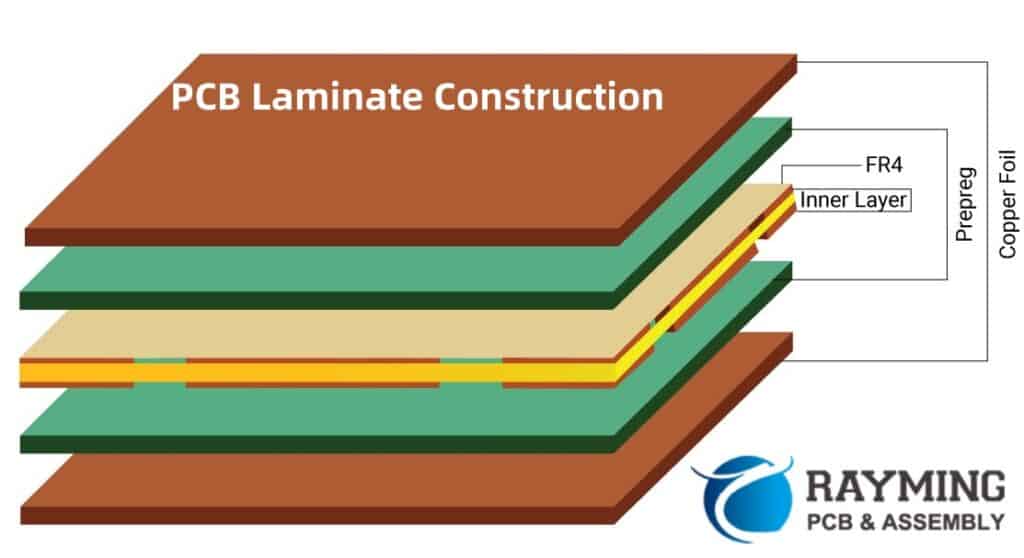
Several factors contribute to the selection of an appropriate PCB thickness for a given application. Understanding these factors is crucial in making an informed decision and ensuring the board meets the desired performance and reliability requirements.
1. Mechanical Strength and Rigidity
Thicker PCBs generally exhibit greater mechanical strength and rigidity, making them more resistant to bending, warping, and physical damage. This characteristic is particularly important for applications that involve harsh environmental conditions, mechanical stress, or large-scale assemblies where the PCB needs to support heavy components.
2. Thermal Management
The thickness of a PCB can significantly impact its thermal management capabilities. Thicker boards typically have better heat dissipation properties, as they provide a larger surface area and volume for heat transfer. This is especially crucial for high-power applications or densely populated boards where effective heat dissipation is essential for reliable operation and component longevity.
3. Signal Integrity
In high-speed and high-frequency applications, signal integrity is a critical consideration. The thickness of the PCB can affect the impedance of the traces, which in turn impacts signal quality and transmission characteristics. Thicker boards generally have higher impedance values, making them more suitable for certain applications that require specific impedance matching or controlled impedance environments.
4. Flexibility
While thicker PCBs offer greater mechanical strength, thinner boards provide increased flexibility, which can be advantageous in applications that require bending or conforming to specific shapes or contours. This is particularly important in wearable electronics, flexible displays, and certain aerospace or automotive applications.
5. Cost and Manufacturing Considerations
The thickness of a PCB can also influence its cost and manufacturing process. In general, thicker boards tend to be more expensive due to the increased material requirements and potential challenges in drilling, routing, and other manufacturing processes. However, in high-volume production runs, the cost difference may be less significant.
Standard PCB Thicknesses and Applications
To assist designers and manufacturers in selecting the appropriate PCB thickness, several standard thicknesses have been established within the industry. The following table provides an overview of common standard PCB thicknesses and their typical applications:
Thickness (mm) | Thickness (mils) | Typical Applications |
---|---|---|
0.6 | 23.6 | Flexible circuits, membrane switches, wearable electronics |
0.8 | 31.5 | Consumer electronics, mobile devices, low-power applications |
1.0 | 39.4 | General-purpose boards, instrumentation, industrial controls |
1.2 | 47.2 | Power supplies, motor drives, high-power applications |
1.6 | 63.0 | High-power applications, automotive electronics, server boards |
2.0 | 78.7 | Telecom equipment, high-density interconnects, backplanes |
2.4 | 94.5 | Power modules, heat sinks, high-power and high-density applications |
3.2 | 126.0 | Extreme high-power applications, heavy industrial equipment |
It is important to note that while these are common standard thicknesses, custom thicknesses can also be manufactured to meet specific design requirements or application demands.
Considerations for PCB Thickness Selection
When selecting the appropriate PCB thickness for a particular design or application, it is essential to consider the following factors:
- Application Requirements: Evaluate the specific needs of your application, such as mechanical strength, thermal management, signal integrity, and flexibility requirements. This will help determine the optimal thickness range for your PCB.
- Component Specifications: Ensure that the selected PCB thickness is compatible with the components and components’ specifications. Some components may have specific thickness requirements or recommendations from the manufacturer.
- Assembly and Manufacturing Processes: Consider the assembly and manufacturing processes involved, as certain thicknesses may be more suitable or pose challenges for specific processes like wave soldering, reflow soldering, or through-hole assembly.
- Regulatory Compliance: Depending on the application and industry, certain regulatory standards or guidelines may specify minimum or maximum PCB thickness requirements. It is crucial to ensure compliance with these regulations.
- Cost and Volume Considerations: While thicker PCBs generally have higher material costs, the overall cost impact may be less significant for high-volume production runs. Evaluate the cost-benefit analysis based on your production volumes and budget constraints.
FQA (Frequently Asked Questions)
- Q: Can I use a PCB thickness outside the standard range? A: Yes, it is possible to use custom PCB thicknesses that fall outside the standard range. However, this may require additional manufacturing considerations and could potentially increase costs. It is essential to ensure that the custom thickness meets the design requirements and is compatible with the intended application.
- Q: What is the most common PCB thickness used in consumer electronics? A: The most common PCB thickness used in consumer electronics is typically between 0.8 mm (31.5 mils) and 1.0 mm (39.4 mils). This thickness range provides a balance between mechanical strength, component density, and cost-effectiveness for most consumer electronics applications.
- Q: Can I use a thicker PCB to improve heat dissipation in my design? A: Yes, using a thicker PCB can generally improve heat dissipation capabilities due to the increased surface area and volume for heat transfer. However, it is important to consider other factors, such as component placement, thermal management strategies, and overall design requirements, to ensure optimal thermal performance.
- Q: How does PCB thickness affect signal integrity in high-speed applications? A: PCB thickness can significantly impact signal integrity in high-speed and high-frequency applications. Thicker PCBs generally have higher impedance values, which can affect signal transmission characteristics and potentially introduce signal degradation or reflections. Careful consideration and simulation of signal integrity are crucial when designing high-speed boards with specific thickness requirements.
- Q: Can I mix different PCB thicknesses within the same design? A: While it is possible to mix different PCB thicknesses within the same design, this practice is generally not recommended as it can introduce challenges in manufacturing, assembly, and overall board reliability. If mixing thicknesses is unavoidable, it is essential to carefully consider the design implications and ensure proper mechanical and electrical integrity throughout the board.
0 Comments