What is PCB Panel Utilization and Why is it Important?
PCB panel utilization refers to maximizing the usable area on a manufactured panel of printed circuit boards. A panel is a large board consisting of multiple individual PCBs that are fabricated together and then separated into the final individual boards after manufacturing.
Optimizing panel utilization is critical for several reasons:
-
Cost reduction: Manufacturing PCBs in panels allows you to produce a higher quantity of boards at a lower cost per unit compared to manufacturing them individually. The more PCBs you can fit on a panel, the lower the cost per board.
-
Material efficiency: Maximizing panel usage minimizes wasted raw materials like the copper and substrate that make up the panel. This improves the material efficiency and reduces waste.
-
Production efficiency: Running fewer panels through the fabrication process to produce the same quantity of PCBs saves time and labor. This makes the overall production process more efficient.
Standard PCB Panel Sizes
While custom panel sizes are possible, most PCB Manufacturers offer a set of standard panel dimensions for cost and compatibility reasons. Using standard sizes simplifies the quoting, tooling, and manufacturing processes.
Common standard panel sizes include:
Size | Dimensions (inches) | Dimensions (mm) |
---|---|---|
18×24 | 18″ x 24″ | 457 mm x 610 mm |
21×24 | 21″ x 24″ | 533 mm x 610 mm |
16×18 | 16″ x 18″ | 406 mm x 457 mm |
12×18 | 12″ x 18″ | 305 mm x 457 mm |
The most common and cost-effective panel size is 18×24 inches (457x610mm). It offers a good balance of panel utilization and compatibility with standard PCB fabrication processes and equipment.
Factors Affecting PCB Panel Utilization
Several factors influence how efficiently you can utilize the area of a PCB panel:
PCB Size and Shape
The size and shape of your individual PCB design is the primary factor in determining panel utilization. Smaller boards allow you to fit more PCBs on a panel. Rectangular boards are easier to arrange efficiently than boards with complex or irregular shapes.
Panelization Scheme
Panelization refers to the process of arranging multiple individual PCBs on a panel. The panelization scheme, or the way the boards are laid out on the panel, greatly affects panel utilization.
Common panelization schemes include:
- Grid: PCBs are arranged in a simple grid pattern with even spacing between boards.
- Staggered: PCBs are offset in alternating rows, allowing them to nest together more closely.
- Stepped: PCBs are arranged in steps or terraces, which can be an efficient way to panel long, narrow boards.
The best panelization scheme depends on the size, shape, and quantity of the individual PCBs being produced.
Tooling and Spacing Requirements
PCB panels require tooling holes and fiducial marks for registration during the fabrication process. These features take up space on the panel and must be accounted for in the panelization design.
Additionally, there must be adequate spacing between individual PCBs on the panel to allow for depaneling (separating the boards) after fabrication. This spacing is typically 3-5mm around the perimeter of each board.
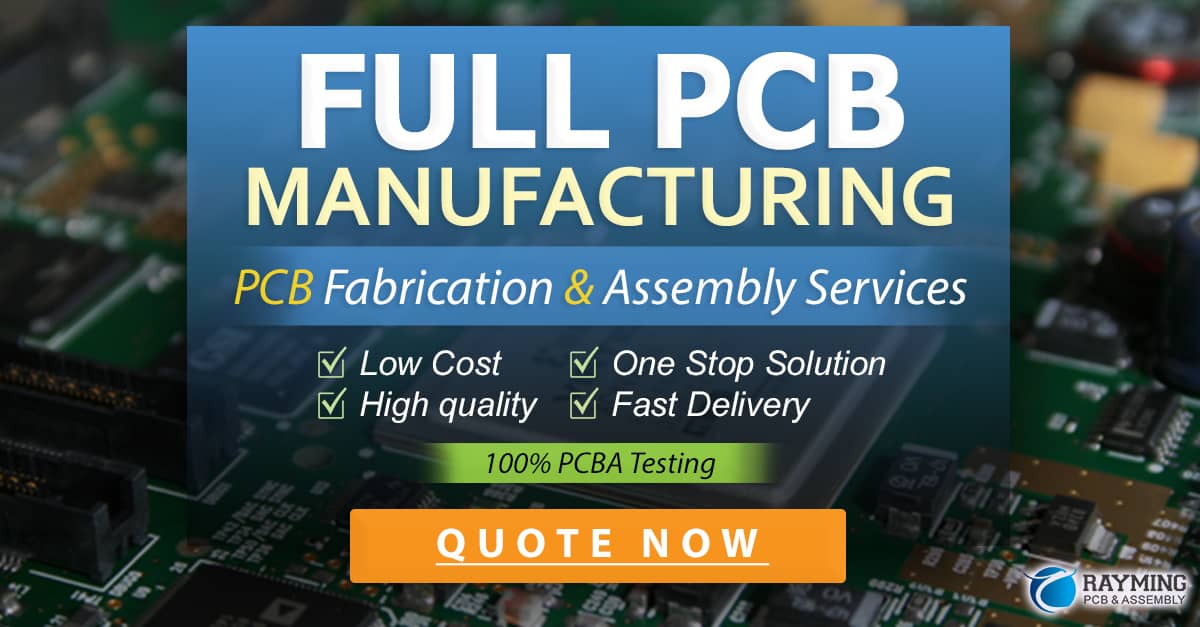
Best Practices for Optimizing PCB Panel Utilization
Choose an Optimal PCB Size
If your design allows, choose PCB dimensions that optimize panel usage. Smaller boards generally provide better panel utilization. If your design requires a larger board, consider using a standard panel size that minimizes wasted space.
Use Efficient Panelization Schemes
Experiment with different panelization schemes to find the most efficient layout for your specific PCB design. A staggered or stepped layout may provide better utilization than a simple grid, depending on the size and shape of your boards.
Minimize Wasted Panel Space
Look for ways to use any empty space on the panel that isn’t large enough for an additional PCB. You can panelize smaller sub-boards or test coupons in these spaces to get some utility out of them.
Consider Panelizing Different PCB Designs Together
If you’re manufacturing multiple different PCB designs, consider panelizing them together on the same panel to maximize panel usage. This is especially effective if the designs are for the same project or customer.
Use a Panelization Tool
Many PCB design software packages include tools for automatically panelizing your PCB designs. These tools can help you quickly generate efficient panels and experiment with different layouts.
Example of Optimized PCB Panelization
Let’s consider an example of optimizing the panelization of a 100mm x 50mm rectangular PCB design. We’ll compare two different panelization schemes on a standard 18×24 inch (457x610mm) panel.
Grid Panelization
In a simple grid arrangement, we can fit 12 PCBs on the panel in a 3×4 grid with 5mm spacing between boards:
100mm | 5mm | 100mm | 5mm | 100mm | 5mm | |
---|---|---|---|---|---|---|
50mm | PCB1 | PCB2 | PCB3 | |||
5mm | ||||||
50mm | PCB4 | PCB5 | PCB6 | |||
5mm | ||||||
50mm | PCB7 | PCB8 | PCB9 | |||
5mm | ||||||
50mm | PCB10 | PCB11 | PCB12 |
Panel utilization = (12 PCBs x 100mm x 50mm) / (457mm x 610mm) = 21.6%
Staggered Panelization
By staggering the PCBs in alternating rows, we can fit 14 PCBs on the panel with the same 5mm spacing:
100mm | 5mm | 100mm | 5mm | 100mm | 5mm | 100mm | 5mm | |
---|---|---|---|---|---|---|---|---|
25mm | PCB1 | PCB2 | PCB3 | PCB4 | ||||
5mm | ||||||||
50mm | PCB5 | PCB6 | PCB7 | PCB8 | ||||
5mm | ||||||||
25mm | PCB9 | PCB10 | PCB11 | PCB12 | ||||
5mm | ||||||||
50mm | PCB13 | PCB14 |
Panel utilization = (14 PCBs x 100mm x 50mm) / (457mm x 610mm) = 25.2%
In this example, the staggered panelization scheme achieves better panel utilization by fitting two additional PCBs on the same size panel.
Frequently Asked Questions (FAQ)
1. What is the most common PCB panel size?
The most common and cost-effective standard PCB panel size is 18×24 inches (457x610mm). This size is compatible with most PCB fabrication processes and offers a good balance of panel utilization and manufacturing efficiency.
2. How much space should I leave between PCBs on a panel?
A spacing of 3-5mm around the perimeter of each PCB is typically recommended to allow for clean depaneling after fabrication. The exact spacing requirements may vary depending on your PCB manufacturer’s capabilities and guidelines.
3. Can I panelize different PCB designs together on the same panel?
Yes, panelizing different PCB designs together on the same panel is a common technique for maximizing panel utilization. This is especially effective if the designs are for the same project, customer, or product.
4. What is the most efficient panelization scheme?
The most efficient panelization scheme depends on the size, shape, and quantity of the individual PCBs being manufactured. A staggered or stepped layout often provides better panel utilization than a simple grid arrangement, but it’s best to experiment with different layouts to find the optimal configuration for your specific design.
5. How can I minimize wasted space on a PCB panel?
To minimize wasted panel space, look for opportunities to panelize additional small PCBs, sub-boards, or test coupons in any empty areas that aren’t large enough for a full PCB. You can also optimize your individual PCB designs to use dimensions that facilitate efficient panelization.
0 Comments