What is an SMT stencil?
An SMT (Surface Mount Technology) stencil, also known as a solder paste stencil, is a thin sheet of material, typically stainless steel or polyester, with laser-cut openings that correspond to the pads on a PCB (Printed Circuit Board). These openings allow for precise application of solder paste onto the PCB pads, ensuring accurate and consistent placement of surface mount components during the assembly process.
Materials Used for SMT Stencils
SMT stencils can be made from various materials, each with its own advantages and disadvantages. The most common materials used are:
Material | Advantages | Disadvantages |
---|---|---|
Stainless Steel | Durable, long lifespan, suitable for high-volume production | More expensive, requires cleaning |
Polyester | Low cost, disposable, no cleaning required | Less durable, shorter lifespan, not suitable for fine-pitch applications |
Nickel | Good durability, suitable for fine-pitch applications | More expensive than stainless steel |
SMT Stencil Thicknesses
The thickness of an SMT stencil plays a crucial role in determining the amount of solder paste deposited on the PCB pads. The most common stencil thicknesses are:
Thickness | Application |
---|---|
100μm (4 mil) | Fine-pitch components, small pads |
125μm (5 mil) | General-purpose, suitable for most applications |
150μm (6 mil) | Large components, high-volume solder paste deposits |
The Importance of SMT Stencils in PCB Assembly
Ensuring Precise Solder Paste Application
One of the primary functions of an SMT stencil is to ensure precise and consistent application of solder paste onto PCB pads. The laser-cut openings in the stencil allow for a controlled amount of solder paste to be deposited, minimizing the risk of insufficient or excessive solder joints.
Improving Production Efficiency
Using an SMT stencil can significantly improve the efficiency of the PCB assembly process. By automating the solder paste application process, manufacturers can reduce the time and labor required for manual application, thereby increasing throughput and reducing production costs.
Reducing Assembly Defects
Accurate solder paste application is essential for reducing assembly defects such as bridging, tombstoning, and insufficient solder joints. By using an SMT stencil, manufacturers can ensure consistent solder paste deposits, minimizing the risk of defects and improving overall product quality.
SMT Stencil Design Considerations
Aperture Size and Shape
The size and shape of the apertures in an SMT stencil directly influence the amount and distribution of solder paste on the PCB pads. Aperture sizes should be carefully calculated based on the pad dimensions, component size, and desired solder volume. Common aperture shapes include square, rectangular, and circular.
Stencil Thickness
As mentioned earlier, the thickness of an SMT stencil determines the amount of solder paste deposited on the PCB pads. Thicker stencils are generally used for larger components and higher-volume solder paste deposits, while thinner stencils are preferred for fine-pitch applications and smaller components.
Aperture Wall Angle
The angle of the aperture walls in an SMT stencil can affect the release of solder paste during the printing process. A wall angle of 5 to 7 degrees is typically recommended to facilitate smooth paste release and prevent clogging of the apertures.
Fiducial Marks
Fiducial marks are reference points on the stencil that help align the stencil with the PCB during the solder paste printing process. These marks should be strategically placed on the stencil to ensure accurate registration and prevent misalignment.
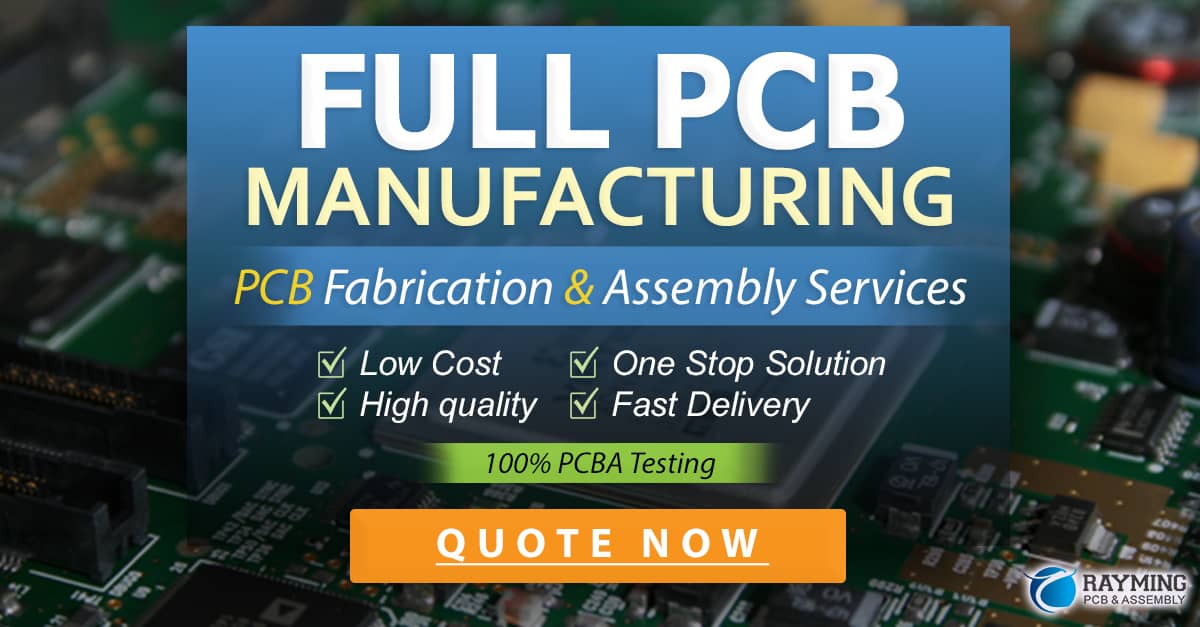
SMT Stencil Printing Process
Stencil Alignment
Before printing, the SMT stencil must be accurately aligned with the PCB. This is typically done using a stencil printer equipped with a vision system that detects the fiducial marks on the stencil and PCB, ensuring precise registration.
Solder Paste Application
Once the stencil is aligned, solder paste is applied to the stencil surface. A squeegee blade then moves across the stencil, forcing the solder paste through the apertures and onto the PCB pads. The blade pressure, speed, and angle should be carefully controlled to ensure even distribution of the solder paste.
Stencil Cleaning
After printing, the SMT stencil must be cleaned to remove any residual solder paste that may clog the apertures or affect the quality of subsequent prints. Stencil cleaning can be done manually or using automated cleaning systems, depending on the production volume and stencil material.
SMT Stencil Maintenance and Storage
Regular Inspection
SMT stencils should be regularly inspected for signs of wear, damage, or clogging. Damaged or worn stencils can lead to inconsistent solder paste deposits and assembly defects, so it is essential to identify and replace them promptly.
Proper Storage
When not in use, SMT stencils should be stored in a clean, dry environment to prevent contamination and damage. Stencils should be placed in protective containers or bags and kept away from sources of heat, humidity, and dust.
Handling Precautions
SMT stencils are delicate and should be handled with care to avoid damage. When handling stencils, operators should wear gloves to prevent contamination and use appropriate tools to avoid bending or scratching the stencil surface.
Frequently Asked Questions (FAQ)
1. How often should I replace my SMT stencil?
The lifespan of an SMT stencil depends on various factors, such as the material, thickness, and printing volume. On average, stainless steel stencils can last for 20,000 to 50,000 prints, while polyester stencils are typically replaced after 5,000 to 10,000 prints. However, it is essential to regularly inspect your stencil for signs of wear or damage and replace it as needed to maintain print quality.
2. Can I use the same SMT stencil for different PCB designs?
While it is possible to use the same SMT stencil for different PCB designs, it is not recommended. Each PCB design has unique pad dimensions and layouts, requiring a stencil with matching apertures. Using a stencil designed for a different PCB can result in incorrect solder paste application and assembly defects.
3. How do I choose the right solder paste for my SMT stencil?
When selecting a solder paste for your SMT stencil, consider factors such as the alloy composition, particle size, and viscosity. The solder paste should be compatible with the stencil aperture sizes and able to achieve the desired print definition and release characteristics. It is also essential to choose a solder paste that meets the requirements of your specific application, such as temperature profile, shelf life, and environmental compliance.
4. What are step stencils, and when are they used?
Step stencils, also known as multi-level stencils, are SMT stencils with varying thicknesses across different areas of the stencil. These stencils are used when a PCB design includes components of different sizes or heights, requiring different solder paste volumes. By using a step stencil, manufacturers can optimize the solder paste deposition for each component type, improving assembly quality and reliability.
5. How can I optimize my SMT stencil design for better print results?
To optimize your SMT stencil design, consider the following factors:
- Ensure proper aperture sizes and shapes based on the pad dimensions and desired solder volume
- Select the appropriate stencil thickness for your components and application
- Maintain a consistent aperture wall angle of 5 to 7 degrees for smooth paste release
- Incorporate fiducial marks for accurate stencil-to-PCB alignment
- Minimize unsupported apertures and use support bridges where necessary
- Consider the aspect ratio (aperture width to stencil thickness) to prevent paste clogging
By carefully designing your SMT stencil and considering these factors, you can achieve better print definition, consistency, and overall assembly quality.
Conclusion
SMT stencils play a critical role in the PCB assembly process, ensuring precise and consistent solder paste application for surface mount components. By understanding the importance of stencil design, materials, and maintenance, manufacturers can optimize their assembly process, reduce defects, and improve product quality. As PCB designs continue to evolve with smaller and more complex components, the use of high-quality SMT stencils will remain essential for successful PCB assembly.
0 Comments