Introduction
Printed Circuit Boards (PCBs) are essential components in modern electronics, providing a platform for electrical connections and mechanical support for various components. The manufacturing process of PCBs involves several critical steps, one of which is drilling. Drilling is a crucial process that creates holes in the PCB for component placement and electrical connectivity. However, drilling defects can occur during the manufacturing process, leading to issues such as poor electrical performance, reduced reliability, and increased manufacturing costs. In this article, we will discuss the causes of PCB drilling defects and explore methods for their elimination.
PCB Drilling Process Overview
Before delving into the causes and elimination methods of PCB drilling defects, it is essential to understand the drilling process itself. PCB drilling involves creating holes of various sizes and locations on the PCB Substrate according to the design requirements. The drilling process typically involves the following steps:
-
Drilling machine setup: The PCB is loaded onto the drilling machine, and the drill bits are installed according to the required hole sizes.
-
Drill file generation: A drill file, containing the coordinates and sizes of the holes to be drilled, is generated from the PCB design software.
-
Drilling operation: The drilling machine follows the drill file instructions and creates holes in the PCB substrate using the installed drill bits.
-
Cleaning and inspection: After drilling, the PCB is cleaned to remove any debris, and the drilled holes are inspected for accuracy and quality.
Common PCB Drilling Defects
Several drilling defects can occur during the PCB manufacturing process, each with its own causes and consequences. Some of the most common PCB drilling defects include:
1. Misaligned Holes
Misaligned holes occur when the drilled holes are not positioned accurately according to the PCB design. This can lead to issues such as component misalignment, poor electrical connections, and reduced reliability.
Causes of Misaligned Holes
- Incorrect drill file generation
- Improper machine setup or calibration
- Worn or damaged drill bits
- PCB material instability or shrinkage
Elimination Methods
- Double-check drill file accuracy before production
- Regularly calibrate and maintain drilling machines
- Use high-quality, sharp drill bits and replace them when worn
- Choose stable PCB materials and consider material properties during design
2. Oversized or Undersized Holes
Oversized or undersized holes occur when the drilled hole diameters deviate from the specified dimensions in the PCB design. This can cause issues such as loose or tight component fits, poor electrical connections, and reduced mechanical strength.
Causes of Oversized or Undersized Holes
- Incorrect drill bit selection
- Drill bit wear or damage
- Improper machine settings, such as feed rate or spindle speed
- PCB material properties, such as hardness or thickness variations
Elimination Methods
- Use the correct drill bit sizes for each hole
- Monitor drill bit wear and replace as needed
- Optimize machine settings based on PCB material properties and hole sizes
- Implement quality control measures to identify and correct hole size deviations
3. Burrs and Breakouts
Burrs are raised edges or protrusions around the drilled holes, while breakouts are cracks or damage to the PCB material surrounding the holes. Both defects can cause issues such as poor electrical connections, component fitment problems, and reduced PCB strength.
Causes of Burrs and Breakouts
- Dull or worn drill bits
- Improper drilling parameters, such as feed rate or spindle speed
- Inadequate PCB support during drilling
- PCB material properties, such as brittleness or low Glass Transition Temperature
Elimination Methods
- Use sharp, high-quality drill bits and replace them regularly
- Optimize drilling parameters based on PCB material properties and hole sizes
- Provide adequate support for the PCB during drilling, such as using backup materials or vacuum tables
- Consider using specialized drill bits or drilling techniques for challenging PCB materials
4. Smear and Debris
Smear is a thin layer of melted PCB material that covers the walls of the drilled holes, while debris refers to the small particles of PCB material that accumulate in the holes during drilling. Both defects can cause issues such as poor electrical connections, insulation resistance reduction, and difficulties in subsequent PCB processing steps.
Causes of Smear and Debris
- Incorrect drilling parameters, such as high feed rates or low spindle speeds
- Dull or worn drill bits
- Inadequate cooling or lubrication during drilling
- PCB material properties, such as low glass transition temperature or high resin content
Elimination Methods
- Optimize drilling parameters to minimize heat generation and material melting
- Use sharp, high-quality drill bits and replace them regularly
- Ensure adequate cooling and lubrication during drilling, such as using compressed air or specialized coolants
- Consider using specialized drill bits or drilling techniques for challenging PCB materials
- Implement thorough cleaning processes after drilling to remove debris
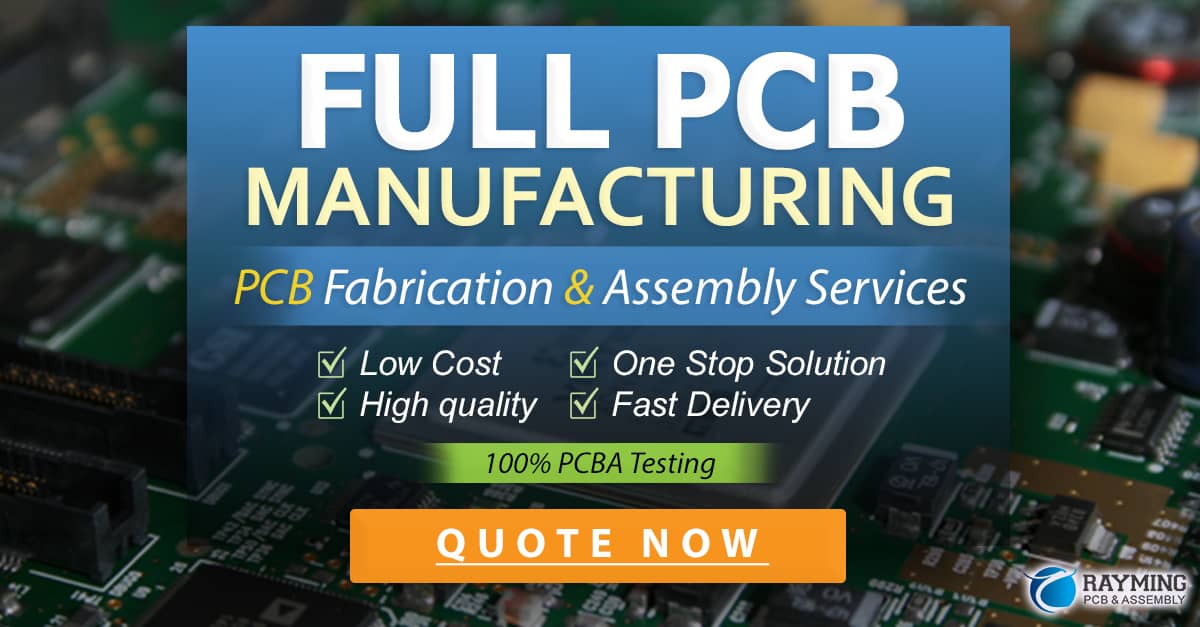
Best Practices for Minimizing PCB Drilling Defects
To minimize the occurrence of PCB drilling defects, manufacturers can adopt several best practices:
-
Design for Manufacturability (DFM): Incorporate DFM principles during the PCB design stage, such as using standard hole sizes, providing adequate spacing between holes, and considering material properties.
-
Regular Machine Maintenance: Implement a regular maintenance schedule for drilling machines, including calibration, lubrication, and cleaning to ensure optimal performance and accuracy.
-
Quality Control and Inspection: Establish robust quality control measures, such as visual inspection, automated optical inspection (AOI), and statistical process control (SPC) to identify and correct drilling defects promptly.
-
Operator Training and Skill Development: Invest in training and skill development for machine operators to ensure they have the knowledge and expertise to optimize drilling processes and identify potential issues.
-
Continuous Improvement: Foster a culture of continuous improvement, encouraging operators and engineers to identify and implement process enhancements that reduce drilling defects and improve overall PCB Quality.
Conclusion
PCB drilling is a critical process in the manufacturing of printed circuit boards, and drilling defects can have significant consequences for the performance, reliability, and cost of the final product. By understanding the causes of common drilling defects, such as misaligned holes, oversized or undersized holes, burrs and breakouts, and smear and debris, manufacturers can implement targeted elimination methods and best practices to minimize their occurrence. Through a combination of design optimization, machine maintenance, quality control, operator training, and continuous improvement, PCB Manufacturers can produce high-quality, defect-free boards that meet the demanding requirements of modern electronics.
FAQ
Q1: What is the most common PCB drilling defect?
A1: One of the most common PCB drilling defects is misaligned holes, which occur when the drilled holes are not positioned accurately according to the PCB design. This can lead to issues such as component misalignment, poor electrical connections, and reduced reliability.
Q2: How can I prevent oversized or undersized holes in my PCBs?
A2: To prevent oversized or undersized holes, use the correct drill bit sizes for each hole, monitor drill bit wear and replace as needed, optimize machine settings based on PCB material properties and hole sizes, and implement quality control measures to identify and correct hole size deviations.
Q3: What causes burrs and breakouts during PCB drilling?
A3: Burrs and breakouts can be caused by dull or worn drill bits, improper drilling parameters, inadequate PCB support during drilling, and PCB material properties, such as brittleness or low glass transition temperature.
Q4: How can I minimize smear and debris in drilled holes?
A4: To minimize smear and debris, optimize drilling parameters to minimize heat generation and material melting, use sharp, high-quality drill bits and replace them regularly, ensure adequate cooling and lubrication during drilling, consider using specialized drill bits or drilling techniques for challenging PCB materials, and implement thorough cleaning processes after drilling.
Q5: What are some best practices for minimizing PCB drilling defects?
A5: Best practices for minimizing PCB drilling defects include incorporating Design for Manufacturability (DFM) principles during the PCB design stage, implementing regular machine maintenance, establishing robust quality control measures, investing in operator training and skill development, and fostering a culture of continuous improvement.
0 Comments