Why is PCB Testing Important?
PCB testing is essential for several reasons:
- Quality assurance: Testing ensures that PCBs meet the required specifications and performance standards.
- Cost savings: Identifying defects early in the manufacturing process reduces the cost of rework and prevents product recalls.
- Reliability: Thorough testing ensures that PCBs will function reliably in the intended application and environment.
- Safety: PCB testing helps identify potential safety hazards, such as short circuits or overheating, which could cause harm to users or equipment.
Types of PCB Testing
There are various types of PCB tests that can be performed at different stages of the manufacturing process. Some of the most common tests include:
Visual Inspection
Visual inspection is the first step in PCB testing and involves examining the board for obvious defects, such as:
- Incorrect component placement
- Solder bridges or shorts
- Damaged or missing components
- Incorrect polarity of components
- Poor solder joints
Visual inspection can be performed manually using a magnifying glass or microscope or automatically using automated optical inspection (AOI) systems.
Automated Optical Inspection (AOI)
AOI systems use high-resolution cameras and image processing software to detect surface-level defects on PCBs. These systems compare the PCB images to a reference image and highlight any discrepancies. AOI is particularly useful for identifying issues such as:
- Missing or misaligned components
- Solder paste defects
- Incorrect component polarity
- Solder bridges or shorts
In-Circuit Testing (ICT)
In-circuit testing verifies the functionality of individual components on a PCB by applying electrical signals and measuring the response. ICT systems use a bed-of-nails fixture that makes contact with specific test points on the PCB. This type of testing can detect issues such as:
- Open or short circuits
- Incorrect component values
- Missing or damaged components
- Incorrect component orientation
Flying Probe Testing
Flying probe testing is an alternative to ICT that uses movable test probes instead of a fixed bed-of-nails fixture. The probes move across the PCB, making contact with test points and performing electrical measurements. Flying probe testing is more flexible than ICT and can be used for smaller production runs or prototypes. However, it is generally slower than ICT.
Functional Testing
Functional testing verifies that the PCB performs as intended in its final application. This type of testing involves applying input signals to the board and measuring the output response. Functional testing can be performed using various methods, such as:
- Boundary scan testing: Uses built-in test circuitry to verify the connectivity and functionality of digital components.
- Burn-in testing: Subjects the PCB to elevated temperatures and voltages to identify potential early-life failures.
- Environmental testing: Exposes the PCB to various environmental conditions, such as temperature, humidity, and vibration, to ensure reliability.
PCB Testing Equipment
To perform the various types of PCB tests, manufacturers use a range of specialized equipment. Some of the most common PCB testing equipment includes:
Multimeters
Multimeters are used to measure basic electrical properties, such as voltage, current, and resistance. They are essential for troubleshooting and verifying the functionality of individual components on a PCB.
Oscilloscopes
Oscilloscopes display waveforms and are used to measure signal timing, frequency, and amplitude. They are particularly useful for debugging and analyzing analog circuits.
Logic Analyzers
Logic analyzers capture and display digital signals and are used to debug and verify the functionality of digital circuits. They can measure multiple signals simultaneously and provide timing diagrams and state listings.
Spectrum Analyzers
Spectrum analyzers measure the frequency content of signals and are used to identify issues such as electromagnetic interference (EMI) or signal distortion.
LCR Meters
LCR meters measure the inductance (L), capacitance (C), and resistance (R) of components. They are used to verify that components meet the specified values and to identify potential issues, such as leakage or degradation.
Thermal Imaging Cameras
Thermal imaging cameras detect heat patterns on a PCB and are used to identify potential hot spots or thermal issues that could lead to component failure.
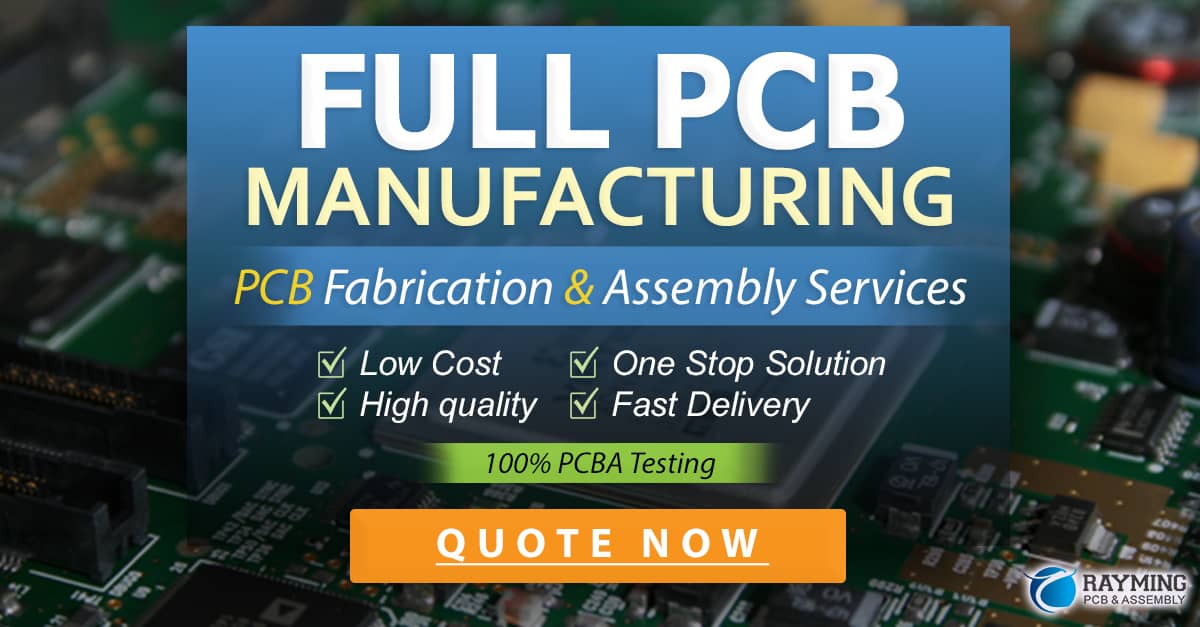
PCB Testing Best Practices
To ensure effective and efficient PCB testing, consider the following best practices:
- Start testing early: Begin testing as early as possible in the design and manufacturing process to identify and address issues quickly.
- Use a combination of testing methods: Employ a mix of visual inspection, AOI, ICT, flying probe, and functional testing to ensure comprehensive coverage.
- Develop a comprehensive test plan: Create a detailed test plan that outlines the specific tests to be performed, the equipment to be used, and the acceptance criteria.
- Use standardized test procedures: Follow standardized test procedures to ensure consistent and repeatable results.
- Regularly calibrate test equipment: Ensure that all test equipment is regularly calibrated and maintained to ensure accurate and reliable measurements.
- Document test results: Keep detailed records of all test results, including any defects found and corrective actions taken.
- Continuously improve the testing process: Regularly review and update the testing process based on feedback from manufacturing and field performance data.
Frequently Asked Questions
How much does PCB testing cost?
The cost of PCB testing varies depending on the complexity of the board, the number of test points, and the type of testing performed. In general, testing costs can range from a few cents to several dollars per board. However, the cost of testing is often offset by the savings from reduced rework and improved product quality.
How long does PCB testing take?
The duration of PCB testing depends on the type of testing performed and the complexity of the board. Visual inspection and AOI can be completed in a matter of seconds, while ICT and functional testing may take several minutes per board. Flying probe testing is generally slower than ICT, with test times ranging from a few minutes to several hours, depending on the number of test points and the complexity of the measurements.
Can PCB testing be outsourced?
Yes, many electronics manufacturers outsource PCB testing to specialized testing service providers. Outsourcing can be cost-effective for companies that do not have the in-house expertise or equipment to perform comprehensive testing. When outsourcing, it is important to choose a reputable provider with experience in the specific type of testing required and to clearly communicate the test requirements and acceptance criteria.
How often should PCB testing be performed?
PCB testing should be performed at various stages throughout the manufacturing process, including:
- Prototype testing: Before mass production begins, prototype boards should be thoroughly tested to verify the design and identify any potential issues.
- Production testing: During mass production, a sample of boards from each manufacturing lot should be tested to ensure consistent quality.
- Failure analysis: If a product fails in the field, the PCB should be tested to identify the root cause of the failure and implement corrective actions.
What are the most common PCB Defects found during testing?
Some of the most common PCB defects found during testing include:
- Solder joint issues: Poor solder joints, bridging, or insufficient solder can cause intermittent or complete failures.
- Component placement errors: Incorrect component placement or orientation can lead to functional failures or damage to the component or board.
- Short or open circuits: Short circuits can cause overheating or damage to components, while open circuits can result in loss of functionality.
- Component value errors: Incorrect component values can cause the circuit to perform outside of its specified range or fail altogether.
- Manufacturing process defects: Issues such as contamination, incorrect etching, or drilling errors can lead to various functional and reliability problems.
By understanding the importance of PCB testing, the various types of tests available, and the best practices for implementing a comprehensive testing strategy, electronics manufacturers can ensure the quality, reliability, and performance of their products. Regular testing and continuous improvement of the testing process are essential for staying competitive in today’s rapidly evolving electronics industry.
Test Type | Description | Detects |
---|---|---|
Visual Inspection | Manual or automated examination of PCB for defects | Incorrect component placement, solder bridges, damaged components |
Automated Optical Inspection (AOI) | Uses cameras and image processing to detect surface-level defects | Missing components, solder paste defects, incorrect polarity |
In-Circuit Testing (ICT) | Verifies functionality of individual components using bed-of-nails fixture | Open/short circuits, incorrect component values, missing components |
Flying Probe Testing | Uses movable test probes to perform electrical measurements | Similar to ICT, but more flexible and suitable for smaller runs |
Functional Testing | Verifies PCB performance in final application using various methods | Boundary scan, burn-in, and environmental testing for reliability |
0 Comments