What is a PCB?
A printed circuit board, commonly known as a PCB, is a fundamental component in modern electronic devices. It is a flat board made of insulating materials, such as fiberglass or composite epoxy, with conductive pathways etched or printed onto its surface. These pathways, called traces, connect various electronic components, such as resistors, capacitors, and integrated circuits, to form a complete electrical circuit.
PCBs come in various sizes, shapes, and complexity levels, ranging from simple single-layer boards to multi-layer boards with intricate designs. They are used in almost every electronic device, from smartphones and computers to industrial equipment and aerospace technology.
Types of PCBs
There are several types of PCBs, each designed to meet specific requirements and applications. The most common types include:
-
Single-layer PCBs: These are the simplest and most cost-effective PCBs, with conductive traces printed on one side of the board. They are suitable for basic electronic projects and low-density designs.
-
Double-layer PCBs: These boards have conductive traces on both sides, allowing for more complex circuits and higher component density. They are widely used in consumer electronics and intermediate-level projects.
-
Multi-layer PCBs: These PCBs consist of multiple layers of conductive traces separated by insulating layers. They can have four, six, eight, or even more layers, depending on the complexity of the design. Multi-layer PCBs are used in advanced electronic devices, such as smartphones, laptops, and medical equipment.
-
Flexible PCBs: These boards are made of flexible materials, such as polyimide or PEEK, allowing them to bend and twist without breaking. They are ideal for applications that require compact packaging or where the PCB needs to conform to a specific shape, such as in wearable devices or automotive electronics.
-
Rigid-flex PCBs: These are a combination of rigid and flexible PCBs, where rigid sections are connected by flexible sections. This design allows for three-dimensional packaging and improved reliability in applications that require both stability and flexibility, such as in aerospace and military equipment.
The PCB Manufacturing Process
The PCB manufacturing process involves several steps, each requiring precision and adherence to industry standards. The main stages of PCB production are:
-
Design: The PCB design is created using specialized software, such as Altium Designer or Eagle. The design includes the component layout, trace routing, and layer stackup.
-
Printing: The PCB design is printed onto a photosensitive film or directly onto the copper-clad board using a plotter or laser printer.
-
Etching: The printed board is exposed to UV light, which hardens the photoresist on the exposed areas. The unexposed areas are then removed using a chemical solution, leaving the desired copper traces.
-
Drilling: Holes are drilled into the board to accommodate through-hole components and vias, which connect traces between layers.
-
Plating: The drilled holes are plated with copper to ensure electrical connectivity between layers.
-
Solder Mask Application: A protective layer, called the solder mask, is applied to the board to insulate the copper traces and prevent short circuits.
-
Silkscreen Printing: The component labels, logos, and other markings are printed onto the board using a silkscreen process.
-
Surface Finish: A surface finish, such as HASL (Hot Air Solder Leveling) or ENIG (Electroless Nickel Immersion Gold), is applied to the exposed copper areas to prevent oxidation and improve solderability.
-
Electrical Testing: The completed PCB undergoes electrical testing to ensure that all connections are correct and that there are no short circuits or open connections.
PCB Manufacturing Equipment
PCB manufacturing requires specialized equipment to ensure precision and quality. Some of the essential equipment used in PCB production includes:
Equipment | Description |
---|---|
CNC Drilling Machine | Used for drilling holes in the PCB with high precision and speed. |
Plotter | Prints the PCB design onto a photosensitive film or directly onto the copper-clad board. |
Exposure Unit | Exposes the photoresist-coated PCB to UV light to harden the exposed areas. |
Etching Machine | Removes the unwanted copper from the PCB using a chemical solution. |
Plating Equipment | Plates the drilled holes with copper to ensure electrical connectivity between layers. |
Solder Mask Coater | Applies the solder mask layer to the PCB to insulate the copper traces. |
Silkscreen Printer | Prints component labels, logos, and other markings onto the PCB. |
Electrical Testing Equipment | Tests the completed PCB for correct connections and potential defects. |
Choosing a PCB Manufacturer
When selecting a PCB manufacturer, several factors should be considered to ensure that you receive high-quality boards that meet your specific requirements. Some key factors to keep in mind include:
-
Capabilities: Ensure that the manufacturer has the necessary equipment and expertise to produce the type of PCB you require, whether it’s a simple single-layer board or a complex multi-layer design.
-
Quality Standards: Look for manufacturers that adhere to industry standards, such as IPC (Association Connecting Electronics Industries) standards, and have quality control processes in place to ensure consistent product quality.
-
Lead Time: Consider the manufacturer’s lead time, which is the time between placing your order and receiving the finished product. If you have tight deadlines, choose a manufacturer that can accommodate your timeline.
-
Cost: Compare prices from multiple manufacturers, but don’t compromise on quality for the sake of a lower price. Consider the total cost of ownership, including potential rework or replacement costs due to poor quality.
-
Customer Support: Choose a manufacturer that offers reliable customer support and is responsive to your inquiries and concerns. Good communication is essential for a successful partnership.
Online PCB Manufacturers
In recent years, online PCB manufacturers have gained popularity due to their convenience, competitive pricing, and quick turnaround times. Some popular online PCB manufacturers include:
- PCBWay
- JLCPCB
- Seeed Studio
- OSH Park
- Eurocircuits
These online platforms allow you to upload your PCB design files, select your desired specifications, and receive a quote instantly. They often have user-friendly interfaces and offer various manufacturing options to suit different budgets and requirements.
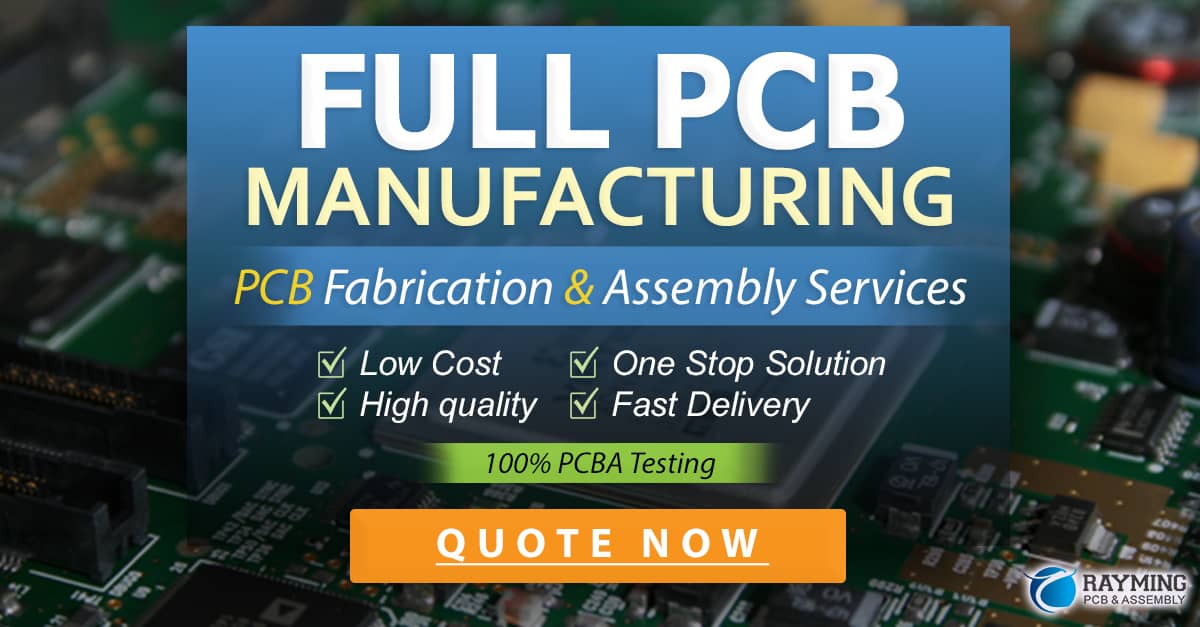
PCB design considerations
When designing a PCB, several factors must be taken into account to ensure optimal performance and manufacturability. Some key considerations include:
-
Component Placement: Place components in a logical and organized manner, considering factors such as signal integrity, heat dissipation, and ease of assembly.
-
Trace Routing: Route traces efficiently to minimize signal interference and ensure that they have the appropriate width and spacing for the desired current carrying capacity.
-
Grounding: Implement a proper grounding scheme to prevent signal interference and ensure the stability of the circuit.
-
Thermal Management: Consider the heat generated by components and design the PCB to dissipate heat effectively, using techniques such as copper pours or thermal vias.
-
Manufacturability: Design the PCB with manufacturability in mind, adhering to the manufacturer’s design guidelines and considering factors such as minimum trace width, hole size, and clearance requirements.
PCB Design Software
Several PCB design software options are available, ranging from free open-source tools to advanced commercial solutions. Some popular PCB design software includes:
- Altium Designer
- Autodesk Eagle
- KiCad
- OrCAD
- Mentor Graphics PADS
These software tools offer features such as schematic capture, layout editing, and design rule checking to help you create accurate and manufacturable PCB designs.
Frequently Asked Questions (FAQ)
- What is the difference between a single-layer and a multi-layer PCB?
-
A single-layer PCB has conductive traces on one side of the board, while a multi-layer PCB has multiple layers of conductive traces separated by insulating layers. Multi-layer PCBs offer higher component density and more complex routing options, but they are also more expensive to manufacture.
-
What is the purpose of a solder mask on a PCB?
-
The solder mask is a protective layer applied to the PCB to insulate the copper traces and prevent short circuits. It also helps to prevent solder bridging during the assembly process and provides a more aesthetically pleasing appearance to the finished board.
-
What is the difference between through-hole and surface-mount components?
-
Through-hole components have leads that are inserted into holes drilled in the PCB and soldered on the opposite side. Surface-mount components are mounted directly onto the surface of the PCB and soldered in place. Surface-mount components are smaller and allow for higher component density, but they can be more challenging to assemble manually.
-
What is the purpose of a via in a PCB?
-
A via is a small hole drilled in a PCB that connects traces on different layers. Vias allow for more efficient routing of traces and help to minimize the size of the PCB.
-
What is the minimum trace width and spacing that can be achieved on a PCB?
- The minimum trace width and spacing depend on the capabilities of the PCB manufacturer and the specific design requirements. Typical minimum trace widths range from 0.1 mm to 0.2 mm, while minimum spacing can be as low as 0.1 mm. However, smaller trace widths and spacing may increase the manufacturing cost and complexity.
Conclusion
PCBs are essential components in modern electronic devices, providing a reliable and efficient means of interconnecting electronic components. Understanding the basics of PCB Types, manufacturing processes, and design considerations is crucial for anyone involved in electronic product development.
When choosing a PCB manufacturer, it’s essential to consider factors such as capabilities, quality standards, lead time, cost, and customer support. Online PCB manufacturers offer a convenient and cost-effective option for many projects, but it’s important to carefully evaluate their capabilities and reputation before placing an order.
By following best practices in PCB design and selecting a reputable manufacturer, you can ensure that your electronic projects are successful and meet your performance and reliability requirements.
0 Comments