Introduction to PCB Stackup
PCB (Printed Circuit Board) stackup is a crucial aspect of Electronic Design that determines the arrangement of layers in a PCB. It plays a significant role in the overall performance, reliability, and manufacturability of the final product. In this comprehensive guide, we will dive deep into the world of PCB stackup planning, exploring its fundamentals, best practices, and optimization techniques.
What is a PCB Stackup?
A PCB stackup refers to the arrangement of copper layers, insulating materials, and other components that make up a printed circuit board. It defines the number of layers, their order, and the materials used between them. The stackup also specifies the thickness of each layer and the spacing between them.
Why is PCB Stackup Planning Important?
Proper PCB stackup planning is essential for several reasons:
-
Signal Integrity: The stackup configuration directly impacts the signal integrity of the PCB. It affects the impedance, crosstalk, and electromagnetic interference (EMI) of the signals traveling through the board.
-
Power Integrity: The stackup also influences the power delivery network of the PCB. It determines the placement of power and ground planes, which are crucial for maintaining a stable and clean power supply to the components.
-
Manufacturability: The choice of materials, layer thicknesses, and spacing in the stackup affects the manufacturability of the PCB. Proper stackup planning ensures that the board can be fabricated reliably and cost-effectively.
-
Reliability: A well-designed stackup enhances the reliability of the PCB by minimizing the risk of signal integrity issues, power supply noise, and mechanical stress.
PCB Stackup Layers and Materials
A typical PCB stackup consists of multiple layers, each serving a specific purpose. Let’s explore the common layers found in a PCB stackup:
Signal Layers
Signal layers are the layers where the majority of the Circuit Traces are routed. They carry the electrical signals between components on the PCB. The number of signal layers in a stackup depends on the complexity of the design and the routing requirements.
Power and Ground Planes
Power and ground planes are dedicated layers that provide a low-impedance path for power distribution and grounding. They help maintain a stable power supply and reduce noise in the system. The placement and spacing of these planes are critical for power integrity.
Dielectric Materials
Dielectric materials are insulating layers that separate the conductive layers in the PCB stackup. They provide electrical insulation and determine the impedance of the traces. Common dielectric materials include FR-4, Rogers, and Isola.
Copper Thickness and Spacing
The thickness of the copper layers and the spacing between them are important factors in PCB stackup planning. Thicker copper layers are used for power and ground planes to handle higher currents, while thinner layers are used for signal routing. The spacing between layers affects the impedance and crosstalk of the signals.
PCB Stackup Configurations
There are various PCB stackup configurations available, each with its own advantages and considerations. Let’s explore some common stackup configurations:
2-Layer Stackup
A 2-layer stackup is the simplest and most cost-effective configuration. It consists of a top and bottom layer, with signal traces routed on both sides. The top layer is typically used for component placement, while the bottom layer is used for routing and power/ground connections.
Layer | Material | Thickness |
---|---|---|
Top | Copper | 1 oz |
Core | FR-4 | 1.6 mm |
Bottom | Copper | 1 oz |
4-Layer Stackup
A 4-layer stackup is a common configuration for more complex designs. It consists of two signal layers and two internal planes (power and ground). The signal layers are routed on the top and bottom, while the internal planes provide a stable power supply and grounding.
Layer | Material | Thickness |
---|---|---|
Top | Copper | 1 oz |
Prepreg | FR-4 | 0.2 mm |
Inner1 | Copper | 1 oz |
Core | FR-4 | 1.6 mm |
Inner2 | Copper | 1 oz |
Prepreg | FR-4 | 0.2 mm |
Bottom | Copper | 1 oz |
6-Layer Stackup
A 6-layer stackup is used for even more complex designs with higher routing density and signal integrity requirements. It typically consists of four signal layers and two internal planes (power and ground). The additional signal layers provide more routing space and flexibility.
Layer | Material | Thickness |
---|---|---|
Top | Copper | 1 oz |
Prepreg | FR-4 | 0.2 mm |
Inner1 | Copper | 1 oz |
Core | FR-4 | 1.6 mm |
Inner2 | Copper | 1 oz |
Prepreg | FR-4 | 0.2 mm |
Inner3 | Copper | 1 oz |
Core | FR-4 | 1.6 mm |
Inner4 | Copper | 1 oz |
Prepreg | FR-4 | 0.2 mm |
Bottom | Copper | 1 oz |
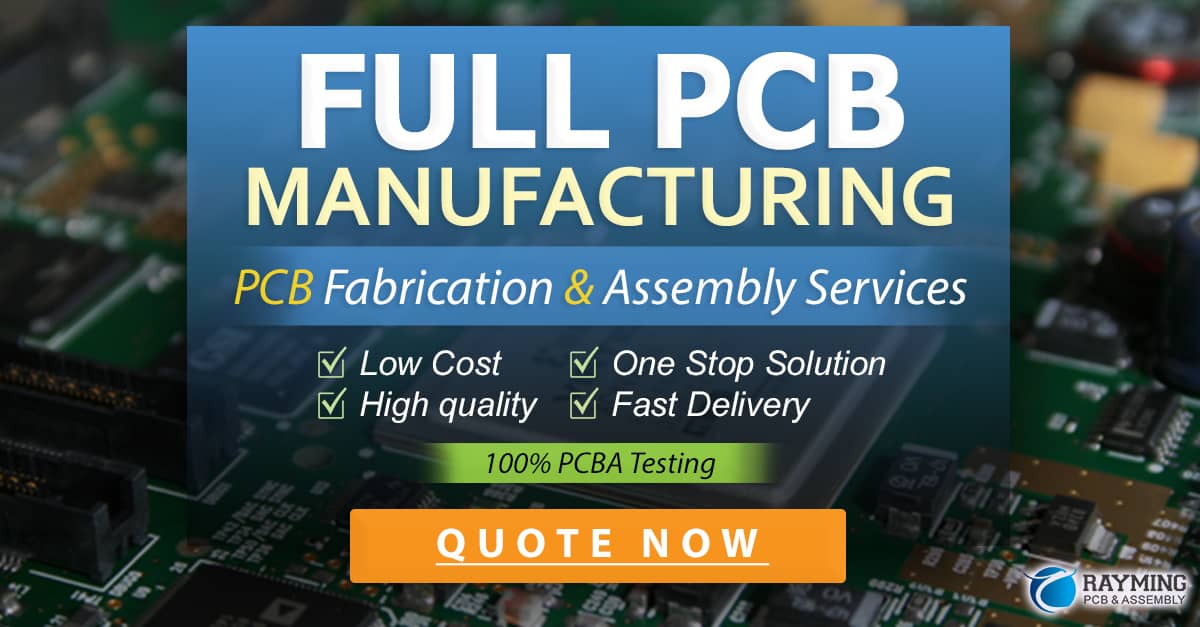
PCB Stackup Design Considerations
When planning a PCB stackup, there are several key considerations to keep in mind:
Signal Integrity
Signal integrity is a critical factor in PCB stackup design. It involves managing the quality of signals as they travel through the board. Some key aspects of signal integrity include:
-
Impedance Control: Maintaining consistent impedance throughout the signal path is crucial for preventing reflections and ensuring proper signal propagation. The stackup configuration, trace width, and dielectric material impact the impedance.
-
Crosstalk: Crosstalk occurs when signals from one trace interfere with adjacent traces. Proper spacing between signal layers and the use of ground planes can help minimize crosstalk.
-
EMI/EMC: Electromagnetic interference (EMI) and electromagnetic compatibility (EMC) are important considerations in PCB stackup design. Proper shielding, grounding, and layer arrangement can help mitigate EMI and ensure EMC compliance.
Power Integrity
Power integrity refers to the quality and stability of the power supply to the components on the PCB. The stackup configuration plays a significant role in power integrity. Consider the following:
-
Power and Ground Planes: Dedicated power and ground planes provide a low-impedance path for power distribution. They should be placed close to the supply pins of components to minimize voltage drop and noise.
-
Decoupling Capacitors: Decoupling capacitors help stabilize the power supply by filtering out high-frequency noise. The placement of decoupling capacitors in relation to the power and ground planes is crucial for effective decoupling.
-
Via Placement: The placement of vias connecting different layers in the stackup can impact power integrity. Proper via placement and sizing help minimize impedance discontinuities and reduce voltage drop.
Manufacturability
PCB stackup planning should also consider the manufacturability of the board. Some key factors to keep in mind include:
-
Material Selection: Choose materials that are compatible with the manufacturing process and meet the required electrical and mechanical properties. Consider the availability and cost of the materials.
-
Layer Thickness and Spacing: Ensure that the layer thicknesses and spacing are within the manufacturing capabilities of the PCB fabricator. Consult with the fabricator to determine the minimum and maximum values for these parameters.
-
Drill Pairs and Aspect Ratio: Consider the number of drill pairs (top and bottom layers) and the aspect ratio of the drilled holes. High aspect ratio holes can be challenging to manufacture reliably.
Best Practices for PCB Stackup Planning
To optimize your PCB stackup planning process, consider the following best practices:
-
Start with a Clear Understanding of Requirements: Begin by gathering all the necessary information about your design requirements, including signal integrity, power integrity, and manufacturability constraints.
-
Choose the Right Number of Layers: Determine the appropriate number of layers based on the complexity of your design, routing requirements, and cost considerations. Avoid using more layers than necessary to minimize cost and manufacturing complexity.
-
Use Dedicated Power and Ground Planes: Incorporate dedicated power and ground planes in your stackup to provide a low-impedance path for power distribution and reduce noise. Place them close to the supply pins of components.
-
Control Impedance: Design your stackup to achieve the desired impedance for your signals. Work with your PCB fabricator to select the appropriate dielectric materials and copper thicknesses to meet your impedance requirements.
-
Minimize Crosstalk: Reduce crosstalk by providing adequate spacing between signal layers and using ground planes to shield sensitive signals. Consider techniques like trace routing and via spacing to minimize crosstalk.
-
Optimize Via Placement: Carefully plan the placement of vias to minimize impedance discontinuities and signal integrity issues. Use appropriate via sizes and spacing to ensure reliable manufacturing.
-
Consider EMI/EMC: Design your stackup with EMI/EMC considerations in mind. Use shielding techniques, proper grounding, and layer arrangement to mitigate electromagnetic interference.
-
Collaborate with PCB Fabricators: Work closely with your PCB fabricator throughout the stackup planning process. They can provide valuable insights into manufacturability, material selection, and design rules.
-
Simulate and Verify: Use simulation tools to analyze your stackup design for signal integrity, power integrity, and EMI/EMC performance. Verify your design through prototyping and testing to ensure it meets your requirements.
-
Document and Communicate: Clearly document your stackup design, including layer arrangement, materials, thicknesses, and spacing. Communicate this information effectively to all stakeholders, including the design team, PCB fabricator, and assembly house.
Frequently Asked Questions (FAQ)
-
What is the difference between a 2-layer and 4-layer PCB stackup?
A 2-layer PCB stackup consists of a top and bottom layer, with signal traces routed on both sides. A 4-layer stackup adds two internal layers, typically used for power and ground planes, providing better signal integrity and power distribution. -
How do I choose the right dielectric material for my PCB stackup?
The choice of dielectric material depends on factors such as the desired electrical properties (e.g., dielectric constant, Loss Tangent), mechanical properties, and cost. Common dielectric materials include FR-4, Rogers, and Isola. Consult with your PCB fabricator to select the most suitable material for your application. -
What is the importance of impedance control in PCB stackup planning?
Impedance control is crucial for maintaining signal integrity in high-speed designs. It ensures that the impedance of the signal traces matches the characteristic impedance of the system, preventing reflections and signal distortions. Proper impedance control requires careful selection of dielectric materials, trace widths, and spacing in the PCB stackup. -
How can I minimize crosstalk in my PCB stackup?
Crosstalk can be minimized by providing adequate spacing between signal layers, using ground planes to shield sensitive signals, and employing proper trace routing techniques. Increasing the spacing between adjacent traces and using differential pair routing can also help reduce crosstalk. -
What are the key considerations for manufacturability in PCB stackup planning?
Key considerations for manufacturability include material selection, layer thickness and spacing, drill pairs, and aspect ratio. Choose materials that are compatible with the manufacturing process and readily available. Ensure that the layer thicknesses and spacing are within the capabilities of the PCB fabricator. Consider the number of drill pairs and the aspect ratio of drilled holes to ensure reliable manufacturing.
Conclusion
PCB stackup planning is a critical aspect of electronic design that directly impacts the performance, reliability, and manufacturability of the final product. By understanding the fundamentals of PCB stackup, considering signal integrity, power integrity, and manufacturability factors, and following best practices, you can optimize your PCB stackup for success.
Remember to collaborate closely with your PCB fabricator, simulate and verify your design, and clearly document and communicate your stackup requirements. By taking a comprehensive approach to PCB stackup planning, you can ensure that your electronic products meet their functional and quality goals while being cost-effective to manufacture.
0 Comments