What are PCB pads?
PCB pads, also known as solder pads or landing pads, are conductive areas on a printed circuit board where electronic components are soldered. These pads provide a surface for the component leads or pins to be attached, enabling electrical connectivity between the component and the PCB traces.
Key Features of PCB Pads
- Conductivity: PCB pads are made of conductive materials, typically copper, to ensure efficient electrical connectivity.
- Size and Shape: Pads come in various sizes and shapes, depending on the component and the soldering requirements.
- Plating: Pads are often plated with additional materials, such as gold, silver, or tin, to improve solderability and prevent oxidation.
Types of PCB Pads
There are several types of PCB pads, each designed for specific component types and soldering techniques. Let’s explore some common pad types:
1. SMD Pads
Surface Mount Device (SMD) pads are used for surface-mounted components. These pads are flat and have no drilled holes. SMD pads come in various shapes, such as rectangular, circular, or oval, depending on the component package.
SMD Pad Shape | Component Package |
---|---|
Rectangular | Chip Resistors, Capacitors |
Circular | Chip Inductors, LEDs |
Oval | SOT-23, SOT-89 |
2. Through-Hole Pads
Through-hole pads are used for components with leads that pass through drilled holes in the PCB. These pads have a hole in the center to accommodate the component lead and are typically circular or oval in shape.
Through-Hole Pad Shape | Component Package |
---|---|
Circular | Resistors, Capacitors, DIP ICs |
Oval | Connectors, Switches |
3. Castellated Pads
Castellated pads, also known as edge-plated pads, are used for connecting multiple PCBs or modules together. These pads are located along the edges of the PCB and have a semi-circular or castellated shape, allowing for secure soldering between boards.
4. Thermal Pads
Thermal pads, also called heat sink pads, are used for components that generate significant heat, such as power transistors or voltage regulators. These pads have a larger surface area to dissipate heat efficiently and often include thermal vias to transfer heat to other layers of the PCB.
PCB Pad Design Considerations
Designing PCB pads requires careful consideration of various factors to ensure optimal performance and reliability. Here are some key design considerations:
1. Pad Size and Spacing
Pad size and spacing should be determined based on the component package and the soldering process. The pad size should be large enough to provide sufficient area for soldering while maintaining appropriate clearance between adjacent pads to prevent short circuits.
2. Solder Mask Clearance
Solder mask is a protective layer applied over the PCB, leaving the pads exposed for soldering. It is crucial to maintain adequate solder mask clearance around the pads to prevent solder bridging and ensure proper soldering.
3. Pad Shape and Orientation
The shape and orientation of pads should be chosen based on the component package and the assembly process. For example, rectangular pads are commonly used for chip components, while circular pads are suitable for through-hole components.
4. Thermal Considerations
For components that generate significant heat, it is essential to design pads with adequate thermal dissipation capabilities. This can be achieved by increasing the pad size, using thermal vias, or incorporating dedicated thermal pads.
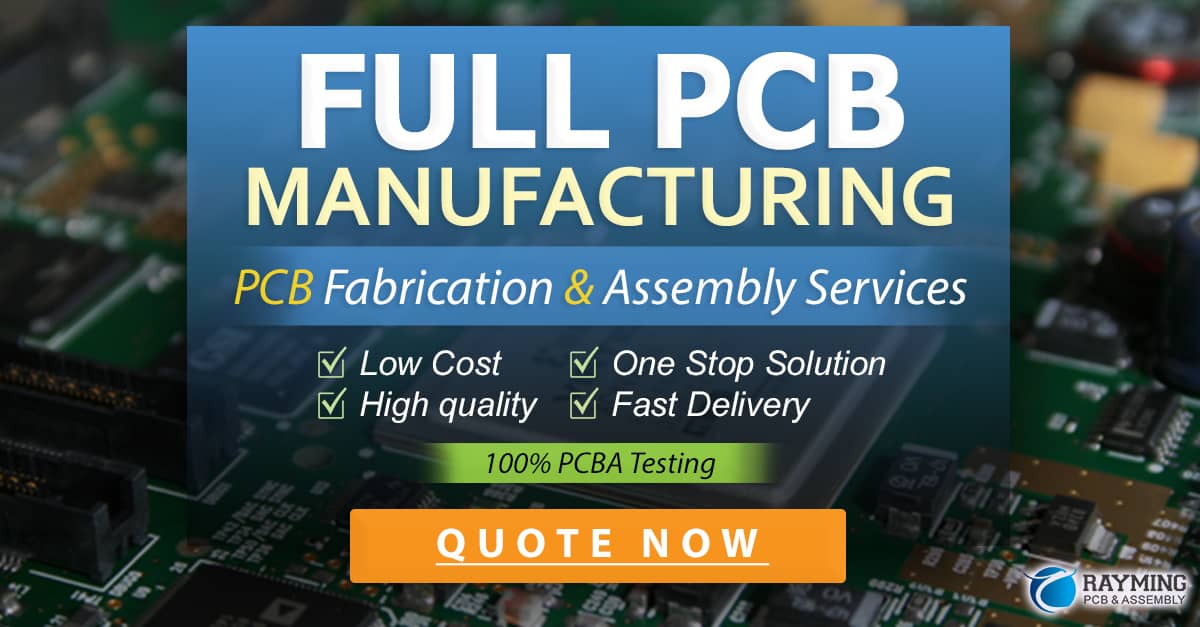
Best Practices for PCB Pad Design
To ensure optimal performance and manufacturability, follow these best practices when designing PCB pads:
-
Adhere to Industry Standards: Follow the recommended pad sizes and spacing guidelines provided by component manufacturers and industry standards, such as IPC (Association Connecting Electronics Industries).
-
Consider Manufacturing Tolerances: Account for manufacturing tolerances when designing pads. Ensure that the pad size and spacing allow for variations in the manufacturing process without compromising functionality.
-
Use Appropriate Solder Mask Clearance: Maintain sufficient solder mask clearance around the pads to prevent solder bridging and ensure proper soldering. The clearance should be based on the soldering process and the component package.
-
Optimize Pad Placement: Place pads strategically to minimize the length of PCB traces and reduce signal interference. Consider the component orientation and the overall PCB layout when placing pads.
-
Conduct Design Reviews: Perform thorough design reviews to catch any potential issues early in the design process. Collaborate with PCB manufacturers and assembly partners to ensure that the pad design is compatible with their processes.
Frequently Asked Questions (FAQ)
-
What is the difference between SMD and through-hole pads?
SMD pads are flat and used for surface-mounted components, while through-hole pads have a drilled hole to accommodate component leads that pass through the PCB. -
How do I determine the appropriate pad size for a component?
Refer to the component manufacturer’s datasheet or consult industry standards, such as IPC, for recommended pad sizes based on the component package and the soldering process. -
What is solder mask clearance, and why is it important?
Solder mask clearance is the space between the edge of the pad and the solder mask opening. It is important to maintain adequate clearance to prevent solder bridging and ensure proper soldering. -
How can I improve thermal dissipation for pads with heat-generating components?
To improve thermal dissipation, you can increase the pad size, use thermal vias to transfer heat to other layers of the PCB, or incorporate dedicated thermal pads. -
What are castellated pads, and when are they used?
Castellated pads, also known as edge-plated pads, are used for connecting multiple PCBs or modules together. They are located along the edges of the PCB and have a semi-circular or castellated shape for secure soldering between boards.
Conclusion
PCB pads play a crucial role in ensuring reliable electrical connections between components and the PCB. Understanding the different types of pads, their design considerations, and best practices is essential for creating high-quality and manufacturable PCB designs.
By following industry standards, considering manufacturing tolerances, optimizing pad placement, and conducting thorough design reviews, you can enhance the performance and reliability of your PCB assembly.
As technology advances and component packages evolve, staying updated with the latest pad design techniques and guidelines is crucial. Collaborating with experienced PCB manufacturers and assembly partners can provide valuable insights and ensure the success of your PCB projects.
With a solid understanding of PCB pads and their intricacies, you can confidently design and manufacture reliable electronic devices that meet the ever-growing demands of the industry.
0 Comments